The Desktop Metal journey is highlighted by big ambitions: a solid materials strategy, key process performance targets and an intriguing plan to become more than just a general service bureau.
In 2020, Desktop Metal (DM) announced its intent to go public through a special purpose acquisition company (SPAC) with Trine Acquisition Corp and global credit investment firm HPS Investment Partners, and confirmed it just before we bid goodbye to that extraordinary year. Nobody would have thought then that this single action from the Additive Manufacturing unicorn would lead to a wave of SPAC-IPO transactions in the industry. Yet, since this IPO, Desktop Metal’s journey has evolved in terms of structural organization, manufacturing processes & applications, and overall vision. 3D ADEPT Media caught up with Arjun Aggarwal, Chief Product Officer, to discuss the journey of the “Pure-Play Additive Manufacturing 2.0 Company”.
Desktop Metal was founded in 2015 with a single goal: making 3D printing an essential tool for engineers and manufacturers around the world. With solutions for every stage of the manufacturing process – from prototyping and pilot runs to mass production and aftermarket parts – Desktop Metal has invested extra miles to transform the way engineering teams work within the same organization or across different organizations, and fabricate metal and composite components across a wide range of applications and industries.
Here is the thing, at some point in its journey, every company undergoes a transition or change in order to remain viable and scalable. Whether it onboards new employees, opens a new department, or merges with another company…these changes can have a significant impact on the trajectory of one’s business.
In Desktop Metal’s case, the company has made great strides since it turned stealth mode off in April 2017. From being the highest ever funded company of the industry – with a total of $438 Million, all funding rounds combined prior to its SPAC merger – to the number of products it develops for the industry and the partnerships it signed to advance key areas of the technology, it is fair to say Desktop Metal has had several reasons to rejoice.
Nevertheless, the turning point of this journey occurred last year when the company officially became a publicly-listed company. The initial public offering has marked the beginning of a new era: Additive Manufacturing 2.0, that Desktop Metal coined. As we all know, the term “2.0” is always used to denote a superior or more advanced version of an original concept, product, service, etc. And our guest company today, wanted the industry to be aware of that inflection point. As a matter of fact, Aggarwal defines the company today as an Additive Manufacturing 2.0 organization which focuses “on solutions that enable the volume production of parts through additive that compete cost-effectively with conventional manufacturing”.
“That focus is agnostic to material and to print process as well – rather the focus is on developing the right platforms solutions and capabilities for our customers that enable high-performance parts with competitive economics, regardless of the application. That’s really the next frontier of additive manufacturing and that’s 100% of our focus. We’re doing that through a variety of technology platforms, leveraging a range of technologies, including binder jetting on the metal side and great DLP technology through our acquisition of EnvisionTEC on the polymer side. We support sand and wood 3D printing through several of these platforms as well, the bulk of which enable superior price performance relative to our peers to help our customers produce parts through AM economically and in larger volumes previously only supported by conventional manufacturing. Across these platforms, we’ve qualified more than 225 materials across metals, composites, polymers, elastomers, ceramics, wood, sand, and biocompatible materials. We’re really trying to build a portfolio of AM 2.0 print platforms with an array of materials to push through these platforms so we can address a broad spectrum of applications”, he adds. So, how did Desktop Metal build a portfolio of AM 2.0 print platforms?
