Admatec introduces medical grade ceramic materials that will be processed on its Admaflex 3D Printing systems. The Hydroxyapatite slurry printing material is supplied by CAM bioceramics, an ISO 13485:2016 certified supplier of medical materials.
Admatec already provides academic medical centers and manufacturers of medical devices with customized solutions throughout the entire process chain of the additive manufacturing of biocompatible and bioresorbable ceramics. With this launch, the Dutch manufacturer of ceramic 3D printers aims to open up new applications for the medical and dental sectors.
“As a supplier for the Orthopaedic and Dental market, CAM Bioceramics acknowledges that 3D Printing will play an increasingly significant role in numerous patient treatment plans. Calcium Phosphate based bone reconstructions will play an important part in this next generation medical device solutions due to its proven biocompatibility. As one of the market leaders in this area, CAM Bioceramics actively partners with 3D print experts and promotes the evolution of 3D printed solutions”, states C. Hogeboom, CEO of CAM Bioceramics.
The use of ceramic 3D printing in medical applications
Ceramic 3D printing is increasingly leveraged in the medical industry. A few applications we have been able to identify include the manufacturing of a 3D printed ceramic cryotherapy probe to prevent breast cancer or the production of vaccines.
As far as biocompatible and bioresorbable ceramics are concerned, it is possible to leverage them to produce patient-specific implants in cranio-maxillofacial and hemi-maxillary operations. These implants will be reabsorbed by the body and will be replaced by native bone tissue, meaning that the implant does not need to be removed once the healing process is finished, eliminating the need for otherwise necessary removal of autologous bone, which is often associated with severe pain and complications. In comparison to tricalcium phosphate, hydroxyapatite takes far more time to be absorbed into the body, therefore giving the body more time to heal.
“Using Hydroxyapatite, we can manufacture patient-specific, bioresorbable implants, which have defined pore structures and geometries. Combinations of functional graded ceramic materials, such as dense and porous structures in a single hemi-maxillary bone-like structure, have been printed successfully with help of the lithography based additive manufacturing technology provided by Admatec”, explains the manufacturer.
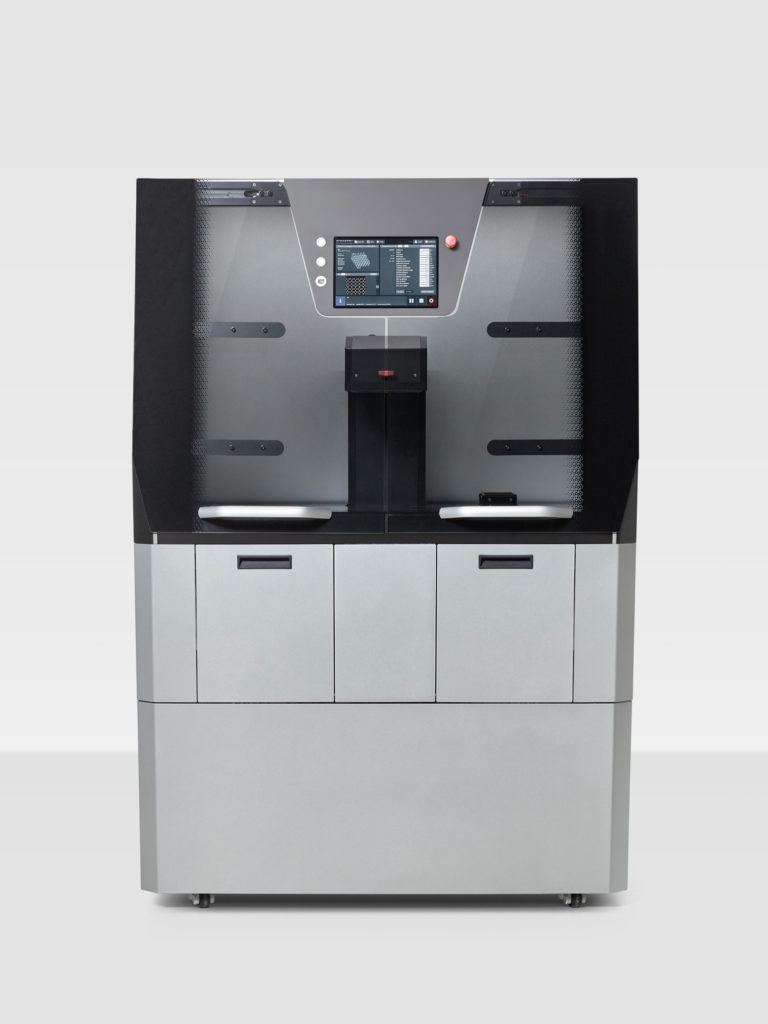
In the future, the Dutch company plans to determine how to combine several materials to achieve medical applications.
For instance, in combination implants for the lower jaw, medical specialists tend to combine Hydroxyapatite and Zirconia. In case of large bone defect due to a severe trauma or bone tumor, the bone itself is not able to heal the defect without appropriate measures. A possible solution is a cage made of high-strength zirconia or other high strength ceramic, which gives support during the healing phase. The inner volume of the implant could be made of bioresorbable ceramic such as hydroxyapatite. The zirconia cage can be left in place due to its outstanding biocompatibility. The hydroxyapatite can be resorbed into the cells and replaced by newly formed bone. That’s why, combining design freedom and the ability to use multiple ceramic materials in DLP 3D printing leads to many new applications for permanent implants.
Remember, you can post free of charge job opportunities in the AM Industry on 3D ADEPT Media or look for a job via our job board. Make sure to follow us on our social networks and subscribe to our weekly newsletter : Facebook, Twitter, LinkedIn & Instagram ! If you want to be featured in the next issue of our digital magazine or if you hear a story that needs to be heard, make sure to send it to contact@3dadept.com