You may spend over a decade in this industry, meeting the same people over and over, heard about others multiple times, yet when you see them in real life, and have your first conversation with them, you ended up that conversation asking yourself: why is it that we are just meeting now? Well, that’s what I asked myself when I met Dr. David Leigh.
Leigh serves as the CTO of 3D Systems, an AM giant that I believe we should no longer introduce. He brings more than three decades of experience in the AM industry, spent in some of the top-notch companies of the field. He is also an entrepreneur whose company – Harvest Technologies, a company that provides end-use parts applications in aerospace – was acquired by Stratasys in 2014.
We may call it coincidence but the feeling I had, at the end of my conversation with Leigh is probably due to the fact that we mostly talked about materials. I like talking about materials. When I was still in the shoes of an end-user inexperienced in 3D printing, what I love the most about 3D printed parts was touching them and feeling the differences in terms of finishing one could get with different types of materials. I was fascinated by the ability of an AM process to transform a material – whether it is a liquid, a powder, a granule or a filament. I still am but with experience, I tend to question a lot.
Over time, I have talked to people, a lot of people; I have been in factories, I have explored things and I have learned many lessons. One of them is that the current challenge with the development of 3D printing materials lies in the ability to deliver properties that are similar or superior to properties of materials created for injection molding or other traditional manufacturing processes. If you’re an engineer reading these lines, it’s no surprise to you.
However, what may raise your interest is that, unlike many AM materials that are developed and finally leveraged for prototyping applications, the 3D Systems team currently focuses on developing materials that may enable end-use applications in demanding industries, especially in the metal AM field.
I am willing to trust their ability to deliver on these stringent requirements in the metal AM field when I look at the latest material developments achieved for the DMP production line – a series of hybrid manufacturing processes co-developed with Swiss machine manufacturer GF Machining Solutions. Beyond the choice of GFMS as a technology partner, to me, it’s about bringing together the best of both AM & traditional manufacturing processes within the same platform – in a context where AM is often underestimated and traditional manufacturing is no longer “trendy” enough -.
So, together both partners co-developed Certified HX, a high-performance nickel alloy that contains a higher percentage of molybdenum (up to 9.5%) versus other nickel alloys. This percentage would enhance the material’s strength and resistance to corrosion, creep deformation, cracking, and oxidation in hot zone environments. Ideal for applications with a service temperature of up to 1200°C, the material would deliver superior printed part quality and part density (typically 99.9%). Some of the applications it enables, include tall, large parts with integrated cooling and flow channels in optimal orientation for the energy, industrial gas turbine (IGT), petro-chemical, and aerospace & defense industries as well as applications such as hot zone stator blades and integrated stators, impellers, turbine vanes, drilling tools, and combustion components.
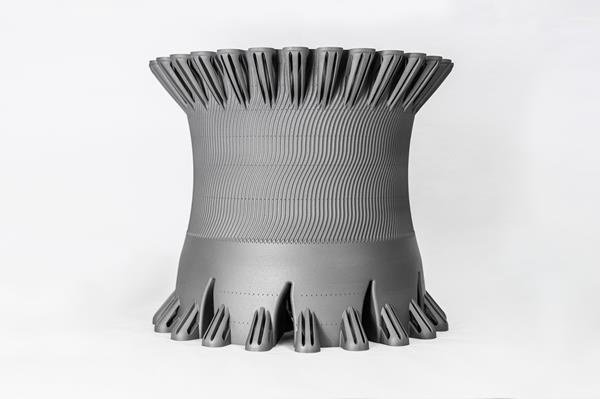
This material comes along the release of another one: Certified CuCr2.4. This high-strength, corrosion-resistant copper alloy would enable superior part density (typically 99.9%) and high conductivity after heat treatment. It enables applications in heat management and cooling systems, consumer goods, automotive, as well as aerospace & defense industries.
