On se concentre généralement tellement sur les applications finales qu’il est facile d’oublier que ce qui rend une application basée sur la fabrication additive viable pour une industrie donnée, c’est un processus pivot de qualification et de certification de bout en bout. Pour une technologie comme la fabrication additive qui n’a commencé à être commercialisée que dans les années 1990, le concept est beaucoup plus complexe qu’il n’y paraît. Un entretien avec Gregor Reischle, de TÜV SÜD, pour comprendre les tenants et aboutissants de ce processus d’évaluation et d’approbation.
Ingénieur en fabrication additive de formation, Gregor Reischle apporte à la table une décennie d’expérience dans le secteur de la fabrication additive. Sa capacité à développer des produits et son expérience à la tête d’entreprises de fabrication additive comme EOS ont fait de lui la personne ressource idéale pour diriger l’unité de fabrication additive de TÜV SÜD, une unité qui a fait ses débuts dans le secteur de la fabrication additive il y a environ quatre ans, lorsque Reischle a rejoint l’entreprise.
Il est logique de voir TÜV SÜD opérer dans l’industrie de la fabrication additive quand on sait que la structure est une société de services indépendante, active au niveau international, qui teste, inspecte et certifie des systèmes techniques, des installations et des composants de toutes sortes. Cependant, le problème avec les technologies de FA est que, si les premiers processus de FA ont pu être commercialisés dans les années 1990, toute une ligne directrice doit encore être développée pour aider les industries existantes et futures à exploiter correctement et commercialement ces technologies.
Quelles sont ces directives ?
Comme vous le savez peut-être, l’objectif ultime de la plupart des industries qui adoptent la fabrication additive est de produire et d’utiliser des pièces qualifiées qui peuvent être utilisées dans des environnements et des marchés critiques. Pour ce faire, plusieurs cadres sont nécessaires, et selon Reischle, des cadres dédiés sont conçus pour des parties prenantes spécifiques :
« Nous nous concentrons sur les « points sensibles » de chaque acteur de l’industrie : les utilisateurs – ceux qui utilisent l’équipement de FA à des fins de production – ainsi que les fabricants de machines, les producteurs de matériaux et les fournisseurs de logiciels.
Chacune de ces parties prenantes aura des besoins uniques : les utilisateurs, par exemple, peuvent avoir besoin d’un audit, d’une formation, d’un conseil et d’une certification pour s’assurer qu’ils sont prêts à produire par fabrication additive, une étape cruciale qui nécessite d’évaluer la qualité et la viabilité des systèmes de FA et des processus opérationnels qui les entourent. En outre, ils doivent s’assurer que l’équipement de FA qu’ils utilisent répond aux exigences en matière de santé et de sécurité et que leurs environnements de production respectent certaines normes pour minimiser les risques et prévenir les dommages. Sans oublier qu’au-delà de la réduction des risques et de la prévention des dommages, un environnement certifié garantit aux clients d’une entreprise qu’elle peut fournir des services de conformité industrielle qui englobent toutes les étapes des spécifications de la FA dans le cycle de vie du développement et de la production des produits. De la conception à l’atelier, en passant par la fabrication et l’assurance qualité.
D’autre part, les fabricants de machines et les producteurs de matériaux ont désormais la possibilité de prouver par une certification tierce que les équipements et matériaux d’impression 3D industrielle qu’ils développent donnent des résultats reproductibles. Comme les imprimantes 3D et les matériaux industriels sont utilisés pour produire des pièces pour différentes industries, ils doivent également répondre à des exigences supplémentaires pour ces secteurs – qui incluent le médical, l’aérospatial, l’espace, pour n’en citer que quelques-uns.
Et la capacité à répondre à toutes ces exigences est la « raison d’être » du positionnement de TÜV SÜD dans l’industrie de la FA », déclare d’emblée M. Reischle.
Parmi les exemples concrets où nous avons vu l’entreprise allemande fournir quelques-uns de ces services, citons notamment la récente certification du processus de FA du filament LUVOCOM® 3F et de l’ensemble Ultimaker S5 Pro, la qualification de 12 sites de fabrication. Rosswag en tant que fabricant de poudre métallique pour la fabrication additive, – ainsi que les services de rapport partiel sur la validation de l’utilisation opérationnelle d’une pièce critique fabriquée de manière additive dans le secteur ferroviaire.
