One usually focuses so much on end-applications that it is easy to forget that what makes an additive manufacturing-based application viable for a given industry, is a pivotal end-to-end qualification and certification process. As the name implies, technology qualification consists in verifying that a manufacturing process meets the specific requirements for its intended service but for a technology like additive manufacturing that has only started to be commercialized in the 1990s, the concept is much more complex than it seems. It takes a conversation with TÜV SÜD’s Gregor Reischle to understand the ins-and-outs of this evaluation and approval process.
Additive Manufacturing Engineer by training, Reischle brings a decade of experience in the additive manufacturing industry to the table. His ability to develop products and his experience in leading AM companies like EOS made him the ideal resource person to lead the additive manufacturing unit at TĂśV SĂśD, a unit that debuted on the AM industry about four years ago, when Reischle joined the company.
It makes sense to see TĂśV SĂśD operate in the additive manufacturing industry when one knows that the structure is an internationally active, independent service company that tests, inspects and certifies technical systems, facilities and components of all kinds. However, the thing with AM technologies is that, if the first AM processes may have been commercialized in the 1990s, a whole guideline still needs to be developed to help existing and future industries properly & commercially leverage these technologies.
What are these guidelines?
As you may know, the ultimate goal for most industries adopting additive manufacturing is to produce and utilize qualified parts that can be used in mission-critical environments and markets. To do so, several frameworks are required, and according to Reischle, dedicated frameworks are designed for specific stakeholders:
“We focus on the “pain points” of each industry player: the users – those who utilize AM equipment for production purpose – as well as machine manufacturers, material producers & software providers.
Each of these stakeholders will have unique needs: users, for instance, might need audit, training, advisory and certification, to ensure their additive manufacturing production readiness, a crucial step that requires assessing quality and viability of AM Systems and their surrounding operational processes. Furthermore, they must ensure that the AM equipment they leverage, meets health and safety requirements and their production environments must meet certain standards to minimize hazards and prevent damages. Not to mention that, beyond the reduction of hazards, and prevention of damages, a certified environment assures an organization’s customers that it can deliver industrial conform services that encompass all the steps of the AM specifications in product development & production lifecycle. From design, shop floor, to manufacturing and quality assurance.
Machine manufacturers & material producers on the other hand, have now the option to proof with a 3rd party certification that the industrial 3D printing equipment/materials they develop, delivers reproducible results. As industrial 3D printers & materials are utilized to produce parts for different industries, they should also fulfil additional requirements for those sectors – which include medical, aerospace, space, to name a few.
And the ability to meet all these requirements is the “raison d’être” of TÜV SÜD’s positioning in the AM industry”,Reischle states from the outset.
Tangible examples where we saw the German company deliver a few of these services include but are not limited to the recent certification of the AM process of LUVOCOM® 3F filament and Ultimaker S5 Pro Bundle, thequalification of 12 Manufacturing sites. Rosswag as manufacturer of metal powder for additive manufacturing, -as well as the Part report services on validation foroperational use of an additively manufactured mission critical parts in the railway sector.
The primary focus might be dedicated to industrial stakeholders but the global head of industrial additive manufacturing also points out the company’s ability to address some health issues raised by desktop 3D printer emissions as well as specific concerns regarding the food industry.
A closer look at the qualification & certification processes for materials, equipment and 3D printed parts
Paths to qualifying materials and processes vary from one structure to another. As far as materials are concerned, we used to see their qualification for a given manufacturing process when they are approved by 3D printer manufacturers or after individual testing and inspection.
This latter process can also be applied for the qualification of 3D printers. It might include statistical-based qualification rooted in empirical testing, equivalence-based qualification if the idea is to demonstrate that a new material or process is similar to a material or process that has already been qualified or a model-based qualification. In this case, experts should prove the performance of the material or the equipment with simulation software and corroborate it with less testing.
At this point, for those who are not familiar with all this jargon, it is crucial to understand that there is a difference between qualification and certification.
The qualification of a prototype design/material /product during the development/testing phase aims to find out whether it meets the specified requirements for a specific phase. In this case, engineers are trying to determine if they have designed or built the product as per the requirements.
As for certification, it consists in assessing a material/product/component during or at the end of the development process /regular production to confirm whether or not, it meets specified technical requirements. These are usually publicly known and released by standardisation bodies like DIN, ISO, ASTM and used for certification by institutions like TUV SUD. –
In both cases, TĂśV SĂśD has the ability to support AM companies. Despite the viability of the aforementioned qualification processes, organizations do not often look at the bigger picture, which in the end, leads to more expensive processes when they address qualification and certification modules one by one.
