3D printing has led to some of the coolest objects we have ever seen in this industry but sometimes, the materials used to produce these objects are fabricated in a very unexpected way. 3D ADEPT Media looks at some of the strangest materials, industrial AM companies, scientists and makers have discovered over time. From industrial applications to “Do-it-Yourself” applications, these innovations can meet the simplest needs of industries to the most urgent needs of the planet.
Sometimes qualified as “strange” or “unusual”, these unique materials are not less efficient. On the contrary, the innovators behind this idea have proved to advance the 3D printing industry in their respective field of expertise. We would like to outline today 5 materials, their unique properties and (at times) the atypical way they have been developed.
1. Keep it sane.
One of the complexities of a technology is making it compatible with “vital products”, in other terms, products that can affect our health if they are not safely produced.
Take for instance a single water fitting. For a part that looks trivial, all it takes is a bad installation or a production with the wrong materials for a disaster to strike. Quite simply because these are elements that can come into contact with (drinking) water.
As we were researching our list of unusual materials, we came to realize that 3D printing has something offer for such type of production. In fact, 3D printing company Ricoh has developed a new powder called Ricoh Polypropylene that could be used to address the needs of parts production that can be in contact with water for instance – as well as for applications in the industrial and energy sectors.
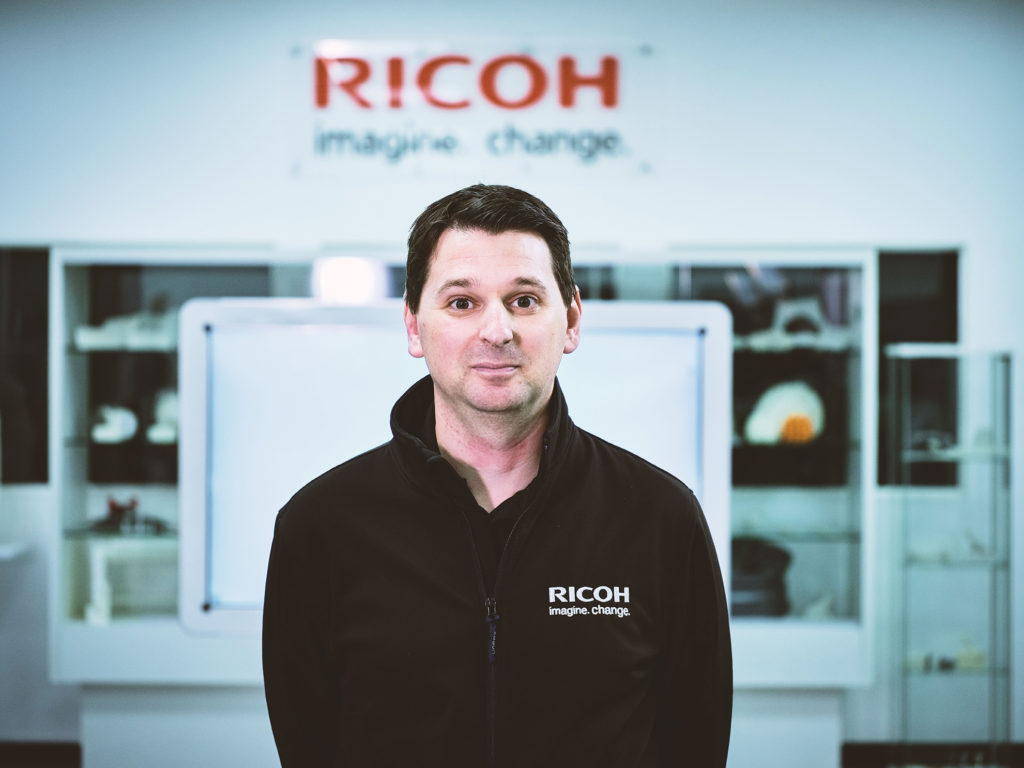
Approved by the WRAS (Water Regulations Advisory Scheme), the 3D printing powder delivers high flexibility and good impact resistance. It has successfully passed rigorous tests to ensure that:
“ – it doesn’t affect the quality of water by changing its appearance, taste or odour;
- it doesn’t leach toxic compounds and heavy metals which may be harmful;
- and it doesn’t promote the microbial growth within piping removing therefore the risk for generating unsightly slime formation.”
