“Now I know what I’m doing every March for the rest of my life.”
That’s one of the remarks made during the feedback session on the last day of AMUG 2023, a tradeshow held in Chicago, US, from March 19th to 23rd – and where 3D ADEPT Media was a media partner. If you want to dive further in the AM world and you’re looking for a life-changing conference, then stay with me.
Additive Manufacturing Users Group 2023 was a blast, packed with cool new technology, valuable knowledge sharing, and warm loveable people, each with their own personal connections to AMUG and the additive manufacturing field.
Things kicked off Sunday with a first timers meet-and-greet, among other things. Monday was when AMUG roared into full force. Breakfast was chatty. Laughter and the clinking of dinner plates filled the Grand Ballroom.
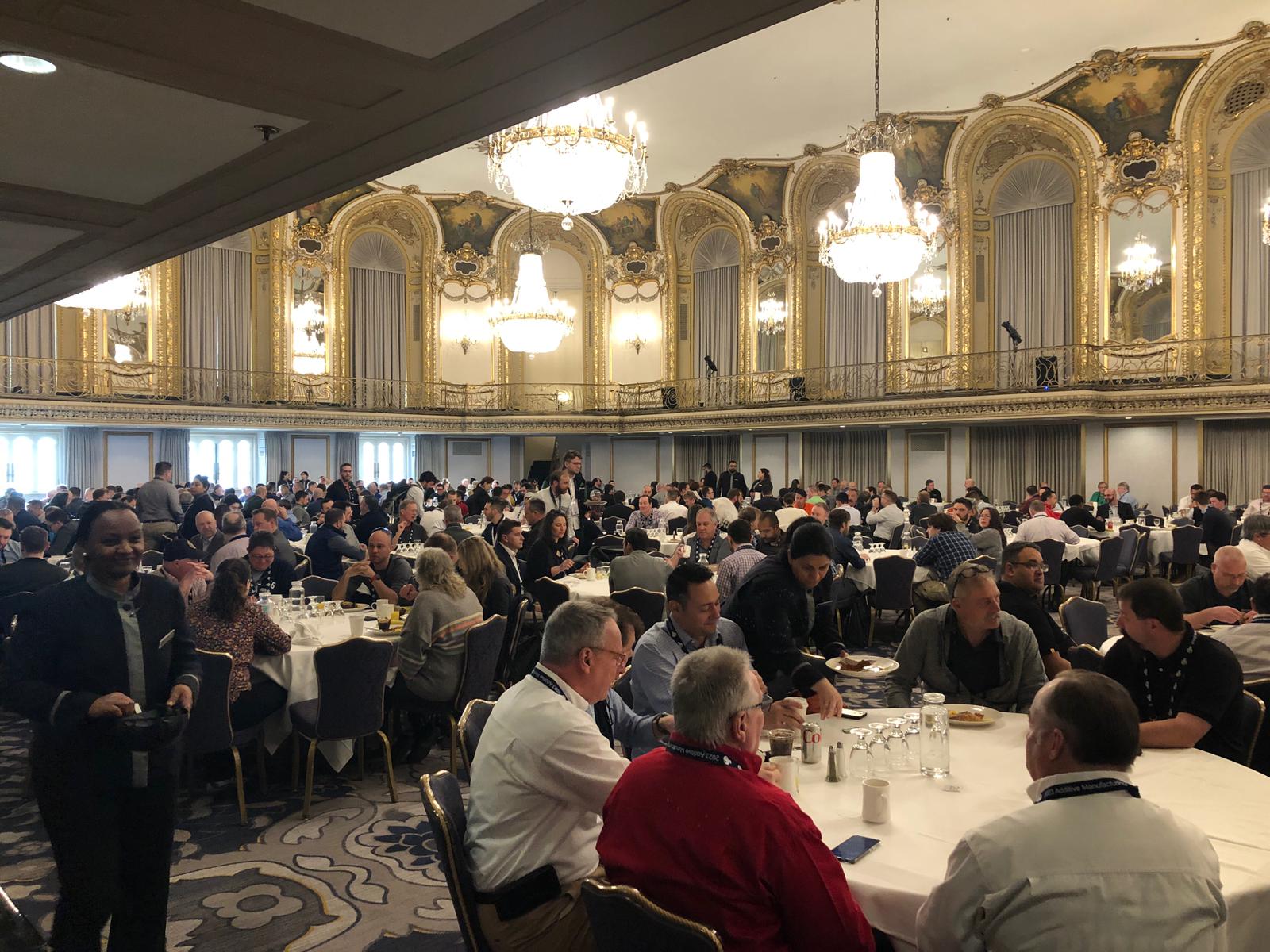
At the opening ceremony, Todd Grimm played the role of MC. He stressed the importance of getting out of your shell and networking. To grease the wheels, he had everyone go through the AMUG handshake. Everyone got to their feet and greeted one of the people sitting next to them, not unlike spreading peace in church. We were instructed to say our names and the organization we came with. I talked to Rene Backx from MX3D, all the way from Amsterdam. We were both first timers and we bonded over the excitement we felt about what might lie ahead.
