L’impression 3D a donné naissance à certains des objets les plus cools que nous ayons jamais vus dans cette industrie, mais parfois, les matériaux utilisés pour produire ces objets sont fabriqués d’une manière très inattendue. 3D ADEPT Media se penche sur certains des matériaux les plus étranges ou inhabituels que les entreprises industrielles, les scientifiques et les « makers » ont découverts au fil du temps. Des applications industrielles aux applications « Do-it-Yourself« , ces innovations peuvent répondre aux besoins les plus simples des industries aux besoins les plus urgents de la planète.
Parfois qualifiés d' »étranges » ou d' »inhabituels », ces matériaux uniques ne sont pas moins efficaces. Au contraire, les innovateurs à l’origine de ces matériaux ont prouvé qu’ils faisaient progresser l’industrie de l’impression 3D dans leur domaine de compétence respectif. Nous aimerions aujourd’hui vous présenter 5 matériaux, leurs propriétés uniques et (parfois) la manière atypique dont ils ont été développés.
1. Garder la production propre.
L’une des complexités d’une technologie est de la rendre compatible avec les « produits vitaux », en d’autres termes, les produits qui peuvent affecter notre santé s’ils ne sont pas fabriqués en toute sécurité.
Prenons par exemple un simple robinet d’eau. Pour une pièce qui semble insignifiante, il suffit d’une mauvaise installation ou d’une production avec les mauvais matériaux pour qu’une catastrophe se produise.
En faisant des recherches sur notre liste de matériaux inhabituels, nous nous sommes rendu compte que l’impression 3D avait quelque chose à offrir pour ce type de production. En fait, la société d’impression 3D Ricoh a mis au point une nouvelle poudre appelée Ricoh Polypropylene qui pourrait être utilisée pour répondre aux besoins de la production de pièces pouvant être en contact avec l’eau par exemple – ainsi que pour des applications dans les secteurs de l’industrie et de l’énergie.
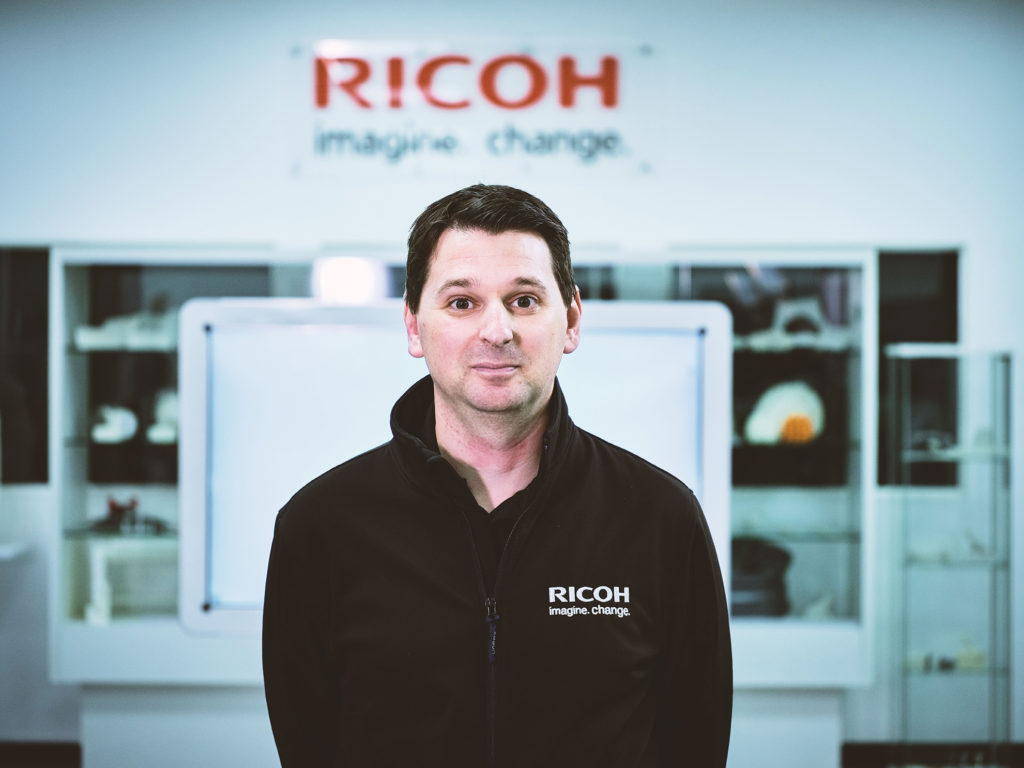
Approuvée par le WRAS (Water Regulations Advisory Scheme), la poudre d’impression 3D offre une grande flexibilité et une bonne résistance aux chocs. Elle a passé avec succès des tests rigoureux pour s’en assurer :
« – elle n’affecte pas la qualité de l’eau en changeant son apparence, son goût ou son odeur ;
– elle n’entraîne pas de lixiviation de composés toxiques et de métaux lourds qui pourraient être nocifs;
– elle ne favorise pas la croissance microbienne dans les canalisations, éliminant ainsi le risque de formation de boue inesthétique ».
