One of the very first additive manufacturing applications in the jewelry industry dates back to 2008: a ring 3D printed in gold, one of the most preferred precious metals for fine jewelry. Over time, innovation in the field has opened up opportunities for jewelry makers and service bureaus to tap into the opportunities offered by AM. The thing is, just like with any manufacturing business, there is a need to scale up, and to do so responsibly – and that’s something the jewelry industry struggles to achieve with Precious Metals AM.
Â
Described as rare metals with a high economic value, precious metals are chemically inert and less reactive than other elements. Unlike in the past where they were mainly used as currency, today, they are regarded as investment and industrial raw materials that can be leveraged across specific industries.
For this niche market, the discussion pops up at a time when consumers have high expectations for what they buy. Ethical sourcing and sustainability issues are now too big to be ignored, even by the most luxurious brands that have built their empire under an unsaid “don’t ask, don’t tell” policy that would retain the mystique of their amazing works — or perhaps make them more attractive to the eyes of the buyer.
The current presumption is that since AM is by nature a “sustainable fabrication process”, it would be much easier to demonstrate the sustainability approach of luxurious jewel brands producing products with precious metals. How far or how close are we from this presumption? That’s the one billion dollar question we would like to address in this exclusive feature.
To discuss this topic, we will explore:
I – Types and main characteristics of precious metals
II – Types of AM technologies that can process precious metals
III – The business case with circular economy and the reason why is it difficult to scale up Precious Metal AM in the jewelry industry
While the focus will be made on jewelry applications, it should be noted that precious metals can also be used in other vertical industries. These industries could be cited when and where required.
I- Types and main characteristics of precious metals
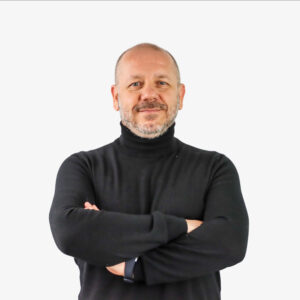
“Precious metals present unique characteristics compared to other metals. They do not oxidize to high temperatures, withstand high corrosion, and do not chemically interact with the environment. Characterized by a long lifetime, they are usually ductile and more lustrous in appearance. While the standards will introduce other material candidates as precious metals, there are currently four primary precious metals on the market: gold, platinum, silver, and palladium”, Damiano Zito, CEO of AM service bureau Progold S.p.A. told 3D ADEPT Media from the outset.
As far as AM is concerned, the technology is suitable for industrial applications when it processes fine spherical precious metal powders made of gold, silver, platinum and palladium alloys. Once refined for AM, they integrate a very fine-grained microstructure, can easily be handled, and deliver high purity and excellent flowability.
“While gold and platinum remain the most widely used precious metals in AM, silver remains the cheapest one compared to other metals. That’s why, we easily see more applications with silver”, David Fletcher completes. The latter is a precious metals 3D printing expert and ex-Head of Business Development AM at Cooksongold, UK’s largest one-stop shop for jewelry makers.
Available in different forms, the forms granules or sponge / powder are most appropriate for industrial use.
Gold – one of the most widely known in jewelry – is unique for its durability, malleability, and ability to conduct both heat and electricity.
Used in jewelry and in other industrial applications, silver is known for its conductive, anti-bacterial and malleable properties.
Platinum on the other hand, receives a great demand from the automotive industry, where it is used to reduce the harmfulness of emissions. When transformed into an alloy, it enables to achieve key applications in jewelry and dentistry. “Platinum is much more mature when we look at metal 3D printing applications that can be achieved with precious metals; not to mention that it is compliant with the industry standards”, the representative of Progold notes. Unlike other precious metals, it is easy to 3D print platinum thanks to its low reflectivity and low thermal conductivity. For instance, an application that may be produced in three hours using platinum might take up to ten hours with silver.
It might not be known as much as gold, silver and platinum, but palladium is a noble metal that is a great fit for jewelry and watch making applications. Resistant to erosion of air and acids, the material is valued for its biocompatibility and resistance to thermal wear. It is also one of the most challenging materials in regard to processing and refining, and incurs high costs in capital.
II – Types of AM technologies that can process precious metals
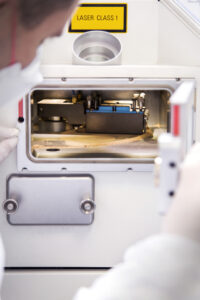
According to Fletcher, the difficulties in 3D printing precious metals lie in the ability of the operator to understand the interdependences between the machine, the powder and the whole process. Taking the example of Cooksongold, he explained that the company can 3D print in 18k yellow gold, 18k red gold, 18k white gold, 925 silver and 950 platinum due to parameters it qualified for their use on EOS machines.
