Given the present economic situation, it’s hard to have a decent conversation about oil and gas without having to complain about current price fluctuation. Yet, if we look at the bigger picture – and leave the governments to handle the war in Ukraine and its consequences -, we might realize that one way for oil and gas companies to lower costs and increase margins would be to focus on sustainability. As it has been mentioned multiple times in this edition of 3D ADEPT Mag, “an organization can truly say it is sustainable when it is responsible vis-à-vis these three aspects: profit, people and planet” – the triple bottom line. What’s crazy about this idea, is that the more you think about it, the more you realize that additive manufacturing can play a key role in meeting the guidelines related to each of these aspects. It’s a virtuous circle.
The challenges of the oil and gas industry with regards to sustainability have already been discussed in a previous edition of 3D ADEPT Mag. Over time we came to realize that, while regulations dictated by governing bodies continue to establish strict guidelines to follow, there has been a strong shift towards the customers themselves setting tight demands on valves in industrial processes.
In case you are an outsider to this industry, please note that valves are a pivotal component of any piping system, hence their importance for the oil and gas industry. They can be used to control flow rates, isolate, protect equipment, and operate in the refining process of oil, gas, hydrogen and other such media. This makes them essential to a wide range of functions and applications.
The thing is, companies that manufacture valves have to respond to a confluence of forces that are changing their manufacturing landscape – automation, agility and digitalization, to name a few – no matter what they are, they have to be perfectly in sync with that triple bottom line.
The triple bottom line
People
For any organization in the oil and gas industry, one of the worst situations that may happen is to have somebody hurt in their facility. To mitigate some of these risks, a lot of companies are investing in artificial intelligence (AI) and robotics to perform high-pressure testing of their valves. Others use control valve diagnostics to monitor valve performance, recondition older valves or simply replace them. Interestingly, in any of the two latter solutions (reconditioning and replacement), you may be able to make profit while complying with environmental guidelines.
Profit and Planet
Those who choose to recondition older valves often do so through the route of a qualified valve repair center which reconditions them back to factory specifications, aka “like new” condition. Through this route, they can save 40-60% compared to buying new valves. Sometimes, it also reduces waste and recycling costs.
On another note, when valves are replaced, they’re often thrown in a landfill or sent for recycling. This might require a certain amount of energy to recycle metal, but with the right manufacturing process and powders, it’s possible to achieve better ROI. That’s something we discovered with materials producer f3nice and oil and gas company Valland.
The confluence of forces changing the manufacturing landscape of valves
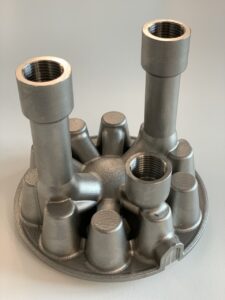
If you are a regular reader of 3D ADEPT Media, you may already have heard about F3nice. Everything about this materials producer is interesting: the history of their creation, their vision, the way they work…but what you should keep in mind here is that they source metal scrap and disused parts and transform them into metal 3D printable powder.
Valland on the other hand, has been operating in the oil and gas industry since 2006. Founded by experts who have been working for more than three decades in the valves business, the company focuses on engineering valves. Their main market is oil & gas exploration and production sectors, including subsea and transmission, and other special service industrial application. In 2016, they started experiencing additive manufacturing (AM) and how the technology could benefit their target industries. The year 2019 marked a period of commitment to developing an AM-related business with the installation of 2 FDM 3D printers. This business continuously expands and 2021 saw the development of an AM-dedicated business unit, named Valland3D, with a 3D printing lab capable of handling a wide range of materials spanning polymers, resins and metals.