“Combined with its chemical stability and water tightness, parts produced with our polypropylene material are an ideal solution for producing functional prototypes and serial components for applications in contact with water” Enrico Gallino, Senior Engineer – Material Specialist Additive Manufacturing at Ricoh UK comments.
2. Space exploration
Let’s explore a little bit more what may happen in space. The following plastic material is a combination of Polyetherimide/Polycarbonate (PEI/PC). It is definitely among the 3D printable tools that brave the vacuum of space.
As you may guess, tools within the station are quickly limited to repairs – given the harsh conditions of the environment. This plastic material developed by Made in Space (MIS) would address this challenge as “it is not going to emit particles in a vacuum, it’s resistant to the UV environment, it’s resistant to atomic oxygen, so it can perform actual uses in space.”
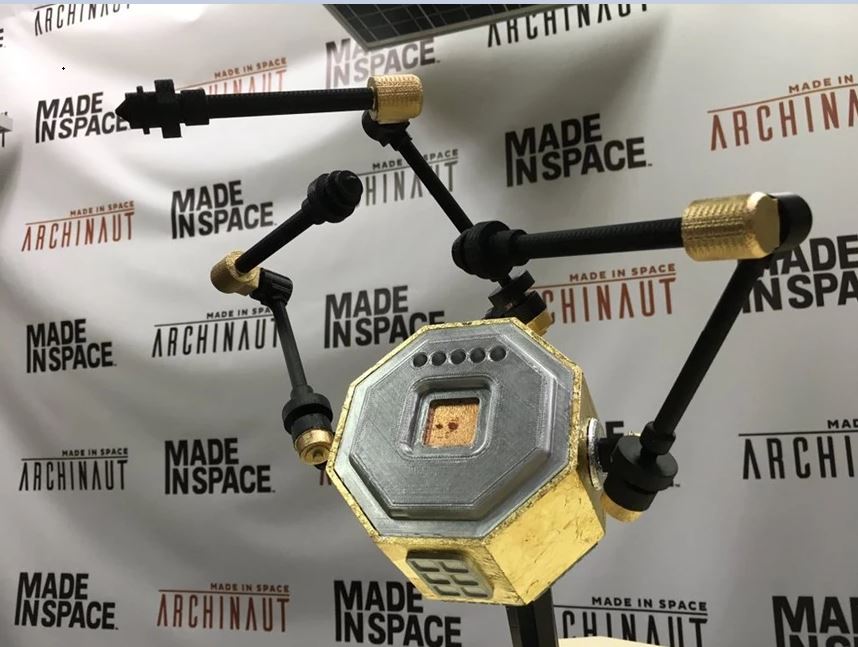
Most of you are certainly aware of blends of PEI/PC, such as ULTEM 9085 and ULTEM 1010, which are used in additive manufacturing for commercial aerospace applications. On earth, one could easily see PEI/PC being adopted in aircraft cabins and in the medical industry. Having nearly triple the tensile strength of ABS, a high strength-to-weight ratio and low off-gassing properties, PEI/PC is the ideal candidate for external hardware and satellites in space.
As MIS’ President & CEO said during the launch of this material: “Manufacturing in PEI/PC really expands the value of in-space manufacturing for human spaceflight. PEI/PC is a truly space-capable material. With it, extra-vehicular activity (EVA) tools and repairs, stronger and more capable intra-vehicular activity (IVA) tools, spares, and repairs, and even satellite structure can be created on site, on demand. That enables safer, less mass-intensive missions and scientific experiments.”
This list is not exhaustive but we hope you get the overall point: 3D printing might be one of the rare manufacturing processes – if not the only manufacturing process – where we can expect the unexpected.
3. Turning human waste into a 3D printing material
Just when we got used to pay attention to objects that can be recycled and turned into 3D printing materials, we learn that there is a tiny chance to turn human excreta into 3D printing material.
This extraordinary solution is the idea of fourteen students from the University of Calgary in Canada who competed two years ago at the International Genetically Engineered Machine (iGEM) Foundation’s Giant Jamboree on the theme “synthetic biology”.