Director of Education Jordan Weston walked the audience through all the features of the AMUG app, including the full schedule, a directory of other participants, a place to give feedback, and a section to cast votes for next year’s board. Weston encouraged us to use the feedback functionality if one came across a presentation at the conference that felt too much like a sales pitch. He stressed that sales were not the purpose of AMUG.
On the exhibition floor
We were released like a herd of animals to frolic on the exhibition floor. The exhibitors, a slew of companies ranging from brands just getting their start to industry giants, were set up in rows in the expansive salons. Most of the Diamond and Platinum sponsors, like software company Dyndrite, AM service provider Wurth, and specialty chemicals company Evonik were in Salon A. This was the area of the week where sales pitches were acceptable. Some vendors were actually selling printers for attendees to take home after the conference.
On the floor, I was able to connect with Zane Marek, a product manager at JEOL, a machine manufacturer who unveiled their first metal 3D printer two years ago: the JAM-5200EBM machine. The latter is based on Electron Beam Powder Bed Fusion (PBF-EB), a process that does not require to conduct heat treatment after the build phase. The electron beam is produced by LaB6, or lanthanum hexaboride, then a high voltage extracts a stream of electrons and differential pumping lens focuses the beam, which then sinters the powder. Electron beam printing sometimes means faster printing and higher density in powder bind then many laser printing devices.
I also caught up with Bruce Bradshaw and Greg Kline at 6K Additive, the AM brand of materials producer 6K. They’re focusing on sustainability and recycling in the additive space. 6K buys waste materials from customers in exchange for credit toward fresh powder that they sell. Then they reprocess the waste by adding back elements and materials that were spent, turning it back into usable powder for AM that can be sold. This means less waste.
“We’re very flexible in the kinds of feedstock we can use, whereas traditional manufacturers are often constrained to a bar or ingot”, says Kline. The company is now looking to double the number of production reactors at their Pittsburgh facility, from four to eight.
Also on the exhibition floor was AM giant Stratasys. They showed up with a flashy arsenal of printers and creations. Colton, one of their application engineers, showed me around. He says a big focus for them is developing more advanced photo-polymers for use in polyjet and stereolithography printing.
Among all the showcased applications, what raised my interest the most was a nylon airflow duct printed by a Stratasys H350 3D printer. The part can be found in the AC system of every NASCAR and is the only 3D printed part standard to the fleet.
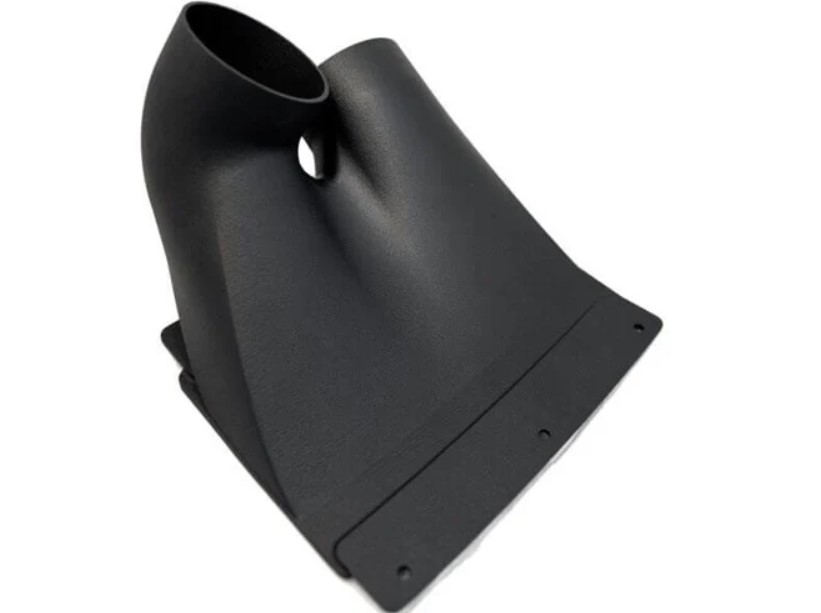
While darting around the floor, I sometimes heard a loud crash shower above the noise and chatter of the crowd. I followed the sound to the source and wound up at the Wurth booth in Salon A. Wurth was selling some printers, and if you bought one, they would let you bang the gong.
