On the metal 3D printing market, DED and LPBF are often the first technology processes that come to one’s mind when looking to produce large-scale parts. Yet, behind the large-scale 3D printed parts built for the land, sea, air, and space industries, often lie an impressive Electron Beam Additive Manufacturing (EBAM) technology.
In such a process, the raw material (metal powder or wire) is placed under a vacuum and fused together from heating by an electron beam – unlike a selective laser sintering method where the powder melts layer by layer. Parts made using EBAM 3D printers are fabricated in a vacuum environment using extremely high temperatures of up to 1000 °C. This process delivers denser parts that tend to be more durable and that do not require any sort of post-printing heat applications.
Interestingly, there are a couple of EBAM technologies on the market. However, just as is the case with LPBF machines, all of them do not necessarily allow the production of large-scale parts. Sciaky on the other hand, a company that draws upon its electron beam welding expertise, is part of the exhaustive list of manufacturers providing an EBAM technology capable of producing large-scale parts.
Established in 1939, Sciaky was founded by a French family that received support from the US government to develop their business. In the mid-1960s, the manufacturer started developing the wire feed EB process as the main product. In the 1970s, they adopted the Electron Beam Welding technology that they gradually enhanced to help manufacturers save significant time and money on the production of large metal parts. 2009 saw the official launch of the EBAM process (which was then marketed as Electron Beam Direct Manufacturing) as a service option.
To date, Sciaky is a subsidiary of Phillips Service Industries, with about 50 employees operating from the headquarters in Chicago, and with several EBAM 3D printers across the world. As the company celebrates over two and a half decades of its EBAM technology, we caught up with John O’Hara to understand EBAM’s key specifications for large-scale parts, the reason why it is still overlooked and the commercial market of this technology.
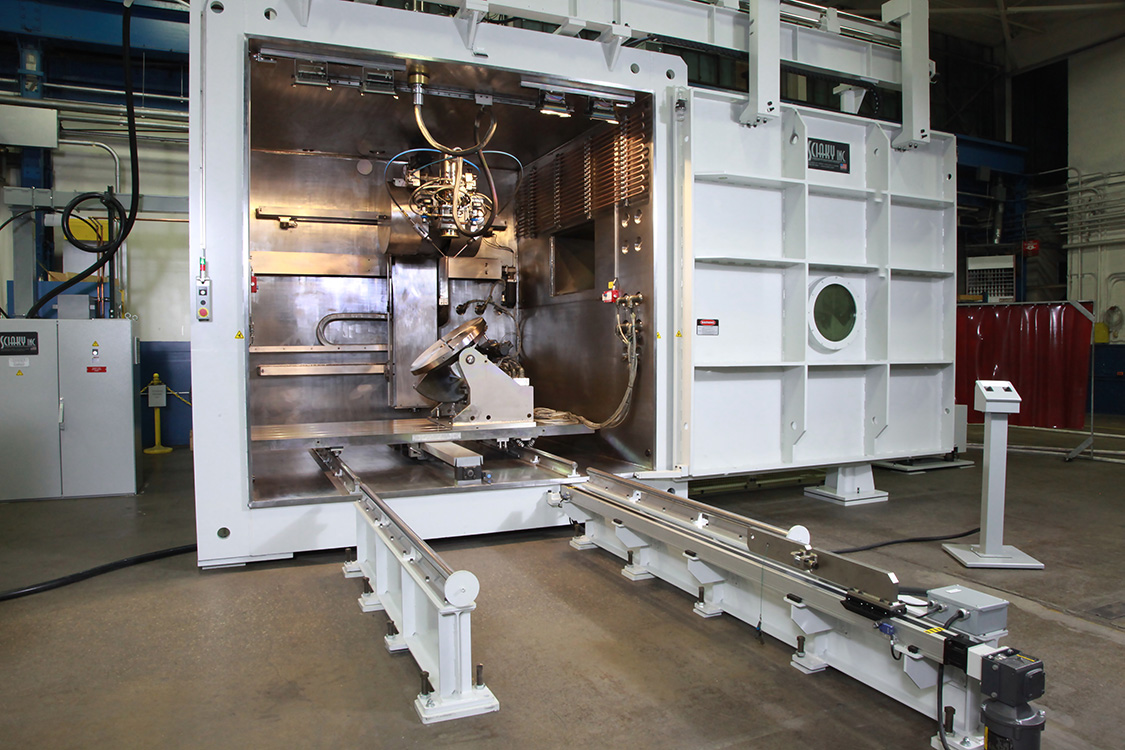
EBAM’s key specifications for large-scale parts
Among the applications that I know Sciaky’s EBAM enabled, I remember a titanium aircraft wing spar that stretched 12 feet in length (3.7m) and a huge titanium aerospace part that weighed over 3,000 pounds (1,360kg), which took 120 hours to build.
