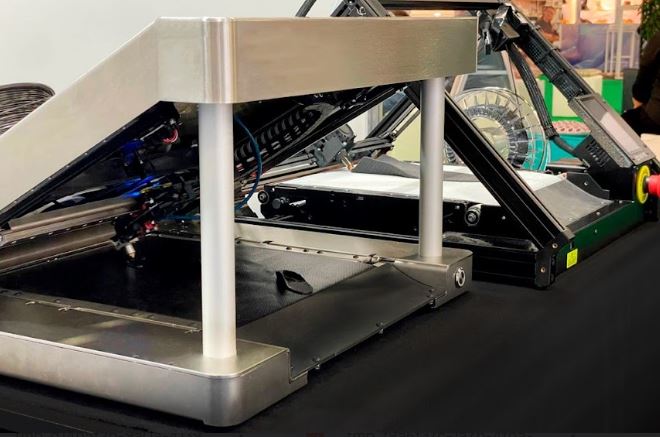
Germany-based 3D belt printer manufacturer iFactory3D and Austrian company Plasmics have optimized orthopedic insoles manufacturing with their serial 3D belt printing and Feetneeds technology respectively.
With the help of iFactory3D’s One Pro 3D belt printer, orthopedic insoles can be printed round the clock without any supervision at a low cost as it has a built-in conveyor belt and remote control.
The initial time savings in the 3D belt printing process is achieved using modern scanning techniques and digital programs for model processing. Then 3D models and patient experiences further helped in saving time by clinical analysis of symptoms which could be treated.
The 3D belt printing process also helps to protect the environment through the selective usage of materials and recycling them for further reuse. It reduces waste as less material is used and waste can be recycled unlike in CNC milling.
The One Pro 3D belt printer by iFactory3D can also address labour shortage issues in orthopedic product manufacturing. Unlike conventional 3D Printers, the One Pro 3D belt printer don’t need specific adjustments and materials and software research as its closed loop system can do it all together. This makes it useful to do the 3D belt printing by one person, ultimately enhancing productivity.
iFactory3D seems to address the problems regarding data transmission and user interface of the 3D printing software used in orthopedic insoles production. The end-to-end closed loop has all parameters from model development to printing come from a single source and seamlessly interact with each other.
The 3D belt printer comes with CAD software for processing data and the right material suitable to the desired production volume. This solution by Feetneeds solves the problem of implementing scanning software. No initial payments are needed for this, only the basic requirement is printing a minimum of 250 pairs of orthopedic insoles every year.
The One Pro 3D belt printer is already in use amongst the orthopedic insoles makers in the UK, France, Belgium, Austria, Poland, Ukraine, Australia and the Czech Republic.
Podologist Akbal Randhawa who started The Foot Clinic1 in the United Kingdom has used the One Pro for the last two years and according to him, 3D belt printing technology is new to the UK and can “print several pairs of orthopaedic insoles per week, which is quick and generates very little waste”.
“Without the One Pro, I would have to send the insoles to a lab and then wait two weeks for them to be manufactured. The orthopaedic insoles I make replace the CNC-milled devices and even some of the moulded plastic insoles”, said Randhawa.
Remember, you can post job opportunities in the AM Industry on 3D ADEPT Media free of charge or look for a job via our job board. Make sure to follow us on our social networks and subscribe to our weekly newsletter : Facebook, Twitter, LinkedIn & Instagram ! If you want to be featured in the next issue of our digital magazine or if you hear a story that needs to be heard, make sure to send it to contact@3dadept.com