AM company Materialise continues to advance its open software platform CO-AM through partnerships with other AM technologies providers. As a reminder, the platform was created after Materialise acquired Link3D; it aims to provide AM users direct access to multiple hardware technologies and their preferred tools from Materialise and other software developers, supporting them along every step of their AM journey – from planning and printing to quality control.
Simply put, if you’re producing more than a dozen parts on a weekly basis, you should consider using an AM workflow software that will optimize your process. While each of the platform available on the market brings its share of advantages, I am glad to see how Materialise continuous improvement process contributes to helping AM users demonstrate AM ROI.
The latest developments of this platform include the integration of HP’s Multi Jet Fusion and Metal Jet additive manufacturing (AM), the introduction of the CO-AM Quality & Process Control (QPC) system; the improvement of the quoting process as well as the integration of the company’s Build Processors into CO-AM for Nikon SLM Solutions printers.
These four highlights yielded interesting conversations at Formnext 2023 between the company and other AM solutions providers and with AM users who can benefit from these solutions.
Materialise and HP
HP is the second 3D printer manufacturer to join the CO-AM platform – the first one being SLM Solutions – and the 12th company to be integrated into the platform. Together both companies aim to address two specific requirements to drive volume production of end-parts: the need for 3D printers with high productivity and an end-to-end workflow solution.
Through this partnership, Materialise and HP highlight the fact that it’s not enough to have a high-productivity 3D printer if it does not work with other manufacturing technologies. In combination with the Materialise CO-AM Software Platform, manufacturers can link HP’s Multi Jet Fusion and Metal Jet technology to their existing production systems and optimize the AM workflow from order entry to delivery.
In other words, it’s about improving traceability, quality control, and machine utilization. In a press communication, Materialise explains that optimized 3D print job management allows production leads to track planned and actual printer activities and optimize machine time. To ensure continuous production, real-time machine monitoring provides operators and engineers with critical process data, including build status, material usage, and machine sensor data. This data can be collected and stored in log files of 3D-printed jobs to enhance traceability and quality control. In addition to their 3D printers, Metal Jet users can connect process-relevant HP machinery to the CO-AM platform, such as the Powder Management Station, Curing Station, and Powder Removal Station. This integration allows Metal Jet users to streamline the post-processing of metal parts within the manufacturing process.
The partnership may be announced now but it is already effective. As a matter of fact, manufacturing company Extol recently powered their HP Multi Jet Fusion printers with CO-AM to produce custom 3D-printed knee braces for Baretta Medical Institute patients.
The CO-AM Quality & Process Control (QPC) system
Earl at the beginning of the year, Materialise shed light on its Process Control software which allows manufacturers to analyze and correlate layer data from the 3D printing process. This solution to improve automated quality control requires to collaborate with other companies like Phase3D and Sigma Additive Solutions.
Materialise is going one step further in this stage of the manufacturing chain as it unveils the CO-AM Quality & Process Control (QPC) system at Formnext 2023. Designed to ensure AM quality and process control in certified manufacturing, QPC would enable AM users to track, monitor, analyze, and correlate all data critical to part quality.
Available in the Materialise CO-AM Software Platform, it interconnects AM data sources like 3D models, raw materials, process parameters, in-situ process monitoring, post-processing, and quality inspection. QPC users can collect and monitor this data during the different stages of product development, like research, validation, and production. This will help them to get an unparalleled holistic view of their process and its interrelationships, the company explains.
The quoting process
Quoting is one of the problems we don’t often think of, yet it causes a lot of administrative hassles, and sometimes unnecessary costs to service bureaus. To ensure high responsiveness and fast delivery, Materialise integrates DigiFabster’s cloud-based SAAS quoting automation and e-commerce solution into the CO-AM platform.
The fully white-labeled e-commerce portal uses machine learning to help manufacturers automate and accelerate their quoting process, saving time and costs. This means that order data will be streamlined into CO-AM’s Order Management System. This will help manufacturers keep track of orders and give instant status updates to their customers.
