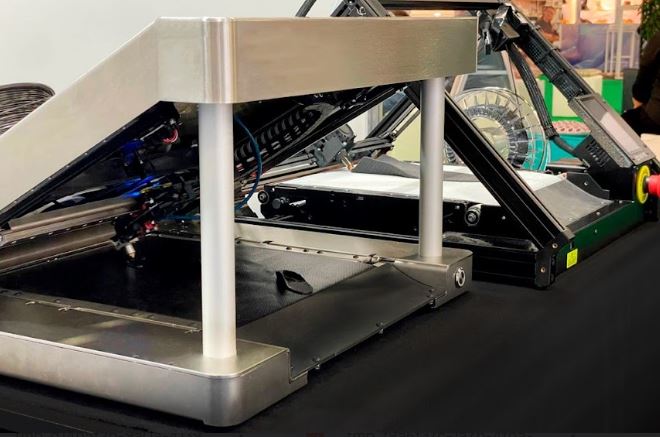
Le fabricant d’imprimantes 3D à bande iFactory3D, basée en Allemagne, et la société autrichienne Plasmics ont optimisé la fabrication de semelles orthopédiques grâce à l’impression 3D de ceinture en série et à la technologie Feetneeds, respectivement.
Grâce à l’imprimante 3D à bande One Pro d’iFactory3D, les semelles orthopédiques peuvent être imprimées 24 heures sur 24 sans aucune supervision et à faible coût, car elle est équipée d’un tapis roulant intégré et d’une commande à distance.
Les gains de temps initiaux dans le processus d’impression 3D sont obtenus grâce à des techniques de numérisation modernes et à des programmes numériques pour le traitement des modèles. Les modèles 3D et les expériences des patients permettent ensuite de gagner du temps grâce à l’analyse clinique des symptômes susceptibles d’être traités.
Le processus d’impression 3D à bande contribue également à la protection de l’environnement grâce à l’utilisation sélective des matériaux et à leur recyclage en vue d’une réutilisation ultérieure. Il réduit les déchets car moins de matériaux sont utilisés et les déchets peuvent être recyclés, contrairement au fraisage CNC.
L’imprimante 3D pour ceintures One Pro d’iFactory3D peut également répondre aux problèmes de pénurie de main-d’œuvre dans la fabrication de produits orthopédiques. Contrairement aux imprimantes 3D conventionnelles, l’imprimante 3D à bande One Pro ne nécessite pas de réglages spécifiques, ni de recherche sur les matériaux et les logiciels, car son système en boucle fermée peut faire tout cela ensemble. Cela permet à une seule personne de réaliser l’impression 3D à bande, ce qui améliore la productivité.
iFactory3D semble résoudre les problèmes de transmission de données et d’interface utilisateur des logiciels d’impression 3D utilisés dans la production de semelles orthopédiques. Avec ce processus de “boucle fermée”, tous les paramètres, du développement du modèle à l’impression, proviennent d’une source unique et interagissent de manière transparente.
L’imprimante 3D à courroie est livrée avec un logiciel de CAO pour le traitement des données et le matériau adéquat pour le volume de production souhaité. La solution Feetneeds résout le problème de la mise en œuvre des logiciels de numérisation. Aucun paiement initial n’est nécessaire, il suffit d’imprimer un minimum de 250 paires de semelles orthopédiques par an.
L’imprimante 3D One Pro est déjà utilisée par les fabricants de semelles orthopédiques du Royaume-Uni, de France, de Belgique, d’Autriche, de Pologne, d’Ukraine, d’Australie et de République tchèque.
Le podologue Akbal Randhawa, qui a créé The Foot Clinic1 au Royaume-Uni, utilise l’imprimante One Pro depuis deux ans. Selon lui, la technologie d’impression 3D à courroie est nouvelle au Royaume-Uni et permet « d’imprimer plusieurs paires de semelles orthopédiques par semaine, ce qui est rapide et génère très peu de déchets ».
« Sans le One Pro, je devrais envoyer les semelles à un laboratoire et attendre deux semaines pour qu’elles soient fabriquées. Les semelles orthopédiques que je fabrique remplacent les dispositifs fraisés par CNC et même certaines semelles en plastique moulé« , a déclaré Randhawa.
N’oubliez pas que vous pouvez poster gratuitement les offres d’emploi de l’industrie de la FA sur 3D ADEPT Media ou rechercher un emploi via notre tableau d’offres d’emploi. N’hésitez pas à nous suivre sur nos réseaux sociaux et à vous inscrire à notre newsletter hebdomadaire : Facebook, Twitter, LinkedIn & Instagram ! Si vous avez une innovation à partager pour le prochain numéro de notre magazine numérique ou si vous avez un article à faire connaître, n’hésitez pas à nous envoyer un email à contact@3dadept.com