Over the past ten years, the additive manufacturing industry has moved from prototyping to final parts production, where complexity and quality requirements are much more important. On the other hand, the industrial sector continuously evolves from low-cost mass production to more personalized production.
Mass production with additive manufacturing is one of the most important challenges for its full industrialization. According to the report “Challenges in the industrialization of additive manufacturing”, published under the AM-Motion project (Horizon 2020 Program, European Commission), some of the challenges that additive manufacturing technology will be facing in the coming years are the integration and automation of production systems, and the rise in productivity and efficiency to gain competitiveness against traditional manufacturing technologies.
The ability to manufacture on demand, to reduce logistics costs and environmental footprint, and to achieve relevant savings with reduction of stocks and physical warehouses, will result from the integration and automation of processes within the AM production environment. This means that integrating equipment and software, as well as integrating physical processes and digital thread will be the key to make the manufacture of parts in a distributed and remote way possible, guaranteeing this way their quality and traceability.
Integrating IT/OT
Additive manufacturing is the paradigm of digital manufacturing. From a 3D file, a full object can be constructed by depositing layer upon layer of material. In this process, at some point, the digital world of a file makes physical in an object. Therefore, digital and physical worlds need to integrate in the process. From a practical point of view, full integration of enterprise systems (IT) and operational systems in the shopfloor (OT) requires the fulfillment of basic steps to achieve an efficient workflow. Automation and smart planning tools are key in this process.

- Construction of a digital inventory, collecting all necessary information and digital files at every stage of the process: specifications, requirements, workflow, manufacturing & postprocessing conditions, certification needs, etc.
- Generation of customized workflow for each part, with full traceability at digital and physical stages, implementing track & trace solutions in the shopfloor, by means of QR/RFID or other suitable devices.
- Implement intelligent prioritization of manufacturing orders based on time and needs, complete process and machine occupancy to maximize productivity (and therefore ROI).
- Guarantee full access to real-time production information.
- Implement intelligent scheduling estimation and automatic replanning against any requirements update, incidents, nonconformities, or changes in demand.
Integrating processes
This workflow in additive manufacturing translates into the integration of several different processes and operations. Starting from raw material management, which must ensure compliance with storage and transport conditions, and provide traceability in storage, during feed process and after recycling. The integration of manufacturing processes (feeding, 3D printing, extraction, inspection, finishing…) presents plenty of opportunities to incorporate automation solutions in these processes, to optimize production times and gain in competitiveness. The incorporation of automation between processes or the development of hybrid and continuous manufacturing systems is no longer a novelty in the indutry. In any case, it is crucial to have an adequate traceability system.
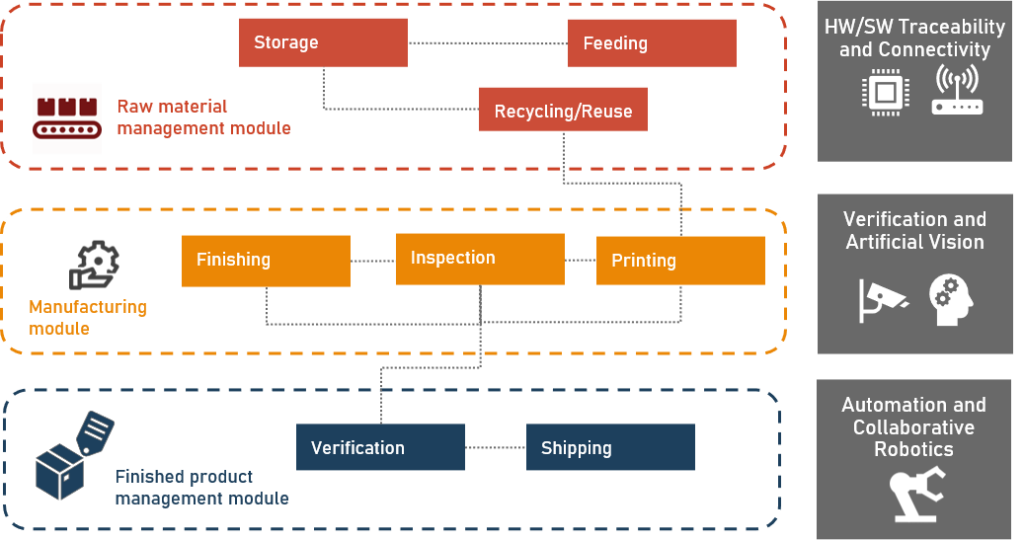
Connectivity with equipment is necessary to perform a real integration of the physical and digital manufacturing flows and allows for real-time process monitoring and validation of manufacturing parameters. Traceability and integration of production systems must be maintained until the finished product management stage. The integration with ERP (Enterprise Resources Planning) system and with MES (Manufacturing Execution System) ensures full process traceability from raw material to shipment, saving time and resources in inspection and documental management tasks.
