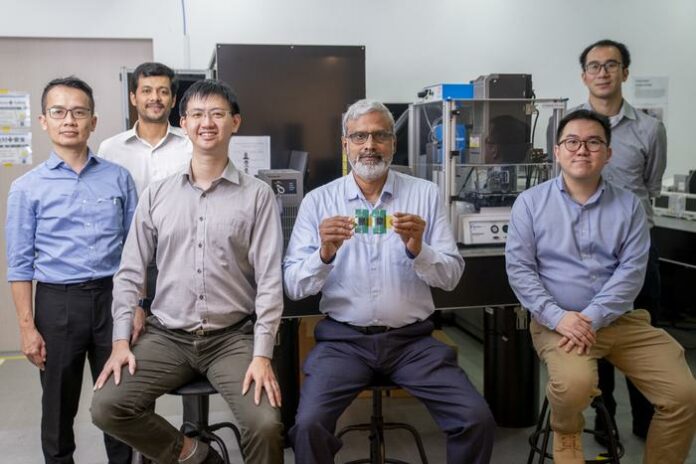
Scientists from Nanyang Technological University, Singapore (NTU Singapore), Panasonic Factory Solutions Asia Pacific Pte. Ltd. (Panasonic), and Singapore Centre for 3D Printing (SC3DP) have developed a multi-material 3D printer using multi-wavelength high-power lasers, for quick and easy 3D printing of smart, flexible devices.
While NTU Singapore has been involved for a long time in AM, it’s the first time a 3D printing activity from Panasonic is publicly revealed.
According to co-leader of the project, Dr Low Mun Ji, General Manager of Panasonic, the company’s technology allows for the creation of highly porous and conductive graphene-based material for use in different applications. “Compared to traditional graphene manufacturing methods, our method is faster, cheaper, and highly compatible with a wide range of materials,” he said.
Why the focus on flexible smart devices?
Electronic devices and components have traditionally been comprised of rigid materials such as metals, silicon, and ceramics, but there has been an increasing interest in the creation of flexible wearable electronics that can be bent, twisted, and easily conformed to various surfaces.
The team behind the project explains that the multi-material 3D printer works by utilizing varying wavelengths of laser, creating thermal and chemical reactions capable of transforming common carbon-based materials (polyimide and graphene oxide) into a new type of highly porous graphene. The resulting structure printed with this new graphene is not only light and conductive, but it can also be printed or coated onto flexible substrates like plastics, glass, gold and fabrics, creating flexible devices.
Co-leader of the project, Associate Professor Murukeshan Vadakke Matham from NTU School of Mechanical and Aerospace Engineering (MAE) and SC3DP, the national centre of excellence in 3D printing housed at NTU, said: “Our project aims to find a way to 3D print new materials like organic polymers and carbon-based materials like graphene, which has properties that allow them to be printed or coated onto flexible substrates like plastics or fabrics, creating flexible and stretchable circuits.”
3D printed sensor for smart intravenous fluid bag
The newly created 3D printer has already attracted interest from various companies, including from American multinational manufacturer JABIL-MTI Penang.
JABIL-MTI Penang aims to integrate 3D-printed graphene-based electronics into a smart infusion system. A proof of concept has been demonstrated through a prototype of a low-cost intravenous (IV) fluid bag with an embedded printed sensor powered by artificial intelligence. The device monitors the status of the IV drip, regulates parameters such as pressure flow and temperature, and transmits the information to a smartphone in real-time. This allows medical personnel to remotely monitor, control and detect abnormally efficiently.
The research team also tested the possibility of integrating 3D printed components into the fabrication of high-performing electronics like pressure sensors and heaters, with funding support from NAMIC.
What’s next?
The project between NTU and Panasonic to develop the new multi-material printer was launched in 2016 with the support of the Singapore Economic Development Board (EDB) under the Industrial Post-graduate Programme (IPP). Over the years, the project team has filed two patents, presented at 11 international conferences, and published 11 papers. It has also supported three Panasonic scientists and engineers who completed a doctorate degree from NTU.
As next steps, Panasonic has set up a new facility for laser-based manufacturing systems at its research hub in Singapore, to enable further trials of concepts using components fabricated by the multi-material printer, as part of “Autonomous Factory” – a Panasonic concept for smart factories of the future. The new facility is to be led by Dr Low and researchers Dr Nicholas Tham and Dr Joel Lim, who were also involved in the joint NTU-Panasonic project.
Remember, you can post job opportunities in the AM Industry on 3D ADEPT Media free of charge or look for a job via our job board. Make sure to follow us on our social networks and subscribe to our weekly newsletter : Facebook, Twitter, LinkedIn & Instagram ! If you want to be featured in the next issue of our digital magazine or if you hear a story that needs to be heard, make sure to send it to contact@3dadept.com