One thing we quickly learned from O’Hara is that the size can always be tailor-made. Since they custom build their welding systems, it was only obvious for the team to build tailor-made chambers for their EBAM machines. “EBAM machines are typically made to order, with the sizes ranging in work envelopes of up to 6000mm x 2000mm x 1800mm as our largest machine, and our most common machine with a work envelope of 2000mm x 1100mm x 1500mm. EBAM is always done in a vacuum environment, which is ideal for reactive metals such as titanium, nickel, and refractory metals,” O’Hara explains.
To manufacture metal parts comparable to those made with traditional manufacturing methods such as casting, designers and engineers need to keep in mind a couple of constraints they will need to monitor and address at the design level and during the manufacturing process.
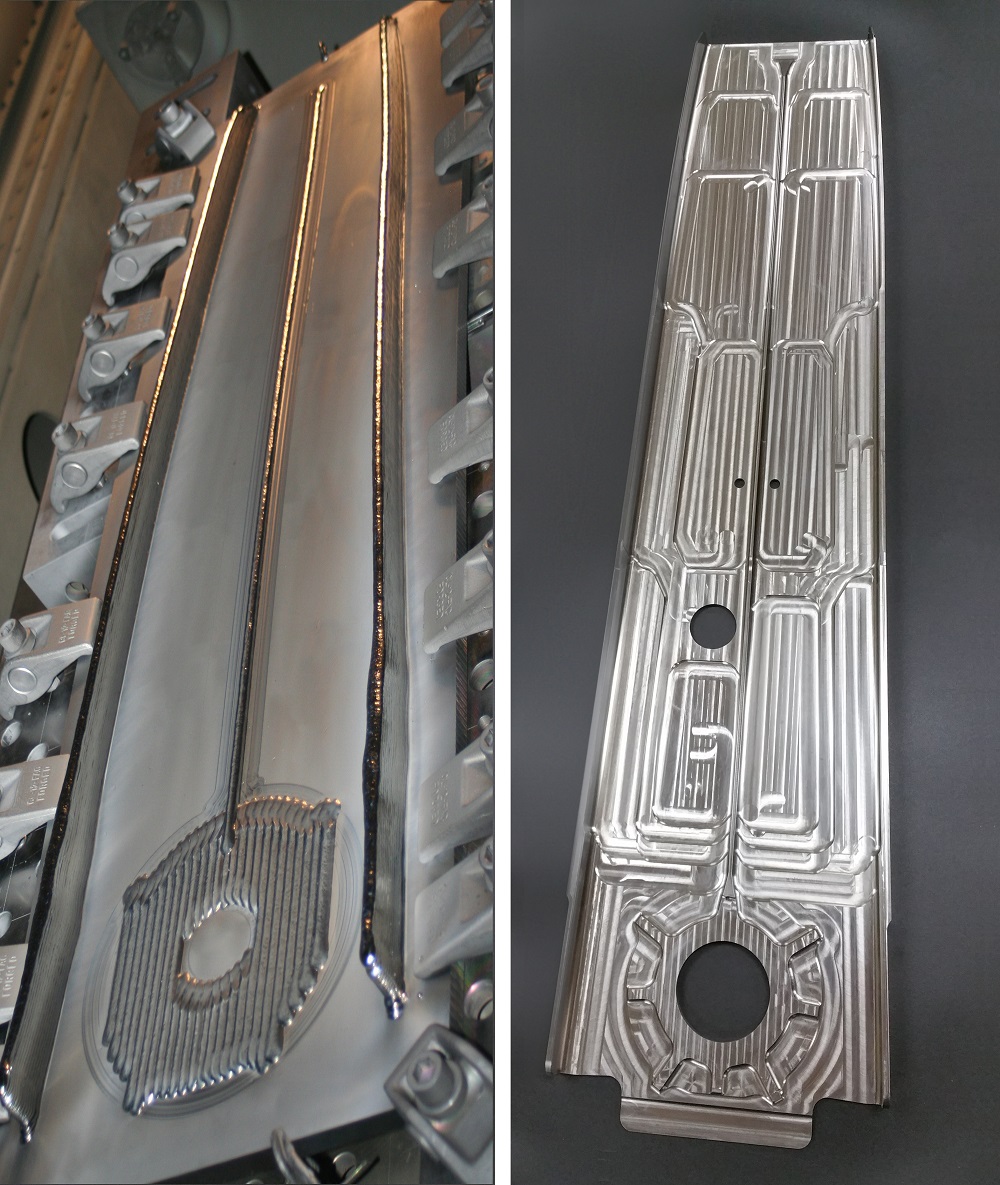
One of the considerations at the design level is that “EBAM must always maintain the melt pool in a horizontal orientation, and must always print onto existing metal. This reduces the opportunities to print hollow cavities. The feature resolution of EBAM at best is 2mm features at low deposition rates, but will typically have a resolution of 8-12 mm,” according to O’Hara.
As concerns the material, due to its use of wire feedstock instead of powder, the technology can minimize waste and cost, resulting in significant savings. Furthermore, unlike powder metallic materials that are quite limited due to their expensive cost, there is a greater availability of wire products.
Like many industrial 3D printers – regardless of their technology, EBAM can also lead to quality issues due to potential changes in the process parameters, in the deposition process or uncontrolled settings in the build chamber. To continuously control and address these parameters, the company has developed a feature that is unique to its machines: a process control system. Named IRISS®, this option which stands for Interlayer Realtime Imaging & Sensing System, is placed inside the 3D printer. It can sense and digitally self-adjust metal deposition with precision and repeatability.
With almost no post-processing, and given the aforementioned features, EBAM seems to be the ideal production technology candidate. So, why is it still overlooked?
The reason why it is still overlooked and the commercial market of this technology.