As the title implies, “Astroplastic: From Colon to Colony”, their project involves the use of human excreta as a major bioplastic ingredient for 3D printing in space. The reflection behind this idea is a really interesting one as many aerospace professionals will tell you the numerous challenges one can have to produce a functional tool that meets the harsh conditions of the space environment not to mention the transportation when resources are lacking.
As part of this issue of 3D ADEPT Mag, we reached out to Alina Kunitskaya, one of the leaders of this project to have further information about its advancement:
Could you please explain the process of using human waste for creating a 3D printing material?
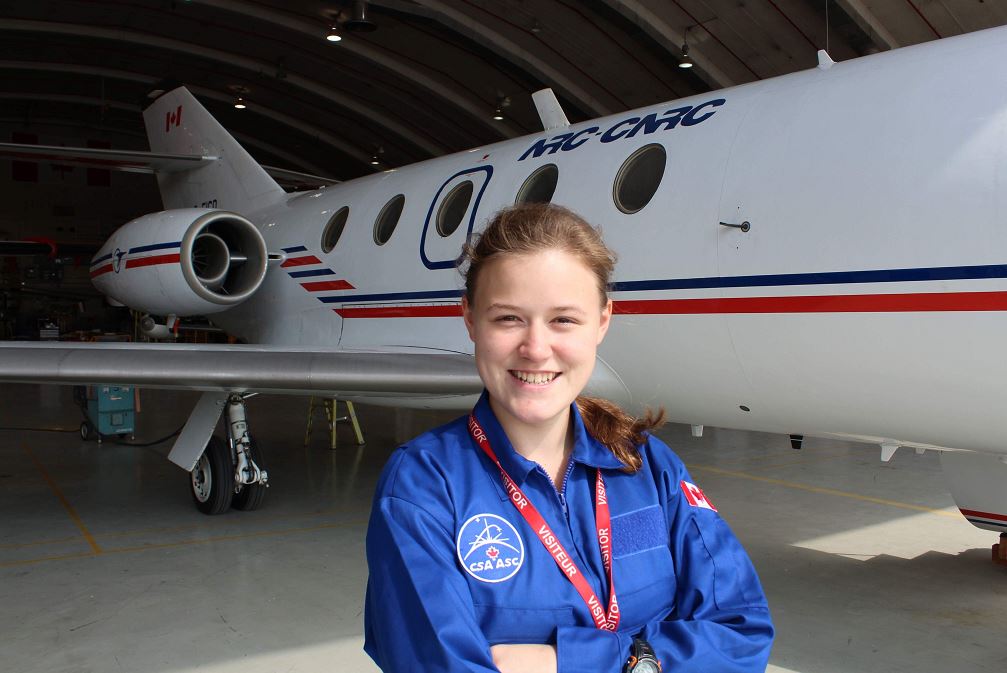
Our project called “Astroplastic” aims to address two major challenges with future human missions to Mars: sustainable waste management and the high cost of shipping materials to space. In our system, poly(3-hydroxybutyrate) bioplastic, or PHB for short, is produced by genetically engineered Escherichia coli bacteria that use volatile fatty acids found in solid human waste.
To describe the proposed process in more details, astronauts’ feces are first collected into a storage tank using a vacuum toilet. Feces are then transferred into another tank and left to ferment for 3 days with bacteria naturally found in human feces to increase the concentration of volatile fatty acids. Next, the liquid containing volatile fatty acids and other nutrients from human waste is separated from solid particles using centrifugation followed by filtration. The obtained volatile fatty acids are then added to a fermenter containing the engineered PHB-producing E. coli. Lastly, PHB produced by bacteria is extracted from the liquid harvest stream and dried, resulting in the powdered bioplastic material.
Did you actually go to the end of the experience to discover what kind of objects (flexible, solid, etc.) – and on which AM technology -one can print such type of materials?
We expect that the produced bioplastic can be used to print solid objects. In particular, we hope astronauts will be able to use it for printing tools and small items that may be used as spare parts for maintenance repairs or science experiments. Since the final product is a powdered plastic material, we considered using selective laser sintering as the most suitable AM technology. However, our experiments have been done on a small scale so we didn’t have enough material to test the use of produced material in selective laser sintering so far.
How different would this 3D printable material be from other materials we usually used for 3D printing?
