Cela devient évident avec le temps. Les professionnels des navires de la Marine, des avions et du secteur militaire rêvent d’un jour où ils pourraient obtenir des pièces de rechange sur place. La mission de GE est de réaliser ce rêve, d’où le montant de 9 millions de dollars que la société a reçu de l’Office of Naval.
Pendant quatre ans, l’équipe de scientifiques de GE mettra au point un processus rapide pour qualifier et certifier les pièces imprimées et nouvellement conçues en 3D pour les navires, les aéronefs et d’autres biens militaires critiques. Ils vont spécifiquement créer des modèles numériques de remplacement ou des pièces nouvellement conçus pour atteindre cet objectif.
Comment vont-ils mener cette mission ?
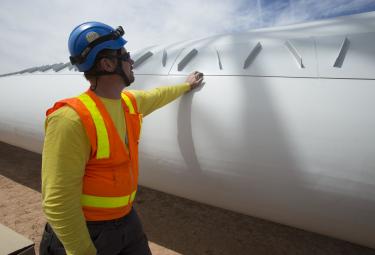
Les jumelles numériques (Digital Twins ) issues de données basées sur des modèles de pièces et de données basées sur des capteurs seront fabriquées à partir d’imprimantes 3D métalliques afin d’accélérer le processus de qualification et de certification des pièces. Les Digital Twins de GE intègrent des modèles numériques d’actifs physiques, de pièces, de processus et même de systèmes.
Le bon point est que les experts mettent continuellement à jour les nouvelles données de capteur ou les connaissances d’ingénierie pour mettre en évidence l’état précis de son homologue physique à tout moment.
« En utilisant la technologie Digital Twin de GE, nous visons à accélérer rapidement la reconfiguration ou la recréation de pièces à l’aide de procédés d’impression 3D », a déclaré Ade Makinde, ingénieur principal chez Additive Technologies chez GE Global Research. « Avec la technologie d’aujourd’hui, le processus de conception d’une nouvelle pièce peut prendre des années. Nous pensons que nous pouvons réduire ce délai à des semaines, avec les solutions numériques uniques en cours de développement. »
Selon Makinde, il serait extrêmement difficile de faire rapidement une pièce de rechange à l’échelle 1: 1 grâce à des procédés d’impression 3D qui ont été produits à l’origine en utilisant des techniques de fabrication conventionnelles. M. Makinde a déclaré : « Le principal défi de l’impression 3D industrielle est de pouvoir construire de manière additive une pièce qui reflète la composition matérielle exacte et les propriétés de la pièce d’origine qui a été formée par des mesures soustractives. Avec le type d’équipement essentiel à la mission de la marine, il n’y a pas de place pour des écarts de performance matérielle ou d’erreur de fabrication. »
Il semble que le défi rencontré au niveau de l’impression par les professionnels soit plus important dans le secteur de l’aérospatiale puisque nous sommes confrontés à des contraintes et des tolérances plus élevées. Les ingénieurs qui travailleront sur ce programme seront donc appelés à « penser différemment » afin d’éliminer cette barrière.
La phase 1 du programme mettra l’accent sur les développements logiciels et matériels sous-jacents. Dans la phase 2, ils fabriqueront un système d’additif complet qui démontre la création rapide et robuste du modèle numérique ou du jumeau numérique d’une pièce et l’impression de cette pièce à l’aide d’une imprimante 3D métal à fusion laser (Direct Metal Laser Melting – DMLM).
Pour des informations exclusives sur l’impression 3D, abonnez-vous à notre newsletter et suivez-nous sur les réseaux sociaux !
Voulez-vous figurer dans le prochain numéro de notre magazine numérique ? Envoyez-nous un email à contact@3dadept.com
//pagead2.googlesyndication.com/pagead/js/adsbygoogle.js
(adsbygoogle = window.adsbygoogle || []).push({});