That being said, it should be noted that additive manufacturing technologies that can process precious metals are divided into two groups: indirect 3D printing methods and direct 3D printing methods. For those who do not know, indirect manufacturing refers to the use of AM to produce tools like dies and molds for traditional processes, while direct 3D printing/manufacturing refers to the creation of parts straight from the design.
In indirect 3D printing, the operator 3D prints a wax pattern that will be used in investment casting to produce the final product. In such operations, resin 3D printing technologies such as SLA are used to create the patterns from castable, wax-like resins. Once the pattern is fabricated, it is covered in a heat-resistant material such as plaster and placed into an oven where the wax is melted. The molten precious metal is then poured into the mold, filling the space left by the wax.
As far as direct manufacturing is concerned, Progold’s CEO explains that Powder-Bed Fusion (also known as Selective Laser Melting) is the most widely used AM process with precious metals. Other technologies that can also be worth exploring are Binder Jetting and Material Jetting.**
“In general, any technology that can process metals, can also process precious metals. However, the appropriate use of powders is of paramount importance to make the most of the manufacturing process and deliver a product with good price-quality ratio”, Zito outlines.
A similar argument has been highlighted by Fletcher. The truth is, given the high value of precious metals, sometimes, the powder that is used for the additive production is worth more than the machine itself. In fact, sometimes, the price of the precious metal can outpace the price of the 3D printer used to process it. That’s the reason why, a lost is an additive production of non-precious metals is less costly than a lost in an additive production of precious metals.
“On the other hand, there is an interest in the use of Binder Jetting technology for manufacturing silver. [Remember this qualification of Sterling Silver for Desktop Metal’s binder jetting technology]. One of the key challenges though, is the fact that silver is an ideal precious metal for mass production, but the resolution of binder jetting does not meet the requirements of mass production yet. From a sustainability standpoint, the technology has the same carbon footprint that traditional technologies. However, SLM currently remains a top-tier technology for precious metals because the small size of the build volume makes it a great deal to save material on the one hand; on the other hand, the technology can enable to save 3 or 4 times the carbon footprint that you usually generate with the traditional technology”, Zito explains.
On another note, Material Jetting might be the least highlighted but it is typically used with highly conductive silver or gold inks to 3D print electronic devices such as antennas, PCB prototypes, circuitry and sensors.
That being said, indirect 3D printing may be the most popular and less costly option when working with precious metals but the use of direct 3D printing processes is currently fostered by the need for more customization and faster time-to-market. But can jewelry brands scale up this process while remaining sustainable?
III – The business case with circular economy and the reason why it is difficult to scale up Precious Metal AM in the jewelry industry.
All three experts invited to this article agree with this truth: “there is no linear economy in Precious Metals Additive Manufacturing (PMAM)”. The industry of precious metals itself relies on a circular economy approach.
The basic idea behind a circular economy is to create closed loops where both waste and new inputs are minimized and existing items/materials get re-purposed, repaired or recycled. In a linear economy, raw materials are extracted, transformed into products (often producing waste in the process), and eventually discarded.
Here is the thing, in fine jewelry, most of the components that go into making it are entirely recyclable. Precious metals such as gold, silver and platinum can be recycled over and over again with no loss of quality.
So, where does the problem lie? Probably in the correlation that should exist between sustainability and scalability. By definition, sustainability is the “idea that goods and services should be produced in ways that do not use resources that cannot be replaced and that do not damage the environment.” It is also “the ability to continue at a particular level for a period of time”.
As organizations are currently exploring new ways to move forward in their sustainability journey, Michela Ferraro-Cuda, Course Director, MA Luxury Jewellery Management, and a Lecturer in Luxury Jewellery and Ethical Branding, at Birmingham City University, UK, draws attention to the fact that sustainability currently concerns three main aspects: Profit, People and Planet.
