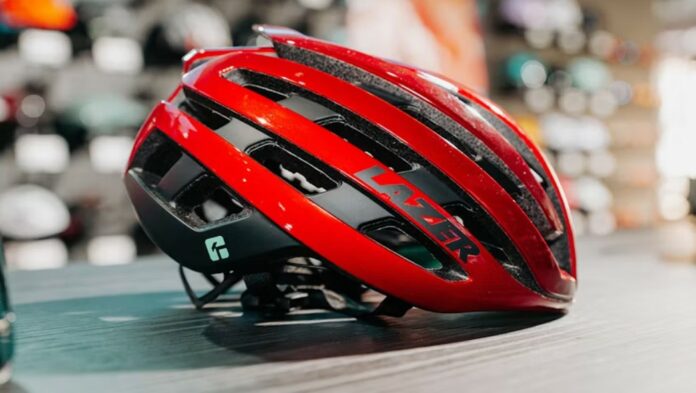
Lazer Sport NV, Belgian cycling helmet manufacturer, has recently brought to market KinetiCore, a proprietary rotational impact protection technology. The manufacturer’s goal was to provide on- and off-road cyclists protection against both direct and rotational impact.
To do so, the engineering team relied on Siemens Xcelerator portfolio from Siemens Digital Industries Software at the design level. As a reminder, the Siemens Xcelerator is an end-to-end ecosystem of 3D printing solutions that has encompassed many partnerships from the AM industry including 110 machine manufacturing companies that make 3D printed parts based on Siemens automation. Over time, Siemens also has integrated software solutions on this platform.
Lazer Sport uses Siemens’ NX™ software for product engineering and manufacturing, along with Simcenter™ 3D software for digital simulation and verification. “The development of KinetiCore required a huge amount of design changes and simulations. We chose the Siemens Xcelerator portfolio for its wide range of applications and the ability to seamlessly connect 3D design with 3D printing for prototyping and digital simulation. With Siemens’ NX we were able to create more complex designs for our helmets and molds and simulate them. This allowed for greater design complexity, enhanced freedom, and faster time to market,” said Emiel Spreeuwers, Product Designer, Lazer Sport.
The uniquely designed EPS foam blocks, called controlled crumple zones, deform under impact and absorb the energy that otherwise would reach the cyclist’s brain. The KinetiCore technology offers up to 23% lighter helmets, as well as 12% better cooling efficiency with innovative vents channeling cool air through to the back of the helmet and expelling warm air, boosting rider comfort and overall experience. KinetiCore is made with less plastic than previous comparable models, supporting Lazer Sport’s commitment to reducing impact on the environment, a press release reads.
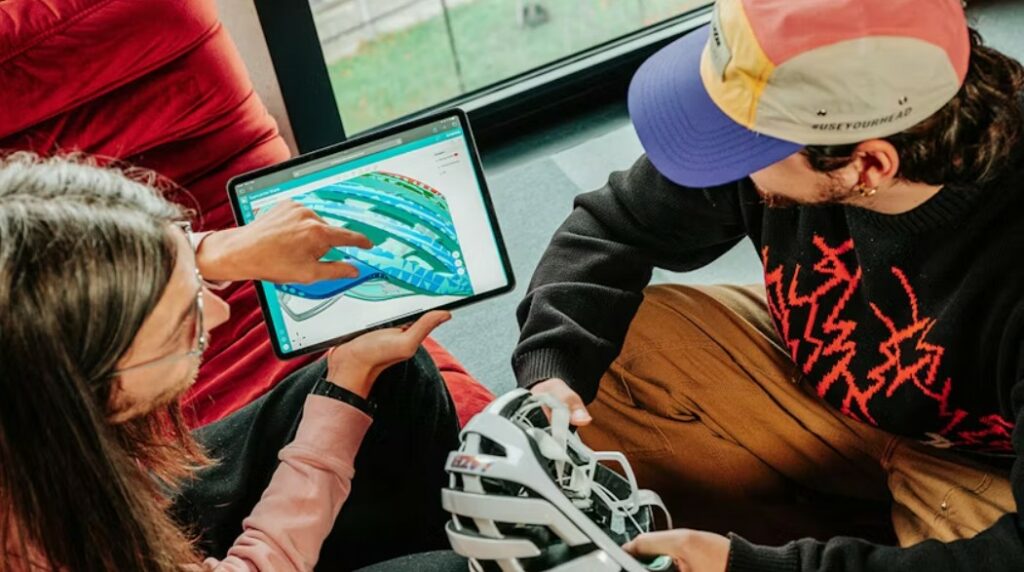
“The 3D CAD files created in NX can also be easily opened in Simcenter for further modification and meshing without any compatibility issues. This streamlined approach helps us to verify KinetiCore’s performance, preventing costly mold modifications post-production,” said Hadi Ghiaballoo, Product Engineer, Lazer Sport.
The manufacturer now envisions to implement KinetiCore in 20 models by the end of 2024, as it has been proven that the helmets could offer enhanced safety and design for all cyclists. One thing is certain, Siemens Digital Industries Software will be part of the process.
Remember, you can post job opportunities in the AM Industry on 3D ADEPT Media free of charge or look for a job via our job board. Make sure to follow us on our social networks and subscribe to our weekly newsletter : Facebook, Twitter, LinkedIn! If you want to be featured in the next issue of our digital magazine or if you hear a story that needs to be heard, make sure to send it to contact@3dadept.com