Whether it is light or cheap, a 3D printed part delivers value when it performs well. The thing is, achieving that performance often begins and ends at the surface. Ensuring the right surface of the 3D printed part often comes down to the right post-processing task. In our efforts to demystify every post-processing task that can be used at the end of the additive production, we’ll focus on infiltration and coating processes in this article.
Remember that post-processing is an umbrella term that covers a variety of stages that 3D printed parts have to undergo before being used for their final purpose. No matter what post-processing stage the AM part needs to go through, the goal remains the same: removing the undesired properties that have been built in the final product during the additive manufacturing process.
Among the various post-processing tasks that can be performed on 3D printed parts, we already studied the use of furnaces, heat treatment, and metal powder removal in previous editions of 3D ADEPT Mag.
Interestingly or frustratingly, when it comes to infiltration and/or coating, what seems simple is yet indescribably complex. Infiltration and coating are often used interchangeably to signify the same process. Therefore, if you ask 5 experts to define or explain what they understand by infiltration or coating, there is a great chance you come up with five different meanings.
We did our homework, we talked to industry experts and conducted some research to clarify each of those terms and the way they should be utilized in an additive manufacturing production.
Coating
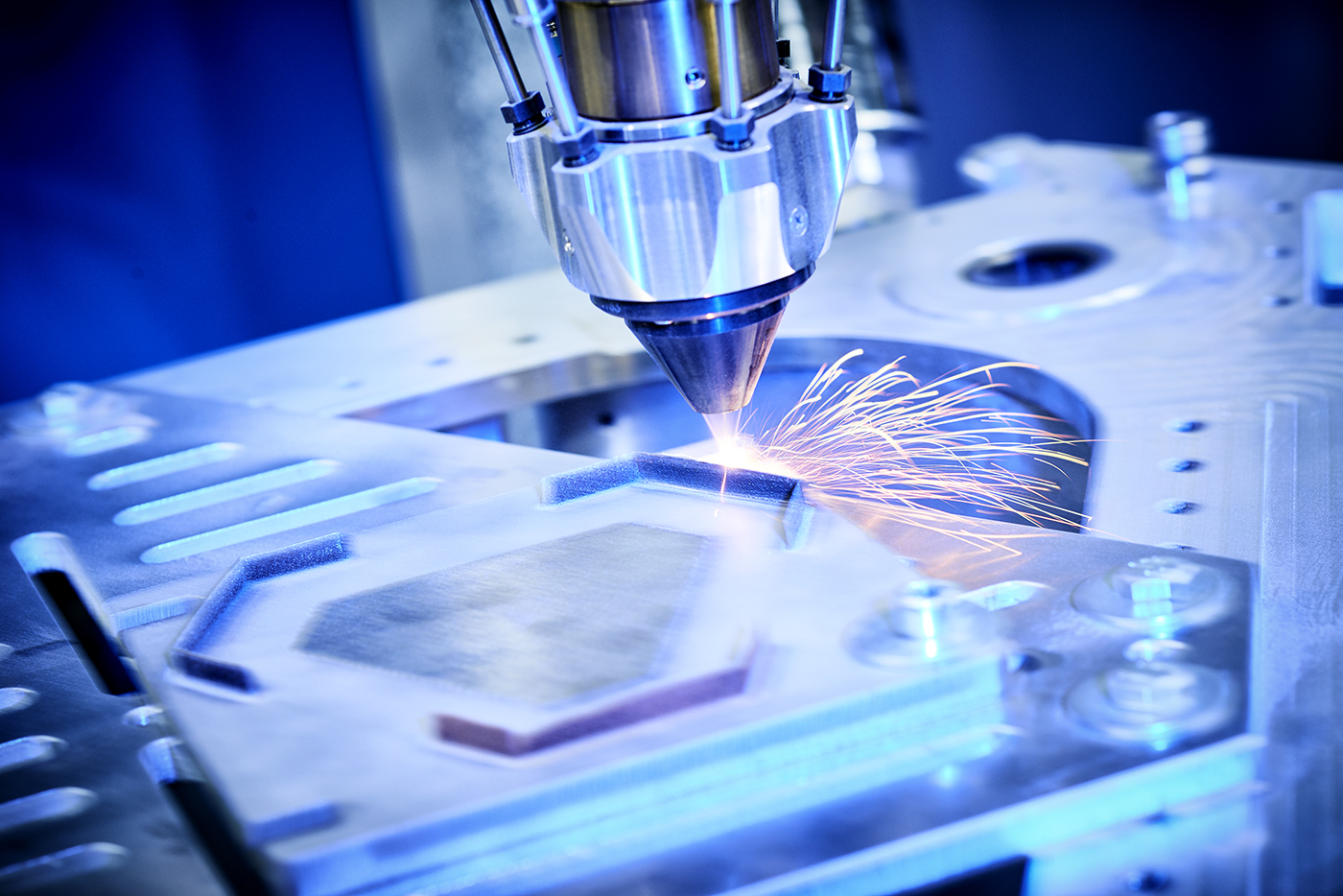
Coating is a word that is widely used in AM: Surface coatings, Additive Manufacturing Coatings, Coating for AM parts, Dry powder coating, Cold spray coating etc. Simply put, a coating is a layer of a substance added to a surface to provide protection and to enhance the appearance of the surface.
“According to our understanding, [it] is a manufacturing process to refine both conventionally and additively manufactured metal parts. The purpose of a coating is to protect a part from harms caused by the characteristics of its operating environment (e.g. high temperature, high humidity, presence of chemicals, mechanical stresses etc.)”, Dr. Ing. Tobias Stittgen, Managing Director at ponticon states. The machine manufacturer develops a technology that enables objects to be coated and printed at a fast pace. The company’s high-speed DED technology can be applied to coat any 3D printed metal component. Highest material flexibility is achieved by feeding the coating material through a nozzle, enabling application-tailored properties at unprecedented productivity.
