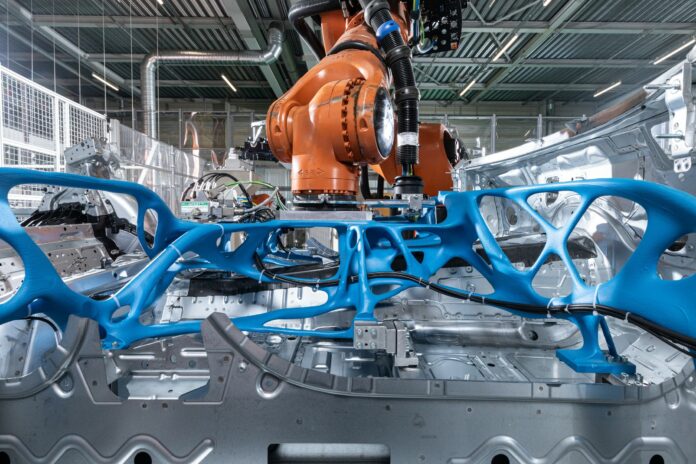
Car manufacturer BMW Group shares a short update on how it has evolved in its use of AM technologies. After three decades of experience as an AM user, one thing we’re sure of is the fact that the company continuously expands its scope of expertise – from tailor-made orthoses for employees, and teaching and production aids, to large, weight-optimized robot grippers, used for such things as CFRP roofs and entire floor assemblies.
To date, the BMW Group’s “Additive Manufacturing Campus” in Oberschleißheim reported on the production of 300,000 parts in 2023; this does not take into account the additional 100,000 printed parts produced per year across all the plants that form the global production network, from Spartanburg and the German plants to sites in Asia.
“As well as the direct additive manufacturing procedure, the BMW Group has also been using sand-based 3D printing to create moulds for many years at its site in Landshut. This technology is typically used to manufacture prototype casts, as well as for the large-scale production of components for high-performance motors. Another very attractive field of application is now that of large production aids,” says Klaus Sammer, Head of Product and Process Planning for Light Metal Casting.
Key focus on the production of grippers
For a number of years, the BMW Group’s Lightweight Construction and Technology Centre in Landshut has been using a particularly large gripper element, which was made using the 3D printing process. Weighing around 120 kilograms, the gripper for a robot can be manufactured in just 22 hours and is then used on a press in the production of all CFRP roofs for BMW M GmbH models. The press is first loaded with the CFRP raw material. The gripper is simply rotated 180 degrees to remove the finished roofs. Compared to conventional grippers, the version manufactured using 3D printing was roughly 20 percent lighter, which in turn extend the operating life of the robots and also reduced wear and tear on the system, as well as cutting maintenance intervals. The combined use for two steps also reduced the cycle time. A unique feature of the robot gripper is the ideal combination of two different 3D printing processes. While the vacuum grippers and the clamps for the needle gripper to lift the CFRP raw material are made using selective laser sintering (SLS), the large roof shell and bearing structure are manufactured using large scale printing (LSP). LSP can be used to produce large components economically and sustainably. The process uses injection moulding granules and recycled plastics, while CFRP residual material can also be used and recycled. Compared to the use of primary raw materials, CO2 emissions when manufacturing the gripper are roughly 60 percent lower.
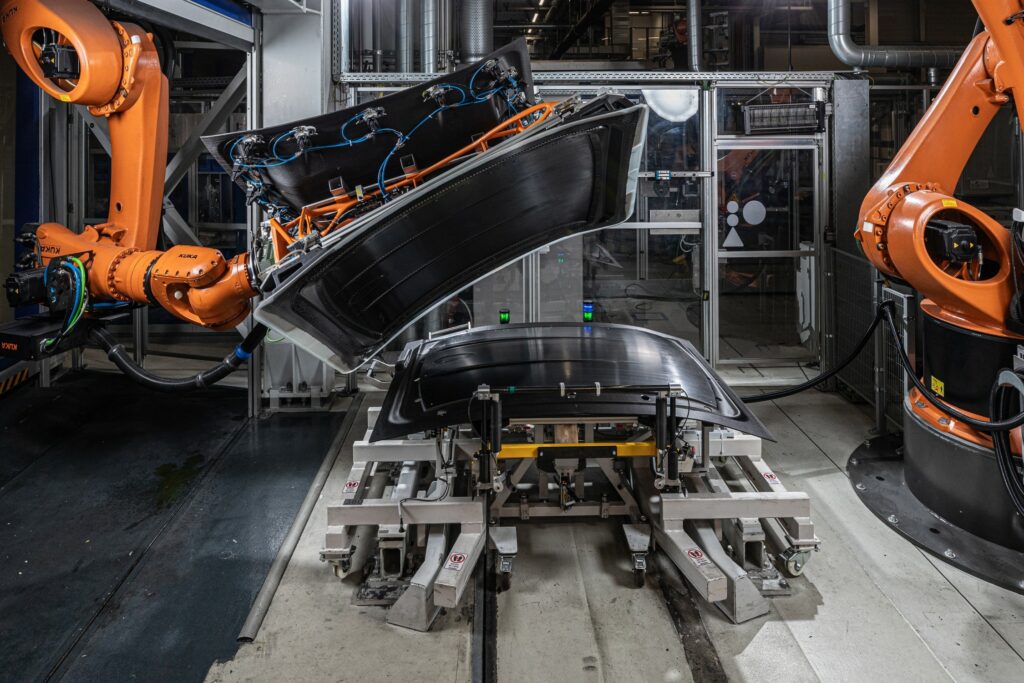
In the summer of 2023, a new, even lighter generation of gripper was introduced. To achieve this, the previous gripper concept was analyzed and optimized topologically – the birth of the bionic robot gripper. This combines the roof shell from the LSP printer with SLS vacuums and a bionically optimized bearing structure. For this, a mold with printed cores is used in the sand casting. This mold is then cast with the intricate aluminum structure. The new gripper is a further 25 percent lighter than its predecessor, meaning the entire process of manufacturing a CFRP roof of the BMW M3 can be performed with just one robot, rather than three as was previously the case. Nowadays, double grippers manufactured individually within the BMW Group, courtesy of 3D printing, are used for all CFRP roofs at BMW Group Plant Landshut.
However, the company is now taking it one step further at BMW Group Plant Munich. As of recently, the first examples of a bionic robot gripper have been used at the parent plant. This gripper can hold and move the entire floor assembly of a BMW i4. For the floor assembly gripper, 3D printing is used to create a sand casting mould, which is filled with liquid aluminium. The bearer is optimised in terms of weight and maximum load capacity, and weighs with all additional add-on elements a mere 110 kilograms. That makes it roughly 30 percent lighter than the previous, conventional model. Manufacturing using sand casting and aluminium makes it possible to represent intricate load-optimised structures. This results in maximum weight reduction and thus makes it possible in the medium term to use smaller and lighter heavy-duty lifting robots, which require less energy and thus reduce CO2 emissions.
Remember, you can post your job opportunities in the AM Industry on 3D ADEPT Media free of charge or look for a job via our job board. Make sure to follow us on our social networks and subscribe to our weekly newsletter : Facebook, Twitter, LinkedIn & Instagram ! If you want to be featured in the next issue of our digital magazine or if you hear a story that needs to be heard, make sure to send it to contact@3dadept.com