Wurth Additive Group is a relatively new branch of Wurth, a giant in European and global manufacturing supplies distribution. At AMUG, the brand was pushing a range of metal and polymer printers. One they were particularly proud of was the Kurtz Ersa Alpha 140, which they described as the perfect entry level machine for metal-additive. Launched two years ago, the compact and mobile 3D printer is based on Laser Beam Powder Bed Fusion technology. According to the team at Wurth Additive, the 3D printer was capable of printing parts on the tarmac of an airport while connected to a small portable generator, in a recent demo. They are testing to see if it can be used in situations where access to the power grid might not be readily available, like on an offshore oil rig, for example. They want to meet the demands for flexibility that the recent supply chain disruptions have placed on engineers.
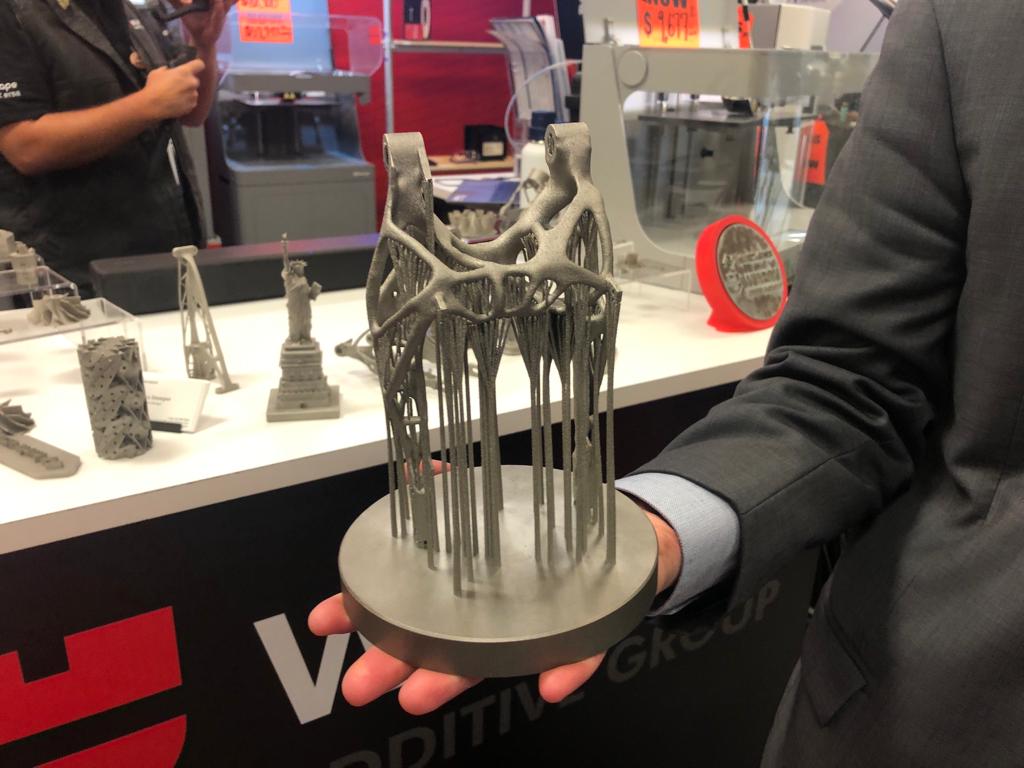
Showing me around Wurth was the kind and gregarious Ed Tackett. He was wearing his Wurth quarter zip sweater with slacks, and has pushed back gray hair and a salt-and-pepper beard. Tackett says this year was his 25th AMUG, and in that time he has taken up lots of responsibilities in education. He’s run several workshops on ink hydro-dipping.
