Updated on January 4th: The article has been updated to reflect the “Arburg” solution in part 4.
2023 has been a very interesting year both from a business and a technology perspective. Whether it was through participation in trade shows, conversations with industry insiders and coverage that encompasses the adoption across vertical industries or companies’ latest developments, there was a lot to see and learn about. In this article, we have decided to highlight 10 important technology highlights that have marked 2023. Hopefully, they will provide some food for thought on how you should approach 2024.
1. The DfAM language is more and more complex
It all starts with design. Design for Additive Manufacturing increasingly requires a deep understanding of the DfAM toolbox and how each of the design tools would help you get the best value for the part. In the May/June edition of 3D ADEPT Mag, we shed light on some of the most used design tools but new startups are working on new advancements that increasingly bet on computational engineering models.
As Matthew Shomper told us, computational design is not for the faint of heart. The tools are rather inaccessible (with large learning curves) and it usually requires a dual knowledge of designing for requirements and aesthetics at the same time. Good design sense is a must, regardless of what’s being created, and computational design is not a ‘shortcut’ to get around solid engineering principles.
That being said, understanding how this approach works and where it can be applied will be crucial to delivering parts in very short lead times.
2. The expanding reach of ceramic 3D printing
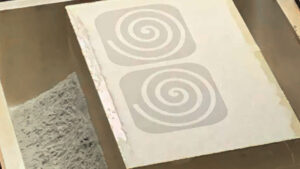
Ceramic 3D printing is growing in a way that I did not expect to see. This specific segment has often been given minor attention compared to metal or polymer 3D printing – which is understandable when we know that metal and polymer have always been the ideal materials for conventional manufacturing processes. Since most adopters of the technology continue to compare conventional manufacturing processes with AM, it makes sense to see less attention to ceramics. But this is changing as more and more companies are increasingly developing solutions in ceramics.
Another reason for this slow adoption is that ceramics are often considered as “exotic” materials – ideal for products in the arts sector. One example that justifies this example, but still worth noting as it is an interesting development in materials, is Nanoe’s porcelain 3D printing filament.
On an industrial scale, I was glad to see the use of ceramic 3D printing in vertical industries such as energy where the technology has proved to be an ideal production candidate that could bring the hydrogen economy closer to effective implementation. My thoughts go here to companies like 3DCeram which has helped to develop an intricate optimization process encompassing printable feedstock Zr8Y, 3D printing parameters, and thermal treatments.
3. The Introduction of intriguing AM processes
There is always a startup that is working in stealth mode on some disruptive processes. In the short list of startups that turned stealth mode off this year, I would like to keep in mind Rosotics and Fabric8Labs.
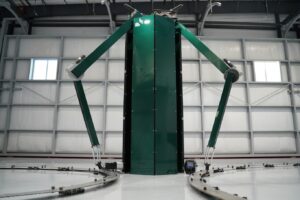
The former is working on a new way to print metals called “rapid induction printing.” This technique would make use of the conductive property of metal to generate heat from within the feedstock. The ultimate goal at the end of the process would be the creation of hardware that is a lot more efficient and simple and less dangerous for the people who operate it. Mantis, the company’s first completed 3D printer prototype is a huge, unfolding contraption capable of printing 45 kg of material per hour on the power from a standard 240V outlet.
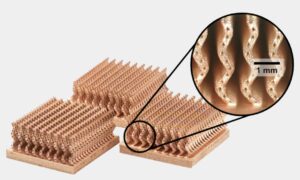
The latter is developing a technology called Electrochemical Additive Manufacturing short for ECAM. Fabric8Labs explains that its proprietary technology ECAM could produce pure copper components, which can be directly printed onto temperature-sensitive substrates such as PCBs, silicon, or existing metal components. Without using powder, neither wire nor lasers, the process can fabricate fully solid metal 3D printed parts. Its secret ingredient? Electroplating – a process that is often leveraged to provide a metallic coat to polymer 3D prints.
Both concepts are intriguing and have raised debates across the community. Beyond delivering on their promise, will they address the challenges of speed and mass production, existing industrial 3D printers have to cope with?