Although PHB has been used in 3D printing before, it can be quite brittle. We would need to further investigate if there is a need for post-processing of the produced bioplastic to create a blend with suitable properties.
feces simulant – image via Alina Plastic wrench – image via Alina
What is happening with the project “Astroplastic: From Colon to Colony” so far?
We were able to successfully engineer E. coli to produce PHB bioplastic, which was tested using a simulant of solid human waste. Since bacteria naturally produces PHB granules internally, we also engineered bacteria to secrete the produced PHB for easier extraction. In parallel to these biological experiments, we also developed a concept for a start-to-finish PHB production process on Mars based on feedback from experts, determined optimal operating conditions for several steps, and tested several steps in the lab. This project was presented at the International Genetically Engineered Machine (iGEM) competition, receiving a gold medal and a nomination for Best Manufacturing Project.
Following the iGEM competition, we also investigated how to adapt the proposed process to the microgravity environment (as the initial process was developed for the Martian gravity environment). In particular, we tested the plastic extraction step of the process in microgravity aboard a parabolic flight.
Is there a one-way guide to determine if a product can be used as good feedstock for creating consistent filament?
As a student group, we had limited resources and expertise to test the use of our product. At this stage of the project, we relied on existing literature involving our product or similar type of products (powdered plastic material) to determine the feasibility of using this material and to identify suitable AM technologies.
4. Keep tape from Old VHS Cassettes for your 3D printing filaments.
If you are part of generation X or Y, then you are certainly familiar with VHS, which stands for Video Home System, a standard for consumer-level analog video recording on tape cassettes. With all the streaming platforms that are available today, these tape cassettes have become quite obsolete.
Rather than throwing them away, Russian maker Andrew aka Brother has given a second life to all of that tape. With the goal of making the planet cleaner, Brother has been experimenting several materials made up of different objects: plastic bottles, Christmas tinsel, medical masks, dvd discs, Styrofoam – most of them are even shared on his personal YouTube account.
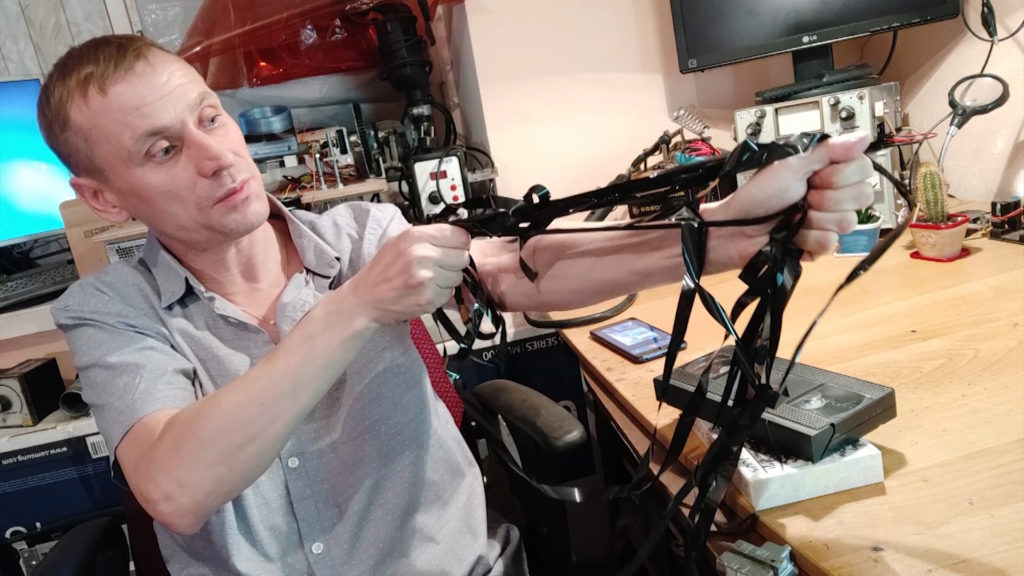
“I want to save the planet from garbage, at least a little. I think that if many people repeat my experiments, the planet will become cleaner. Passing by the landfill, I saw over 100 VHS cassettes. At first, I thought I would use cassette casings, but I finally decided to try melting the tape”, he told 3D ADEPT Media.
