Key insights into a depowdering test with a build plate of medical 3D printed parts
Once you’ve decided that an automated depowdering machine is the right device for your (medical) 3D printed parts, the next step can be quite stressful: making the right decision when it comes to purchasing a machine that will ensure your products and personnel safety, reduce the risk of product failures and most importantly comply with industry standards. That’s the reason why, in another article, we discussed the must-have technical features in an automated powder removal system. The thing is, the more the market advances, the more new features are being developed and the more customers’ requirements become complex and stringent. At this point, a holistic experience that comes from a depowdering test might help tilt the balance in favor of one machine or another and confirm certification for use in a given industry or for a given application. To understand how such a test is being performed, we asked Solukon Maschinenbau GmbH something unusual: share insights into a depowdering test performed for one of their customers active in the medical and healthcare industries.
Solukon’s core expertise remains automated depowdering for AM. For this article, the depowdering test was performed on the company’s latest system – the SFM-AT350-E for medium-sized parts up to 60 kg– in collaboration with the Swiss m4m Center, a technology transfer center that leverages AM for the medical and dental industries. As an advocate for AM technologies, we have been following Swiss m4m’s journey with AM since its beginning.
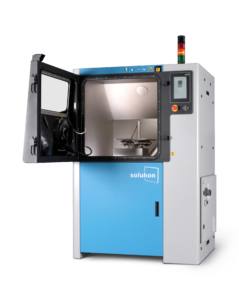
Insights into the brand-new SFM-AT350-E & applications at the heart of the test
Designed for metal 3D printed parts, the SFM-AT350-E is a special version of the automated depowdering machine SFM-AT350. Unveiled last year at Formnext 2023, the new machine comes with three key upgrades: full compatibility with intelligent SPR-Pathfinder® depowdering software, enhanced functions of the Digital Factory Tool as well as piezoelectric excitation.
If the SPR-Pathfinder® depowdering software and the Digital Factory Tool are now well-known features of Solukon’s depowdering systems and also available for the standard SFM-AT350 machine, the piezoelectric excitation tool remains intriguing for most users as a unique and special solution in the field.
During the launch, Solukon explained that excitation originates directly at the rotary table of the automated depowdering system which enables the part to be shifted to the optimal vibration range with high precision. The high frequencies of the electronic excitation are considerably higher than the harmful natural frequency of the part. As the frequency constantly controls and regulates itself, the risk of exciting the resonance frequency and damaging sensitive structures is avoided.
The test was performed with several medical 3D printed parts provided by Swiss m4m: hip cups, spinal cages and medical instruments.
“Hip cups are a very typical application. The characteristic lattice structures allow tissue ingrowth. Also, the spinal cages for stiffening the spine in cases of instability (e.g. herniated disc). The medical instruments are used as prototypes for wet room testing. Their complex support structures with lots of long tight channels are the most difficult to depowder,” Marco Flury, Project Manager at Swiss m4M explains. As you will see below, Swiss m4m provided Solukon with different data on these parts.
Overall, the test enabled to identify specific considerations that should be taken into account for these applications as well as key specifications related to the piezoelectric excitation tool.
The depowdering test: 6 key steps
According to Hemank Raj, Process Development Engineer at Solukon, the depowdering test requires to assess machine data, component data, visual control prior to cleaning, perform the cleaning procedure, assess the cleaning results and ensure a visual control after the cleaning step.
1- As far as machine data are concerned, it’s important to note that the alloy used during the test is not classified as reactive. The process was carried out in a non-inert atmosphere.
2- As for the component data, Swiss m4m shared information related to the measurements of the parts (W x L x H), buildplate, buildplate thickness, weight (including buildplate), hole pattern, and material. Figures translate into this:
Component measurements |
|
|
Buildplate measurements | Round buildplate. Diameter 204 mm. | |
Buildplate thickness | 23 mm | |
Weight incl. buildplate | Approx. 13 kg | |
Hole pattern of the buildplate | TRUMPF TruPrint 2000 buildplate. No through holes. | |
Material | Stainless Steel 17-4 PH |
3- The visual control revealed there was no visual damage, and no powder lumps on the build plate which means the material can withstand moisture absorption. However, the structures of the parts seemed to be entirely filled with powder.