Another process that I would like you to keep in mind is the one of voxeljet. The company has a solid experience in sand 3D printing and knows how to deliver solutions that answer the needs of the foundry industry. Its Cold IOB (Inorganic Binding) 3D printing technology targets this specific industry again; it would enable molds and cores for the foundry industry to be produced from sand and an inorganic binder without the need for microwave treatment.
4. Multi-material 3D printing remains challenging but continues to gain attention
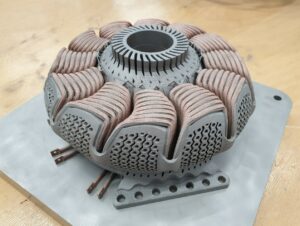
I have said it before. Multi-material 3D printing is one of the manufacturing techniques with the strongest unique selling proposition: using multiple materials at the same time to fabricate a part. Unfortunately, its adoption remains utopian for many users due to a range of limitations at the design, materials, and manufacturing levels. For instance, in FDM 3D printing, with a very complex design, the designer would have to change their materials several times to get to a definite part.
That being said, companies are still working on how to improve this approach and I am happy to see Lithoz as part of this small group. Apart from FDM, SLA, material jetting, binder jetting, DED, and powder-bed/SLS have often been mentioned as the types of AM technologies that could enable multi-material 3D printing. Lithoz is making new strides by exploring the combinations of ceramics-ceramics, and very soon polymer-ceramics or metal-ceramics with its new CeraFab Multi 2M30 3D printer.
Another company that seems to provide a viable solution here is Arburg with its APF high-resolution thermoplastic material jetting solution. According to Tomasz Taubert, this solution could handle two-material builds with soluble supports while delivering the best possible geometry.
I am also keen to discover new applications the Quantica’s NovoJet OPEN multi-material 3D printer will enable and Schaeffler AG, the new parent company of multi-material 3D printing expert Aerosint.
5. AI and ChatGPT are making their way in the Additive Manufacturing industry but should we trust them yet?
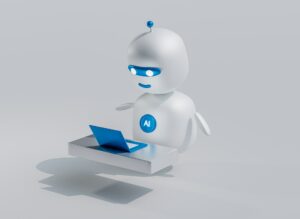
If the first three industrial revolutions were defined by breakthroughs in manufacturing processes, electricity and digital technology, today, we are at the threshold of the fourth industrial revolution, where AI and ChatGPT technology are positioned as the driving forces.
I am sure about a couple of things, AI enhances AM at multiple levels and I would like to highlight three examples here:
- Leveraging AI for analyzing operational data allows for preemptive equipment maintenance is undeniably an appropriate use. Predictive maintenance can help you reduce unplanned downtime while ensuring a smooth and more efficient manufacturing process.
- At the design level, by exploring a wide range of design variations, the technology can help produce a wide range of parts that are more efficient than those humanly conceptualized. However, in the very first edition of 3D ADEPT Mag of this year, we urged product designers to remain cautious. There are various forms of AI bias, and some of them can be detrimental. In addition to data and algorithmic bias (the latter sometimes reinforcing the former), AI is developed by humans — and humans are inherently biased. So, the challenge here goes beyond gender and race, to encompass people with disabilities. For the product designer leveraging AI-powered tools, it’s about daring to think broadly about world issues.
- At the manufacturing level, one applies AI, specifically machine learning, to capture a user’s knowledge, and leverage it to automate repetitive tasks. This integration would make more sense to me in a conventional manufacturing sector like sheet metal which requires mass manufacturing but in AM, where there is more interest in customization and personalized products, should we already bet on it?
This year also saw the introduction 3DGPT, a ChatGPT concept for AM. The concept might definitely seduce more than just investors, but I am still questioning its credibility in an AM industry that is still trying to define itself and its concepts.
6. An increasing focus on real-time inspection methods
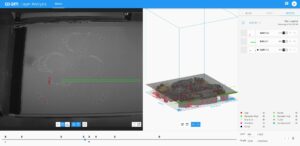
I will call this one a trend. Last year, in my “2022 Year in review” article, I mentioned Quality Assurance as one of the areas we should focus on to deliver 3D printed parts that meet specific industry criteria. I was glad to see a few developments here and there in the industry. It’s a pity that a lot of companies specializing in the field do not communicate more about their solutions and their capabilities but their lack of communication is playing to the strengths of the likes of Materialise, Phase3D and ZEISS that are working on solutions to improve this specific stage of the manufacturing process.
