A few years ago, to understand how to “rethink design” while taking into account AM technologies’ capabilities, we discussed the transition from Design for Manufacturing (DfM) to Design for Additive Manufacturing (DfAM). The dossier we released discussed the real definition of DfAM and shed light on one thing: when performed well, designing for AM can truly increase the value of the part. Fast forward to today, one realizes that the DfAM toolbox continues to be a mystery for many engineers and designers, and one reason that may explain this enigma is the fact that this toolbox is most of the time limited to two principles: Generative Design & Topology Optimization.
The article below aims to serve as an entry point to help designers and engineers understand the different design tools included in the DfAM toolbox, the ones that can enable production and industrialization (strengths and limitations), as well as the ones we should keep on our radar as the field continues to progress. Moving forward, each design tool will be discussed in an in-depth way in dedicated articles.
So, yes, Generative Design (GD) & Topology Optimization (TO) are often the most highlighted design techniques when it comes to designing for AM. According to Tim W. Simpson, Professor of Mechanical Engineering and Industrial Engineering, Pennsylvania State University, this can be explained by the fact they “have been around the longest and often show immediate benefits in terms of saving weight and increasing value when using AM.” The truth is, since AM is a technology whose history is still in the making, there are many concepts that are not universally standardized – and DfAM is one of them. That’s the reason why a thorough understanding of each concept needs a combination of insights from both academia and industry.
In this specific case, we have decided to rely on Tim Simpson’s expertise as he has one of the most published academic papers and presentations that focus on DfAM.
According to our expert, other techniques include:
- Lattice structures, a way to reduce weight or increase stiffness. This is often referred to as “design for multiscale structures” such as lattice or cellular structures
- Bio-inspiration, an approach that is often equated with generative design algorithms, but much broader.
- Part consolidation or “unitization”, used to save weight and assembly costs, while increasing the structural integrity of an AM part.
- Conversely, one can also use AM to make intentionally porous structures, which offer many benefits when it comes to fluids and thermal management, for example.
- AI that enables all sorts of new computational approaches when it comes to DFAM.
“Good old-fashioned “smart” design can also go a long way when it comes to DFAM. We have become so accustomed to designing parts in CAD, that we tend to limit ourselves to what is easy to do in CAD: move in X, Y, Z dimensions, extrude, sweep, revolve, etc. AM frees you from those constraints, which requires freeing your mind from how one often thinks when creating a model in CAD, which often involves subtracting material away from larger geometries that are combined to make complex shapes. In short, designers need to think “inside out” versus “outside in” when using CAD for AM. This is one way to start changing one’s mindset for AM, which is really what the generative design and AI do – inspire designers to think differently about how to create unique geometries that can now be made with AM”, Prof. Simpson adds.
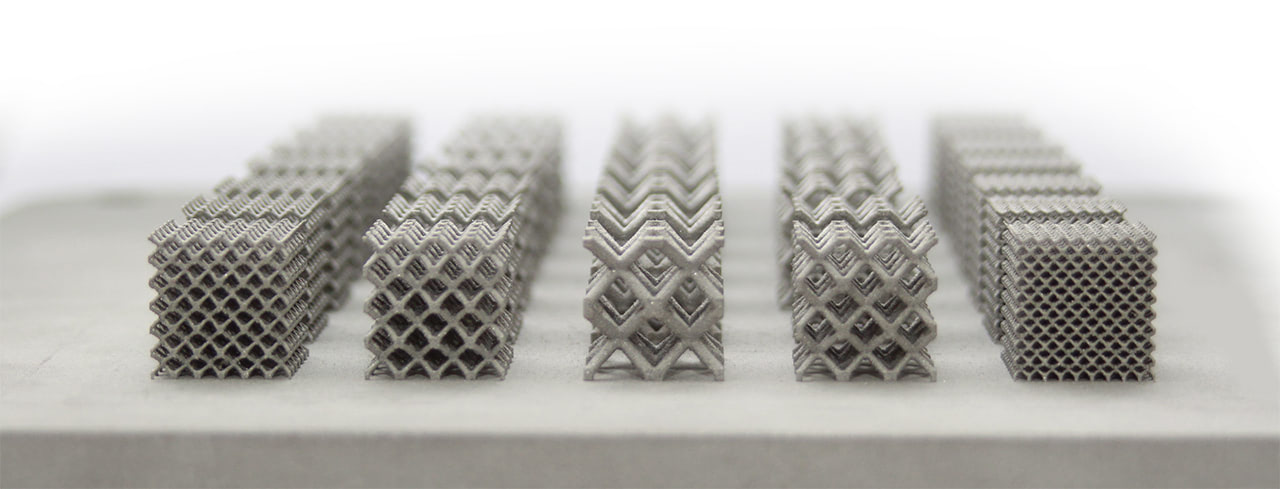
Apart from these tools, many experts often consider mass customization a design technique. If it is not a method per se, we believe it is counted as one because producing a different mold for each demanded product adjustment usually requires a lot of time, but this time is shortened with an easy-to-modify 3D file that enables customization.
