It is hard to recall that there was a time when we only talked about “Design for Manufacturing” (DfM). The concept of “Design for Additive Manufacturing” (DfAM) has emerged so fast that it seems to be on everybody’s lip. Prominent AM companies do not only talk about it. Just like universities, they also launch courses dedicated to DfAM. Indeed, design is the primary step required to take a product idea and translate it into something that can be brought to life.
It is, therefore, crucial for companies to master this stage of product development.
Given the increasing demand for such expertise, and the lack of reliable resources, we have decided to address this topic in this Software Segment.
With the development of new materials and the rise of manufacturing requirements, the concept of “Design for Manufacturing” has led to the development of new concepts and techniques to achieve more sustainable products. However, the emergence of AM technologies has also brought its array of challenges, that are beyond the well-known conventional concept. Therefore, to understand how to “rethink design” while taking into account AM technologies capabilities, there is a need to understand this transition from DfM to DfAM. A transition that inevitably raises the question of the real definition of DfAM: how should designers understand it? Are there specific principles they should follow when designing for AM? Moreover, in this quest for continuous improvement, how do we increase part value through the DfAM concept?
We believe answering these questions will be helpful to beginners and experienced engineers alike. This article also aims to be an introductory guide for companies that are interested in starting or improving their experience in AM.
Il would have been hard to discuss this topic alone or just with researches’ results as examples. To combine theory with practice, three companies joined us in this initiative: Materialise, nTopology and Blueprint. A detailed presentation of their core business will be given at the end of this dossier.
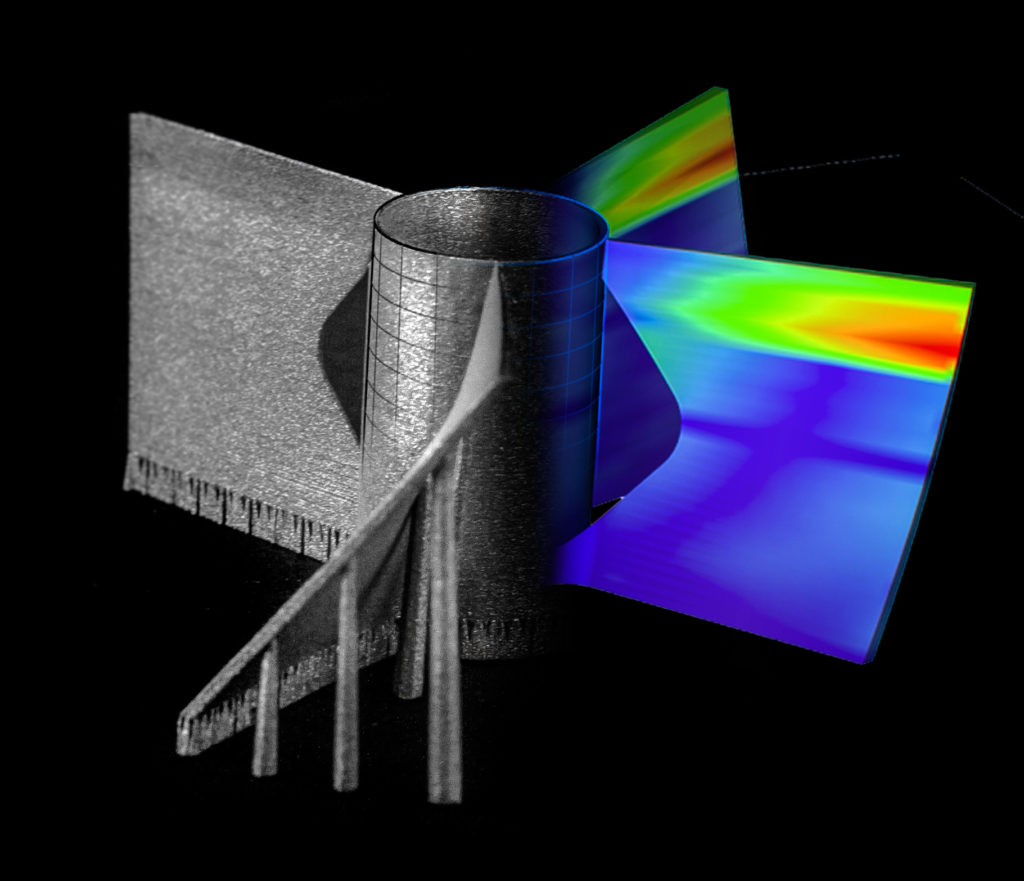
Transition from DfM to DfAM
Let’s first try to explain what both concepts mean.