« Combinées à sa stabilité chimique et à son étanchéité, les pièces produites avec notre matériau polypropylène sont une solution idéale pour la production de prototypes fonctionnels et de composants en série pour les applications en contact avec l’eau », commente Enrico Gallino, ingénieur principal – spécialiste de la fabrication additive pour les matériaux chez Ricoh UK.
2. L’exploration spatiale
Voyons un peu plus en détail ce qui peut se passer dans l’espace. La matière plastique suivante est une combinaison de polyétherimide/polycarbonate (PEI/PC). Il fait définitivement partie des outils imprimables en 3D qui bravent le vide de l’espace.
Comme vous pouvez le deviner, les outils de la station sont rapidement limités aux réparations – étant donné les conditions difficiles de l’environnement. Ce matériau plastique développé par Made in Space (MIS) permettrait de relever ce défi car « il ne va pas émettre de particules dans le vide, il est résistant à l’environnement UV, il est résistant à l’oxygène atomique, il peut donc effectuer des utilisations réelles dans l’espace ».
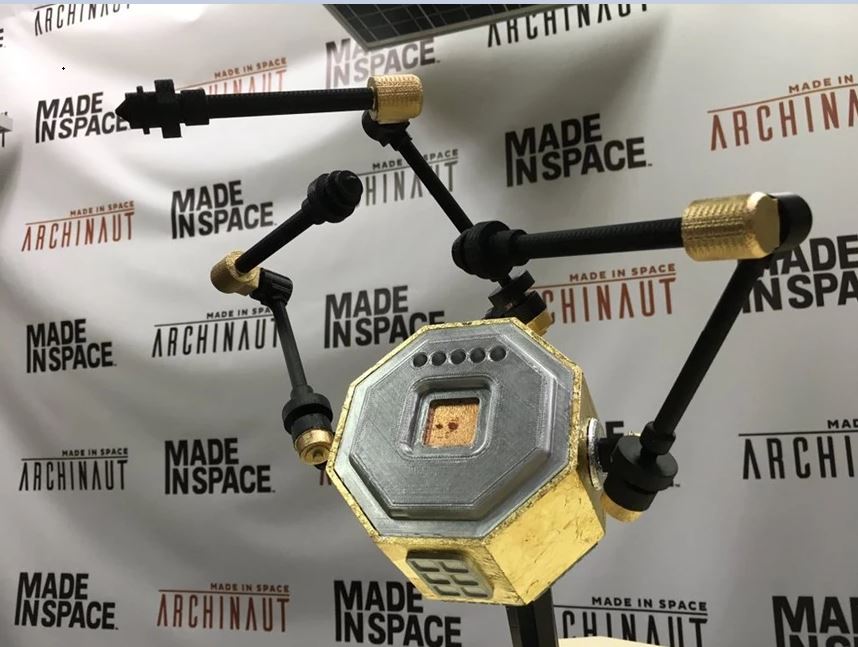
La plupart d’entre vous connaissent certainement les mélanges de PEI/PC, tels que ULTEM 9085 et ULTEM 1010, qui sont utilisés dans la fabrication additive pour des applications aérospatiales commerciales. Sur terre, on pourrait facilement voir l’adoption de PEI/PC dans les cabines d’avion et dans l’industrie médicale. Avec une résistance à la traction presque trois fois supérieure à celle de l’ABS, un rapport résistance/poids élevé et de faibles dégagements gazeux, le PEI/PC est le candidat idéal pour le matériel externe et les satellites dans l’espace.
