Due to the market growth and its main properties (strength, corrosion resistance, ease of fabrication, etc.), the use of duplex stainless steel has rapidly replaced the use of conventional stainless steel in powder metallurgy applications – in the offshore oil and gas industry.
Here is the thing no matter what grades of duplex stainless steel operators are dealing with (Standard duplex (PREN range: 28–38), Super-duplex (PREN range: 38-45), Lean duplex grades (PREN range: 22–27)), they still need to cope with heat treatment. Indeed, Duplex stainless steel grades must be cooled as quickly as possible to room temperature after hot forming to avoid the precipitation of intermetallic phases (Sigma phase in particular) which drastically reduce the impact resistance at room temperature as well as the corrosion resistance.
So far, the only companies that have officially highlight their ability to master the manufacturing challenges with this material in AM production processes, are Sandvik and BeamIT. AM Solutions provider Oerlikon AM on the other hand, has developed a new high entropy alloy that could replace this material in the additive production of structural components, such as centrifugal pump impellers.
Leveraging an inherent benefit of additive manufacturing, customers can create complex geometries using this new alloy that super duplex steel cannot address with conventional manufacturing. Smoother surfaces for the same structural application can also be realized in the printing process. Additionally, parts printed with the new alloy are crack-free when using a standard Powder Bed Fusion – Laser Beam process without baseplate preheating, Oerlikon explains.
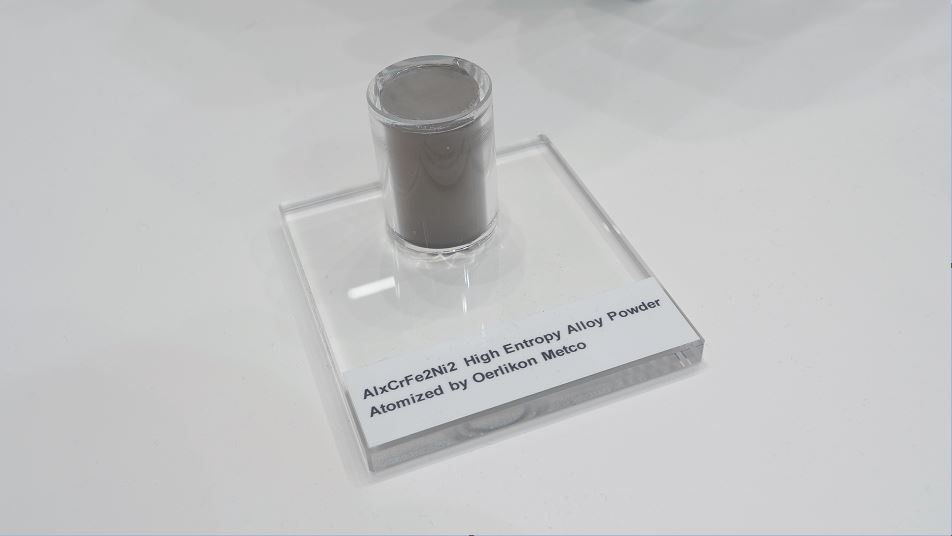
The new alloy is the solution to replace DSS (Duplex Stainless Steel) as it not only matches the corrosion resistance standards of DSS and provides superior strength properties, but is also less susceptible to changes caused by high temperature operation and requires only a single-step heat treatment. Oerlikon developed this alloy as part of the NADEA project – a European research initiative on high-entropy alloys and in partnership with several industrial and academic partners. Using its proprietary Scoperta Rapid Alloy Development tool, Oerlikon was able to significantly shorten the process in developing the alloy, a press release reports.
Remember, you can post free of charge job opportunities in the AM Industry on 3D ADEPT Media or look for a job via our job board. Make sure to follow us on our social networks and subscribe to our weekly newsletter : Facebook, Twitter, LinkedIn & Instagram ! If you want to be featured in the next issue of our digital magazine or if you hear a story that needs to be heard, make sure to send it to contact@3dadept.com