Design for Manufacturing should not be a new concept for most people that will read this paper. As a reminder, the concept refers to designing a product while considering manufacturing knowledge throughout the product development process.
Design for AM, on the other hand, refers to a set of design methods or tools whereby functional performance and/or other key product life-cycle considerations such as manufacturability, reliability, and cost can be optimized to leverage the full capabilities of additive manufacturing technologies.
In other terms, to take full advantage of AM capabilities, DFAM methods or tools are needed. However, it does not mean that the concept is separated from the broader techniques of DfM. The manufacturing of some parts, sometimes require to leverage both additive and subtractive processes.
Furthermore, after further analysis, we can even say that both concepts somehow share the same goal: reduce manufacturing cost and improve product quality by addressing the manufacturing constraints.
According to Loic Le Merlus, Consulting Manager at Blueprint, “when you design a part, you typically design for functionality, then figure out how to manufacture it. This often means changing geometries or even splitting a single part into several parts to be manufactured with different methods. Although you still need to design for manufacturability, AM can allow you to produce geometries closer to your design intent and can allow different optimisations than traditional methods. AM is a great tool for consolidating assemblies, reducing part sizes and weight, and creating prototypes close to the intended functionality.”
If functionality is a crucial goal when you design for AM, it should be noted that AM technologies are very different from conventional technologies. AM technologies for instance take into account different parameters that are not considered when designing for manufacturability, and sometimes, people do not take into account these differences at the level of design. That’s exactly what Stijn De Rijck, Director Training and Consultancy at Materialise explains:
“Every design is created with a specific combination of material and production technology in mind, and that is not different for AM technologies. A mistake that is often made is to take a product that was designed for a given conventional technology and try to print it, for instance, as a spare part, without changing the design. There is an obvious chance that it will not optimally function or that production cost will rise significantly. If such sub-optimal design is used as the basis for a cost-comparison, you can be sure AM will lose the battle. But turn this around: what if you take a design that is optimized for AM and try to make it with a mould or through milling? A complex shape that is a piece of cake for AM, for instance, will create serious challenges in conventional technologies.”
nTopology’s CEO and founder Bradley Rothenberg agrees with Stijn De Rijck regarding this point. Indeed, in DfM, engineers should address the issue of optimum design that is required by various applications. In other terms, they should continuously look for the best compromise between the size, shape or topology of a part and utilization of as minimum as possible material while ensuring the overall performance of the part. Those issues are addressed in the DfAM concept. Rothenberg takes the example of challenges materials might raise in a production process, to point out the differences between the two concepts and the type of parameters that should be taken into account when designing for AM:
“The requirements that the design must fulfil are very different — in fact even amongst conventional manufacturing constraints they can vary greatly — For subtractive manufacturing, the requirements for a 5-axis CNC part vs even 3-Axis will produce a part that might look totally different. There is also, of course, the cost aspect that one has to look into.
You can think of the design as the result of putting material in the best place that is balancing a number of requirements, so the final shape of a part, or what the part looks like, is a result of balancing the things that are important: cost, weight, manufacturing process, even aesthetics could be taken into account. When designing a part for AM, the geometric requirements are generally more free because you are building the part up from raw material (additive) instead of starting with a block and chipping away at it.
Also, parts designed for AM can take an architected materials approach if the design software is capable.”
Our three experts in this dossier made it clear: when you design for a specific technology, you have different requirements to meet. Despite their common goals, both DfM and DfAM leverage different techniques and it makes sense when we know that the challenges of one lead to the development of the other.
DfAM: tools and impact on the part
You know you are designing for AM when your methods/tools make you take into consideration topology optimisation, design for multiscale structures (lattice or cellular structures), multi-material design, mass customization or part consolidation. This list is not exhaustive since other tools can be added based on the AM technology used for a specific production.