With four to five layers – one being magnetic -, Brother explained it is easy to remove tape from a VHS by pushing a button on the top left of the cassette. Once it pops the top open, you need to press down in the middle of the back of the cassette to unlock it before you can unwind all of the tape.
To create the filament, the maker used a purpose-built press to tightly spin the tape from several cassettes into one strand of 3 mm filament. This stage requires several tests to make sure the strand did not end up being too thin.
“The tape filament needs to be heated higher than a standard 3D printer filament so he prints at a much slower rate, but the resulting product is indistinguishable from a normal print except for the color,” Bryan Cockfield stated in the Hackaday post. “It has some other interesting properties as well, such as retaining its magnetism from the magnetic tape, and being a little more brittle than PET plastic although it seems to be a little stronger.”
After several tests on his Omni 3D printer, the maker noted that filament is quite strong and delivers prints with a smooth texture. However, when asked how different is this 3D printable material from other materials he usually used for 3D printing, he said:
“I usually print with unusual materials which are recycled plastics. Therefore, I cannot compare such materials with 3D printing materials used in factories. The VHS filament is interesting in that it has electrical conductivity, albeit with high resistance, and magnetization. Post-processing is unnecessary for this material. The printed objects have a very nice structure. There are not many tapes left in the world. And of course, such a filament production technology cannot be introduced into mass production, but you can peep the composition of the tape and create a factory filament on its basis.”
5. Inspired by nature.
While construction 3D printing provides a wide range of benefits for the building industry, one of the most important challenges builders face is with materials. Researchers keep exploring the materials possibilities for this specific segment and have already come out with some unexpected ideas to print structures in the construction industry. One of them includes fly ash – a residue from burnt coal.
However, if we write these lines, it’s to address one of the challenges raised by one of the most used materials in construction 3D printing: concrete. Except that this time, we’ll talk about lobsters and concrete.
The truth is, making concrete strong enough for complex, creative structures is a holy grail for builders. A team of researchers from RMIT University has recently explored the natural strength of lobster shells to design special 3D printing patterns.
Needless to remind that what makes these marine crustaceans outstanding in the eyes of ordinary people is their muscular tails. However, a thorough analysis of scientists revealed that lobsters present bio-mimicking spiral patterns that could improve the overall durability of the 3D printed concrete. Furthermore, the aforementioned patterns could also enable the strength to be precisely directed for structural support where needed.
When the team combined the twisting patterns with a specialised concrete mix enhanced with steel fibres, the resulting material was stronger than traditionally-made concrete.
Speaking of the benefits of bio-inspired approach in 3D concrete printing, lead researcher Dr Jonathan Tran said: “We know that natural materials like lobster exoskeletons have evolved into high-performance structures over millions of years, so by mimicking their key advantages we can follow where nature has already innovated.”
The team tested the impact of printing the concrete in helicoidal patterns (inspired by the internal structure of lobster shells), cross-ply and quasi-isotropic patterns (similar to those used for laminated composite structures and layer-by-layer deposited composites) and standard unidirectional patterns.
The results showed strength improvement from each of the patterns, compared with unidirectional printing, but Tran said the spiral patterns hold the most promise for supporting complex 3D printed concrete structures.
“As lobster shells are naturally strong and naturally curved, we know this could help us deliver stronger concrete shapes like arches and flowing or twisted structures,” Tran said.
“This work is in early stages so we need further research to test how the concrete performs on a wider range of parameters, but our initial experimental results show we are on the right track.”
Further studies will be supported through a new large-scale mobile concrete 3D printer recently acquired by RMIT – making it the first research institution in the southern hemisphere to commission a machine of this kind.
There is a still a long list of unusual & strange materials used in the additive manufacturing industry but those five materials are the ones that raised the most our interest, for now. If you believe that should absolutely be in that list, please, feel free to let us know.
This exclusive feature was initially published in the January/February issue of 3D ADEPT Mag.
Remember, you can post job opportunities in the AM Industry on 3D ADEPT Media free of charge or look for a job via our job board. Make sure to follow us on our social networks and subscribe to our weekly newsletter : Facebook, Twitter, LinkedIn & Instagram ! If you want to be featured in the next issue of our digital magazine or if you hear a story that needs to be heard, make sure you send it to contact@3dadept.com