The Desktop Metal journey
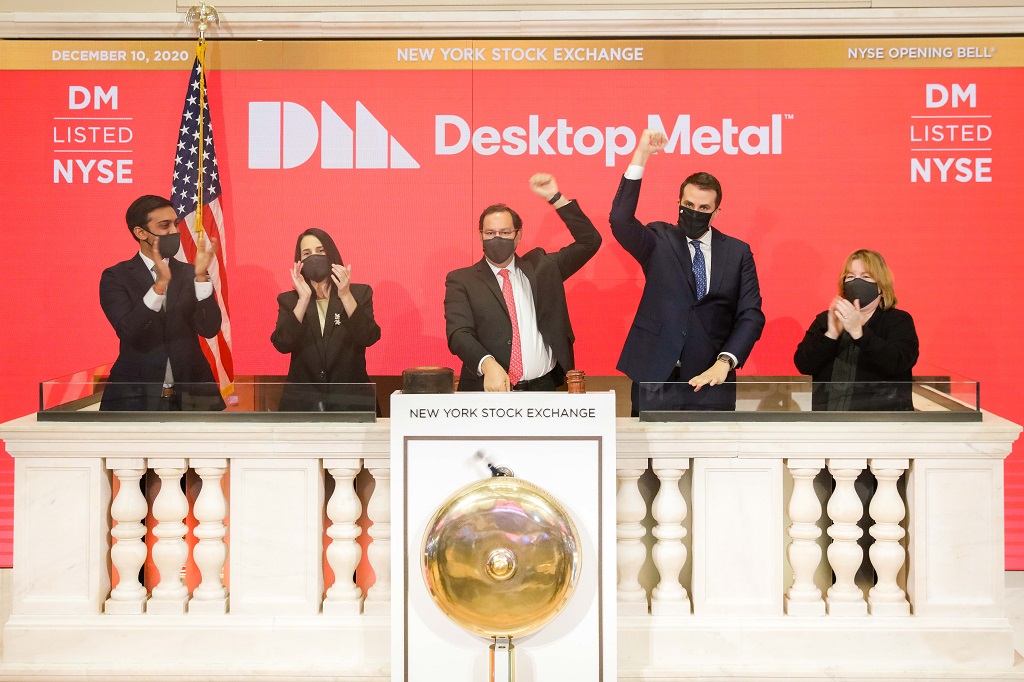
This journey starts with Ric Fulop, a man who is approximately 46 and (based on the last time we hear him) comes from a country in South America. Together with a bunch of experts in materials science, engineering, and 3D printing (Jonah Myerberg, Ely Sachs, Rick Chin, John Hart, Christopher A. Schuh, and Yet-Ming Chiang), their first step in remaking manufacturing was to develop a Desktop metal 3D printing system we all know: the Studio System.
Designed to produce low-volume runs of metal 3D printed parts, first shipments of this $ 120,000 occurred in 2018, alongside the introduction and first commercialization of the Production System, one of the first binder jet systems to be equipped with an industrial inert environment that integrates gas recycling and solvent recovery for the safe printing of reactive metals. With a build volume of 750 x 330 x 250 mm, and a bi-directional system that enables high-resolution printing at up to 12 000 cm3/hr – which means the ability to produce over 60 kg of metal parts per hour – this industrial 3D printer has been so far the fastest binder jetting 3D printer we’ve seen on the market.
With these flagship products, they cemented their positioning in the global manufacturing industry, selling their products to the military, the automotive and other industries ranging from medical devices to apparel.
However, the company’s advancement in the 3D metal printing market is taking place in a context where companies are becoming increasingly aware of the potential of digital manufacturing and are rushing to the most promising sectors. For savvy machine manufacturers, it is no longer enough to build expertise in one single field; it becomes crucial to be able to diversify one’s offer as much as possible in order to maintain a leading position in a market where 3D printing startups abound. Not to mention that AM companies are trying their best to evolve in industries that continuously compare AM companies with conventional manufacturing processes.
While the area of rapid prototyping and the 3D printing production of simple jigs and fixtures was coming to its end, competition came and made the game more interesting. Players like GE and HP, were coming with other serious yet intriguing AM processes while at the regulation level, ASTM was standardizing seven AM processes. And this was just the machines’ side of the iceberg. Across the value chain, companies were demonstrating the need to pay attention to materials, software, and post-processing areas to make the entire AM production worthy. “Broadly speaking, our growth strategy revolves around building out three key pillars of the business – printers, materials and parts. With respect to printers or print platforms, we want to have a broad set of technologies that enable us to compete cost-effectively with conventional manufacturing across a range of applications”, the CPO states.
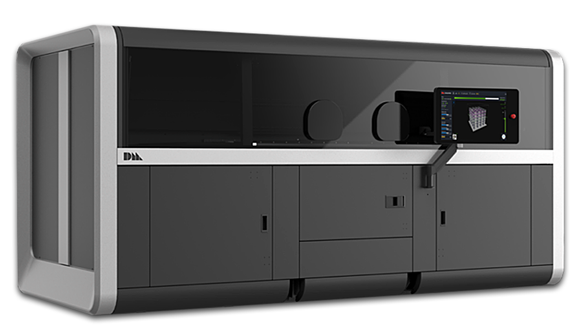
While one should recognize the ability to this unicorn to pull in money, it should be noted that to build these three pillars, more cash and time were necessary. When the Coronavirus pandemic hit, many businesses filed bankruptcy but Desktop Metal has not only been able to survive this crisis, but secure a well-funded yet super-secret stealth operation ($575 million) through its SPAC merger with Trine Acquisition Corp.