In general, to refine metal parts, operators often apply a layer of material onto the substrate to enhance the parts’ surface properties. As Stittgen implies, choosing a coating often depends on what is affected in the operating environment. It also depends on life expectancy, substrate material compatibility, component shape and size, and obviously price.
Furthermore, while coating can be utilized with all metal-based AM processes, it should be noted that “protective properties are better achieved with materials that differ from the actual part’s material. As the coating materials are often high-value, manufacturing the entire part is economically unviable”, Stittgen notes.
In this vein, to help categorize the different types of coatings, operators often look at the way the coating material is deposited onto the substrate surface. Four methods of depositing the coating material have been identified: atomic deposition, particulate deposition and bulk coating or cladding. Each of these methods includes a wide range of sub-processes and are compatible with specific operations:
Atomic deposition | Electrolytic deposition | Physical vapour deposition (PVD) | Plasma deposition | Chemical vapour deposition (CVD) |
Particulate deposition | Thermal spraying | Impact plating | Enamelling | Electrophoresis |
Bulk coating or cladding | Painting and dipping | Laser cladding | Weld overlays | Roll bonding |
Surface modification | Anodising | Electrolytic conversion |
Table created by TWI Global.
On another note, surface modification methods used for metal AM include a lot more processes: shot peening, rolling sand blasting, laser surface treatment, friction stir processing, ultrasonic surface rolling heat treatment, cryogenic treatment or surface mechanical attrition treatment.
These methods are often the least highlighted in the additive manufacturing of a part – probably because some of them are still being explored at the research level. However, it is important that manufacturers keep track of their influence on the surface quality of AM components to better assess innovations at the production and performance levels.
Infiltration
Infiltration is one of those operations that is only performed with specific AM processes – in this case, binder jetting or laser sintering. Binder jetting is one of the AM processes that will mostly require this post-processing task though. After the printing process, Metal Binder Jetting parts often undergo an infiltration or a sintering process.

