“It wasn’t accessible to professionals who aim to leverage the technology”, an example of sentences that announces the reason why a company decides to get into a new segment, to create a new business/company. Additive manufacturing is so intriguing that that there is always (and there will certainly always be) a reason to launch a new business.
Today, we wanted to discover the reason behind the creation of One Click Metal, that’s why we invited Björn Ullmann in this Opinion of the Week.
One Click Metal is a venture that has been recently created. Founded in April 2019, the company is a spin-off of the machine manufacturer TRUMPF. They develop metal additive manufacturing systems based on Laser Powder Bed Fusion, a process that is acknowledged for its ability to deliver high-dimensional accurate parts with good material properties.
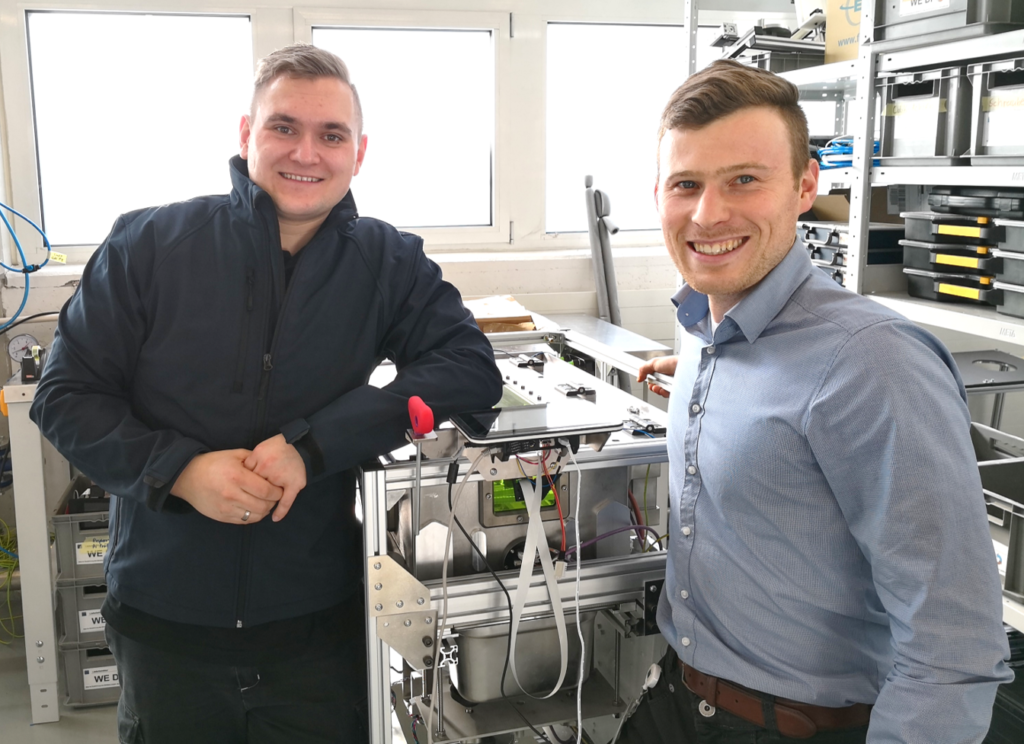
The story begins with Björn Ullmann and Stefan Weber. In their previous job (at Trumpf), the two founders were mostly involved in the management part of the business. With a keen interest in do-it-yourself activities, they were working on various technical projects outside their work. Assigned to the AM department at Trumpf, they have been able to build extensive experience in the field, to develop a very good network but also to assess a blatant reality of the market: metal AM technologies are not affordable. Indeed, accuracy and quality come with a price, which may vary from around $50,000 to $1 million (45 251 € to 905 000 €), price range that big fortune can easily afford but not SMEs, which happen to be the main target of our company guest.
Their 3D metal printer happens to be in a price range that does not exceed €55,000 and for a good reason: “Our aim was to develop an affordable system that is also easy-to-use. We might have benefited from our experience at Trumpf, but today One Click Metal is a complete standalone company”, Ullmann points out from the outset of the interview.
Why did you choose the name “One Click Metal”?
The main idea came from the previous start-up where I worked, that developed a software. As you may know, in an additive manufacturing process, the production starts with a model that you design using a specific software. Once your file is ready to print, you just click on a button to send the file to the 3D printer that will take in charge the production. Our aim was to portray the vision of an easy manufacturing process, which can be achieved with the click of a button. In this specific case, “One Click” is the perfect metaphor for several concepts that remain a challenge for professionals: “making production possible with metal AM”, “reducing complexity”, “affordability”, “ease of use” and “technology know how”.
What makes One Click Metal systems affordable?