In this vein, the first step for designers is to keep in mind the capabilities of AM: shape complexity, material complexity, functional complexity and hierarchical complexity.
As far as shape complexity is concerned, AM enables to “build near net shape, complex shape geometry and interconnected internal channels.”
“AM has sort of flipped the relationship of software & hardware on its head — it used to be that you could come up with shapes in the computer that would be impossible to make (for example topology optimisation was popular amongst academics 30 years ago, but didn’t really make it to industrial uses until recently). Today, the manufacturing process is capable of making shapes that the current standard of design tools are not capable of representing. This is because those tools were designed at a time when drawings and traditional manufacturing were the paradigm”, explains nTopology’s Rothenberg.
Materials, on the other hand, are quite complex. They raise many issues with regards to their properties, the amount used and even the type of AM technology used. Depending on the object to produce or the technology leveraged, they can be processed one point at a time as a single material or as an alloy. In fact, sometimes the aim is to observe their properties in different locations of a single part hence the need to be able to alter their physical, chemical, biochemical or mechanical properties locally.
“Unlike subtractive manufacturing where removing material is expensive, with AM, adding material is expensive. You also have the added complexity of support structure. The more material and support structure your part contains, the longer it takes to build. Tools like topology optimisation can generate highly-optimized organic shapes, but often at the cost of requiring more support structure. Surface roughness is another limitation, but this can be mitigated with clever design. A designer can re-orient a part to reduce roughness on critical faces, avoid certain angles, or even add texturing to hide surface imperfections”, explains Blueprint’s Loic Le Merlus.
The functional aspect that AM allows has already been mentioned earlier by Le Merlus. Operators can produce fully functional devices in one build as the technology enables consolidation of parts. It is also possible to produce parts separately. In that case, their assembly does not present much challenges.
As for the hierarchical complexity, researchers from the University of Stavanger in Norway explain that features can be designed with complex shapes across multiple size scales. Internal structure, for instance, can be changed using cellular structures including honeycombs, foams, or even lattices, to fill certain regions of a geometry. This increases a part’s strength to weight or stiffness to weight ratio, so that excess use of materials is avoided; thus cost is saved.
Reality shows that it is interesting to know all these unique capabilities of AM. They are certainly a great help for engineers that want to design for AM. However, for Materialise, something more valuable is also important when it comes to DfAM: experience and creativity. As per the words of Stijn De Rijck:
“Design engineers are trained to deal with the limitations of conventional production technologies. Thinking in limitations instead of opportunities leads to limited use of the design freedom of Additive manufacturing. You need to build up experience and use your creativity to look beyond the limitations, and start to make use of the real strengths of the technologies. Take the example of the midsole we created with Adidas in the Futurecraft project: at the time we had no AM material available that was soft enough to create the right cushioning in the midsole, so at first sight, we would never reach the requirements for optimal performance. But instead of getting blocked by that limitation, we created a structure that changed the part flexibility and as a bonus, we also reduced the weight of the running shoe significantly.”
These capabilities are interesting to keep in mind. But what happened when different AM processes are involved?
Impact
We looked at the impact “Designing for AM” can have at two levels: the first one consists in knowing if the concept is the same for different processes and the second one consists in determining the impact on the part.
When different processes are involved
Our experts shared different views regarding DfAM and AM processes. When asked if the design remains the same whatever the AM process is, Blueprint, for instance, said it depends on some conditions:
“For simple parts that haven’t been optimized to a particular AM process, yes. If you are just looking to print a one-off part, then it often does not make sense to optimize for a process. But there are a lot of different AM processes, each with different materials and mechanical properties.
If you want to start using AM as a production technology then, like with every other manufacturing technology, you should spend the time, resources, and energy to make sure your part is optimized for the exact manufacturing process you are using. This is how you get the cost and business benefits of the technology.”
nTopology, on the other hand, remains categorical. For the spokesperson, the design does not remain the same whatever the AM process is:
“No, each process has different requirements — you might have heard of terms like “support structures” or “laser toolpaths” or “bead diameter” — there are many new design variables, or things that can be changed that affect the output and quality of the part. Understanding these variables and the limitations on them will produce in some cases variations on the same design (like using a different machine but with the same process). For example, building on two different industrial-scale polymer FDM machines, or an entirely new design or, as another example, building two metal parts using binder jet vs laser powder-bed fusion. Each AM process makes more sense for some parts and not others, depending on the requirements of the part, [if you need 10K parts for example, or if you really need high-quality material properties for strength].”