If there is something you should keep in mind here is that the new era of AM in-situ inspection goes beyond monitoring, to enable reduced part costs. As we are looking to each tool that could help reduce the overall production cost, I can only encourage AM users to sign up for this type of action.
7. The development of specific parameter marketplaces should continue
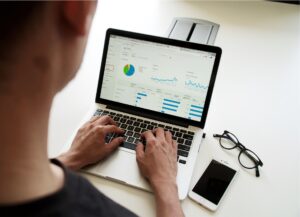
Entire libraries of material properties somehow propelled the adoption of casting for traditional processes. “In comparison, you only have a couple of boxes with AM. Trying to compete with that difference in material characterization is very difficult.” Throughout the year, this challenge has been one of the most shared limitations by AM users I have talked to (AM experts from Honeywell Aerospace are one of them). The good news is that since last year, companies like Rosswag have started developing a process parameter marketplace that aims to address this type of issue.
While it is only available for LPBF right now, it could be interesting to see the development of such marketplaces for other AM technologies.
8. Development of new materials
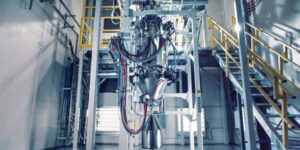
Given the importance of materials in the manufacturing value chain, and the gap that still needs to be filled to develop materials for specific AM processes, I don’t think we will ever see an end-of-year review without any new material developments.
Apart from qualification and certification of the most-used materials for LPBF metal processes, we’ve noticed that refractory metals such as tantalum debuted on the AM industry. With the ability to deliver implants with improved biocompatibility (reduced clotting) and stability, enhanced bone in-growth, tolerable to higher stress, tantalum’s benefits should lower the rate of surgery revisions. Its use in AM is relatively new and I hope we will see more applications of this material next year.
On another note, with the growing environmental concerns, I can’t help but recognize the efforts of some material producers in the field. We have closely followed the work of Evonik this year which has enabled us to discover the steps that still need to be taken in material producers’ sustainability journey. Looking at material developments with this topic in mind, we witnessed the development of bio-based materials for some applications and something tells me that this type of development will continue next year.
9. Adoption is different from one continent to another
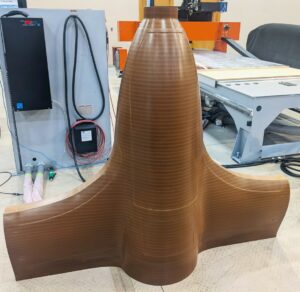
I tried to compare the different coverages we’ve done this year in AM trade shows we attended in the US and in Europe and I assessed the different conversations we had with industry insiders. I discovered for instance that the new Cut Layer Additive from Thermwood is gaining traction in the USA whereas industrials are not yet interested in this technology in Europe. In Europe, the main interest remains LSAM.
On another note, with most American adopters or potential users of AM, the experience with AM technology is always explained in comparison with some conventional manufacturing technologies whereas with European AM users, the focus is directly on their experience with the technology itself, and how they feel about it.
While the USA and Europe remain the largest adopters, the APAC region is transforming into the fastest-growing AM market. It will come as no surprise that China is the biggest force behind the growth of AM on the continent with machine manufacturers like BLT and Eplus3D trying to penetrate the European AM market. Interestingly, in this region, a user will come to AM after a thorough comparison between AM processes themselves – for instance between a metal AM and a polymer 3D printing application.
Overall, European AM technology providers often compare themselves to North American AM technology providers and vice-versa. They often forget that they have a different culture, thus a fundamentally different approach with AM.
10. AM remains expensive
Between the demand for more customized AM machines and the demand for more customized applications, AM has a cost that does not always satisfy everyone. The cost consideration will continue to raise debate within the industry, and somehow I believe I will be fine with that as long as speed, reliability and repeatability are met.
What about you? What have been your key highlights of 2023?
Discover Part 1 of our 2023 review. This article has first been published in the November/December edition of 3D ADEPT Mag. Featured image: A variety of designs produced by Matthew Shomper. Credit: Matthew Shomper.