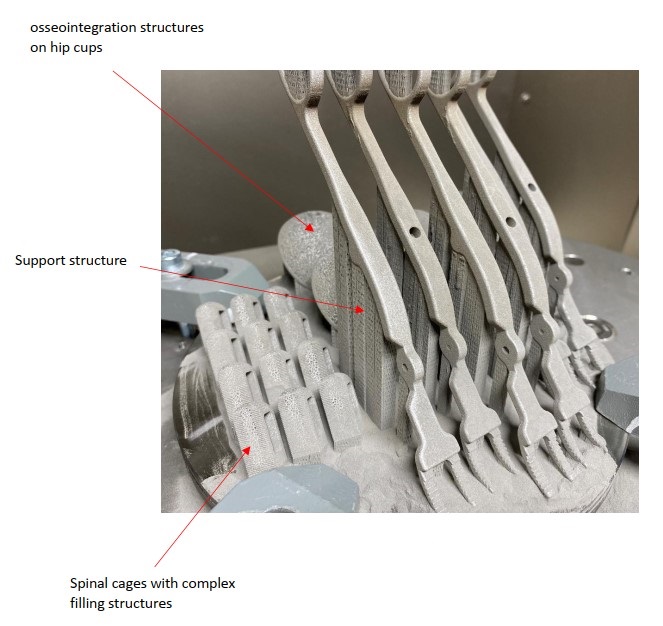
4- During the cleaning phase, the build plate was mounted on the rotating plate using four clamps.
Each part of this process was well timed and lasts approx. 17,5 minutes – from part loading, cleaning in automatic mode, cleaning part using air gun, checking cleaning results to part unloading.
For those who are familiar with a depowdering process based on pneumatic excitation, it’s important to note that the cleaning steps are similar with those conducted in a depowdering process based on ultrasonic.
Raj drew our attention to one key advantage though: “You do not have to set any excitation
parameters because the depowdering system automatically sets the best excitation (=
self-regulating frequency). In addition, the process was conducted in a volume maximum
of 53.6 dB (for reference: a normal conversation = 60 dB) which is very silent. The process
in ultrasonic excitation comes with a minimum compressed air consumption.”
(That being said, in terms of technology features, a depowdering process based on pneumatic excitation comes with a programmable high-frequency knocker to dissolve powder clumps and the SPR-technology integrates a combination of rotation and vibration).
As explained above, the test confirmed that the piezoelectric excitation tool excites the 3D-printed part at an ultrahigh frequency. According to Raj, this acceleration is enormous while the amplitude is minimal. Due to the acceleration at this frequency, the powder loses its adhesion (literally the “ground under its feet”) and slides off the surface.
The team realized that the SFM-AT350-E has proven to be the ideal depowdering candidate for delicate and fragile structures. Not to mention that with the “Digital-Factory-Tool we have access to all relevant depowdering data (e.g. temperature in the machine chamber, humidity and all customer specified presets) – crucial for data-sensitive industries like MedTech”, Raj adds.
5- After the cleaning phase, the team checked the cleaning results by visual control and by blowing into the opening of the parts with compressed air.
Not only did they not find any powder residues in the complex structures, but the powder covering the component’s surface was removed by blowing. However, to avoid any potential minor powder residues that may have been left inside the complex structures, they recommend conducting a final cleaning (ultrasonic cleaning) before using the 3D-printed part or before the next step of the manufacturing process.
In total, Flury from Swiss m4m recollected 977 grams of powder from this testing.
6- Lastly, with the visual inspection, no damages and no powder resting were found. All parts were still well attached to the substrate plate.
Concluding thoughts
First and foremost, it’s crucial to keep in mind that the time and figures outlined in this article are only meant for the depowdering process of medical 3D printed parts performed as part of this test. This means that operators should be mindful of the component data and specifications of each 3D-printed part they will have to depowder. In the end, although the SFM-AT350-E and its piezoelectric excitation tool have proven advantages compared to conventional depowdering with pneumatic excitation, a few nuances can be observed for 3D-printed parts produced in other industries or for other medical applications.