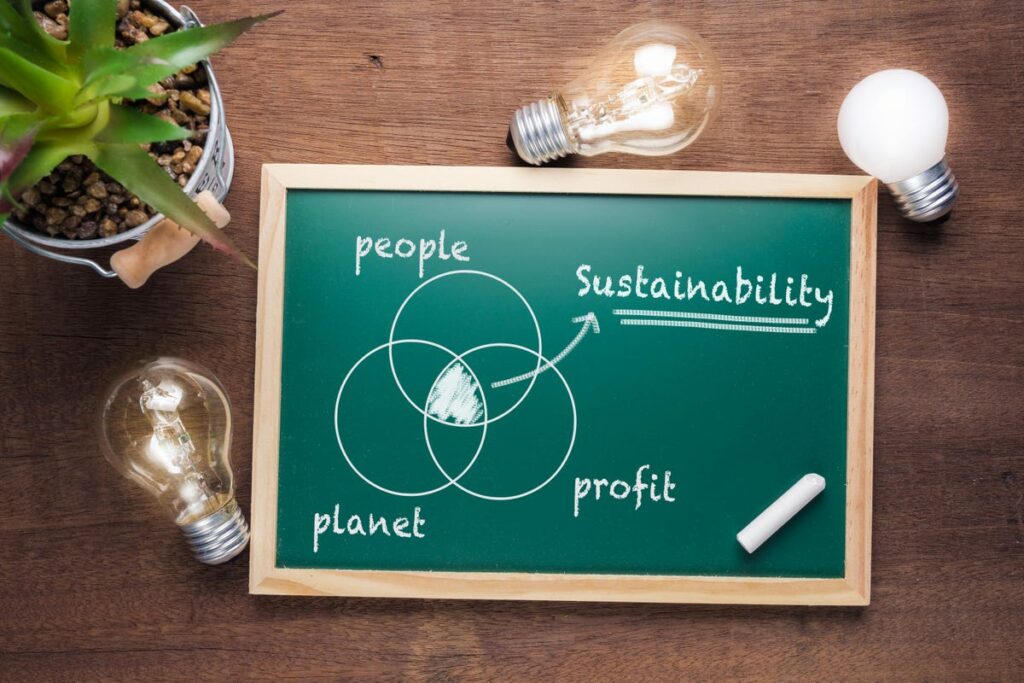
“First, not only should we agree with the type of sustainability we refer to, but we should also keep in mind that an organization can truly say it is sustainable when it is responsible vis-à -vis these three aspects: it should be profitable, and responsible vis-à -vis its people and the planet” Ferraro-Cuda highlights. Based on our conversation with Ferraro-Cuda, there are two groups of people in this sustainability journey; each of them employing or may employ a different path to sustainability:
People | Planet | Profit | |
Artisans | Small group of people. | Produce and distribute locally which is good for the environment. However, they use “mercury” in their processes because it is cheap, but it is very damaging for the environment as it releases harmful gases. | Do not make too much profit. |
Big corporations |
The traditional jewelry industry is often pointed at as an industry that exploits people and that does not have ideal working conditions (minimum wage, environment, etc.) but this can change with AM. Less people involved in the manufacturing value chain due to appropriate technologies. |
With AM in particular, they can leverage the exact amount of powder needed for manufacturing – and depending on the technology leveraged, they might save time and energy. Can apply the concept of “distributed manufacturing” to produce locally with AM. |
Can easily make profit thanks to marketing resources. |
On paper, leading jewelry brands hold all the cards (financial resources included) to be successful in using AM for precious metals. In reality, only a very short number of organizations are exploring the AM route. For Ferraro, there is only one reason that can explain this: “the lack of data to support their decisions.” Is it not the very one thing we request from AM companies and AM users? Releasing data that demonstrates how sustainable a use case is, is the only way to back up words with actions.
At the end of the day, the price of precious metals remains very expensive – let alone the price of AM technologies. Big corporations won’t take the risk to produce with AM what they can produce at cheaper costs with CNC or casting.
To this, Damiano Zeto replies that big corporations should realize that the end customer likes to change and increasingly wants customized products and that’s something that AM alone can enable while allowing to control all the manufacturing-related costs. For the CEO, it’s “a matter of time and a problem of culture”. As he reflects on his company’s journey, he realized that they have been on this market for a decade now, and it’s been a few years that other companies have penetrated this market. “This means that there is a demand that is increasing over time, and that’s positive for the AM industry”, he concludes.
Conclusion
As a report from consultancy firm SmarTech outlines, the penetration of AM into low-batch, high-end, high-performance parts production is the most natural evolution for the use of AM in global manufacturing. The greater accessibility and cost amortization of powder bed fusion systems capable of processing precious metal alloys is expected to drive an increasingly high use of precious metals especially in the jewelry and aerospace segments. Coupled with wider adoption of 3D printing (or multiplanar 2D printing) in electronics, these trends are expected to increase the interest and revenue opportunity around precious metal material for additive manufacturing and the use of AM for precious metal parts.
Moving forward, the overall market for precious alloys in AM will become a major segment in metal 3D printing, with materials revenues alone topping $250 million by 2028 and overall PMAM related revenues nearing $2 billion at the end of the 10-year forecast period.
This dossier has first been published in the 2022 September/October edition of 3D ADEPT Mag. Remember, you can post job opportunities in the AM Industry on 3D ADEPT Media or look for a job via our job board. Make sure to follow us on our social networks and subscribe to our weekly newsletter : Facebook, Twitter, LinkedIn & Instagram ! If you want to be featured in the next issue of our digital magazine or if you hear a story that needs to be heard, make sure you send it to contact@3dadept.com