Materialise on its side presents a balance between the two arguments. For the company’s expert, “AM is a group of production technologies that have the basic principles in common, but each of them has its characteristics, possibilities and design rules.”
It is important to note that different technologies require different optimisation techniques. We understand our experts’ thoroughness regarding this point. Indeed, the path the operator chooses to implement AM will determine how a great tool the technology can be in a given project.
For instance, for some people, AM just replaces traditional processes. This might be true, but it is not enough as people need to be able to leverage all tools to improve manufacturing aid functionality and cost. So, if an engineer takes an existing part that he designs and simply prints it off, he will certainly get his part, but one that has not been optimized. It is, therefore, very likely that he can’t make the most of it. That’s a poor way to deploy AM, which brings us to our next part, the impact on part quality.
Part quality
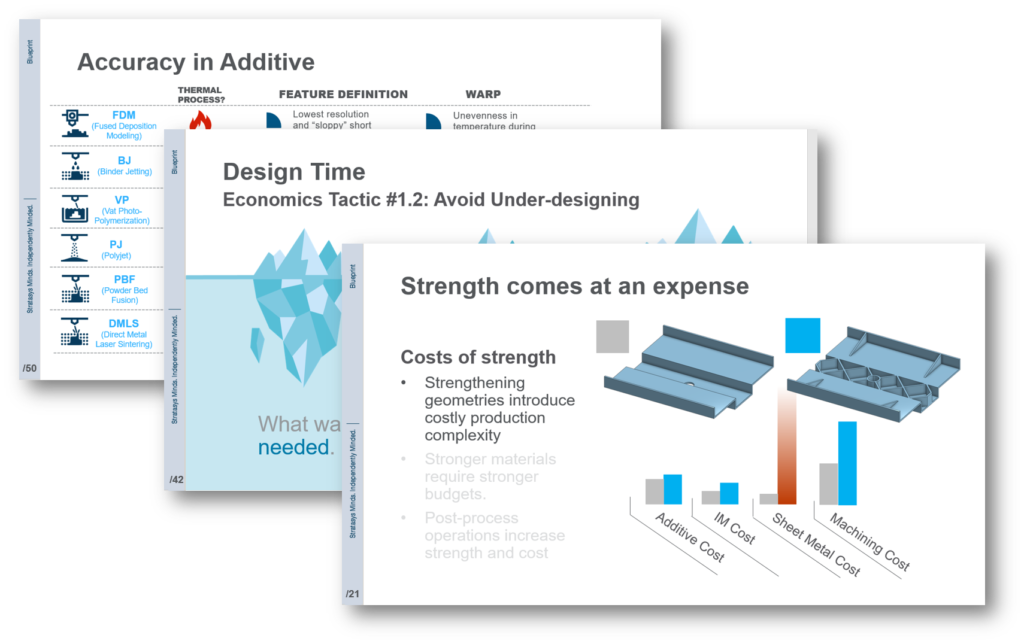
What’s the impact of designing for AM on the part? That’s a crucial question because in the end, the most important is the result, the part value. If it is a success, then everybody is happy. If it is not, it is a waste of time and money. Answering this question inevitably raises the question of intelligent optimisation. Is intelligent optimisation a synonym of topology optimisation? What does it really mean?
The Consulting Manager at Blueprint outlines the distinction between the two terms:
“Software that can create highly optimized structures isn’t necessarily intelligent; it could be like your car’s navigation system, following a human-defined algorithm, to produce a result based on initial inputs. A more accurate label would be “algorithmic optimisation.” This can encompass all optimisation methodologies including topological, generative, and structural. Furthermore, the geometry generated from such an algorithm doesn’t necessarily ensure the manufacturability of the part. The intelligence still resides with the designer who sets the starting parameters or boundary conditions and then must interpret, approve, and sometimes tweak the output of that algorithmic process to ensure the design meets requirements and is manufacturable.”