That being said, whatever method they choose, the designer will always keep in mind the form, function, aesthetics, and now, increasingly, the sustainability elements of a product design.
Design strategies vs Design techniques
It’s pointless to know all these design techniques if you don’t know where and how to use each of them. Needless to say, the choice of a design technique, first and foremost, requires a thorough understanding of the design process steps: the component design, the part design and the process design.

To support the decision-making regarding which products or components should be manufactured using AM, research from /a study by Christoph Klahn, Head of the Design for New Technologies group at ETH Product Development Group, mentions four points where AM creates possibilities to add value to the product compared to conventional manufacturing methods.
The first one is integrated design, where the focus is on reducing the number of parts in the system. The second is the availability for individualization of products or components. The third point is that the manufacturing method enables a more lightweight design compared to conventional manufacturing. The fourth is the possibility to create more efficient designs, based on the fact that a more complex part is not more expensive to manufacture than a simple part.
To these items, Klahn adds the business case perspective which can be driven by manufacturing (fast production, potential customization, with no need for specific tools or molds – therefore the possibility to change the manufacturing process in other product development stages) or function (take full advantage of the freeform of design offered by AM; may be locked to a specific AM technique and maybe even a specific machine.)
In addition to helping choose the ideal design strategy one may follow for a given application, they also help to decide which design tools one should use. To this, Prof. Tim W. Simpson responds:
“Unfortunately, the design tools and techniques are often limited—or dictated—by what software is approved for use within a company. There are countless start-ups and cloud-based software tools, for instance, that are now available for DFAM, but they often aren’t on the approval list or can’t be accessed through a corporate firewall. Students and academics have a lot more flexibility and freedom in what they can use, which may eventually help to transform what DFAM tools and software are used in the industry.
The impact of any design technique is evaluated in terms of how effectively and efficiently the software can help designers engineer a solution that meets the requirements, which still exist for anything that is being designed, no matter how it is being manufactured. So, finding lighter weight designs, for instance, may be a basis for comparing two solutions, provided all other requirements are satisfied.”
Key specifications of design methods
Let’s make something clear: this part of the article does not ambition to say that a specific design technique is better than the other. However, the more one analyzes the manufacturing process of 3D printed parts, the more one realizes that certain advantages can play to the strengths of some design techniques depending on whether they help the 3D printed part deliver an economic, ecological or experience value.
For example, TO is a technique primarily used for lightweighting the design of structural parts (à experience/functional value). This means it can help to create one design that’s been optimized for structural integrity based on existing criteria, whereas GD can help to create several designs in an evolutionary way.
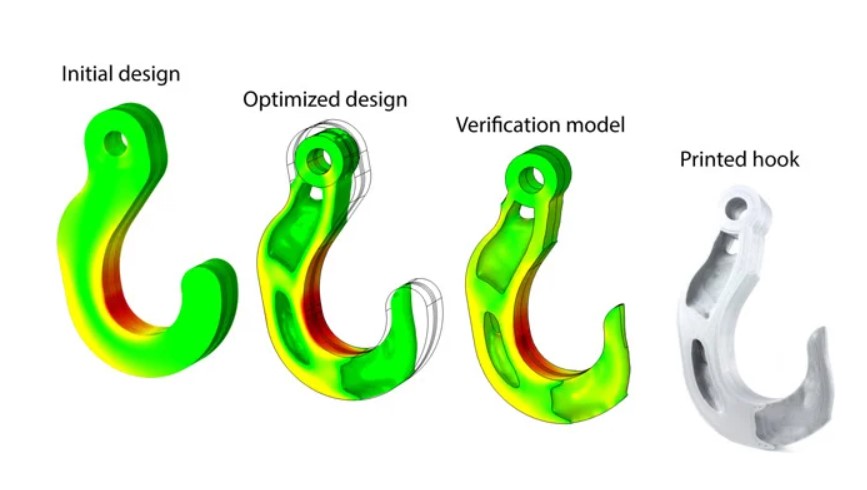
“Topology optimization tools certainly have a leg up, given how long these software tools and algorithms have been around. Generative design tools are quickly catching up, and we are seeing a lot more lattice-based designs now given the availability of better software tools to generate complex lattice geometries. AI-based tools are starting to explode around us, and we will certainly see all sorts of novel approaches coming in the next 2-3 years.
At the end of the day, the AM part has to satisfy the requirements and be more cost-effective than any other manufacturing options; otherwise, why would a company want to use AM? Granted, there are many ways for an AM part to be more cost-effective, beyond just a head-to-head comparison of material and manufacturing costs, but this remains central to enabling the production and industrialization of AM parts and products, Prof. Tim W. Simpson outlines.
On another note, computational design (which includes parametric design, generative design, and algorithmic design) is increasingly evolving as standards are established within the field. However, keep in mind what Matthew Shomper told us in the March/April edition of 3D ADEPT Mag (Software segment | pp -35-36): “Computational design is a great enabler of complex structures. […But it is] not for the faint of heart. The tools are rather inaccessible (with large learning curves) and it usually requires a dual knowledge of designing for requirements and aesthetics at the same time.”
