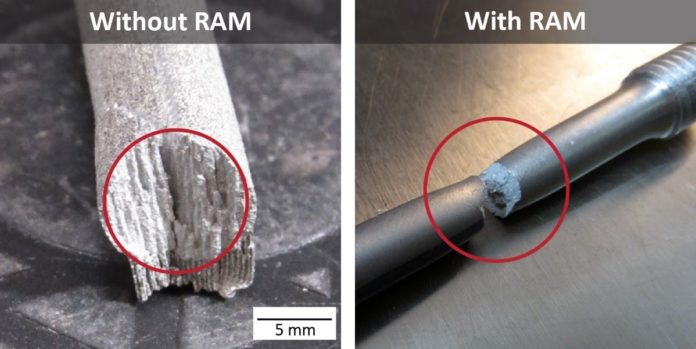
Elementum 3D has been granted patents in the U.S., Canada and Australia for its Reactive Additive Manufacturing Technology (RAM).
Elementum 3D leverages its RAM technology for the creation of printable, high-performance alloy powders based on established wrought alloys, including aluminum 1000, 2024, 6061, 7050, and 7075.
The announcement sheds further light on the manufacturer’s capabilities to produce materials. Indeed, thanks to its core technology, the US-based company has been working on a new range of metallic materials that could be processed on laser powder bed fusion (LPBF).  This new range of materials is the result of the combination of AM with desirable-but-previously unprintable traditional manufacturing materials.
“Popular high strength wrought aluminum alloys could not previously be printed because they suffer hot tearing (solidification cracking), resulting in parts with very poor mechanical properties. The RAM process forms sub-micron inoculants in the melt pool that nucleate aluminum grains to produce a fine equiaxed microstructure for good printability and exceptional performance. By making AM versions of these alloys widely available, Elementum 3D eliminates material compromises and democratizes materials freedom”, explains the company.
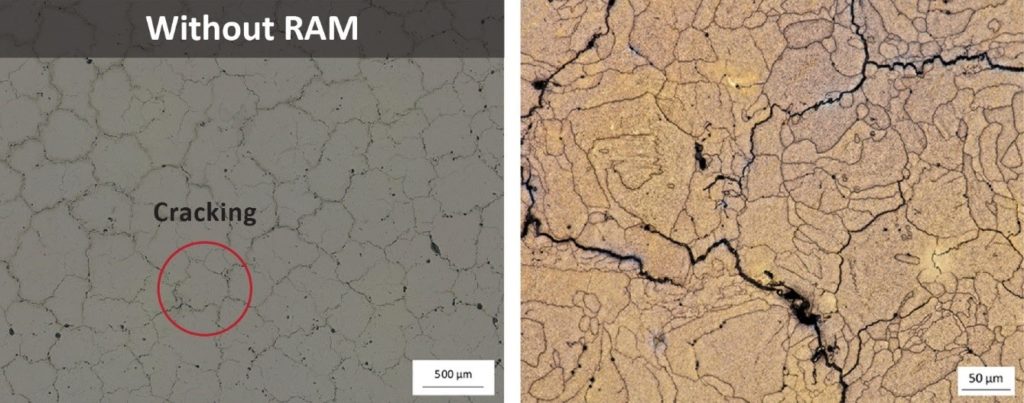
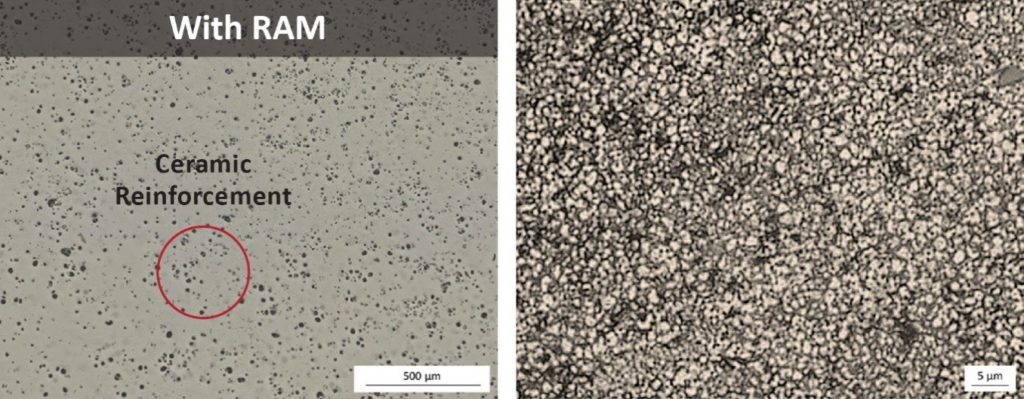
We usually only highlight the “Design for Freedom” capability allowed by AM. However, it should be noted that a similar capability should be provided by materials. In a metal AM process especially, operators should take advantage of a form of materials freedom, yet framed by concise printing parameters. Indeed, the path of the material in an AM process is crucial for a successful fabrication. That’s why, operators should be able to pre-define printing process parameters for feedstock powders and that’s something Elementum 3D can provide via its material process development.
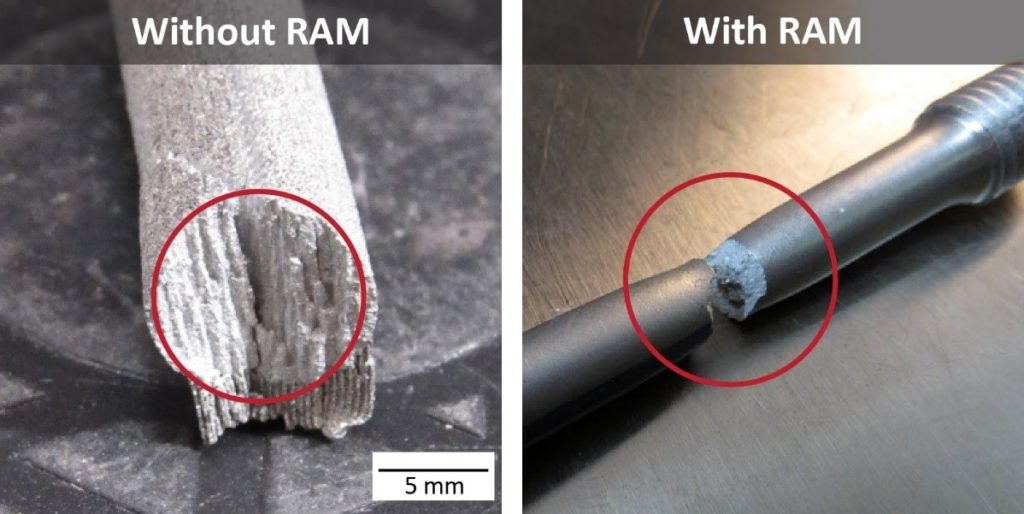
According to Dr. Jacob Nuechterlein, President and Founder of the company, the limited selection of printable metal materials slows down the wider adoption of AM. Their “technology advances metals development for additive manufacturing at an unprecedented pace. It gives engineers the extra degree of freedom they have never experienced, inspiring them to bring into existence new and innovative applications.“
For the company that has recently achieved ISO 9001:2015 certification for quality management, these newly granted patents will further inspire trust in its existing and new clients.
Remember, you
can post free of charge job opportunities in the AM Industry on 3D ADEPT Media or
look for a job via our job board. Make sure to follow us on our social networks
and subscribe to our weekly newsletter : Facebook, Twitter, LinkedIn & Instagram ! If you want to be featured in the next
issue of our digital magazine or if you hear a story that needs to be heard,
make sure to send it to contact@3dadept.com