L’accent est peut-être mis sur les acteurs industriels, mais l’expert en fabrication additive industrielle souligne également la capacité de l’entreprise à répondre à certains problèmes de santé soulevés par les émissions des imprimantes 3D de bureau ainsi qu’à des préoccupations spécifiques concernant l’industrie alimentaire.
Un regard plus attentif sur les processus de qualification et de certification des matériaux, des équipements et des pièces imprimées en 3D
Les chemins vers la qualification des matériaux et des processus varient d’une structure à l’autre. En ce qui concerne les matériaux, nous avons l’habitude de voir leur qualification pour un processus de fabrication donné lorsqu’ils sont approuvés par les fabricants d’imprimantes 3D ou après des tests et inspections individuels.
Ce dernier processus peut également être appliqué pour la qualification des imprimantes 3D. Il peut s’agir d’une qualification basée sur des statistiques et fondée sur des tests empiriques, d’une qualification basée sur l’équivalence si l’idée est de démontrer qu’un nouveau matériau ou processus est similaire à un matériau ou processus déjà qualifié ou d’une qualification basée sur un modèle. Dans ce cas, les experts doivent prouver les performances du matériau ou de l’équipement à l’aide d’un logiciel de simulation et les corroborer par des essais moins nombreux.
À ce stade, pour ceux qui ne sont pas familiers avec tout ce jargon, il est crucial de comprendre qu’il existe une différence entre la qualification et la certification.
La qualification d’un prototype de conception/matériel/produit pendant la phase de développement/essai vise à déterminer s’il répond aux exigences spécifiées pour une phase spécifique. Dans ce cas, les ingénieurs tentent de déterminer s’ils ont conçu ou construit le produit conformément aux exigences.
Quant à la certification, elle consiste à évaluer un matériau/produit/composant pendant ou à la fin du processus de développement/production régulière pour confirmer qu’il répond ou non à des exigences techniques spécifiées. Celles-ci sont généralement connues et publiées par des organismes de normalisation comme DIN, ISO, ASTM et utilisées pour la certification par des institutions comme TUV SUD. –
Dans les deux cas, TÜV SÜD est en mesure de soutenir les entreprises de FA. Malgré la viabilité des processus de qualification susmentionnés, les organisations n’ont pas souvent une vue d’ensemble, ce qui, au final, entraîne des processus plus coûteux lorsqu’elles abordent les modules de qualification et de certification un par un.
En mettant en avant l’approche modulaire de TÜV SÜD que son équipe a développée au cours des quatre dernières années, Reischle centre le débat sur ce qui devrait être le premier point sur lequel toute organisation devrait se pencher lorsqu’il s’agit de qualification et de certification en général : les employés.
« Nous formons des professionnels dans leur domaine d’expertise industriel AM respectif. Ensuite, nous établissons avec les organisations comment mettre en place une assurance qualité de pointe, ce qui est particulièrement important si elles veulent se concentrer sur la production. Pour ce faire, l’installation doit répondre aux normes DIN/ISO/ASTM spécifiques à l’AM développées au sein du TC 261.
Ensuite, il faut avoir une proposition de valeur pour les machines, les matériaux et les processus. Avec Ultimaker et LEHVOSS Group par exemple, nous avons combiné l’imprimante 3D et le matériau pour certifier le « processus d’impression reproductible ». Une fois que les machines et les matériaux d’AM sont certifiés comme expliqué précédemment, il devient beaucoup plus facile pour chaque utilisateur de faire bénéficier les clients finaux des avantages de la production.
La vérité est que la bonne vieille approche de mise en œuvre de la FA par « essais et erreurs » n’est plus « l’état de l’art » et doit diminuer. Toutes les nouvelles abeilles qui se concentrent sur l’AM industriel devraient utiliser « l’approche de mise en œuvre standardisée ». Sinon, le risque d’échec reste très élevé. Et la mise en œuvre de la FA ne se fera pas à l’échelle.