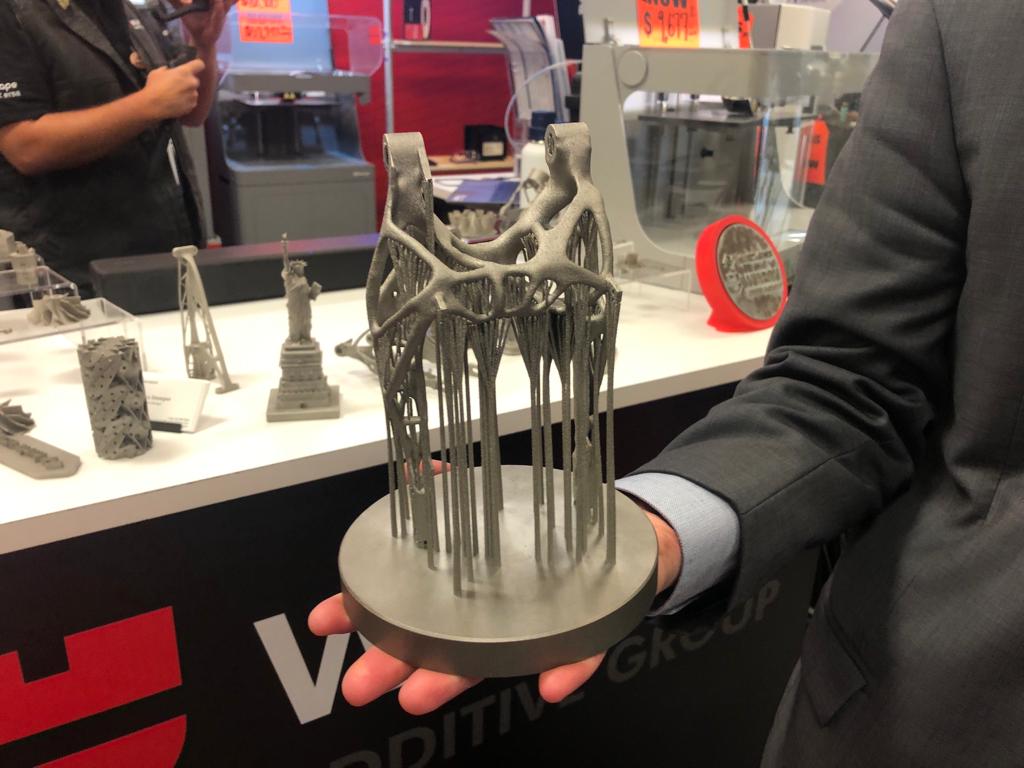
I asked him what was hot when he first started coming to the meeting in the mid-nineties. He said Z-Corp was a big player at the time, having developed a new way of color 3D printing, borrowing the inkjet technologies already developed in 2D printing. He sees laser-scanning and metrology as big developments through the years as well.
For Tackett, a significant trend in the industry now is additive’s ability to ease supply chain issues that have arisen throughout the pandemic times. As you know, AM is the perfect solution when someone needs a variety of parts that they can’t get because orders are backed up, or there is nobody to transport them.