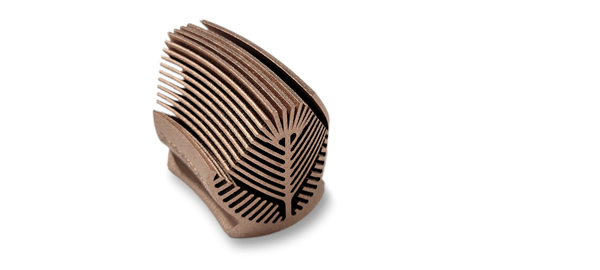
Both materials can be used on the DMP Flex 350, and DMP Factory 350 3D printers and HX is also certified for the DMP Factory 500 system.
“Being able to achieve prototyping applications is a good step forward with AM but achieving end-use parts is even better. That’s the reason why, we focus on applications. In the metal AM field especially, there are several [items that require the manufacturer’s attention: the manufacturing process itself, the software solutions and the powder. When we look at the powder, it’s crucial] to match the material with a specific application. The difficulty often lies in processing the material to achieve the right application. Therefore, we find value in addressing these challenges simultaneously. We push the envelope on alloys, process parameters, etc. to obtain the perfect combination for hard-to-achieve applications”, Leigh explains.
So, what’s really challenging in the development of certified materials for specific 3D printers like the DMP production line?
“Oxidation”, Leigh says, with no hesitation. “Whether we talk about titanium, aluminum, copper, nickel…they all share the same problems.” According to Leigh, materials designed for applications in corrosive environments must provide good creep strength as well as corrosion resistance at high temperatures. Surface oxidation of metallic powders may significantly affect their melting and solidification behavior and limit their service life in the additive manufacturing (AM) process. The challenge therefore, lies in the ability to find the right temperature at which they should melt.
Furthermore, oxidation or metallurgical surface defects occurring during AM processing are not the only challenges that can slow down the adoption of a given material on a specific AM process. Insufficiency in qualification and certification (Q&C) procedures and in globally accepted standards, as well as challenges in mechanical testing and verification of these alloys can also come into play. It’s also about evolving “on the edge of what can or cannot be done”, the CTO notes.
And does this evolution find balance with sustainability?
As our conversation became more and more relaxed, I tried to explore touchy topics. I know that OEMs may be greatly tempted to deploy transformative solutions for vertical industries adopting AM when in the end, the latter might just be needing sustaining ones. And at the materials level, “there is a lot of building blocks that go into sustainability”, 3D Systems’ CTO told me. Those building blocks require to choose the right material; to use as little material as possible (for large parts for instance, getting closer to the shape will make you save the material), and to recycle the material. “In the long-run, we will start looking at the full circle. What will need to do, is to look for materials that we can substitute”, he continues.
3D Systems embarked on a long journey that we will have to watch closely. Furthermore, we talk a lot about sustainability from the product and planet standpoints – (remember the September/October edition of 3D ADEPT Mag), because it’s easy to justify with LCA methods but let us not forget that sustainability is also about people – And their working environment, skills and ability to fulfil customers’ requests are things that also matter and that one should look at.
We may have mainly discussed about AM materials, but Leigh’s responsibilities at 3D Systems go beyond the materials field to also encompass the development of solutions that create new opportunities in regenerative medicine and bioprinting technologies. In this vein, if you’ve followed the company’s activities in the field, then you have probably realized that it leverages its long-standing expertise in AM to invest in this field. From a new bioprinting company formed to the development of a 3D printed human lung scaffold and 3D bioprinters, 3D Systems is implementing resources that enable to close the gap between the somewhat misguided preconceptions and what can actually be done with 3D bioprinting.
You may want to read this dossier: The different roads that lead to effective 3D bioprinting.
Last but not least, if we look at existing applications that are being achieved across industries, one can say that 3D Systems’ technology solutions are ready to deliver on AM’s promise, especially in aerospace and space. “We don’t” measure [the results] by the amount of money spent, but by the amount of money made. We don’t have to compete with injection molding, we can just replace it by AM”, Leigh concludes.
Remember, you can post job opportunities in the AM Industry on 3D ADEPT Media or look for a job via our job board. Make sure to follow us on our social networks and subscribe to our weekly newsletter : Facebook, Twitter, LinkedIn & Instagram ! If you want to be featured in the next issue of our digital magazine or if you hear a story that needs to be heard, make sure you send it to contact@3dadept.com