In a recent conversation, Brian Baughman and Curtis Swift from Honeywell Aerospace, shared with 3D ADEPT Media that their team relied on ceramic 3D printing to create molds for casting. The engineering team has continued to deepen its expertise in this technology and provides today further information about their process.
“Traditionally, turbine blades are made through an investment casting process that only a few foundries in the world can handle,” said Honeywell Chief Manufacturing Engineer Brian Baughman. “It involves machining extremely complex metal dies and tooling to create ceramic molds, which are then cast with a molten superalloy to form the blades.”
Using vat-based high-resolution 3D printing, they can process ceramic slurry and print the molds directly. The 3D printer developed by OEM Prodways is based on the company’s proprietary technology called MovingLight and would have already served for the manufacture of several aircraft engine components in the aerospace industry.
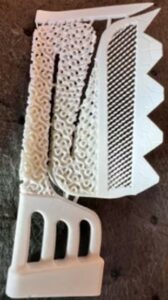
“With the conventional investment casting process, it can take one to two years to produce the turbine blades needed for the development process,” said Mike Baldwin, Principal R&D Scientist. “Additive manufacturing lets us take the design, print the mold, cast it, test it and get real numbers to validate our models – all in just seven to eight weeks. If we need to tweak the design, we can change it electronically and get another blade in about six weeks. Before 3D printing, even minor changes to the blade design could be very costly, he said. “Additive manufacturing enables rapid prototyping and gives us greater flexibility to accelerate development, manage costs and create the best possible product for our customers. Reducing development cycle time is our primary objective, but we also anticipate saving several million dollars in development costs compared to using the traditional blade casting process.”
While the Honeywell Aerospace team is using the ProMaker Ceram Pro 365 – a 3D printer installed last year at their facility, the Prodways Group said that despite the
recent progress that opens up commercial opportunities in a very significant addressable market for 3D printing of ceramic parts, in the short term, they remain cautious about the prospects for printer sales for this application.
“Low volumes are often a struggle since the upfront tooling cost for a turbine blade is very high and fabrication requires a long lead time. Additive manufacturing makes a lot of sense in cases like this,” Baughman reassures.
Remember, you can post job opportunities in the AM Industry on 3D ADEPT Media free of charge or look for a job via our job board. Make sure to follow us on our social networks and subscribe to our weekly newsletter : Facebook, Twitter, LinkedIn & Instagram ! If you want to be featured in the next issue of our digital magazine or if you hear a story that needs to be heard, make sure to send it to contact@3dadept.com