“Valland3D currently make uses of AM technologies to develop innovative solutions and produce components for Valland’s core and related products which consist of high quality and tailor-made valves for the oil & gas and energy sectors. Building on this, the company aims at spreading through the AM industry an innovative approach based on the concept of working in synergy with the client (eg: end users or EPCs) assisting it along the entire AM value chain. To confirm this, in addition to the pure 3D printing-related services, we offer components’ design or re-design applying advanced topology optimization tools and additive process simulation services. Moreover, Valland3D’s action is also geared toward supporting partners during the components’ usage life cycle through the possibility of adopting spare parts digital inventory solutions significantly contributing in squeezing the spare parts lead time and allowing so for the full realization of an on-demand maintenance approach”, Alex Giorgini, R&D Engineer told 3D ADEPT Media. In addition to their in-house AM capabilities that include FDM, SLA, LB-PBF technologies and a metal powder atomization R&D hybrid platform capable of combining alternative AM feedstock production technologies, Valland3D can also handle post-processing activities such as components heat treatment and optimization of surface finishing degree through shot peening and sandblasting processes.
Valland3D is one of those companies that believes that AM can positively influence the shift towards a triple bottom line paradigm. As a matter of fact, it has become a regular practice for the team to support AM projects through Life Cycle Assessment (LCA) studies. Last year, it took part in a Joint Industrial Project promoted by Wilhelmsen and thyssenkrupp related to the redesign for AM and subsequent 3D printing of critical valve components. “In the context of the described project roughly 50% of GHG emissions savings have been assessed by comparing the AM scenario to the conventional manufacturing one through the development of a simulation model based on LCA methodologies”, Giorgini comments.
However, what raises our interest further is the LCA of an additively manufactured part conducted in collaboration with f3nice. The latter aimed to provide a qualitative evaluation of the environmental savings related to the redesign and printing of the body and closure parts of a valve.
LCA of 3D printed valve components
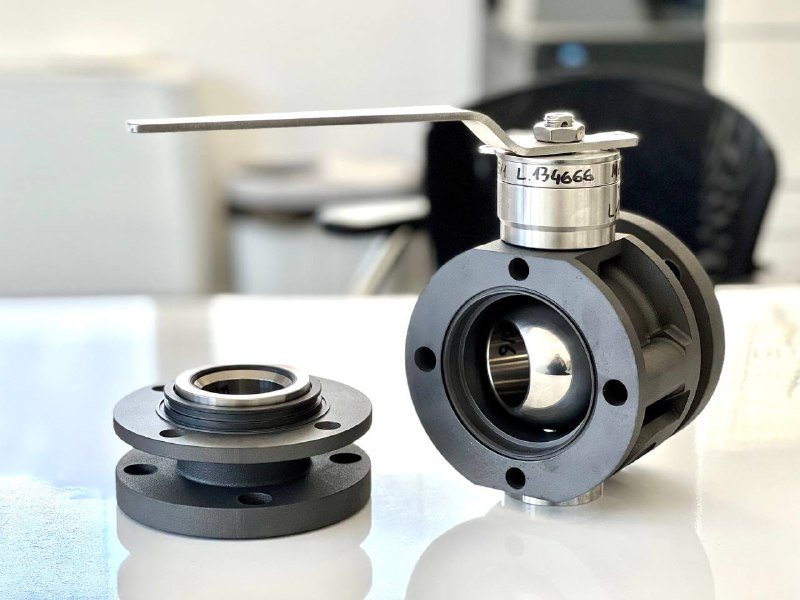
As part of this project, f3nice brought its expertise in the development of metal 3D printable powder through the sourcing of metal scrap and disused parts while Valland brought its experience in the design and manufacture of valve components in the oil and gas industry.
According to a report issued on this topic, five main contributions in respect to both the conventional as well as the Additive Manufacturing (AM) routes have been considered:
- The embodied energy in the steel material, which is the energetic cost associated with the mining of new material to produce the steel and/or the recycling of pre-existing metal scrap.
- The creation of the raw product. This term accounts for the manufacturing of the metal bar which is later used to fabricate the valves components from traditional machining. On the other hand, in the AM values chain, the energy required to produce the steel powder is considered.
- The manufacturing of the finished components, consisting in the CNC machining for the conventional parts, while printing and finishing for the AM ones.