Luckily for the American organization, the IPO has not changed much of its leadership team. It did help save time as the first step in building these pillars consisted in increasing its technologies portfolio and refocusing its vision on key segments.
Scaling one’s business with other businesses
To increase its technologies portfolio, Desktop Metal has successfully acquired EnvisionTEC , Adaptive3D, Aerosint and most recently ExOne. Apart from the polymer resin supplier Adaptive3D, and the soon-to-be confirmed acquisition of ExOne, each of these companies helps Desk top M etal debut on a new field of the additive manufacturing industry.
“We brought on Al Siblani through the acquisition of EnvisionTEC, who oversees our photopolymer product roadmap and development efforts. Al works very closely with Mike Jafar, who we brought on to lead our new Desktop Health business – that’s a group within Desktop Metal focused on developing and commercializing solutions targeted specifically towards the healthcare and dental markets. Segmenting this business is allowing the rest of the company to focus on consumer and industrial end markets such as automotive, consumer products, oil and gas, industrial machinery, aerospace and defense. Additional changes to our organization have largely been bolting on a few new R&D stage start-ups that we continue to integrate from a back-end M&A perspective, while we let the entrepreneurs operate pretty independently. A great example is Aerosint, which we acquired very recently. They have developed a unique multi-material printing technology with initial applications in powder bed fusion, so we want to make sure they can operate relatively independently and retain the ability to commercialize this solution into that market with third parties. At the same time, we will also work with the team to mature the technology and look to integrate it into Desktop Metal products in the future”, Aggarwal points out.
However, amid these M&A transactions, ExOne has been the most surprising one. Not only would we have suspected that , if there was to be an acquisition, it would have to be ExOne buying Desktop Metal, but beyond that, Desktop Metal decides to bring into its portfolio a company that has always been considered as its biggest competitor. The announcement states that, ExOne shareholders will receive $8.50 in cash and $17.00 in shares of Desktop Metal common stock for each share of ExOne common stock, for a total consideration of $25.50 per share. All of this represents a transaction value of $575 million, subject to a collar mechanism and implying a 47.6% premium to the closing price of ExOne’s common stock on August 11, 2021 and a 43.9% premium based on the 30-day average closing price of ExOne common stock. The transaction value also implies an acquisition multiple of 6.4x 2021 consensus revenue estimates for ExOne.
Furthermore, let’s remind that ExOne, founded in 2005, is one of the first players that started the commercialization of metal binder jetting systems. Over time, the company launched several metal binder jetting systems, with each being an evolution on the previous one.
There are so many questions about this acquisition, questions that ExOne may not have all the answers to in the short-run. However, apart from this potential real powerhouse marriage for binder jetting, the ExOne team also believes in the complementary potential of two main fields of activities: – Their material expertise in metals and ceramics, made possible through the company’s patented Triple ACT system and the work of their R&D and engineering teams, combined with the speeds of Desktop Metal’s Single Pass system; – The combination of ExOne’s sand 3D printing platforms with DM’s low-cost Viridis3D robotic sand 3D printing technology.
Manufacturing processes & applications
Even though several actions are being implemented to drive the growth of each pillar – printers, materials, and parts -, at the end of the day, they are interrelated as they are part of a “big puzzle”.
As far as 3D printers are concerned, Desktop does not intend to release new products anytime soon, but rather to improve existing manufacturing processes. Be it for its in-house metals and composites processes, or photopolymer 3D printing and multi-material AM technologies it acquired through EnvisionTec and Aerosint, the main goal will be to enhance performance of the processes by working on how to achieve better material properties, surface finish, tolerances, and most critically, speed and cost.
With the acquisition of ExOne, all eyes will be on the binder jetting technology, which is the main technology that both companies have independently developed in this industry.