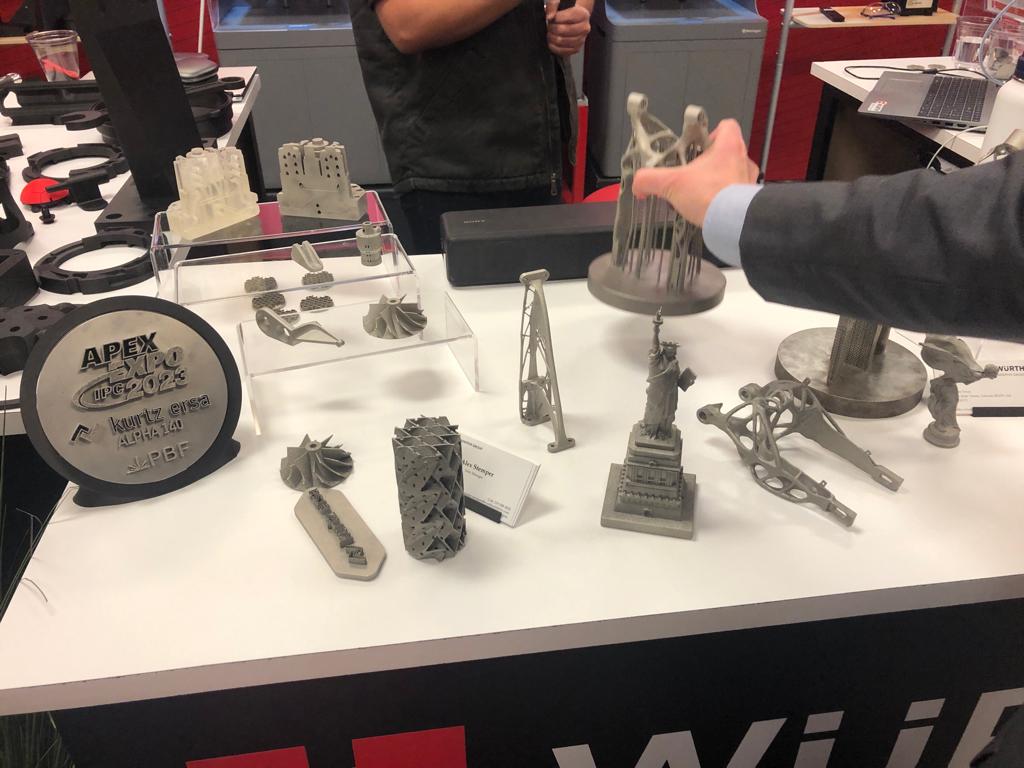
The last thing Tackett noted was the need to look to the future of the conference and the industry. He thinks AMUG should invest more in young people coming to the conference and presenting research, while also familiarizing themselves with what’s out there. “Who’s going to be the next Ed Tackett around here?” he said. I told him I was wondering the same thing.
After the exhibits on Monday, we all sat down for a networking lunch, then transitioned over to the more educational activities. These took over as the dominant programming throughout the rest of the week, since Monday by far was the most active day on the exhibition floor.
The educational events
The educational events were a mix of panels, presentations and workshops, each sorted into an experience level of beginning, intermediate and advanced. These covered a broad sweep of topics, from medical and dental to aerospace to business skills for starting up your own AM company.
Here are some of the educational sessions that I went to that stood out to me:
I sat in on a presentation from Patrick Gannon of Ricoh on 3D printing radiographic phantoms used in the medical field. That’s basically printing things that look like body parts in broad daylight, while also mimicking human tissue in a CT-scanner. This is really helpful when calibrating CT-scanners, and it saves a lot of money and time when the scanner can be calibrated with a 3D-printed model instead of a person. It also saves that person from being over-exposed to X-rays.
Gannon was also running to be on the board (he didn’t end up winning). He says AMUG has done a great job at maintaining the feel of the conference even as it has grown far beyond the attendance numbers that it started with. He says he loves things like the app, that make the whole week run more smoothly without changing its fundamental character.
This fundamental character is one of the biggest themes I picked up on all week. Is AMUG getting too big? Has the amount of money in AM forever changed the nature of knowledge sharing, raising the stakes such that it’s no longer kosher to talk shop with somebody who’s not working for the same company as you? Are there too many sales reps and not enough engineers?
For starters, there were definitely PLENTY of engineers.
I heard several people ask these questions and I think they’re all valid. But at the end of the day, it was meeting people like Ed Tackett, and hearing him describe how he looks forward to coming back and seeing his industry friends every year, that convinced me the people who have been coming for years are still at the heart of the event. And all they want is to share it with as many people as will listen.
Another presentation that stood out to me was on CT Scanning and Digital Radiography. Not only were the panelists good and the MC engaging, but the Q&A session, where the audience was able to ask the panelists questions, was a real bonding moment. All the questions were specific and unique, and it felt like everyone in the room related to them and couldn’t wait to hear the answer. The panelists covered the limitations of CT-scanning, materials that can be difficult to work with and how scanning for use in production is gaining steam in Europe, and might be bigger in North America soon.