Comme l’a déclaré le président-directeur général de MIS lors du lancement de ce matériau : « La fabrication avec le matériau PEI augmente réellement la valeur de la fabrication dans l’espace pour les vols spatiaux habités. Le PEI est un matériau véritablement adapté à l’espace. Grâce à lui, il est possible de créer sur place, à la demande, des outils et des réparations pour les activités extravéhiculaires (EVA), des outils, des pièces de rechange et des réparations pour les activités intra-véhiculaires (IVA) plus solides et plus performantes, et même une structure de satellite. Cela permet des missions et des expériences scientifiques plus sûres et moins massives ».
Cette liste n’est pas exhaustive, mais nous espérons que vous comprenez l’essentiel : l’impression 3D est peut-être l’un des rares procédés de fabrication – si ce n’est le seul – où on peut s’attendre à l’inattendu.
3. Transformer les déchets humains en un matériau d’impression 3D
Juste au moment où nous nous sommes habitués à prêter attention aux objets qui peuvent être recyclés et transformés en matériau d’impression 3D, nous apprenons qu’il y a une infime chance de transformer les excréments humains en matériau d’impression 3D.
Cette solution extraordinaire est l’idée de quatorze étudiants de l’université de Calgary au Canada qui ont participé il y a deux ans au Jamboree géant de la Fondation internationale pour les machines génétiquement modifiées (iGEM) sur le thème de la « biologie synthétique ».
Comme le titre l’indique, « Astroplastic : From Colon to Colony« , leur projet implique l’utilisation d’excréments humains comme ingrédient bioplastique majeur pour l’impression 3D dans l’espace. La réflexion derrière cette idée est vraiment intéressante car de nombreux professionnels de l’aérospatiale vous diront les nombreux défis qu’on peut avoir à relever pour produire un outil fonctionnel qui réponde aux conditions difficiles de l’environnement spatial, sans parler du transport lorsque les ressources font défaut.
Dans le cadre de ce numéro de 3D ADEPT Mag, nous avons contacté Alina Kunitskaya, l’une des responsables de ce projet, pour avoir plus d’informations sur son avancement :
Pourriez-vous nous expliquer le processus d’utilisation des déchets humains pour la création d’un matériau d’impression en 3D ?
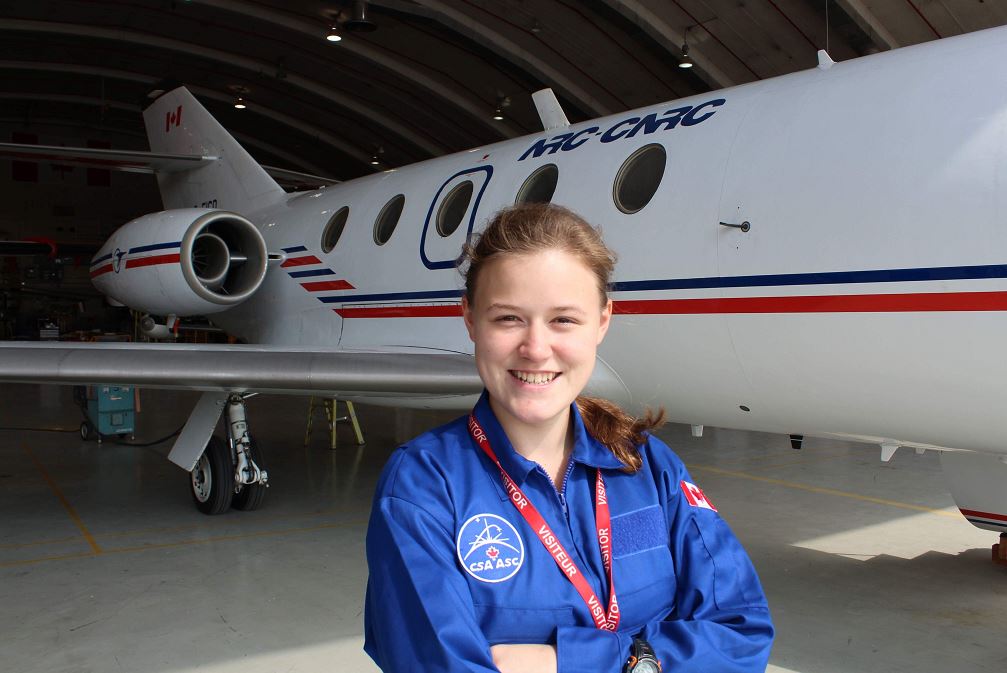
Notre projet intitulé « Astroplastic » vise à relever deux défis majeurs dans le cadre des futures missions humaines vers Mars : la gestion durable des déchets et le coût élevé de l’expédition de matériaux vers l’espace. Dans notre système, le bioplastique poly(3-hydroxybutyrate), ou PHB en abrégé, est produit par des bactéries Escherichia coli génétiquement modifiées qui utilisent les acides gras volatils présents dans les déchets humains solides.