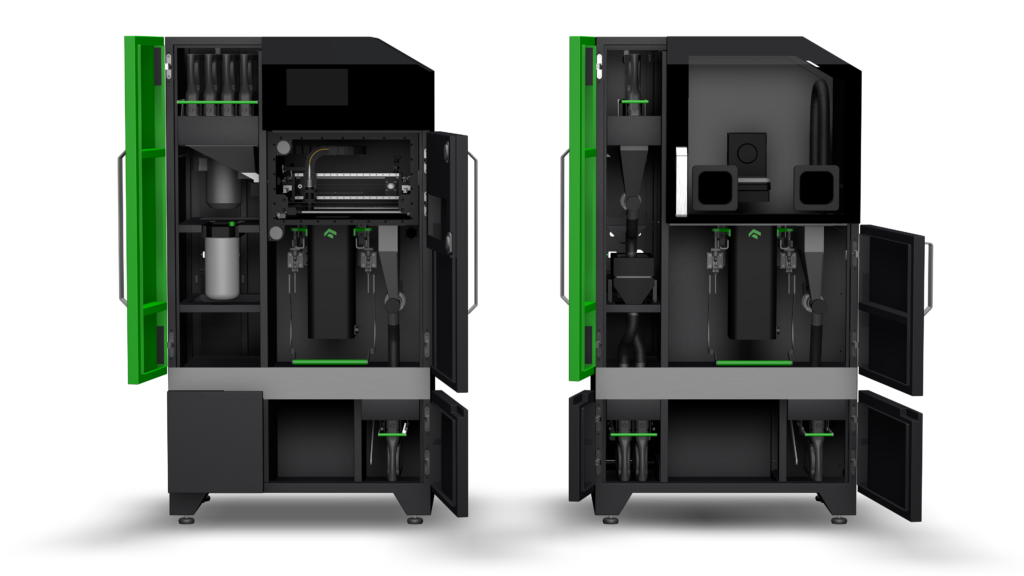
AM is much more than just the printing process and our aim is to make the whole value chain easy as possible for the customer who in the end, just wants something easy to handle.
We have therefore decided to put together a complete package that the customer would utilize. This package includes a preparation software, an unpacking station and a metal 3D printer.
The software calculates the toolpath of the uploaded model. The simulation tool that comes thereafter enables the operator to get closer to a first-time right approach during the manufacturing.
Furthermore, as part of the development of our systems, we realized that those who are often looking for affordable metal AM systems do not usually require very high-volume production. With that in mind, we had to build the machine differently. Not only our design is different, but we also reduce costs by focusing on one of the most expensive part utilized in a metal AM system: laser optic. We started developing our own diode laser and that’s where we shift most of the parts.
Are the printers already available for commercialization?
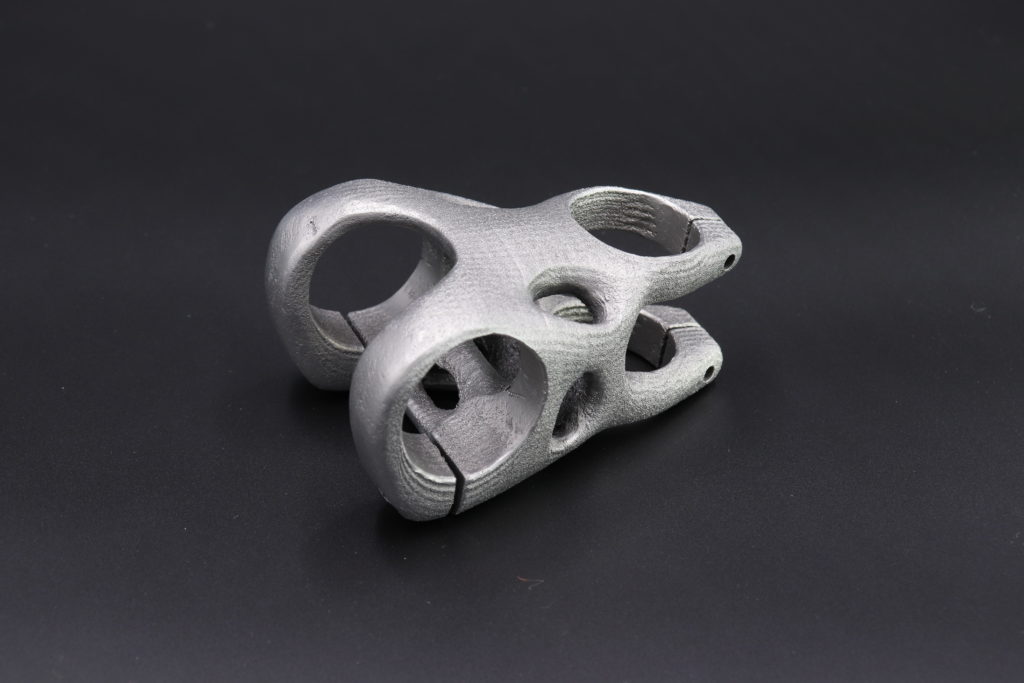
Yes, it is already possible to pre-order our systems. The first shippings will probably start in Q3. However, in order to focus on what we are good at, which is the development, One Click Metal systems will be sold from Q4 via our partner, Alphacam, which is a Germany-based reseller.
Also, it should be noted that our machines are built to be self-maintained. Nevetherless, it goes without saying that our service partners will always be there for any customer who needs support.
2019 saw the official launch of One Click Metal at Formnext. What was the goal of the company?
Our goal was to get a first feedback from professionals, to see how the product would be perceived in order to know in which direction, we should be moving forward. It turns out that we received a great response from customers and technology specialists. For us, this means that we did – and we are doing – things right. This recognition from the main target also proves that there is a certain demand on the market that we will be able to meet: the need for a more affordable metal AM system.
How do you see the year 2020: any specific projects in the box to share?
This year is going to be our round up year: making a lot of machines. It will certainly be a tough one as we want to scale very fast. It’s one thing to manufacture 10 machines, it’s a different thing to make 100 or 10 000 machines. The challenge will be to ensure the ramping up of the production and we are ready for it.
Images: One Click Metal.Remember, you can post free of charge job opportunities in the AM Industry on 3D ADEPT Media or look for a job via our job board. Make sure to follow us on our social networks and subscribe to our weekly newsletter : Facebook, Twitter, LinkedIn & Instagram ! If you want to be featured in the next issue of our digital magazine or if you hear a story that needs to be heard, make sure to send it to contact@3dadept.com.