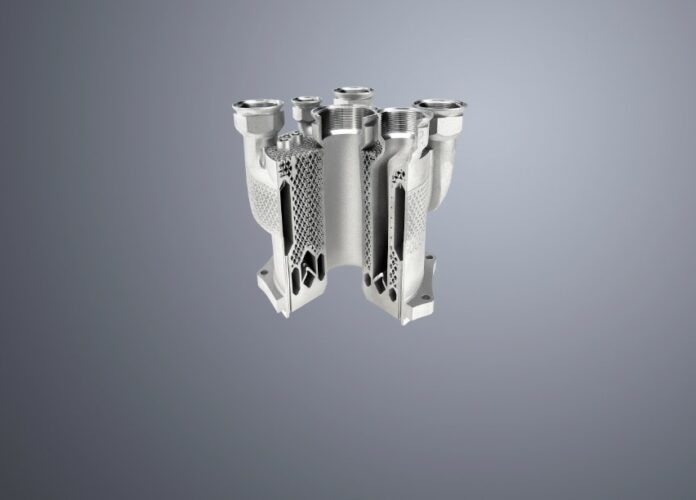
Machine manufacturer TRUMPF has focused its presence at Formnext on helping organizations find “the right solution for every metal AM application”. Whether you were looking to achieve a specific application, buy a 3D printer, or consulting services, the company ambitioned to highlight all the resources that can be deployed to foster digital connectivity in manufacturing.
As 3D ADEPT Media mainly focused on discovering applications that enable to deliver on AM’s promise, one of the parts that raised our interest in the show was a 3D printed pure copper radio frequency quadrupole achieved as part of the I.FAST project coordinated by CERN.
You may probably want to hear 3D ADEPT Media Managing Editor’s conversation with Severin Luzius, Application, Materials and Consulting AM expert at TRUMPF.
However, as far as materials and technology processes are concerned, TRUMPF highlighted a range of new materials that can now be processed on its systems. These materials include for instance titanium 6242, the CustAlloy aluminum alloy, the Printdur HSA alloy as well as the M789 AMPO tool steel. These materials can be used across the medical, aerospace and automotive industries.
Speaking of the titanium 6242, Jan Christian Schauer, materials expert for additive manufacturing at TRUMPF, said it should not displace the top dog, titanium 64. “At room temperature, titanium 64 and titanium 6242 behave very similarly. But at higher operating temperatures of 300 degrees Celsius and above, titanium 6242 has higher strengths compared to titanium 64“, he adds. This titanium alloy is often recognized as a hard one to process but that’s something that becomes less complex when it’s processed on the TruPrint 5000 that can reach up to 500-degree Celsius preheating.
Ideal for the automotive industry, the CustAlloy aluminum alloy developed by ECKA Granules does not break or crack as quickly, making a good fit for crash-relevant applications. According to TRUMPF, is also far less expensive to purchase than comparable high-end aluminum alloys, which use expensive alloying elements to achieve their properties.
The M789 AMPO tool steel on the other hand, is one of those materials that can be used without preheating. It is a great fit for corrosion-resistant applications in tool and mold making.
Interestingly, the Printdur HSA alloy would enable industrials to explore a more sustainable production as this material is made from recycled scrap. Qualified for the TruPrint 2000, it presents properties that are similar to the Medidur alloy: it does not require any thermal post-treatment and is a particular good fit for the medical industry given the stringent requirements of this industry for the purity of materials. “In addition, both Printdur HSA and Medidur do not contain nickel or cobalt. Since both substances are considered potentially carcinogenic, this has a positive effect on the hazard load for employees who process these powders,” says Schauer.
Last but not least, we may have seen the capabilities of TRUMPF’s TruPrint 5000 green edition through the fabrication of the radio frequency quadrupole but the new TruPrint 1000 for additive series production should not be left behind.
Ideally suited for series production in the dental or medical industry, the TruPrint 1000 can produce all night without a worker having to be present. In addition to its key specifications mentioned in this article, the machine may raise interest thanks to its improved gas flow, an exchange cylinder option, and a Multiplate function ( up to four build plates can be placed on top of each other in the build cylinder, printing parts one after the other).
Last but not least, the special feature is that both lasers can process the entire build plate. “With two lasers we can improve the productivity of this machine even further,” says Mirko De Boni, Product Manager at TRUMPF. “The TruPrint 1000 also uses the so-called beam expander to automatically adjust the spot diameter of the laser to the particular build job. The spot diameter is 55 or 80 micrometers, depending on the application. The wider spot allows for higher productivity, while the 55 micrometer spot can be used when special powders need higher energy density”, he concludes.
Remember, you can post job opportunities in the AM Industry on 3D ADEPT Media free of charge or look for a job via our job board. Make sure to follow us on our social networks and subscribe to our weekly newsletter : Facebook, Twitter, LinkedIn & Instagram ! If you want to be featured in the next issue of our digital magazine or if you hear a story that needs to be heard, make sure you send it to contact@3dadept.com