I knew, from day one, that Conflux Technology was the kind of company I would closely watch in this industry. Founded in 2017, it came out of nowhere last year by closing a Series A investment round of AUD $8.5 million to develop 3D printed heat exchangers. At the time, I had never talked to founder and CEO Michael Fuller. The reason why I knew I would watch this company is that its core business focuses on a pretty vertically integrated business enabled by additive manufacturing, and not just any applications, the one that most metal 3D printer manufacturers will create to demonstrate the capabilities of their technology. It seemed too simple, but it wasn’t. It is not. When I recently discussed with Fuller, I couldn’t help but smile while listening to his story and company’s journey. Without knowing it, he gave me three more reasons to follow Conflux, and on top of that, discussed a misconception about the additive manufacturing of heat exchangers.
Three reasons that may raise interest in Conflux Technology
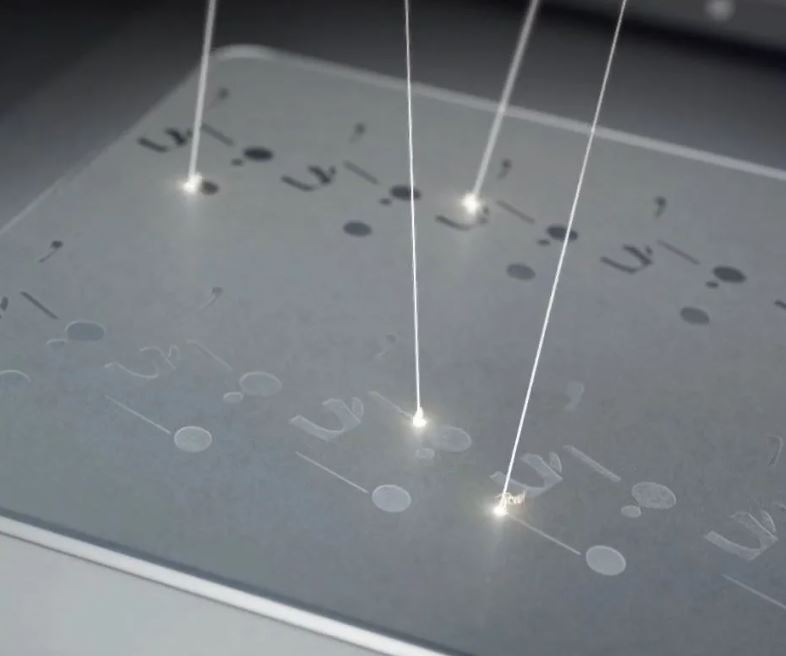
I don’t know about you, but I am the kind of person who looks beyond the quality of a product in business. For me to remain faithful to a product or service, I need to know something about the founder or the people behind the brand, or at least there should be something I respect or value in the company’s vision or values.
- One thing I learned from Michael Fuller is that he is a man who knows how to seize opportunities when they come – and in this case, how to create them.
“There were a few different circumstances that led to a creative “ah ha” moment for me, these were off the back of a 15+ year career in the European motorsport industry, chasing my boyhood dream of designing racing cars. I found myself back in Australia for family reasons and I happened to have a broken ankle. So, I had my laptop out and I got designing”, he told 3D ADEPT Media.
- The second thing you will realize is that he brings credibility to the table.
“I have history as a design engineer and had early adopter exposure to additive manufacturing in the motorsport industry. I also had quite a bit of experience with the pain point of heat transfer. Occasionally you have a good idea, and I wanted to pursue this one a bit further to see if I could get to a proof of concept from a technical feasibility point of view. From here I decided to put a bit of money into getting something made and then tested, and convinced myself to continue forward in terms of commercialization. At that point I needed to figure out how to start and then run a business. So just did a whole bunch of research and got stuck straight in”, he said.
- The third thing enables you to understand the reason why Conflux focuses on heat exchangers and it is “a little bit more of a noble cause.”
If you are new to this area, note that most of our daily electrical appliances (air conditioners, car engines, fridges, etc.) work thanks to heat exchangers. These devices are used to transfer heat between a source and a working fluid. The thing is, designing these devices used to be quite challenging given the complexity to take into account to enable fluids to cool efficiently in such a narrow space.
For Fuller, “it’s so ubiquitous, that the opportunity to improve efficiency in heat transfer means that it can be transferred across almost every sector that you can imagine. For example, improvements in heat transfer efficiency can mean that your aircraft can use less fuel for the same flight. You can achieve that whether it’s in weight reduction or in fuel consumption directly. In the automotive sector, if you can package things into tighter stranger spaces, then you can improve overall aerodynamic drag and so you can improve efficiency there. In microelectronics, if you’re able to take the heat away from the chips more efficiently, then you can calculate more, and you can calculate faster. This then has knock-on effects – as you can imagine in medical research and space exploration- and in all sorts of things. The fundamental impact of improved heat transfer efficiency goes on and on”.
Furthermore, when you look at the way heat exchangers are usually produced, you quickly realize that the traditional manufacturing route may involve a combination of braising, welding, extrusion, machining and molding. In one of the manual processes for example, if there’s a failure between any of those brazing joints it can lead to failure of the unit. Although our goal is not to make a sort of comparison between traditional manufacturing processes and AM processes, it’s fair to say that on a practical level, AM brings a number of pros that are hard to not mention: the ability to manufacture heat exchangers as a single component, the ability to manufacture smaller, lighter objects, more efficiently…However, all of this comes with its own share of challenges.
From design to production: what the manufacturing process looks like at Conflux.
