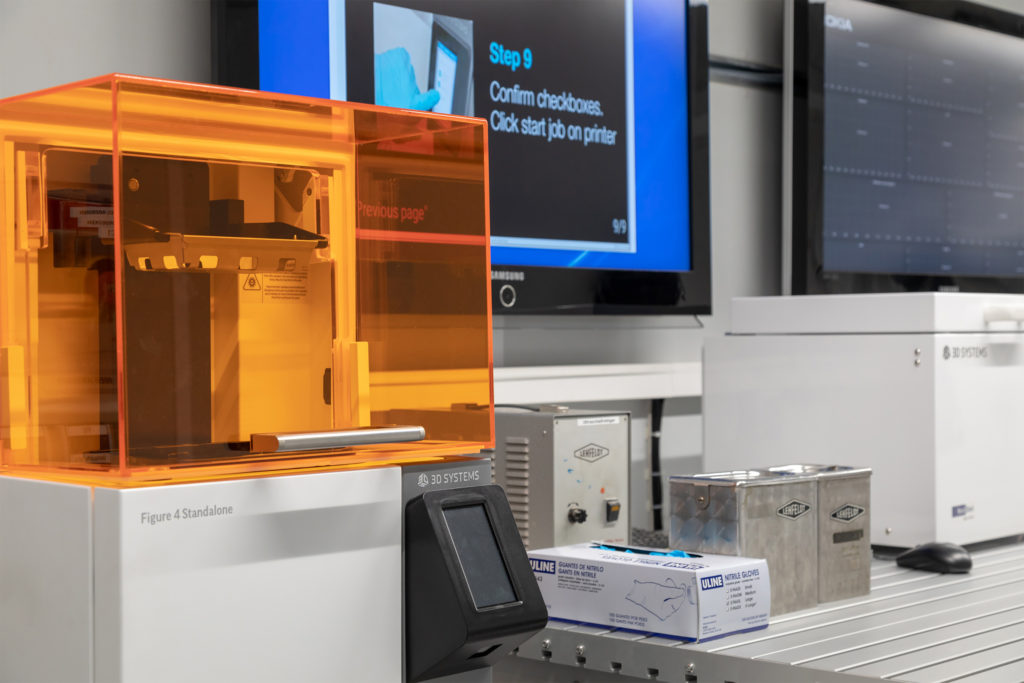
Nokia chose 3D Systems additive manufacturing solutions for its “Factory in a Box” mobile manufacturing solution
3D Systems announced yesterday that three global manufacturers – Nokia, rms Company, and GF Precicast – will take advantage of its AM solutions in their production workflows. We have seen a variety of applications of AM in the healthcare 3D printing and in industrial gas turbines.
However, the use of the technology is not well that spread in the telecommunications area and yet, this field is considered as a potential area of growth of the industry, given the increasing use of 3D printed electronics.
In this specific case, Nokia has integrated 3D Systems’ Figure 4 Standalone to its “Factory in a Box” mobile manufacturing solution –
In 2018, the specialist of mobile phones partnered with several technology providers to unveil its “factory in a box” concept. The intent was to demonstrate how manufacturers can stay ahead of the demands of Industry 4.0 through agile production capabilities that can be packed, transported and brought back into service in a matter of hours.
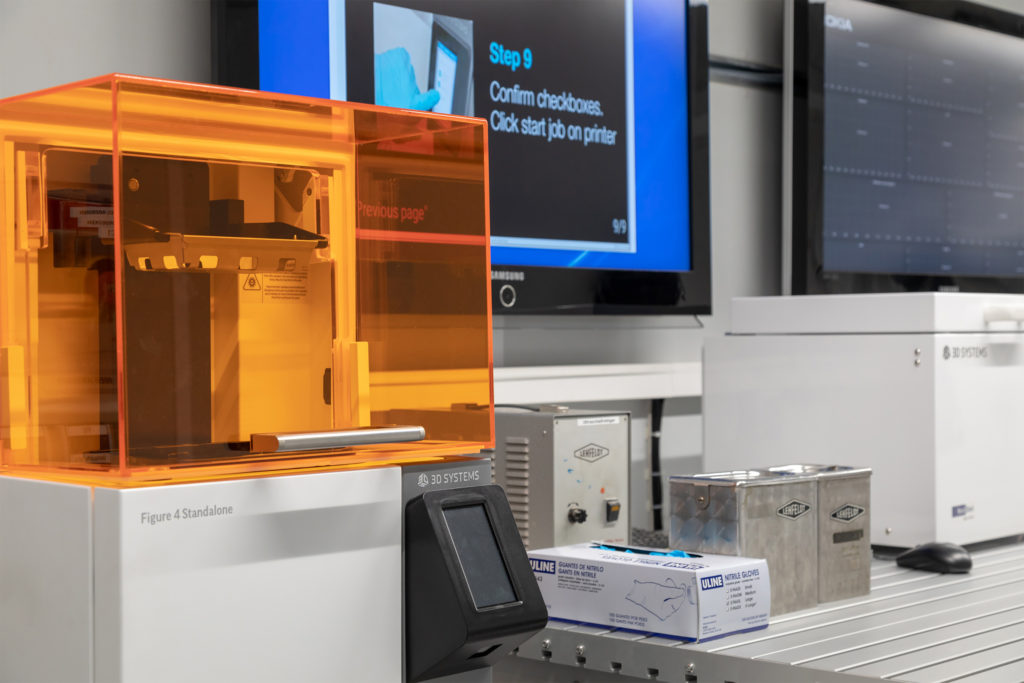
“After the positive feedback we received for our factory in a box concept last year, it was important to reach a new level with version 2.0,” said Grant Marshall, VP supply network & engineering, Nokia. “We did so in terms of connectivity, because factory in a box 2.0 is integrated into the Nokia Worldwide IoT Network Grid and has Nokia Digital Automation Cloud on board. But we also wanted to add new and advanced technology like 3D printing. 3D Systems’ Figure 4 Standalone was an obvious choice because of its high throughput and six sigma repeatability. These capabilities are exactly what we want to showcase as part of our consciousmanufacturing solution where speed, accuracy, and durability are critical.”
The integration of additive manufacturing alongside augmented reality/virtual reality (AR/VR) and robotics, all powered by Nokia private 4G / 5G connectivity, results in a semi-automated production workflow.
For further information about 3D Printing, follow us on our social networks and subscribe to our newsletter
Would you like to subscribe to 3D Adept Mag? Would you like to be featured in the next issue of our digital magazine? Send us an email at contact@3dadept.com