The CEO of nTopology this time, agrees with Blueprint. The founder explains that topology optimisation can be a part of an “intelligent optimisation”: “I would define intelligent optimisation” as a workflow, or process that captures engineering intent within it in order to make a better part faster. This can be a manual process, a hybrid of some manual & some algorithmic, or fully algorithmic. Ideally, the inputs would be defined, and if changed you get a new output, a new part. Topology optimisation can be one component of an “intelligent optimisation.”
Intelligent optimisation, therefore, lies in the ability to create a “smart” design and make it work perfectly on an AM system. As De Rijck said while warning designers: “One thing is to create an intelligent design, the other thing is to prepare parts for successful building in AM. You should consider this build preparation work to be a design process as well. Take for instance metal 3D printing: each component that goes on a metal AM machine needs to be printed with a support structure to anchor the part to the build platform and to control the heat dissipation. The ideal support structure is strong enough to anchor the part, but very light, so it does not consume valuable machine time and material. Searching for the optimal combination is a daily challenge if you run a metal machine in AM.”
In the end, the impact of the DfAM” concept is huge. As per the words of Rothenberg, “it’s bigger than any of us thinks.” It looks like we are just at the beginning of a big chapter in the engineering software industry. The DfAM concept involves new tools and new ways to increase part value while taking into account materials and hardware. In terms of part quality, we do not only talk about higher performing parts anymore, but, according to Rothenberg, we also talk about the speed that these new parts can be iterated on.
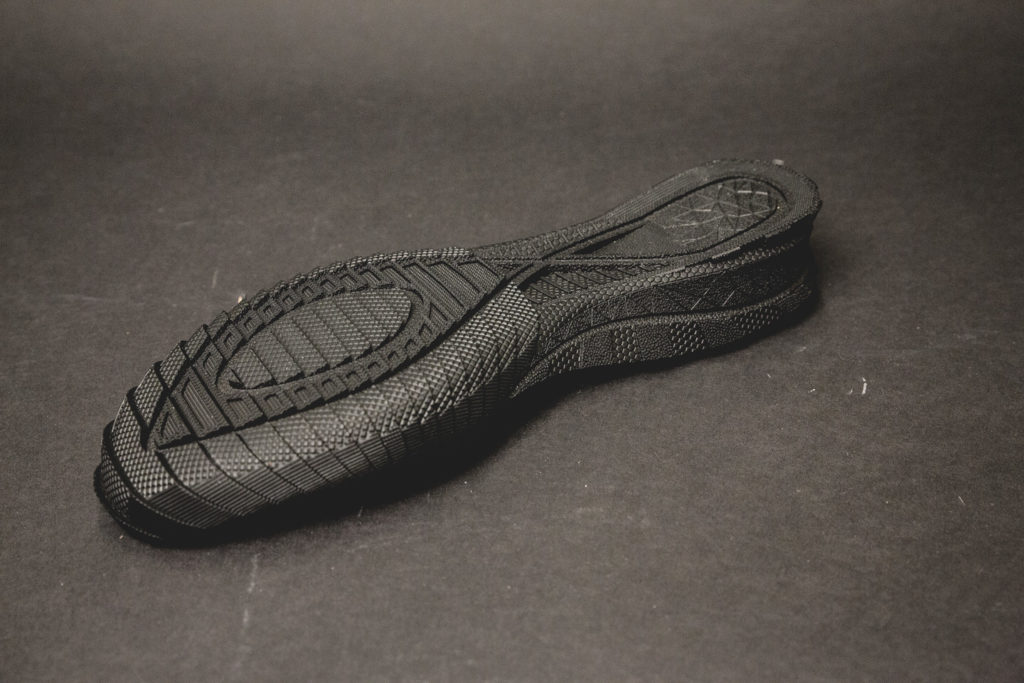
Future prospects
Even though there is still room for improvement, the toolbox designers used for traditional manufacturing does not raise much questions. In general, everything is integrated into their design environment.