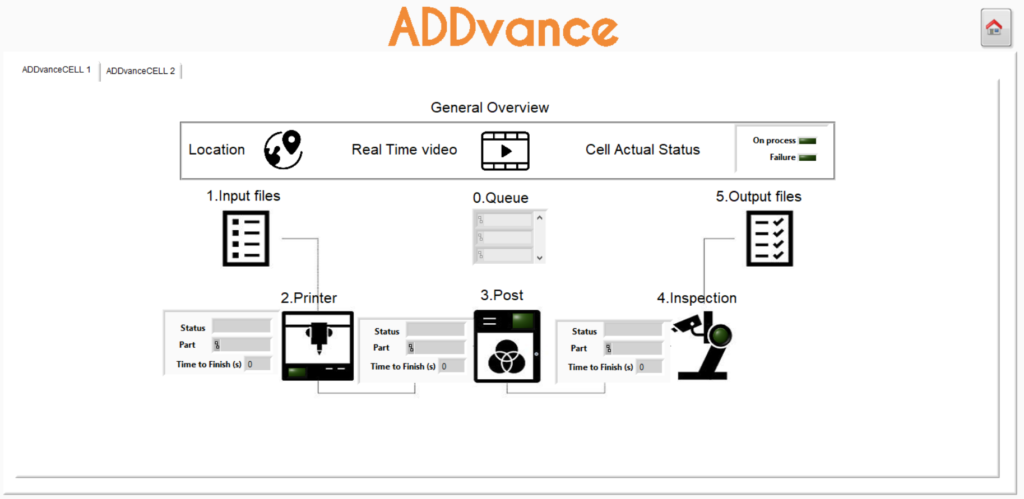
Integrating Digital technologies in AM
Some of the challenges in additive manufacturing to gain competitiveness over conventional manufacturing technologies, are reproducibility and productivity. In both cases, advances and improvements in new systems are huge, with the integration of different digital technologies, as Data Analytics and Machine Learning for process monitoring, Robotics solutions for automation or IOT (Internet of things) and Digital Platforms to connect equipment, devices and IT systems.
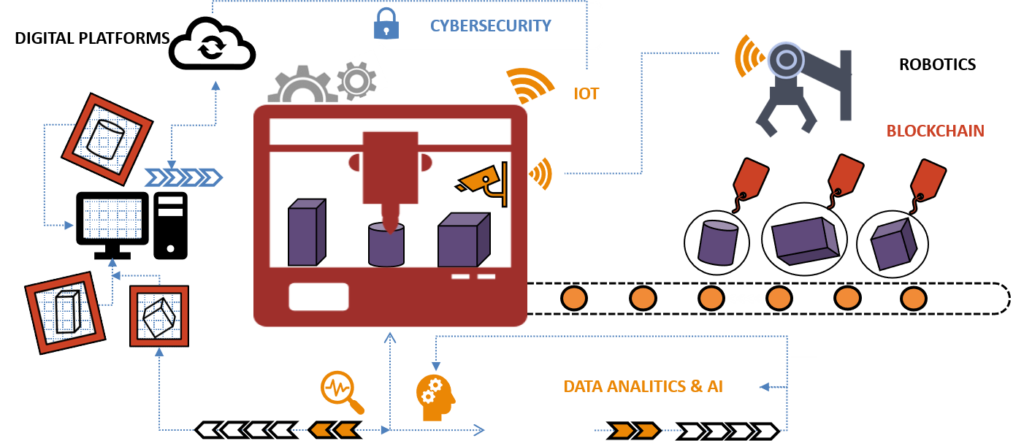
Influence of the manufacturing process
Additive manufacturing is a manufacturing process that is considered as ‘special’ as welding, adhesive or manufacturing of composite materials. This means that the effect of variability of the numerous parameters of the manufacturing process can substantially influence the results. Therefore, it is very important to define these parameters and their range of variations and monitor them during the process. The first step therefore consists in defining the parameters, in low-cost technologies. To do so, one can resort to experience or some tests that help us define the manufacturing parameters. For high-cost technologies, the trial-and-error technique can be too costly, hence the use of process simulation techniques.