- The utilization, a relative contribution based on the weight reduction of the printed parts installed on the FPSO vessel.
- The transportation and logistics, due to the different supply chain models adopted in the conventional and AM approaches.
The project team have studied three scenarios for this last consideration (transport and logistics).
In Scenario 1 dedicated to a conventional manufacturing process, they took into account the fact that the production of the steel billets occurs in major countries located in the South East Asia area, such as India or China while the CNC machining place is performed in Singapore.
Two other scenarios have been explored for AM: one (Scenario 2) where the powder is atomized in Germany from the recycling of metal scrap from Europe –and later used in Singapore for the AM production of the part and another one (Scenario 3) where the powder is atomized closed to Singapore (again, in Indonesia or Malaysia) from local scrap, and 3D printed in Singapore.
Calculations have been carried out taking reference data for each specific process (i.e., energy consumption values in MJ/kg). When possible, real data have been used instead, starting from the atomization of powder carried out by f3nice in 2021, one reads. The final results have been shared through various tables:
Energy Consumption (MJ/unit) | |||
Scenario 1
Conventional manufacturing |
Scenario 2
AM from Europe |
Scenario 3
AM in Singapore |
|
Embodied energy | 874 | 95 | 95 |
Raw product | 266 | 80 | 80 |
Manufacturing | 93 | 867 | 867 |
Utilization | 0 | -116 | -116 |
Logistics | 15 | 18 | 2 |
TOTAL | 1248 | 945 | 928 |
The project team could achieve these results thanks to the 100% recycled content in the f3nice powder. The energy savings are in the order of 24% – 26% compared to the conventional supply chain. Despite the significant contribution coming from the manufacturing phase (i.e., printing) in the AM scenarios, the use of scrap material guarantees a better LCA. At the same time, the reduction of the total weight of the parts by AM also decreases the raw product costs (less metal to be treated). Finally, the reduction of weight contributes beneficially also in the utilization phase, since the present analysis relates to components that will be transported all along their lifetime, the team noted.
The results of the energy consumption in each scenario have also helped to estimate each of their carbon footprint. With the goal of making calculations easier, the standard energy mixes of the aforementioned countries have been considered as input parameters here.
Carbon emissions [kgCO2eq/unit] | |||
Scenario 1
Conventional manufacturing |
Scenario 2
AM from Europe |
Scenario 3
AM in Singapore |
|
Embodied energy | 64,6 | 3,4 | 4,9 |
Raw product | 19,6 | 2,8 | 4,1 |
Manufacturing | 4,8 | 44,8 | 44,8 |
Utilization | 0 | -8,2 | -8,2 |
Logistics | 1,1 | 1,3 | 0,1 |
TOTAL | 90,1 | 44,1 | 45,7 |
Results for the carbon emissions are even more positive than what was previously observed for the energy consumptions. The total carbon emissions per unit are nearly half of what was calculated for the conventional supply chain. AM savings range between 51% and 49% for the powder produced in Europe or locally in Singapore, respectively. The increment in savings depends on the carbon intensity (i.e., the energy mix) of the countries considered in the calculations. As for the creation of the raw product in the conventional supply chain, the carbon intensity of India or China dramatically worsens the total carbon footprint of Scenario 1. On the other hand, the average carbon intensities of Europe (e.g., Germany or Italy) and Singapore offer a beneficial contribution to carbon emissions calculations, further increasing the gap between the conventional and the AM supply chains, the report details.
At the end of the day, despite their encouraging outcome, these scenarios are not (really yet) applied in real life – at least the part regarding the use of AM and recycled metal to produce valve components. One of the very first step that will encourage organizations to follow the AM scenarios and benefit from the triple bottom line advantages might be to foster the adoption of sustainable feedstocks produced from waste material or end-of-life components. For Valland’s E&D Engineer, another area of interest would be the “energy and consumables consumption efficiency of AM technologies”. By focusing on this area, the environmental impact related to the components building process would be significantly reduced.
