Around two weeks ago, we gave a sneak-peek at Solukon’s new machine for automated unpacking and cleaning. Named SFP770, the new system is meant for 3D printed parts manufactured on polymer powder bed fusion additive manufacturing systems.
“With the launch of the SFP770, we bring the benefit of years of experience in the depowdering and unpacking of metal AM parts to polymer AM applications. As with its highly successful line of solutions for metal AM depowdering, the concept for the SFP770 was driven by the needs of its leading customers”, Andreas Hartmann, Technical Director and Co-Founder of Solukon comments.
The polymer powder removal process
In a production environment, challenges encountered by operators using metallic powders are pretty much the same than challenges encountered with polymer powders: labour and time intensive operation, unsafe work environment, inconsistent and unregulated cleaning results as well as dust assessment.
In such cases too, an automated powder removal enables to address these challenges. The process is therefore quite simple: loading – unpacking – cleaning and unloading.
Just as we used to see with metallic powders, it is also possible to recycle and reuse excess powder collected at the end of the removal process.
Interestingly, the unpacking function can be supplied with or without the cleaning function, which provides certain flexibility to the machine user. Furthermore, according to Solukon, it would only take about 30 minutes to unpack and remove residual powder from a fully loaded build box of 150 litres of polymer parts.
For instance, in the case of polymer 3D printed parts, once a completed build box of an EOS P7 system is loaded into the unpacking area of the SFP770, the top of the box is covered by a special cover device containing an integrated sieve.
Experts at Solukon explain that the build box is rotated around the horizontal axis by a swivel device into an inverted position while the sieve inside the cover device starts vibrating, separating the parts from the loose powder. A vacuum conveyer thereafter directly extracts the powder and expedite the residuals to an external recycled unit.
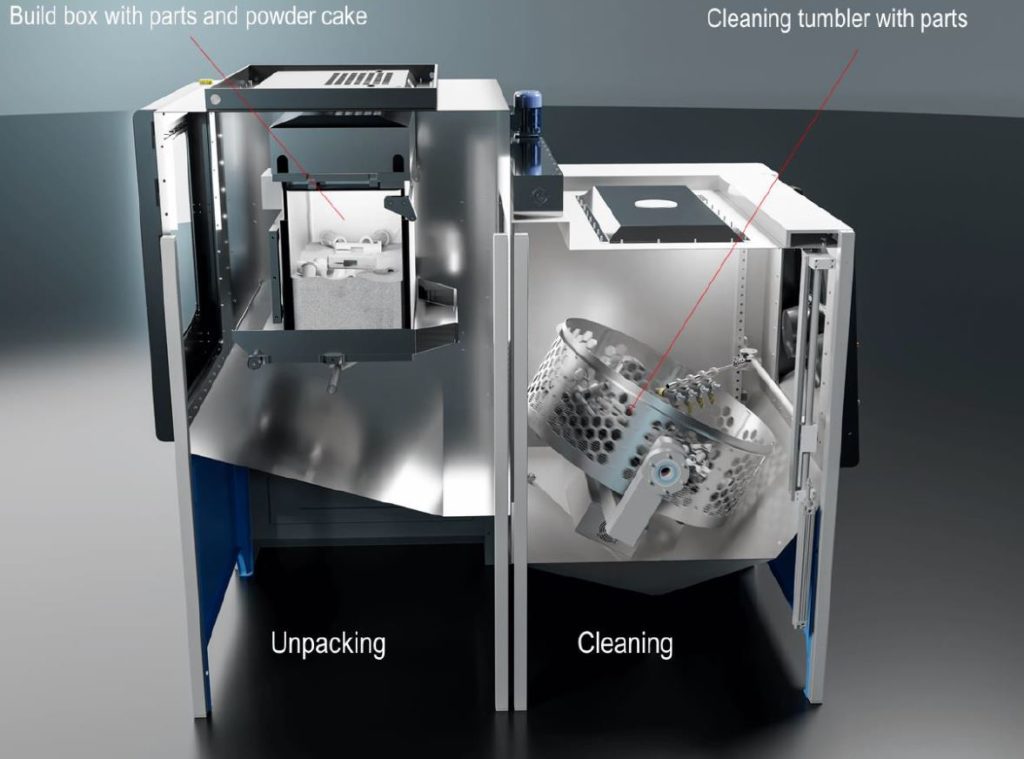
Following the unpacking process, parts are automatically transferred to the cleaning tumbler which starts rotating.