Ceci est principalement dû au parcours de mise en œuvre standardisé qui parvient à répondre à toutes ces questions que les industriels se posaient : comment mettre en place une ligne de production ? Comment construire un guide de gestion de la qualité et de la production ? Comment mettre en place un processus de fabrication permettant la reproductibilité ? etc. Nous changeons la façon dont la production est mise en œuvre dans l’industrie en nous concentrant sur les moyens de gagner du temps et de réduire les coûts, en aidant les organisations à passer à l’échelle plus rapidement, à réguler leurs processus et à atteindre la maturité industrielle.
En ce qui concerne les produits imprimés en 3D, nous sommes également dans une position unique pour accélérer leur certification », explique-t-il. Prenant l’exemple de la pièce imprimée en 3D produite par Siemens Mobility GmbH, l’expert a mis l’accent sur le fait que le processus de certification n’est pas si différent de la certification des machines et des matériaux. Pour les applications spécifiques, il est important de mettre en place un système de gestion des risques qui traite à la fois les risques spécifiques aux applications et à la technologie de FA. Dans le cas présent, il fallait s’assurer que la pièce était sûre et reproductible, d’où les nombreux tests que la pièce a subis après sa production dans les installations de Siemens Mobility. « Nous avons ensuite publié un rapport sur les risques résiduels liés aux spécifications, consacré à l’application elle-même, car il était essentiel que la pièce réponde aux exigences supplémentaires du secteur ferroviaire. En tant qu’organisme notifié, TÜV SÜD est également habilité à évaluer la conformité de certains produits avant leur mise sur le marché », souligne l’expert.
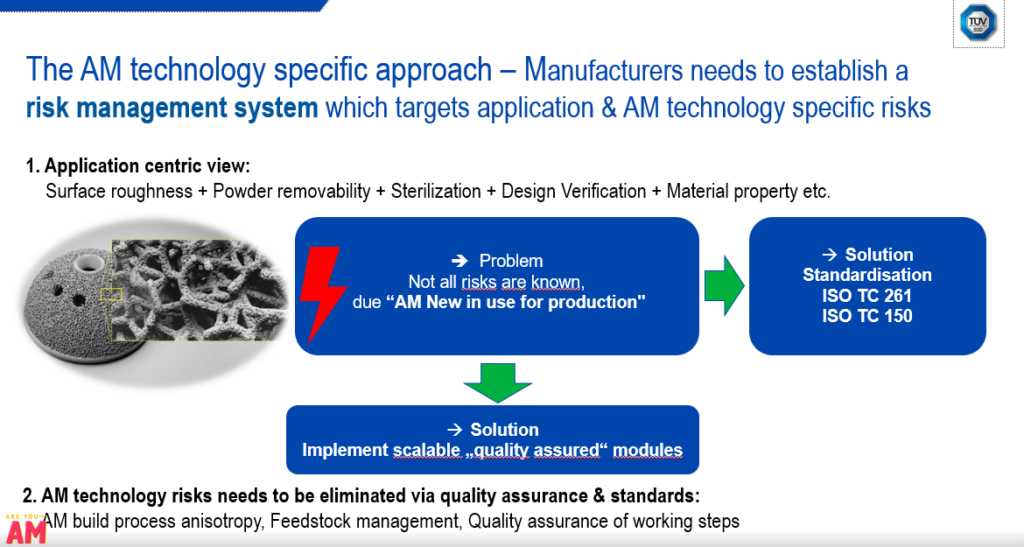
Le défi de ces processus centrés sur l’application est que tous les risques ne peuvent pas toujours être connus en raison de « l’utilisation relativement nouvelle de la FA en production ».