Furthermore, while AM technology providers would need to continually work on the optimization of their processes, exploring the replacement of valve components using AM and 3D printable recycled metal powder could be a win-win for both the end-user and materials producer’ business. The role of “AM feedstocks suppliers (…) will become increasingly relevant considering the issues of critical raw material availability which the world economy will progressively have to face”, Giorgini explains.
Agility and Change
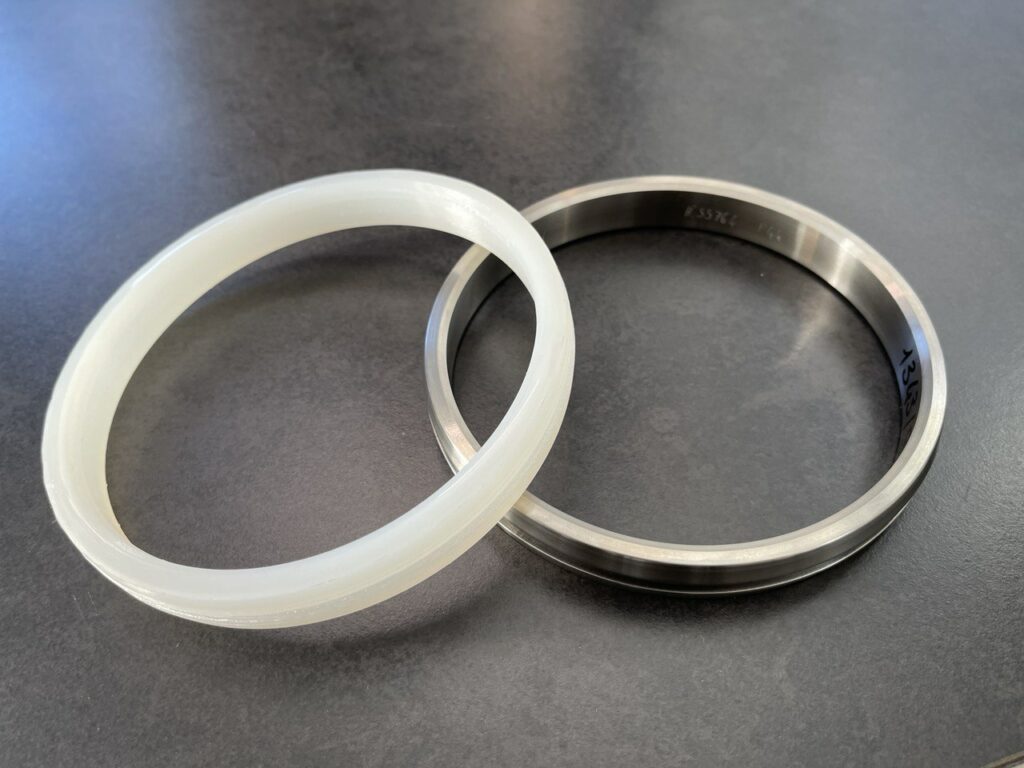
While the growing sustainability considerations affect valve design and manufacturing, it’s important to keep in mind that not every sustainability action needs to be complicated and huge. Sometimes, lifesaving solutions may come down to the use of agile manufacturing which involved automation and digitalization tools, AM, and recycled 3D printable metallic powder. It’s too soon to say where this niche industry is headed, but the timing is right to tell organizations they should plan for change in their manufacturing process in order to stay competitive. That’s in any case what companies like Valland do by helping target industries to navigate this new era of manufacturing valves with sustainability in mind.
This article was initially published in the 2022 September/October edition of 3D ADEPT Mag.
Remember, you can post job opportunities in the AM Industry on 3D ADEPT Media for free or look for a job via our job board. Make sure to follow us on our social networks and subscribe to our weekly newsletter: Facebook, Twitter, LinkedIn & Instagram ! If you want to be featured in the next issue of our digital magazine or if you hear a story that needs to be heard, make sure you send it to contact@3dadept.com