As explained in our dossier on the use of furnaces, during the sintering process, “green parts (a combination of metal powder and binder) are first heated to a temperature where the binder evolves and is removed from the parts. The furnace then ramps up to the sintering temperature of the metal which is just below the melting temperature of the material, fusing together the metal particles. After sintering is complete there is little or no evidence of the original powder particles, fabrication process and parts have very low porosity”.
As per the words of 3DEO’s CEO Matt Petros, infiltration comes into play for two main reasons: “the full densification is not possible solely through sintering and high-temperature sintering can introduce extreme dimensional distortion to the part – [the ultimate goal being to improve part density]”. In case you’re not familiar with them, 3DEO is a machine manufacturer and a parts producer that provides manufacturing services based on a proprietary Intelligent Layering® technology. We have been following the company for a couple of years now and their expertise has helped us understand more than once many of the rules AM breaks. In this specific case, 3DEO does not use infiltration as a consolidation step. In their process Intelligent Layering®, the parts are sintered to full density.
But, how does the infiltration process work?
Once the manufacturing is complete, the component is placed in a furnace where the binder is burnt out leaving voids. The part’s density will reduce to around 60%. The operator can thereafter fill the voids left behind with bronze or another low-melting-temperature metal until it reaches at least 90% density.
Speaking of a specific process named liquid-metal Infiltration which can be employed as a post-sintering step to produce a fully-dense part, 3DEO’s CEO explains that “after binder removal, a low temperature sintering step is performed to initiate necking of the metal particles. This lightly sintered part will act as a frame for the liquid-metal to fill. A lower melting-temperature infiltrant is melted and diffused into the porous network of the part via capillary action.”

One of the advantages of this process, according to Petros, is the fact that one avoids “extreme dimensional distortions in the part after high-temperature sintering. Any open pores within the part are filled, bolstering its mechanical properties and structural integrity.”
Moreover, infiltrated parts are relatively strong and have good mechanical properties, but they will be around 2% smaller after infiltration.
“One of the biggest drawbacks of infiltration is the heterogeneous nature of infiltrated metal parts. Infiltrated metal parts will exhibit properties that are difficult to predict due to the part being a composite of two different materials. Other disadvantages include increased processing time due to the additional steps required for infiltration” Petros adds.
Those who would like to explore other methods of densification to full density can go for a sintering additive. According to Petros, the latter can help to sinter particles at a lower temperature while maintaining dimensional accuracy. “Hot Isostatic Pressing (HIP) is another popular consolidation process to achieve almost theoretical density”, he notes.
While infiltration is mostly highlighted in the manufacturing of parts through metal binder jetting, it should be noted that this post-processing step has a different meaning and understanding for those working with SLS 3D printing.
For these part producers, infiltration enables a better surface protection and gives more “stability” to the 3D printed parts. The parts are therefore protected from contaminants because they are more resistant to pressure, and waterproof.
Tracy Beard from 3D printing service bureau Quickparts explains that this post-processing method is mainly used to seal or color SLS parts. To do so, they use a vacuum impregnation process when parts need to be watertight. When a color other than the natural color of the SLS powder is required, they infiltrate or impregnate the parts with dye.
The infiltration process continues to be studied in conjunction with various thermal treatments to increase the strength and decrease the volatile content of the parts. Just like we saw with coating, highlighting their influence on the surface quality of AM components will help to better assess innovations at the production and performance levels.
This article has first been produced in the January/February edition of 3D ADEPT Mag.
Remember, you can post free of charge job opportunities in the AM Industry on 3D ADEPT Media or look for a job via our job board. Make sure to follow us on our social networks and subscribe to our weekly newsletter : Facebook, Twitter, LinkedIn & Instagram ! If you want to be featured in the next issue of our digital magazine or if you hear a story that needs to be heard, make sure to send it to contact@3dadept.com