Engineered materials company Uniformity Labs has qualified its ultra-low porosity 17-4PH stainless steel powder UniJet™ SS17-4PH for the Desktop Metal Production System™.
During the qualification on Desktop Metal’s Production System™, the physical and mechanical properties of UniJet™ 17-4PH powder were extensively evaluated. The uniform powder bed layering of UniJet™ 17-4PH delivers double the green strength and an average of 20% less shrinkage than other stainless-steel powders qualified for use with Desktop Metal’s Production System™. These factors, alongside the highest powder bed uniformity in the industry, mean far better-sintered part geometric accuracy and less breakage of green and brown parts during post-print handling and depowdering, resulting in high process yield at high throughput.
One of the key advantages of UniJet™ 17-4PH is its exceptional apparent and tapped densities, resulting in green parts with many more contact points between particles and higher density (10% reduction in relative porosity) than the standard binder jetting powders.
This allows for green parts with nearly twice the magnitude of transverse rupture strength across all layer thicknesses. Such green parts, alongside the very high flowability of Uniformity powder, make the fabrication of more complex thin-walled or heavier green parts with larger aspect ratios viable by minimizing breakage during de-powdering of large, high aspect ratio and geometrically complex parts with fine features and channels.
Uniformity’s UniJet™ 17-4PH powder on the Production System™ consistently achieved about 25% less shrinkage in X, 19% less shrinkage in Y, and almost 20% less shrinkage in Z axes than the standard binder jetting powder across all layer thicknesses. The powder repeatably delivers 99-100% final part density for best-in-class material properties. UniJetTM 17-4PH powder yielded parts with, on average, three times lower standard deviation in green density than standard binder jetting powder. This roughly translates into three times better absolute geometric tolerance in sintered parts fabricated from UniJetTM powder using Desktop Metal’s Production System™.
The highly flowable powder improves throughput by allowing repeatable fast layering at thicker layers. At 75um layer thickness and with 20% reduced shrinkage (more parts fit on the bed), a net throughput benefit of approximately 25% relative to standard binder jetting powders for Desktop Metal’s Production System™, thereby enabling substantial cost reduction for parts manufacturers to begin to plan for the adoption of metal AM at scale. At 110um layer thickness, still delivering all the beneficial improvements in green strength, uniformity of powder bed, and sintered density relative to standard inert gas-atomized binder jetting powders printing at 65um layer thickness, the throughput improvement is 80%+.
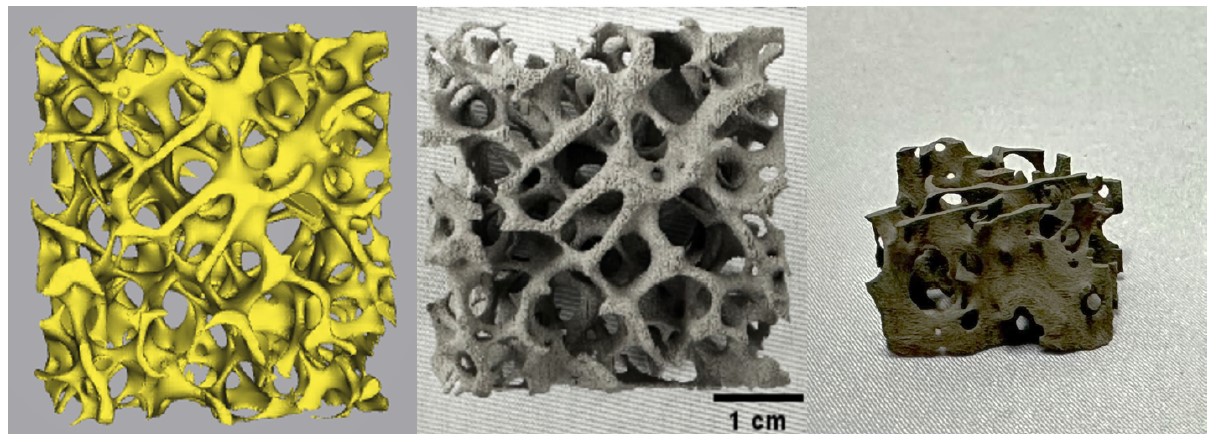
Green part BJT L25- didn’t survive de-powdering (Right)
Uniformity Labs previously qualified its UniFuse™ IN718 Nickel Alloy for laser powder bed fusion 3D printing.
Remember, you can post free of charge job opportunities in the AM Industry on 3D ADEPT Media or look for a job via our job board. Make sure to follow us on our social networks and subscribe to our weekly newsletter : Facebook, Twitter, LinkedIn & Instagram ! If you want to be featured in the next issue of our digital magazine or if you hear a story that needs to be heard, make sure to send it to contact@3dadept.com