As you may have understood through the lines above, designing heat transfer devices has often been challenging due to technical requirements raised by conduction, convection, and radiation. Heat is energy and, therefore, must conform to the laws of physics. Understanding the principles of heat and heat transfer is thus pivotal for the success rate of projects in the field and to address common challenges before they occur. Needless to say, challenges can increase when we know that AM is the production technology that will be leveraged.
“We have our own series of product families, which are created based off market research and market understanding of what our customers’ pain points are, some of these being they need relatively off-the-shelf, yet highly configurable products. The problem definition is where we start our design process. We’ll then go into either concept selection or an ideation process where we have engineers that are experts in first principles, calculations and multi-physics modelling. We also have design engineers that have got a lot of history in CAD modelling. We run our physics modelling simulations on an in-house, high-performance compute cluster, and utilize the best tools such as CATIA for our CAD modelling. We also have these teams working with the AM process engineers that are in house as well”, Conflux’ CEO explains.
As far as manufacturing is concerned, Fuller first recalls that “the heat exchanger has intricate geometry with very thin walls, and fine feature distances. Quite often these are internal geometries within the device.” “And so what we needed to do was make sure that we had a technology that could print very dense structures, so highly dense that we could have gas type walls separating different heat transfer fluids. We also needed to make sure that we could remove any residual material from the manufacturing process that could be removed completely. Therefore, if you are looking at electron beam melting, this is not suitable, because you can’t get the thinness of walls that you need and you can’t get the internal powder out without having some pretty elaborate processes. With the metal binder jet process, this results in a lower density”.
That’s the reason why, their divergent study on AM processes led them to choose powder-bed fusion technology as the production candidate for these applications. For the most part, they can achieve the sort of heat transfer coefficients that they need to and also remove the residual material.
That being said, thin-walled internal core lattices can expand the surface area and capability of these devices. Betting on a technology like LPBF can lead to the production of walls of 0.1 millimeters of thickness or less. Achieving that requires a lot of development on the ideal process parameters that the machine will follow. And these are some of the key areas where the AM process engineers at Conflux focus.
Another interesting advantage that is very often highlighted is the technology’s ability to deliver lighter parts. The advantage is so common to most AM applications that it might be easy to think that it’s an absolute must in all “heat exchangers” applications. Fuller said no to this misconception:
“A lot of heat exchangers, sit on the ground, and might be mounted to large concrete slabs on the ground. Heat exchangers in the energy generation industry, or in large scale renewables, or in the nuclear industry might be as big as a house, making it smaller in that case can be advantageous because there’s less real estate required, but in terms of light-weighting it’s not all heat exchangers applications. If you look at different industries then you can start seeing where light weighting is important; aerospace, automotive, particularly in the motorsports sector of automotive, increasingly more and more Electric Vehicles. Anything you can do to reduce weight results in fundamental energy efficiency. If you’ve got less weight, then you need less energy to move the thing around. And, you know, laptops, if they can be lighter, then that’s better.”
Current challenges, short & long-term objectives.
On paper, Conflux Technology has everything to succeed. The partnerships the company has signed this year with Dallara Autobili, and GKN Additive, show the team is on the right path in their journey. But this journey would have been tasteless without some pitfalls on the road. In this case, despite significant investment in R&D to match the technology with their vision, the company’s current challenges are now centered around commercialization.  “The industrialization of additive manufacturing is still quite nascent, and the cost of machines are still very high. One of the biggest challenges is making sure that we design and manufacture solutions for customers and markets that are in the right sweet spot for the sort of industrial maturity of the enabling technology which we’re doing”, Fuller notes.
For Conflux’ representative, the productivity is going up and costs are coming down. However, as regards its level of industrialization, it’s not near the hundreds of 1000s of units per annum, so there aren’t those sorts of applications that [they] have developed yet. [They]’re constantly working to drop the asymptote on cost per unit per machine.
Moving forward, we shouldn’t be surprised to see Conflux apply the expertise they have built so far to other areas – an expertise that is characterized by “thin walls and high resolution geometries” as per Fuller’s words. Somehow, it’s already happening, as one of their clients who completed a project on heat exchangers with the team is now working with them on building substrates for catalytic converters in emissions reduction technology. “So, there is transfer there from the sort of expertise in high resolution AM geometries”, Fuller comments.
However, in the short run, Conflux has other plans in terms of expansion and location:
“We’ve been lucky to have a first phase of the business housed at the back of Deakin University in Waurn Ponds, Geelong. They have a large parcel of land which is sectioned off for advanced manufacturing where young, advanced manufacturing businesses like Conflux can spend the first number of years getting settled, which is what we’ve done for nearly five years [now]. We’ll move at the end of this year to a larger facility with more production capacity as well as more testing capabilities. We’ve got boots on the ground now in our key customer regions, with people based in Japan that are covering Japan, Korea, India, and non-Australia Asia region. We have a person based in Central Europe, just outside of Munich and we are also just about to have someone start in North America. So we’re getting a global footprint underway. This is so that we can be near our customers, so we can share time zones with our customers, which is quite tricky from Australia. This is really an expansion on all fronts, but our commercial activities will increase significantly in the coming 12 to 18 months” the CEO of Conflux Technology concludes.
This interview has first been published in the July-August edition of 3D ADEPT Mag. Remember, you can post job opportunities in the AM Industry on 3D ADEPT Media free of charge or look for a job via our job board. Make sure to follow us on our social networks and subscribe to our weekly newsletter : Facebook, Twitter, LinkedIn & Instagram ! If you want to be featured in the next issue of our digital magazine or if you hear a story that needs to be heard, make sure you send it to contact@3dadept.com