Pour décrire le processus proposé plus en détail, les excréments des astronautes sont d’abord collectés dans un réservoir de stockage à l’aide d’une toilette à vide. Les fèces sont ensuite transférées dans un autre réservoir et laissées à fermenter pendant 3 jours avec des bactéries naturellement présentes dans les fèces humaines pour augmenter la concentration d’acides gras volatils. Ensuite, le liquide contenant les acides gras volatils et d’autres nutriments provenant des déchets humains est séparé des particules solides par centrifugation suivie d’une filtration. Les acides gras volatils obtenus sont ensuite ajoutés à un fermenteur contenant la bactérie E. coli productrice de PHB. Enfin, le PHB produit par les bactéries est extrait du flux de récolte liquide et séché, ce qui donne la matière bioplastique en poudre.
Êtes-vous vraiment allé jusqu’au bout de l’expérience pour découvrir quel type d’objets (souples, solides, etc.) – et sur quelle technologie AM – on peut imprimer ce type de matériaux ?
Nous pensons que le bioplastique produit peut être utilisé pour imprimer des objets solides. Nous espérons en particulier que les astronautes pourront l’utiliser pour imprimer des outils et de petits objets qui pourront servir de pièces de rechange pour les réparations d’entretien ou les expériences scientifiques. Comme le produit final est une matière plastique en poudre, nous avons considéré que le frittage sélectif au laser était la technologie de FA la plus appropriée. Cependant, nos expériences ont été réalisées à petite échelle et nous n’avions donc pas assez de matériel pour tester l’utilisation du matériel produit dans le frittage laser sélectif jusqu’à présent.
simulateur de fèces – image via Alina Clé en plastique – image via Alina
Dans quelle mesure ce matériau imprimable en 3D serait-il différent des autres matériaux que nous utilisons habituellement pour l’impression 3D ?
Bien que le PHB ait déjà été utilisé pour l’impression 3D, il peut être assez fragile. Nous devrions étudier plus en profondeur s’il est nécessaire de post-traiter le bioplastique produit pour créer un mélange aux propriétés appropriées.
Que se passe-t-il avec le projet « Astroplastic : De colonie à colonie » ?
Nous avons réussi à mettre au point un E. coli pour produire le bioplastique PHB, qui a été testé en utilisant un simulateur de déchets humains solides. Comme les bactéries produisent naturellement des granules de PHB en interne, nous avons également conçu des bactéries pour qu’elles sécrètent le PHB produit afin d’en faciliter l’extraction. Parallèlement à ces expériences biologiques, nous avons également mis au point un concept de processus de production de PHB sur Mars, du début à la fin, en nous basant sur les commentaires des experts, déterminé les conditions de fonctionnement optimales pour plusieurs étapes et testé plusieurs étapes en laboratoire. Ce projet a été présenté lors du concours international « Genetically Engineered Machine » (iGEM), et a reçu une médaille d’or et une nomination pour le meilleur projet de fabrication.
À la suite du concours iGEM, nous avons également étudié comment adapter le processus proposé à l’environnement de microgravité (puisque le processus initial a été développé pour l’environnement de gravité martien). En particulier, nous avons testé l’étape d’extraction plastique du procédé en microgravité à bord d’un vol parabolique.
Existe-t-il un guide à sens unique pour déterminer si un produit peut être utilisé comme une bonne matière première pour créer un filament cohérent ?
En tant que groupe d’étudiants, nous avions des ressources et une expertise limitées pour tester l’utilisation de notre produit. À ce stade du projet, nous nous sommes appuyés sur la littérature existante concernant notre produit ou des produits similaires (matière plastique en poudre) pour déterminer la faisabilité de l’utilisation de ce matériau et pour identifier les technologies de FA appropriées.
4. Conserver le ruban adhésif des anciennes cassettes VHS pour en faire des filaments d’impression 3D.
Si vous faites partie de la génération X ou Y, alors vous connaissez certainement le VHS, qui signifie Video Home System, une norme pour l’enregistrement vidéo analogique sur cassettes au niveau du consommateur. Avec toutes les plates-formes de streaming disponibles aujourd’hui, ces cassettes sont devenues assez obsolètes.