For O’hara, the main challenge is to fund the qualification of their metal technology for production processes.
“As a manufacturer, we always pursue cost-saving measures. However, regardless of the industry, making a big part remains expensive. The biggest challenge for large format machines is that they are very expensive. The investment that you make is rather large in the development cycle and the operational investment should be proportional to the type of parts you want to produce,” the Global Sales Director points out.
While EBAM lags far behind in adoption, compared to LPBF, “these two technologies have no overlap, and are not in competition with each other,” he adds. “LPBF cannot make parts the size of EBAM, and EBAM is not economical to use on parts with ideal sizes for LPBF. LPBF has been available longer, and has many more companies working on advancing the technology.”
The million-dollar question that comes next is: how do we address this? Educating adopters on the potential of EBAM for large-scale parts is definitely one step to explore but it shouldn’t be the only one. A big part of the work also lies in the development of applications that are not always harnessed in industries with the most stringent requirements. In the end, the more demanding the qualification requirements are, the more time it will take to achieve applications.
On another note, one road adopters could always take – regardless of their industry – is the one that leads to the AM service provider.
“Most people are interested in working with AM service providers. Most of the machines we sell are used for in-house applications. However, Sciaky can take on a production contract. We help our customers justify the cost of the machine, develop the technology for their own use as well as the material properties ideal for their applications,” O’Hara concludes.
This article was first published in the May/June edition of 3D ADEPT Mag
Remember, you can post free of charge job opportunities in the AM Industry on 3D ADEPT Media or look for a job via our job board. Make sure to follow us on our social networks and subscribe to our weekly newsletter : Facebook, Twitter, LinkedIn & Instagram ! If you want to be featured in the next issue of our digital magazine or if you hear a story that needs to be heard, make sure to send it to contact@3dadept.com