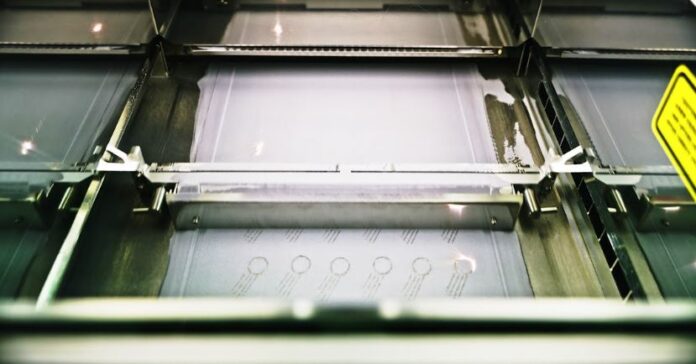
Renishaw has launched TEMPUS technology™, which enhances the productivity of its AM systems without hampering quality.
The new 3D printing technology reduces build times by 50% and will help in the usage of AM as a volume production method across industries.
The company unveiled TEMPUS technology™ at Formnext 2023 where it explained how the technology used a new scanning algorithm for its RenAM 500 series metal AM systems. This allows the laser to fire while the recoater is moving, ultimately saving 9 secs per build layer which over the cycle reduces the build time by 50%.
The new TEMPUS technology™
During the fabrication process, the recoater spreads a layer of powder and as the lasers follow the recoater, it melts the powder spread before the recoater completes its stroke. The lasers “jump over” the recoater when it goes back to the doser to collect more powder, and continue to melt the layer. This mitigates the wiper time as the lasers simultaneously start processing the new layer after finishing the previous layer as soon as the recoater starts spreading it. In this way, the TEMPUS technology™ reduces dwell time per layer and shortens cycle times.
TEMPUS technology™ uses advanced scanning algorithms that sequence layer data to maximise productivity. Although this optimisation is suitable for some AM parts geometries, all geometries can witness enhanced productivity.
AM parts having thin vertical features will experience higher productivity savings in TEMPUS technology™.
The Director of Additive Manufacturing at Renishaw, Louise Callanan explained this when she said: “Usually, the laser would turn off while the recoater is moving. Firing the laser while the recoater is moving minimises the laser off-time per build. The time and cost saving TEMPUS brings will open AM up to mass production applications where the technology would previously have been unviable.”
TEMPUS technology™ is standard fitment with new RenAM Ultra metal AM systems, which are available with quad or single laser configuration. Renishaw explained how existing RenAM 500 series customers benefit from upgrading to TEMPUS as it adds an extra layer of laser to the machine.
Computing and consumer electronics manufacturers can get it from metal component expert Alloyed who has a partnership with Renishaw and has been using its TEMPUS technology™ since 2021.
Remember, you can post job opportunities in the AM Industry on 3D ADEPT Media free of charge or look for a job via our job board. Make sure to follow us on our social networks and subscribe to our weekly newsletter : Facebook, Twitter, LinkedIn & Instagram ! If you want to be featured in the next issue of our digital magazine or if you hear a story that needs to be heard, make sure to send it to contact@3dadept.com