New Materialise Build Processors and seamless integration into CO-AM for Nikon SLM Solutions printers
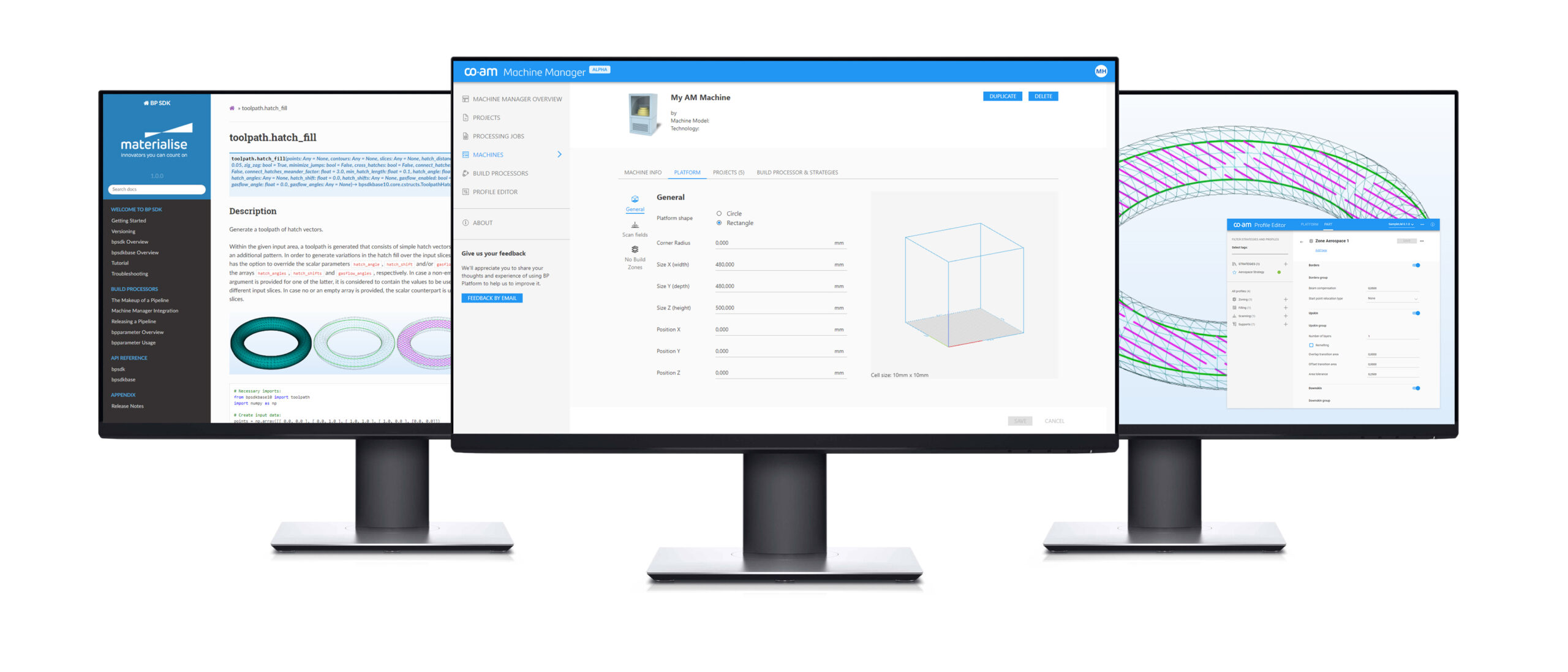
Materialise Build Processors (BPs) are at the heart of this new collaboration between the software company and the machine manufacturer NIKON SLM Solutions. For those who do not know, a BP acts as a conduit, linking 3D printers with data preparation software like Materialise Magics.
Post-data preparation, an extensive data volume requires processing to furnish the requisite information for the 3D printer to fabricate the parts. The Belgian 3D printing company explains that its BPs expedite this phase, to allow for customization of process parameters to optimize application outcomes.
As NXG machines powered by twelve 1kW lasers might require the processing of a substantial data volume, it is crucial to bridge the gap between data preparation and actual printing to unlock the full productivity potential of each application.
In this vein, Nikon SLM Solutions and Materialise will curate the next-gen BPs, addressing this bottleneck and providing AM users the latitude to modify their 3D printing process as per their requisites. The novel BP is slated for release in the upcoming months for NXG and all SLM users employing Materialise software solutions.
Remember, you can post job opportunities in the AM Industry on 3D ADEPT Media free of charge or look for a job via our job board. Make sure to follow us on our social networks and subscribe to our weekly newsletter : Facebook, Twitter, LinkedIn & Instagram ! If you want to be featured in the next issue of our digital magazine or if you hear a story that needs to be heard, make sure you send it to contact@3dadept.com.