By highlighting TÜV SÜD’s modular approach that their team has been developing during the past four years, Reischle focuses the debate on what should be the first point every organization should look at when it comes to qualification and certification in general: employees.
“We train professionals within their respective industrial AM area of expertise. Thereafter, we establish with organizations how to setup a state of the art quality assurance, which is especially important if they want to focus on production. To do so, the facility should meet AM specific DIN/ISO/ASTM standards developed within the TC 261.
Thereafter, we need to have a value proposition for the machines, materials and processes. With Ultimaker and LEHVOSS Group for instance, we combined the 3D printer and the material to certify the “reproducible print process”. Once AM machines and materials are certified as explained before, it becomes much easier for every user to make the end-customers benefit from the production advantages.
The truth is, the good old “trial & error» AM implementation approach is no longer “state of the art” and has to decrease. All new bees focusing on industrial AM should use the “standardised implementation approach. Otherwise the risk to fail remains very high. And the implementation of AM will not scale.
This is mainly due to the standardized implementation path that manages to answer all these questions industrials used to ask themselves: how to set up a production line? How to build up a quality management and production guide? How to set up a build process that enables reproducibility? etc. We are changing the way production is implemented in the industry by focusing on how to save time and costs, by supporting organizations to scale faster, to regulate their processes and to achieve industrial readiness.
As far as 3D printed products are concerned, we are also uniquely positioned to speed up their certification”, he explains. Taking the example of the 3D printed part produced by Siemens Mobility GmbH, the expert laid emphasis on the fact that the certification process is not that different from machines and materials certification. For specific applications, it is important to set up a risk management system that addresses both the applications & AM technology specific risks. Here, they needed to ensure that the part is safe and reproducible, hence the numerous tests the part underwent after its production at Siemens Mobility’s facility. “We thereafter issued a report on the remaining specifications risks dedicated to the application itself as it was crucial for the part to meet the additional requirements of the railway sector. As a notified body, TÜV SÜD also has the authority to assess the conformity of certain products before they are placed on the market”, the expert points out.
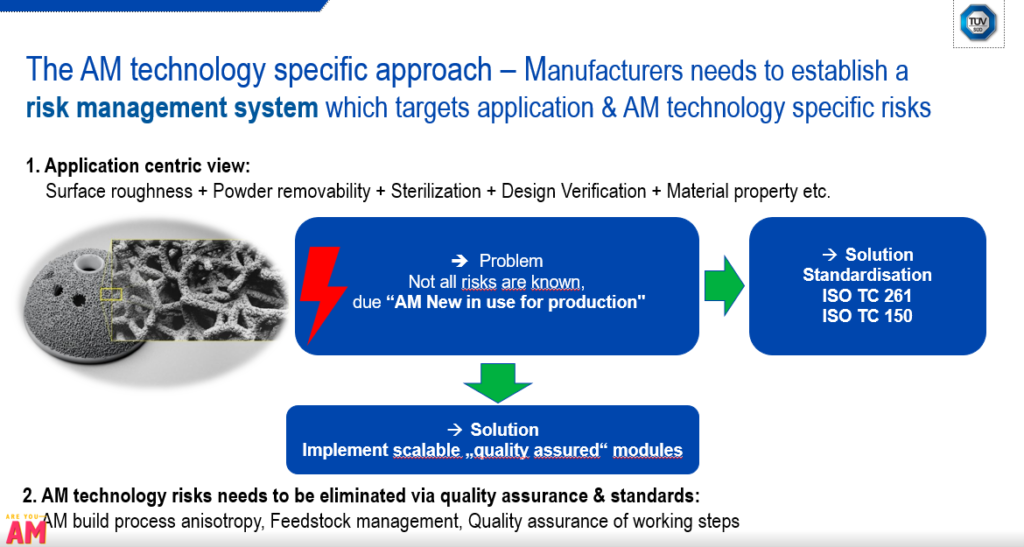
The challenge with these application-centric processes is that not all risks can always be known due to the “relatively new usage of AM in production”.