According to the CPO’s explanation, we can probably expect more development at the materials level: “Binder jetting is a technology that can enable materials that you wouldn’t necessarily manufacture via conventional manufacturing like CNC machining because the material is too hard or it takes too long, or via powder bed fusion in the case of non-weldable alloys. There’s a whole set of materials that you can manufacture with powder metallurgy and that binder jetting makes possible. So again, it’s not so much that 3D printing requires complex materials as it enables high performance, complex materials that you can’t manufacture with other processes. That’s one of the reasons that we’re really excited about it. But, at the same time our platforms, including the Shop System and Production System, support workhorse or commodity materials like stainless steels and enable customers to manufacture parts with these metals cost-effectively and at scale. And we continue to invest in materials not just on the metals side, but across our polymer platforms as well – our Adaptive3D elastomers offer best-in-class performance for industrial applications, and we also recently launched two new photopolymer materials for the dental market, Flexcera Base and Flexcera Smile, that enable high-performance functional dentures.” Still on the materials’ side of its business, last year saw the release of a number of materials including the sinterable 6061 aluminum and later on the 4140 low alloy steel, all of which can be processed by its metal binder jetting systems.
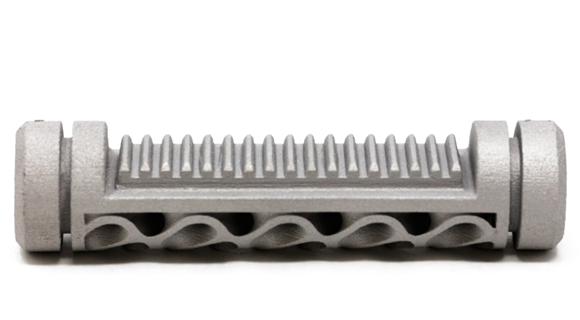
Those material developments predict a new era of competition in the metallurgy industry, an era that metalcasting experts should watch closely. Indeed, demands from industries have become more stringent as they no longer limit their manufacturing goals to design and production. They are going one step further by challenging metallurgy, as it was the preserve of foundries and die casters.
Indeed, one used to say that the higher the strength of aluminum, the more difficult it is to form with traditional manufacturing. “We’re getting properties with Al 6061 that are better than wrought, and with binder jetting you can produce more complex geometries than with traditional CNC machining” Aggarwal affirms. Add to that the fact that, Al 6061 is one of the rare lightweight metals that can finally be processed by metal binder jetting, you obtain a wide variety of thermal and structural applications across industries.
“Materials are really what unlock applications, and so we’re focused on bringing to market materials that we think are going to unlock the widest variety of applications. 4140 and Al 6061 are two of those key materials. We have also qualified 17-4PH and 316L stainless steels, and our roadmap also includes carbon steels, super alloys, titanium, copper, and other materials for which we see key that either already exist or are emerging in the market”, he completes.