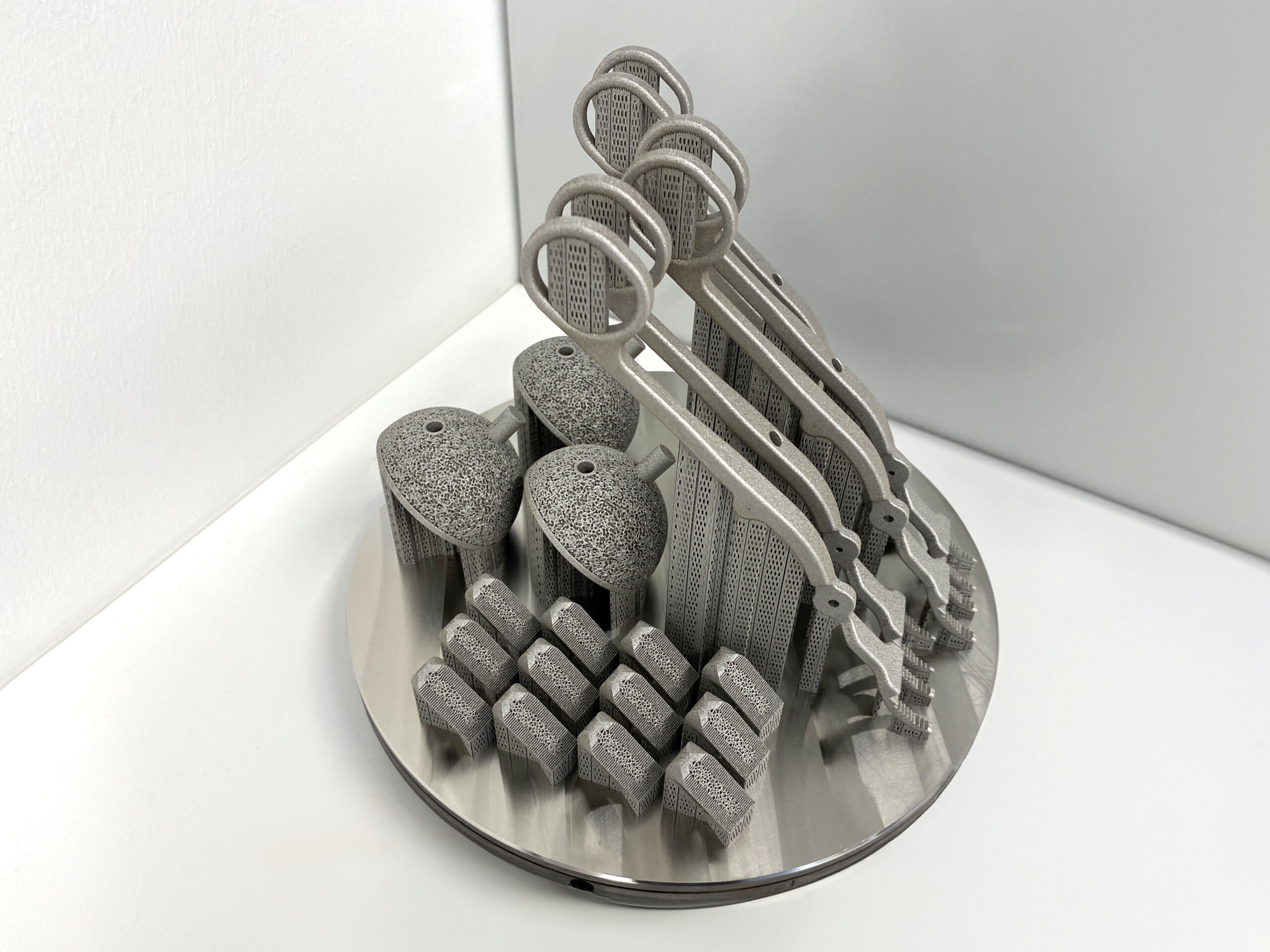
As Raj notes for instance, “compared to pneumatic excitation with a turbine or knocker, the acceleration and frequency are many times higher and the amplitude much lower. (This is why you do not see any vibration/movement of the component during excitation). The excitation frequency is between 30 kHz and 38 kHz. This means that we are far beyond the natural frequencies of the components. This prevents oscillation and damage at the resonance frequency.”
Between its ability to ensure a low-noise depowdering process, its self-regulating excitation mode and minimized compressed air consumption, this test reveals advantages that play to the strengths of this automated depowdering machine when it comes to its certification for a medical production environment. Not to mention that, even though the Digital-Factory-Tool and the SPR-Pathfinder® Software are optional tools, they remain interesting to make the most out of this machine. “With specially developed technology, we were able to set up endless rotation of the turntable in the SFM-AT350-E and thus enabled the unlimited use of the SPR-Pathfinder software”, says Andreas Hartmann, CEO/CTO at Solukon.
Overall, “the results suggest that the process works similarly well with titanium alloys. The excitation form of the SFM-AT350-E is ideal for this type of sensitive components. The cleaning process is very short and you can achieve a very high cycle rate since one single cleaning is completed in under 7.5 minutes. If we assume that loading and unloading together take 10 minutes, then you could aim for four cleaning jobs per hour with one depowdering system (given that no inert atmosphere is required where inerting time and door holding time need to be considered)”, Raj concludes.
All images: Courtesy of Solukon.
This dossier has first been published in the March – April 2024 edition of 3D ADEPT Mag.