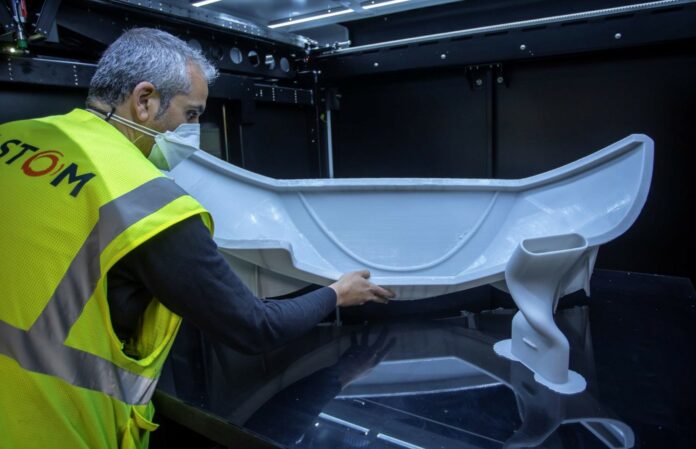
Alstom, the French rolling stock manufacturer operating in rail transport markets, continues to build expertise in AM and by doing so, the company contributes to positioning AM as a key technology process in the transportation industry.
If the team prides itself on having produced 150 000 3D printed parts today, nothing would have predicted this milestone given their humble beginnings. The company started its journey in 2016 in a startup mode, with just Aurelien Fussel. Fussel is head of Alstom’s additive manufacturing industrial program today and through his leadership succeeded in making AM a core technology tool within the company.
Today, the company owns various 3D printing hubs across several regions: in Saint Bruno, Canada; Barcelona, Spain; Sesto San Giovanni, Italy; Bangalore, India; Valenciennes and Tarbes in France; Hennigsdorf and Salzgitter in Germany; Istanbul, Türkiye; and Singapore. With about 150 machines and one supplier minimum per region, the manufacturer can print a few parts in-house and relies on contract manufacturers for the production of thousands of parts.
Through various projects, we’ve learned how Alstom has been able to save millions of euros and lead times using the right AM processes. Time, experience and knowledge led the team to leverage AM for the production of machine tools and jigs, spare parts, missing parts, and new designs.
“We can print three types of materials: polymers, ceramics and metal. We have about 20 validated polymers (including fire and smoke compliant ones – EN45545 for Europe and NFPA130 for North America) and four metals: aluminium, stainless steel, high-performance steel and titanium. The range of parts is impressive: for example, we’ve just produced a headlamp case for a new high-speed train in France, a jig to ease screwing holes in carbody shells in Germany, a part in a soft material for an air conditioning evacuation tube for a metro project in Spain, and a steel cover for a bogie in the Nordics,” Aurelien Fussel, states.
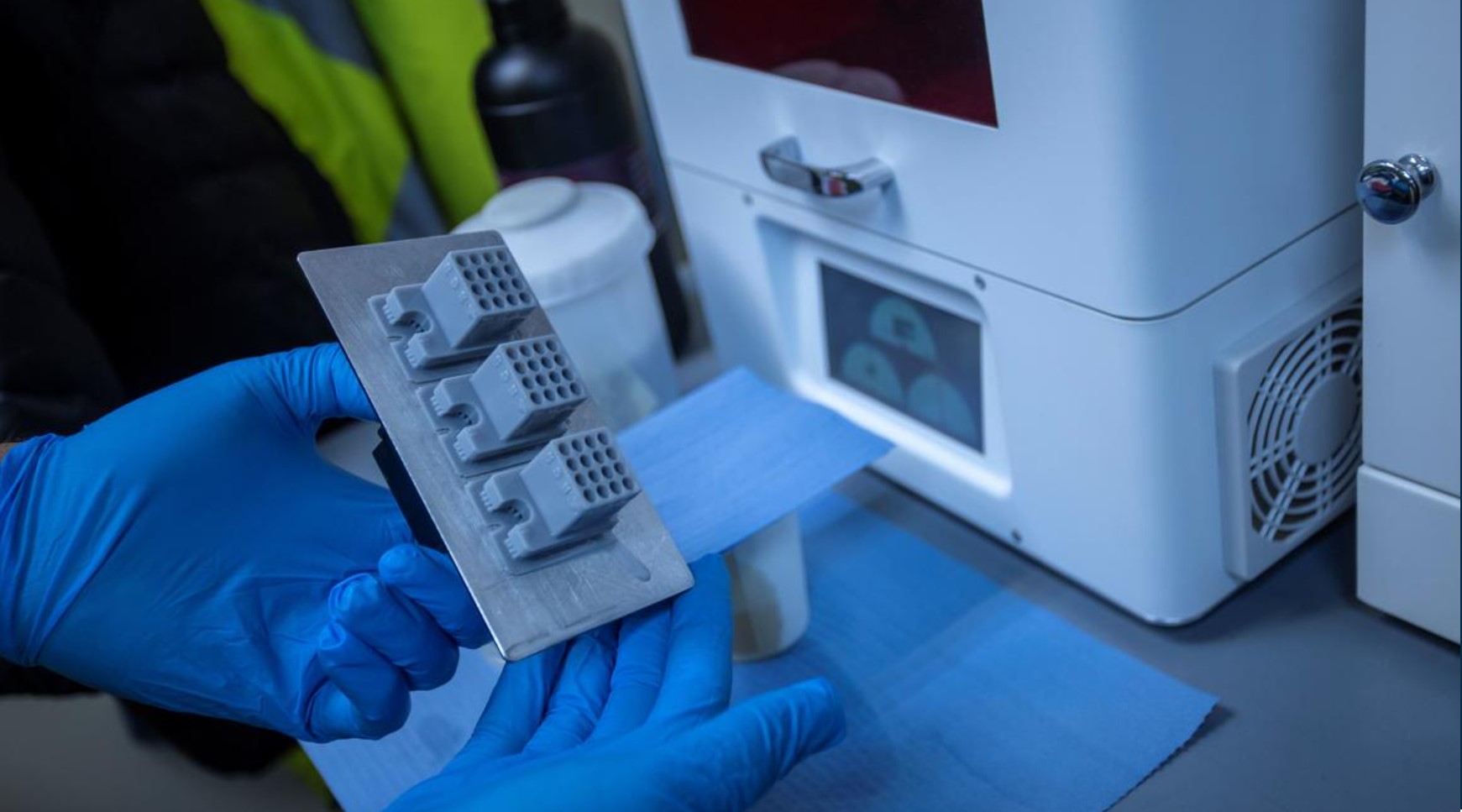
The next steps?
At the technology level, the AM team at Alstom monitors the technology evolution in the market and plans to explore the capabilities of robotics solutions with AM.
As for its business model, with new business cases that show the technology’s value in digital warehousing, we can expect the company to explore this avenue.
“With 20% of the parts in a train now printable, operators are moving faster than ever to adopt this technology. The world of tomorrow will be more data-centric. We can send digital files of parts around the world and print parts as close as possible to the customer. This contrasts with today, where we might buy raw material in the Far East, manufacture in Europe and sell, say, a carbody shell to North America. With digital printing, we eliminate customs taxes, massively reduce lead times and fulfil local manufacturing contract needs,” Fussel concludes.
Remember, you can post job opportunities in the AM Industry on 3D ADEPT Media free of charge or look for a job via our job board. Make sure to follow us on our social networks and subscribe to our weekly newsletter : Facebook, Twitter, LinkedIn & Instagram ! If you want to be featured in the next issue of our digital magazine or if you hear a story that needs to be heard, make sure you send it to contact@3dadept.com