In the additive manufacturing industry, there is still a long road ahead. Software companies and consultants are certainly here to guide and advise but a fast learning curve begins by the willingness of the user. In the meantime, to drive the adoption of MA into production lines, our experts share the current focus of companies:
“The data exchange between AM machines and ERP systems needs to be improved. Nowadays, companies want to know what is happening on the manufacturing floor all the time to identify problems and bottlenecks as fast as possible. AM is still too much of a black box to get all the required production intelligence”, said Blueprint.
What nTopology hears the “most often as barriers to wider adoption are: the need for more automation in design process (DOEs, etc.); STL files introducing uncertainty into the build process and causing data handling and build crash issues; part complexity making design process really long or really difficult and, in general, existing design software holding back engineers from optimizing parts to take full advantage of AM processes.”
For Materialise, connectivity is the key issue to tackle. “Connecting additive manufacturing into manufacturing setups, linking it to other technologies and business systems, is allowing fast-growing applications to grow even more rapidly. It allows scaling and fast adoption and it allows to combine technologies and software systems to get the best of all worlds in one production flow. Next to state-of-art software, in-depth knowledge of the AM-specific process, the adoption of industry standards like MT Connect & OPC-UA and last but not least access into a broad network of partnerships and collaborations, are crucial to turn Additive Manufacturing into a widely trusted manufacturing technology and create applications that open up new possibilities.”
This dossier has originally been published in the October-November Issue of 3D ADEPT Mag. During the Additive-Talks Day, Materialise will be discussing another crucial topic for operators “Make It Worthwhile: How To Increase Efficiency In The Printing Process?” – Make sure you save your seat now.
A few notes on the participating companies
Blueprint, Materialise and nTopology joined us to address this issue of our Software segment. If you do not know them yet, the notes below might enable you to understand the reasons why we invited them.
Blueprint
Blueprint is a Stratasys company that provides companies with strategic, operational and applications consulting that help them to navigate the additive manufacturing world. The company first appeared on our radar when they launched its “Think Additively program” but it traces its beginnings to early 2015 when Stratasys Services Group integrated the Econolyst team.
As part of this dossier, the company firmly believes that, “while there are software solutions to help with certain elements of design for additive, such as topology optimisation to minimize material, or simulation to predict deformation or defects, there isn’t a single, turnkey solution for all the steps in the design process. The human element is still very much at the heart of designing for AM. As an industry, [they] can build better tools, but [they] must teach people how to use them. Currently this skill shortage… the lack of knowledge of how to use the tools… is slowing down AM adoption.”
Materialise
It may be not necessary to introduce Materialise but we will do it again. The Belgian company brings three decades of 3D printing experience into a range of software solutions and 3D printing services for medical and manufacturing. To help companies to make the most of AM, the company recently entered a new phase of co-creation with companies that collaborate with them.
Several reasons raise Materialise’s interest in this topic:
- First, they guide companies through the design process, and make sure to tailor the knowledge transfer to the specific technology-material combination for their specific case.
- Secondly, they “have created software tools that help designers and manufacturers to cope with the specific needs of AM. Materialise 3-matic for instance, is a package that allows [users] to enhance [their] design by creating 3D textures on surfaces or lattice structures in volumes, [just to name a few examples]. With the scripting function in 3-matic [the user] can easily automate repetitive tasks, [and] focus on the more creative part of Design for AM. Materialise Magics is [a] software used to prepare parts for production. It helps [the user] choose the orientation of parts and guides [him] in designing smart support structures. The recent simulation module allows manufacturers to predict and thus avoid build failures, so there is significantly less down time with machines.”
nTopology
nTopology is a young entrant into this niche market. Founded in 2015, the company is significantly gaining momentum thanks to the ability of its generative design software to break the main barriers engineers currently overcome in manufacturing. With a total of $31 million raised to date, the company has recently expanded its reach into Europe with new office in Germany and plans to accelerate its growth with a focus on expanding its customer base.
The main features of the company’s software include lattice design, topology optimisation, and direct output to manufacturing, in other terms, no more unreliable STL files required to go from design to manufacturing. Furthermore, the company claims that modelling operations like unions, offsets, fillets are reliable and never fail.
With regards to this dossier, Rothenberg strongly believes that “the impact that [has] the ability to take an architected-materials approach to part design is game changing and it is the combination of AM hardware and nTop Platform software that makes this possible.”