Although materials will enhance the performance of its various platforms, Desktop Metal strongly believes they will also help their customers remove some of the margin stack-up that would otherwise take place. Although its subsidiary is relatively new, Forust which enables wood 3D printing via binder jet, might help deliver this economic advantage to customers in the architecture and construction industries. This material strategy is just as important here as it’s about taking waste byproducts from traditional wood manufacturing, like sawdust and lignin, and recombining them using 3D printing. However, while with Forust, the environmental benefit in this material strategy was clearly understandable, we can’t help but ask ourselves if the other materials developed for the metal binder jetting systems also provide any environmental benefit as compared to other materials this technology can process.
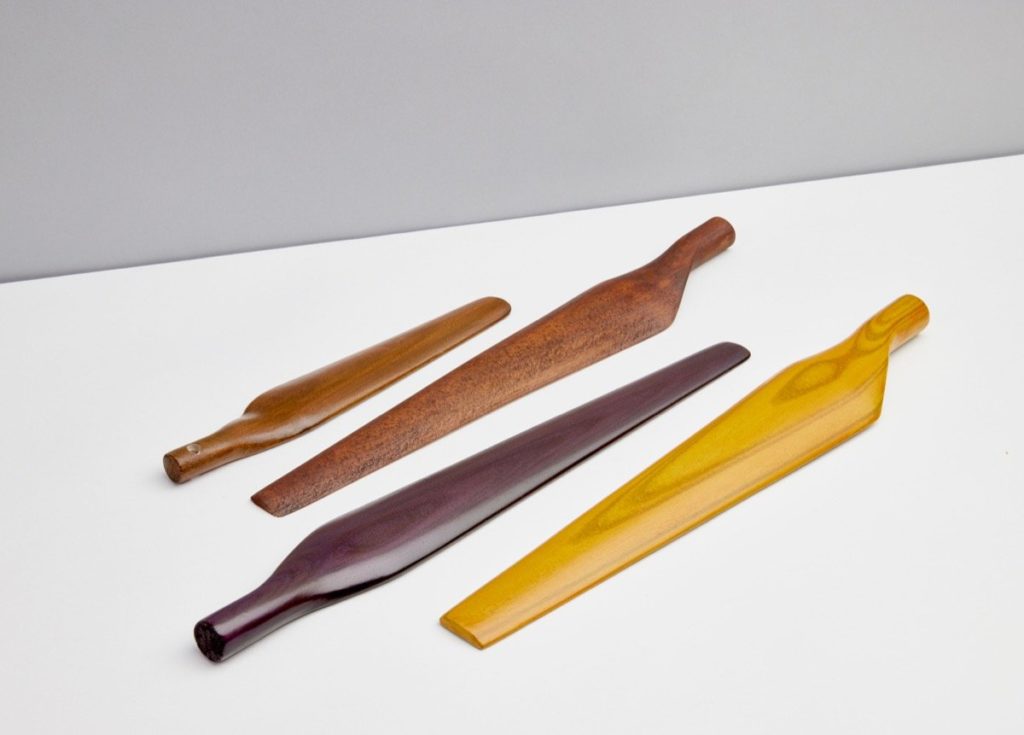
“ I think it’s twofold. First, binder jetting is inherently a green process. All of the powder that does not end up in parts at the end of a print can be recycled and reused in future prints. There’s not a huge amount of waste that’s generated as a result of this process, which is in contrast to CNC machining where you’re basically starting from a billet of material, and you have to cut your part out. The more intricate the part is, the longer machining takes, and the more waste you actually generate. Binder jetting is also different from powder bed fusion, where there are actually some constraints on the re-use of the material as it can degrade with each print. With binder jetting, by contrast, the material is almost reusable endlessly – in fact, we are still running prints in our lab using powder that has been recycled many times over. From that perspective, binder jetting is a very green process compared to some other additive and conventional manufacturing methods. Second, by using binder jetting in combination with high-performance materials, some of which have high strength and stiffness, you can produce highly optimized structures, which may have been difficult to produce via conventional manufacturing. As a result, with our platforms, you can create products that use less material and there are positive downstream effects, too. For example, if you are able to lightweight components for a vehicle, it can reduce the fuel consumption of that vehicle, and the same goes for an aerospace component. So, while the materials themselves may not provide an environmental benefit today, the core binder jetting process is green. Through more complex, optimized geometries, you can reduce material usage and take advantage of downstream benefits, like reduced fuel consumption. Our new Forust process for binder jetting wood has been designed to upcycle traditional wood manufacturing byproducts – sawdust and lignin – so that new material and cradle-to-cradle process is enabling a totally new, more environmentally friendly way to manufacture functional, wood parts”, the company’s representative replied.
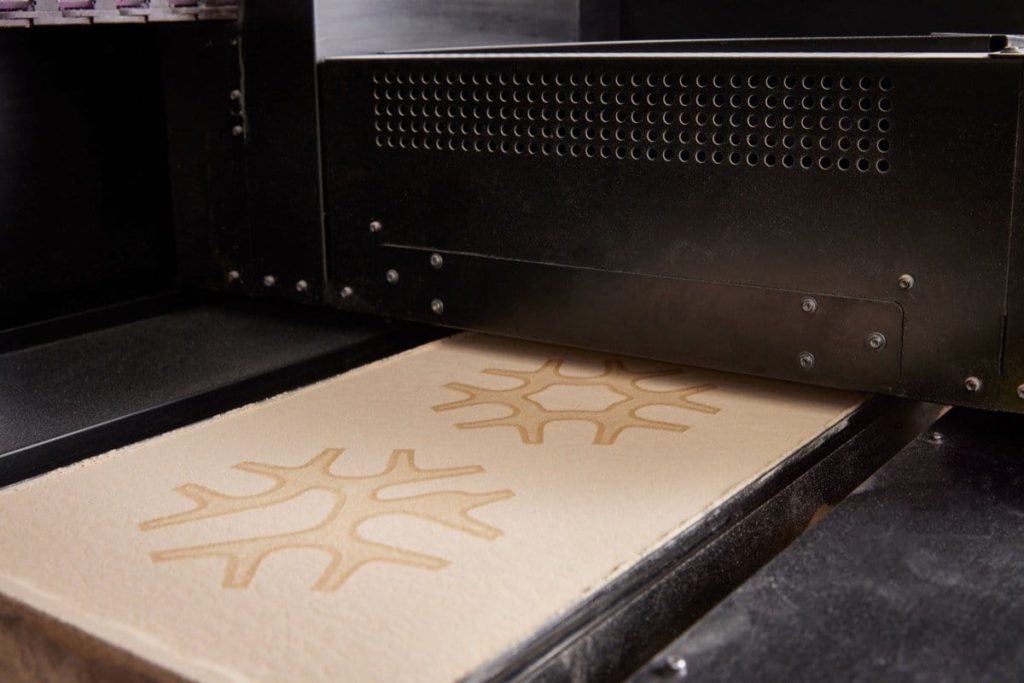
As for applications? It’s easy to predict that DM will focus on those vertical industries that foster the adoption of AM technologies. As we saw from the very beginning, the company has already indicated a firm interest in focusing on the healthcare through a dedicated line – Desktop Health.