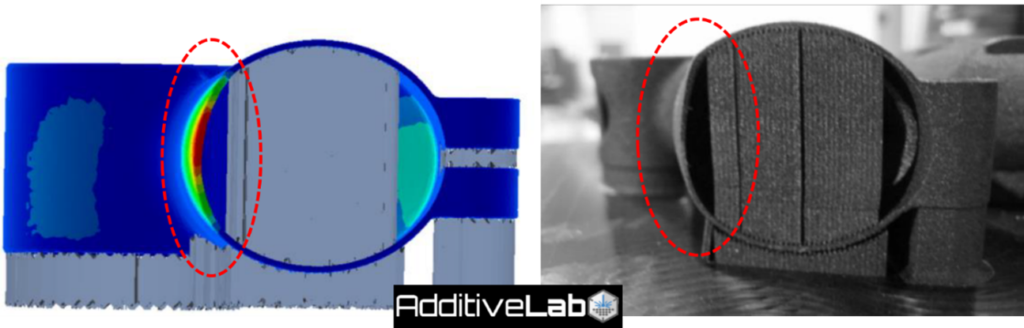
As far as process monitoring and control are concerned, let’s note that data analysis techniques using Machine Learning and Deep Learning are being used to identify potential deviations. They analyze interaction between different parameters, which would be impossible to detect with simpler monitoring techniques. Furthermore, advances in this area also include the development of predictive models (warning of deviation before it occurs) and even prescriptive (establishing action to counteract the identified deviation).
Information flow and security
Because of the nature of digital manufacturing intrinsic to additive manufacturing, security of digital thread is a critical factor. Huge progress is being made in this area, to ensure that there are no variations or attacks on data throughout the process (system security protection). This progress also lies in the fact that access to data is done in a controlled and authoritative way (intellectual property protection). These two factors are critical and essential to enable a distributed manufacturing business model.
System security (Cybersecurity) involves protecting the hardware, software, and firmware of computers (IoT and OT systems)
For the protection of intellectual property, Blockchain technology is used to track and trace the flow of information, and to assess that objects are produced in a previously validated equipment.
This feature has initially been published in the 2021 January/February issue of 3D ADEPT Mag.
ADDvance provides services and products to support an efficient industrialization of additive manufacturing. ADDvance supports their customers to build their own digital parts inventory and enable distributed and remote manufacturing, ensuring the quality and traceability indispensable in those parts by using ADDvance platform. ADDvance also commercialize fully autonomous production cells (ADDvanCELL®) enabling in-field manufacturing and remote management. ADDvanCELL® production cells integrate all the equipment and software necessary for printing, finishing and verifying, and provide the platform to manage production autonomously and remotely, with total traceability and security. ADDvanCELL® solutions can integrate robotics and artificial vision in those applications in which human interaction needs to be minimized.
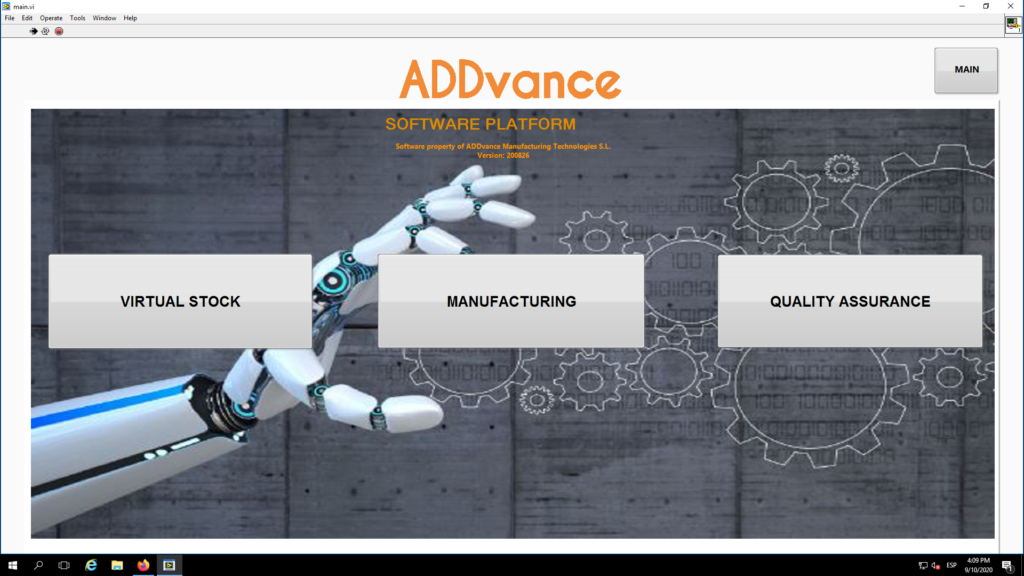