Plutôt que de les jeter, le fabricant russe Andrew alias Brother a donné une seconde vie à toutes ces cassettes. Dans le but de rendre la planète plus propre, Brother a expérimenté plusieurs matériaux composés de différents objets : bouteilles en plastique, guirlandes de Noël, masques médicaux, disques dvd, polystyrène – la plupart d’entre eux sont même partagés sur son compte YouTube personnel.
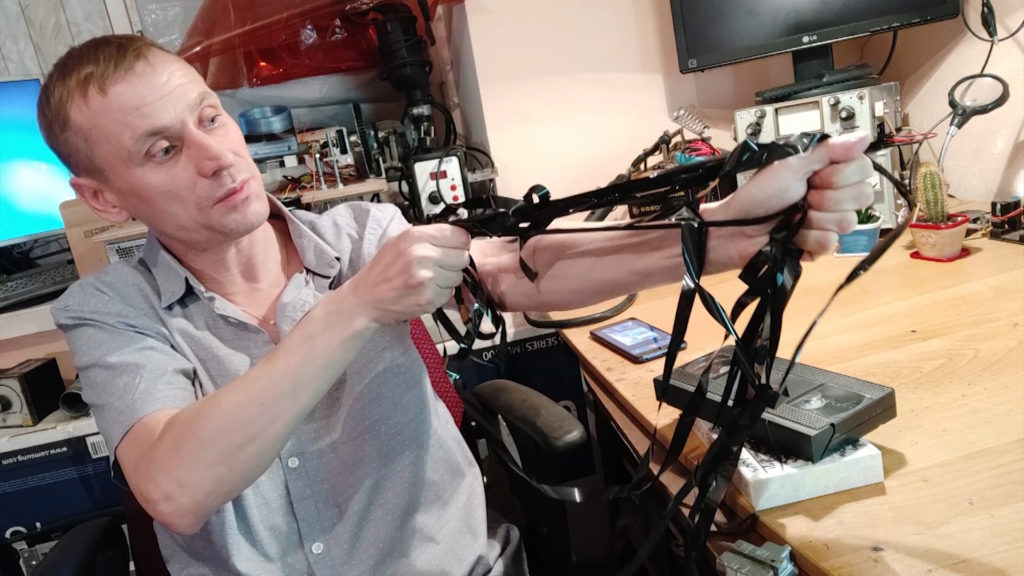
« Je veux sauver la planète des ordures, au moins un tout petit peu. Je pense que si beaucoup de gens répètent mes expériences, la planète deviendra plus propre. En passant devant la décharge, j’ai vu plus de 100 cassettes VHS. Au début, je pensais utiliser des boîtiers de cassettes, mais j’ai finalement décidé d’essayer de faire fondre la cassette, » a-t-il déclaré à 3D ADEPT Media.
Avec quatre à cinq couches – dont une magnétique -, Brother a expliqué qu’il est facile de retirer la bande d’un VHS en appuyant sur un bouton en haut à gauche de la cassette. Une fois que le haut de la cassette est ouvert, il faut appuyer au milieu du dos de la cassette pour la déverrouiller avant de pouvoir dérouler toute la bande.
Pour créer le filament, le fabricant a utilisé une presse spécialement conçue pour faire tourner la bande de plusieurs cassettes en un seul brin de filament de 3 mm. Cette étape nécessite plusieurs tests pour s’assurer que le brin n’a pas été trop fin.
« Le filament de la bande doit être chauffé plus que le filament d’une imprimante 3D standard, de sorte qu’il imprime à une vitesse beaucoup plus lente, mais le produit qui en résulte est impossible à distinguer d’une impression normale, sauf pour la couleur », a déclaré Bryan Cockfield dans le Hackaday post. « Il possède également d’autres propriétés intéressantes, comme le fait de conserver le magnétisme de la bande magnétique, et d’être un peu plus fragile que le plastique PET bien qu’il semble un peu plus résistant ».