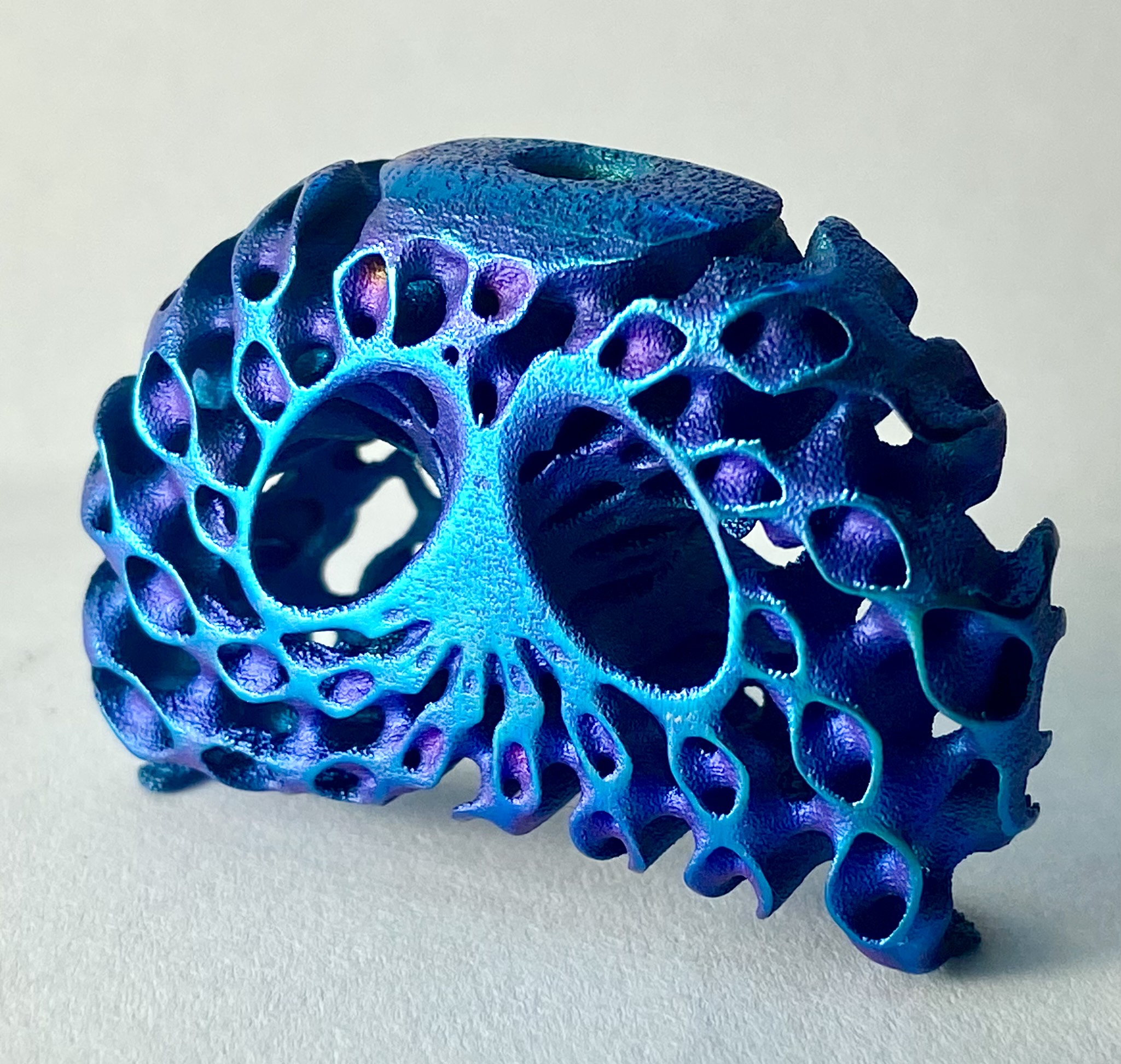
According to Simpson, the problem here lies in the fact that confidence in the results and the supporting analysis outcomes remain challenging for many companies. For instance, it is very easy to generate complex lattice structures with some of the new software tools, but analyzing the lattices with sufficient accuracy to understand how they may fail in practice increases uncertainty and therefore risk, which can often derail a project. Likewise, differences in the as-printed part from the as-designed part can lead to uncertainty and further increase perceptions of risk when it comes to AM. Finally, a lack of understanding and awareness of what AM is now capable of may lead to resistance to using AM and any computational design tools.
Lastly, any design technique powered by AI will raise a number of questions to date. As we increasingly witness a number of solutions powered by AI, it’s fair to say that we are gradually moving from an era of Design for AM to Design for AI. While most designers are still trying to assess the good and the bad of these techniques, the current reality shows that AI can help design an AM part faster and better than a human designer. And for Prof. Simpson, “the real win will be combining the two into hybrid approaches that leverage what humans do well with what AI and computational design algorithms can do well.”
This dossier has first been published in the May/June edition of 3D ADEPT Mag.