Some other educational sessions were “Printer Hacks You Wish You Knew”, a workshop in which a presenter recommended using toaster ovens (like the ones you buy at Home Goods) to dry out parts after soaking them in an IPA solution. There was also “Benefits of Metal Paste Feedstock”, “Snap Crack and Pop: Hands-On Material Testing”, and “Applying Machine Learning to Enable Rapid Material Property Allowables Development for AM”, among other things.
What else?
Tuesday night featured an offsite party at the gorgeous Museum of Science and Industry. Wednesday night was a combination of Steampunk and Las Vegas dinner party.
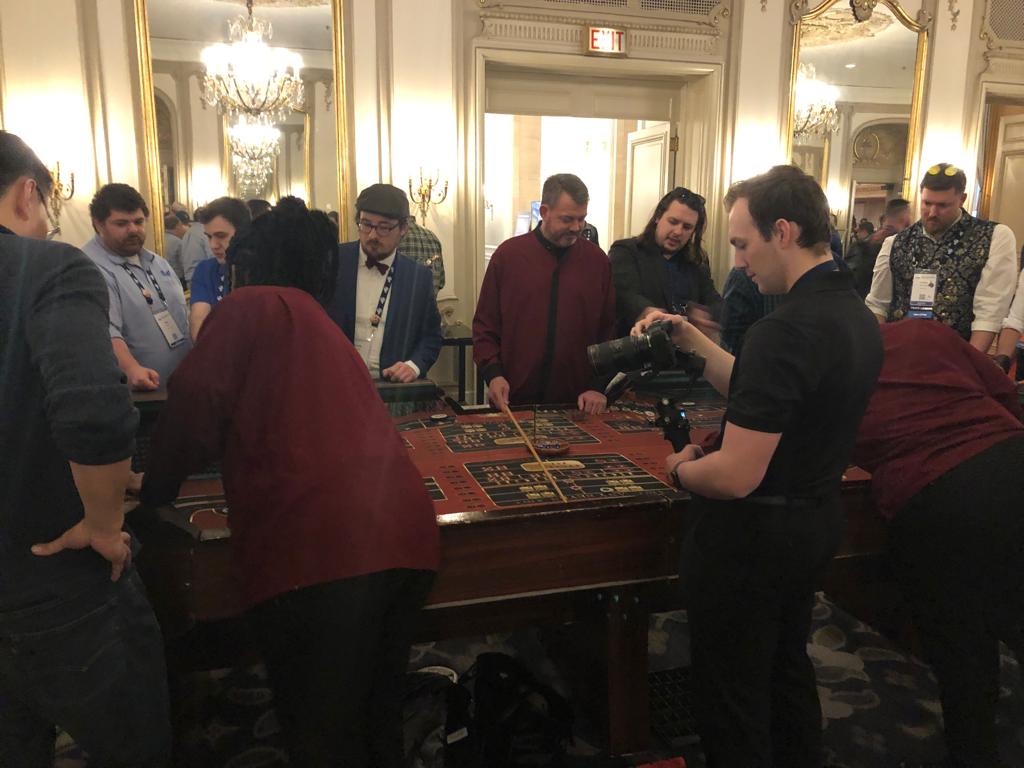
Ben Loerke from University of Dayton is a notable name from the Tech Competition. His additively-manufactured microturbine took home first in the Tech Competition for Advanced Concepts, as well as the Member’s Choice Award.
Max Hoat of space company Launcher gave an interesting keynote speech on Thursday morning. He presented on the High Performance, Low Cost liquid Propulsion enabled by AM. The topic is timely considering Relativity Space’ recent launch. Hoat said in his speech “AM has changed the game completely” as he described how AM has allowed Launcher to print a copper chromium zirconium combustion chamber with intricate cooling channels, to allow for novel cooling methods that increase performance. Hoat played mesmerizing videos of the engine tests. The crowd ooo-ed and ahhh-ed.
The ooos and ahhhs became goodbyes and farewells as the conference began to wind down on Thursday.
So you got plans every March for the rest of your life? Consider penciling in AMUG.
Catch up with the latest announcements on AMUG here.