Après plusieurs tests sur son imprimante 3D Omni, le maker a constaté que le filament est assez solide et donne des impressions avec une texture lisse. Toutefois, lorsqu’on lui a demandé dans quelle mesure ce matériau imprimable en 3D est différent des autres matériaux qu’il utilise habituellement pour l’impression 3D, il a répondu :
« J’imprime généralement avec des matériaux inhabituels qui sont des plastiques recyclés. Par conséquent, je ne peux pas comparer ces matériaux avec les matériaux d’impression 3D utilisés dans les usines. Le filament VHS est intéressant en ce sens qu’il présente une conductivité électrique, bien qu’ayant une résistance élevée, et une magnétisation. Le post-traitement est inutile pour ce matériau. Les objets imprimés ont une très belle structure. Il ne reste pas beaucoup de bandes dans le monde. Et bien sûr, une telle technologie de production de filaments ne peut pas être introduite dans la production de masse, mais vous pouvez observer la composition du ruban et créer un filament d’usine sur sa base ».
5. Inspiré par la nature.
Si l’impression 3D en construction offre de nombreux avantages pour l’industrie du bâtiment, l’un des défis les plus importants auxquels les constructeurs sont confrontés concerne les matériaux. Les chercheurs continuent d’explorer les possibilités des matériaux pour ce segment spécifique et ont déjà sorti quelques idées inattendues pour imprimer des structures dans l’industrie de la construction. L’une d’entre elles concerne les cendres volantes, un résidu du charbon brûlé.
Cependant, si nous écrivons ces lignes, c’est pour répondre à l’un des défis posés par l’un des matériaux les plus utilisés dans l’impression 3D de construction : le béton. Sauf que cette fois, nous parlerons de homards et de béton.
La vérité est que rendre le béton suffisamment solide pour des structures complexes et créatives est un saint graal pour les constructeurs. Une équipe de chercheurs de l’université RMIT a récemment exploré la résistance naturelle des carapaces de homard pour concevoir des motifs spéciaux d’impression 3D.
Inutile de rappeler que ce qui rend ces crustacés marins exceptionnels aux yeux des gens ordinaires, c’est leur queue musclée. Cependant, une analyse approfondie des scientifiques a révélé que les homards présentent des motifs en spirale bio-mimétiques qui pourraient améliorer la durabilité globale du béton imprimé en 3D. En outre, les motifs susmentionnés pourraient également permettre d’orienter précisément la force vers le soutien structurel nécessaire.
Lorsque l’équipe a combiné les motifs de torsion avec un mélange de béton spécialisé enrichi de fibres d’acier, le matériau résultant était plus résistant que le béton traditionnel.
En parlant des avantages de l’approche bio-inspirée dans l’impression 3D du béton, le chercheur principal, le Dr Jonathan Tran, a déclaré : « Nous savons que les matériaux naturels comme les exosquelettes de homard ont évolué en structures de haute performance au cours de millions d’années, donc en imitant leurs avantages clés, nous pouvons suivre là où la nature a déjà innové ».
L’équipe a testé l’impact de l’impression du béton selon des motifs hélicoïdaux (inspirés de la structure interne des carapaces de homard), des motifs croisés et quasi-isotropes (similaires à ceux utilisés pour les structures composites laminées et les composites déposés couche par couche) et des motifs unidirectionnels standard.
Les résultats ont montré une amélioration de la résistance de chacun des motifs, par rapport à l’impression unidirectionnelle, mais Tran a déclaré que les motifs en spirale étaient les plus prometteurs pour soutenir des structures complexes en béton imprimé en 3D.
« Comme les coquilles de homard sont naturellement résistantes et naturellement courbées, nous savons que cela pourrait nous aider à obtenir des formes en béton plus résistantes comme des arcs et des structures fluides ou tordues », a déclaré Tran.
« Ce travail n’en est qu’à ses débuts, nous devons donc poursuivre les recherches pour tester les performances du béton sur un plus large éventail de paramètres, mais nos premiers résultats expérimentaux montrent que nous sommes sur la bonne voie ».
D’autres études seront soutenues par une nouvelle imprimante 3D mobile à grande échelle pour le béton, récemment acquise par le RMIT – ce qui en fait le premier institut de recherche de l’hémisphère sud à mettre en service une machine de ce type.
Il existe encore une longue liste de matériaux inhabituels et étranges utilisés dans l’industrie de la fabrication additive, mais ces cinq matériaux sont ceux qui ont suscité le plus d’intérêt de notre part, pour l’instant. Si vous pensez qu’un autre matériau devrait absolument figurer dans cette liste, n’hésitez pas à nous le faire savoir.
Ce dossier a d’abord été publié dans le numéro de Janvier/Février de 3D ADEPT Mag.