“Glass beads and ionized air are jetted onto the printed parts to remove residual powder that may have remained or does not have the quality to be recycled. At the same time the swivel device rotates the build box to the home position and can be loaded with the next box. Due to the independence of both processes, a new unpacking job can start simultaneously while the cleaning process is still ongoing. Cleaning time, air pressure, the angle of the cleaning tumbler, as well as the distance between the jetting and blowing devices and the part, can be easily programmed online”, the manufacturer explains in a press communication.
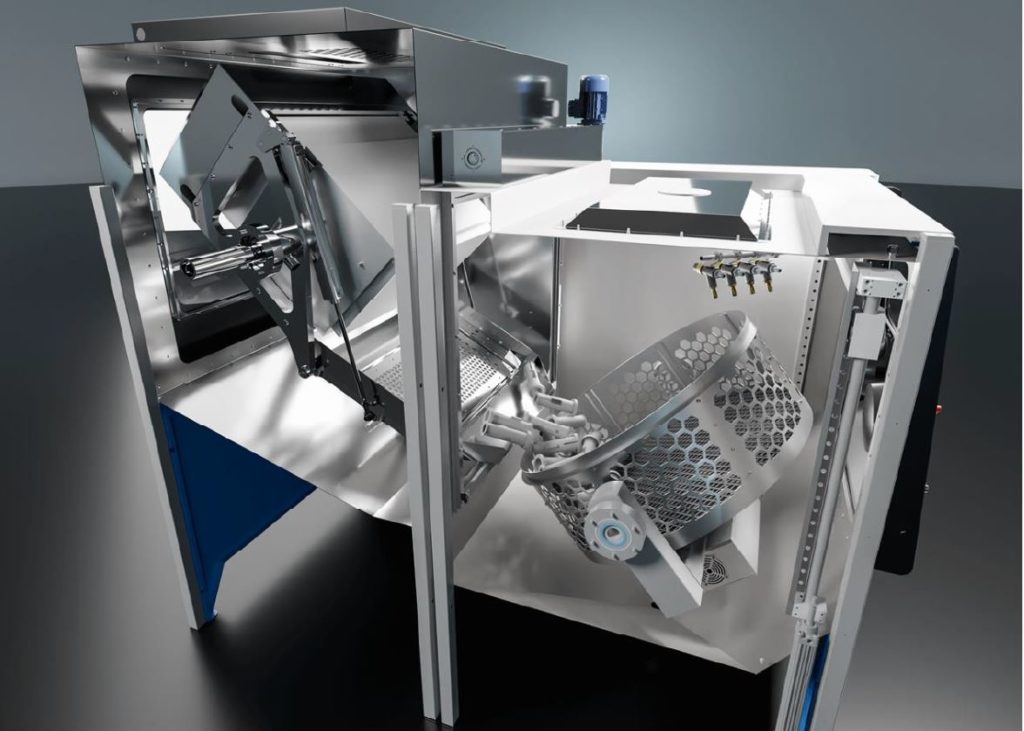
Once the parts are unloaded from the SFP770 into a receptacle for other post-processing tasks, they are already powder free.
Solukon’s Co-Founder Dominik Schmid said: “we have applied to polymer depowdering the same rigorous attention to detail, and dedication to the needs of customers, that we have shown in metal powder applications over the years.”
The German machine manufacturer has been able to develop the polymer powder removal system as part of a collaboration with a customer. Even though the name of that customer has not been revealed, we know that the system is already running at its place, so hopefully, further feedback will be released in the upcoming months regarding its utilization.
In the meantime, please note that live demos of the machine will be performed during Formnext Connect from 10-12 November.
Remember, you can post free of charge job opportunities in the AM Industry on 3D ADEPT Media or look for a job via our job board. Make sure to follow us on our social networks and subscribe to our weekly newsletter : Facebook, Twitter, LinkedIn & Instagram ! If you want to be featured in the next issue of our digital magazine or if you hear a story that needs to be heard, make sure to send it to contact@3dadept.com