However, whether it is in the automotive, consumer products or other industrial sectors, today more than ever it is crucial for the machine manufacturer to focus on applications that make sense. As per the words of Aggarwal, there’s a real benefit to metal 3D printing, where one can improve sustainability by creating products that can be re-used multiple times versus those created in plastic. In the automotive sector especially, manufacturing should deliver a tangible environmental benefit by light weighting and optimizing components, by taking into consideration fewer material usage, fewer material costs, and by improving the fuel consumption economics of vehicles. Furthermore, in heavy industries like oil & gas where applications are often highlighted with other types of metal AM technologies, the expert refocuses the debate on the capability of Single Pass Jetting to scale a production (in-situ) while removing many of the shipping and logistics burdens associated with conventional manufacturing.
“More than just a general service bureau”
Moreover, as it moves forward, this focus on applications that make sense will lead DM to further implement and develop an online manufacturing platform where parts to manufacture will be selected wisely.
“We see a huge opportunity to actually own the entire value chain, not just the technology and materials but also the supply of parts to the end customer. We want to be selective about building a parts’ offering to address from of these killer applications for AM as they hit inflection points. An example of us starting to organically go there is with Forust – in addition to selling the technology platform and materials, we are offering parts produced by Desktop Metal and Forust through an eCommerce platform. The parts focus area is one where you’ll see us play a little bit more in the future. We don’t intend to be just a general service bureau, but we may continue to evaluate opportunities to provide parts in specific verticals and applications where AM enables really unique products and high value, high margin offerings. We believe these three pillars — print platforms, materials and parts — are all synergistic and will reinforce each other as Desktop Metal continues to grow” the CPO told 3D ADEPT Media.
What’s next in the pipeline…
Even though the company remains super-secret about what expertise they will add to their companies’ portfolio, Aggarwal ensures that we may expect DM will pursue its acquisitions strategy. However, after this incredible first half of the year, we can legitimately say metal AM will remain at the heart of its next phase of growth.
“While we have broadened our strategy to focus on providing cost-effective AM solutions at scale across materials, metal remains one of the core foundations of the Desktop Metal business. In fact, we have more employees focused on metal 3D printing today than we have had at any point in the past. I think because we were a metal company from the start, some of the announcements that we’ve made more recently have been related to investments outside of metal, but we continue to invest heavily in metals organically and inorganically. We’ve had a number of new metal material releases over the past few months, and we’ve had several new products that we’ve launched just in the last year – in binder jetting, our Shop System and P-1 in Q4 last year, and the P-50, scheduled for later this year. The Studio System 2 also launched in the first quarter of the year – so we’ve had considerable new developments from a print platform perspective, as well as an extensive material roadmap we are working towards. We announced Aluminum 6061, 4140 low-alloy steel, and 316L stainless steel for our binder jet platforms, and we have a couple of exciting announcements on the horizon there as well. Success for Desktop Metal is capturing double digit market share in the overall AM market over the next decade, and metal is a key ingredient to that success along with broadening our AM 2.0 portfolio to address a growing set of applications through additional materials, including polymers, elastomers, sand, wood, and biocompatible materials”, Aggarwal concludes.
This content has first been published in the 2021 July/August edition of 3D ADEPT Mag.
Remember, you can post job opportunities in the AM Industry on 3D ADEPT Media free of charge or look for a job via our job board. Make sure to follow us on our social networks and subscribe to our weekly newsletter: Facebook, Twitter, LinkedIn & Instagram ! If you want to be featured in the next issue of our digital magazine or if you hear a story that needs to be heard, make sure you send it to contact@3dadept.com