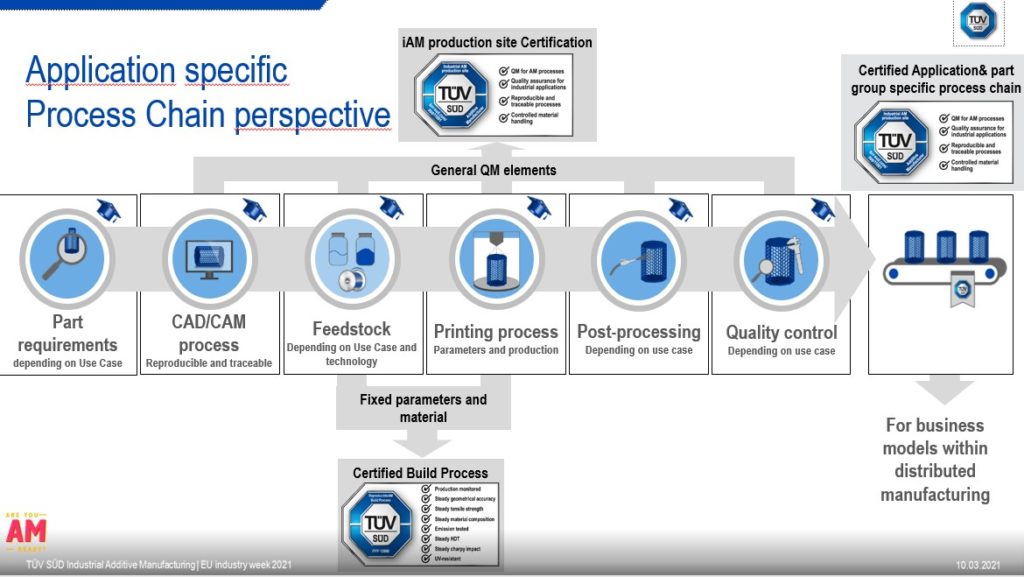
The next challenges to address
With the growing demand for standardization in additive manufacturing, several barriers need to be addressed across various key verticals adopting AM technologies and within manufacturing processes.
Speaking of standardization within manufacturing processes, Reischle outlines that there are various AM technologies and the team at TÜV SÜD understands that “each AM technology is unique. Therefore, the challenges operators faced at the production level certainly vary from one technology to another. That’s why we are collaborating with all involved industry players at the ISO/TC 261 that aims to standardise the processes of Additive Manufacturing, the process chains [(Data, Materials, Processes, Hard- and Software, Applications), test procedures, quality parameters, supply agreements, environment, health and safety, fundamentals and vocabularies].”
As part of this group, Reischle is the convener for the JG 75 Conformity Assessment, Quality Assurance and risks and the JG 80, which takes care of 3D printing in the construction industry.
Moreover, with the increasing development of advanced manufacturing technologies and robotics, manufacturing is undergoing a transformation that requires a cross-functional implementation of seamless connected processes. This will inevitably lead to fundamental improvements, which will enable 100% product transparency and traceability.
Whilst this transformation drives data collection and connectivity, it also raises certain concerns when it comes to security. To prevent vulnerabilities or cyberattacks to occur throughout the component or system lifecycle, TĂśV SĂśD is capable to support with the implementation of the international standard IEC 62443. That guarantees that all applicable security aspects are addressed in a structured manner.According to the company, this includes a systematic approach to cybersecurity throughout the stages of specification, integration, operation, maintenance and decommissioning.
Furthermore, in this mission to facilitate adoption and trust in AM technologies, the company joined forces with global standards organization ASTM International to develop new educational, advisory, qualification and certification services in sectors such as transport (land and air), industrial plants, consumer products and healthcare. Additionally TUV SUD is very active within the MgA Network , where over 100 international companies collaboratively work on the success of AM technologies.
In four years of activity on the AM market, TÜV SÜD can legitimately say it has raised awareness on the importance of qualification and certification for AM in Europe. With a global team across the world – in the ASEAN region with an entry point in Singapore as well as in Japan, the company is determined to “move forward additive manufacturing implementation into the industrial world.
This Interview has initially been posted in the March/April issue of 3D ADEPT Mag.
Remember, you can post free of charge job opportunities in the AM Industry on 3D ADEPT Media or look for a job via our job board. Make sure to follow us on our social networks and subscribe to our weekly newsletter : Facebook, Twitter, LinkedIn & Instagram ! If you want to be featured in the next issue of our digital magazine or if you hear a story that needs to be heard, make sure to send it to contact@3dadept.com