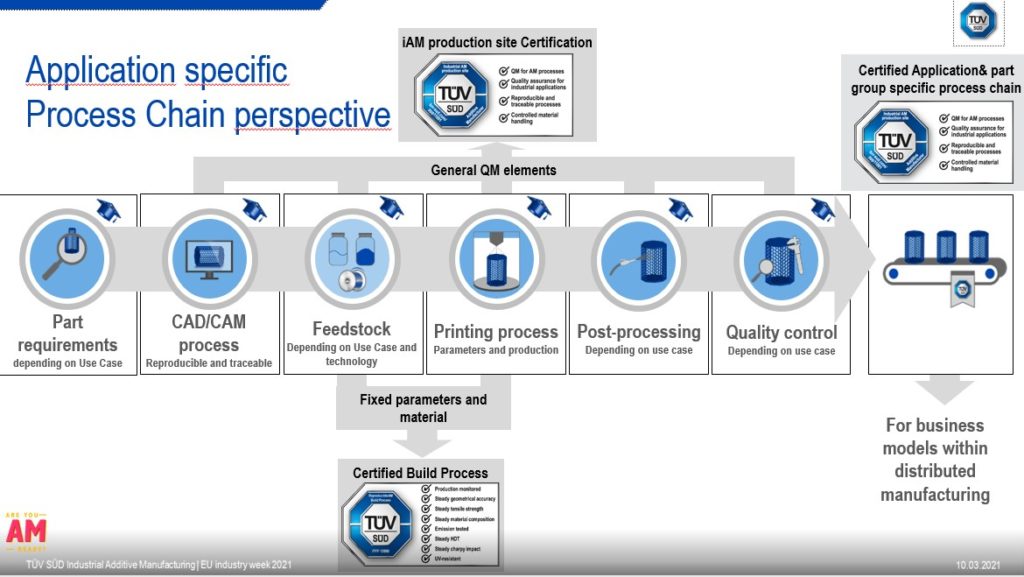
Les prochains défis à relever
Avec la demande croissante de normalisation dans la fabrication additive, plusieurs obstacles doivent être levés dans les différents secteurs clés qui adoptent les technologies de FA et dans les processus de fabrication.
En ce qui concerne la normalisation au sein des processus de fabrication, Reischle souligne qu’il existe différentes technologies de FA et que l’équipe de TÜV SÜD comprend que « chaque technologie d’AM est unique. Par conséquent, les défis auxquels les opérateurs sont confrontés au niveau de la production varient certainement d’une technologie à l’autre. C’est pourquoi nous collaborons avec tous les acteurs industriels concernés au sein de l’ISO/TC 261, qui vise à normaliser les processus de fabrication additive, les chaînes de processus [(données, matériaux, processus, matériel et logiciel, applications), les procédures d’essai, les paramètres de qualité, les accords d’approvisionnement, l’environnement, la santé et la sécurité, les principes fondamentaux et les vocabulaires] ».
Au sein de ce groupe, Reischle est l’animateur du ‘Joint Group’ (JG) 75 « Évaluation de la conformité, assurance de la qualité et risques » et du JG 80, qui s’occupe de l’impression 3D dans le secteur de la construction.
En outre, avec le développement croissant des technologies de fabrication avancées et de la robotique, la fabrication subit une transformation qui nécessite une mise en œuvre transversale de processus connectés sans faille. Cela entraînera inévitablement des améliorations fondamentales, qui permettront une transparence et une traçabilité à 100 % des produits.
Si cette transformation favorise la collecte de données et la connectivité, elle suscite également certaines inquiétudes en matière de sécurité. Pour éviter les vulnérabilités ou les cyberattaques tout au long du cycle de vie des composants ou des systèmes, TÜV SÜD est en mesure de vous aider à mettre en œuvre la norme internationale IEC 62443. Cela garantit que tous les aspects de sécurité applicables sont traités de manière structurée. Selon l’entreprise, cela inclut une approche systématique de la cybersécurité tout au long des étapes de spécification, d’intégration, d’exploitation, de maintenance et de mise hors service.
En outre, dans le cadre de cette mission visant à faciliter l’adoption et la confiance dans les technologies de FA, l’entreprise s’est associée à l’organisme international de normalisation ASTM International pour développer de nouveaux services d’éducation, de conseil, de qualification et de certification dans des secteurs tels que les transports (terrestres et aériens), les installations industrielles, les produits de consommation et les soins de santé. En outre, TUV SUD est très actif au sein du réseau MgA, où plus de 100 entreprises internationales collaborent pour faire avancer les technologies de FA.
En quatre ans d’activité sur le marché de la FA, TÜV SÜD peut légitimement dire qu’il a fait prendre conscience de l’importance de la qualification et de la certification pour la FA en Europe. Avec une équipe internationale présente dans le monde entier – dans la région de l’ANASE avec un point d’entrée à Singapour ainsi qu’au Japon, l’entreprise est déterminée à « faire avancer la mise en œuvre de la fabrication additive dans le monde industriel. »
Ce contenu a été initialement publié dans le numéro de Mars/Avril de 3D ADEPT Mag.