Whether one deals with full-body wearable suits or an appendage, exoskeletons aim to strengthen or improve human motilities and abilities. Their biggest advantages lie in their ability to protect and support internal components.
To date, there are different types of exoskeletons and each of them comes with its share of challenges. If their manufacturing process does not meet certain expectations, they can result in an unexpected reduction of human flexibility leading to new sources of musculoskeletal disorders (MSD) and accidents. Furthermore, depending on what led someone to wear such a device, exoskeletons may often represent a psychological burden for the patient due to their aesthetic and functional impairment – let alone the cost of the final device.
All these pain points can be addressed using advanced manufacturing technologies. The basic questions are: What? Why? How? Beyond these questions, there is a need to understand how to shorten a manufacturing process that is still described as lengthy and full of complexities.
The next Additive Talks session ambitions to discuss the challenges in the manufacturing and the performance for structural articulated parts in exoskeletons and/or humanoid robots. It will also address the advanced manufacturing opportunities that may serve these applications as well as limitations that still need to be addressed in this industry. Entitled “Is AM an untapped potential for exoskeleton applications”, the virtual panel will take place on Wednesday 28th June, from 03.30 pm to 04.30 pm CET (09.30 am – 10.30 am New York Time, USA).
Around this table, you will find:
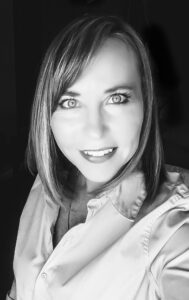
Diana Hall, Founder & CEO at ActivArmorTM. With a degree in Chemical Engineering, Hall worked in Fortune 500 companies in software and engineering. She founded 3D printed biomedical company, ActivArmor, in 2016 and currently holds several patents on 3D-printed exoskeletons.
ActivArmor is the market leader in patient-specific, custom-fitted casts and splints in waterproof, sanitizable plastics, that allow people to live their active lifestyles while healing. ActivArmor’s market-proven products are now available in the first point-of-care digital custom casting/splinting fabrication system that utilizes the latest 3D scanning and printing technologies to empower medical providers with a next-gen casting option that reduces complications and gives their patients the ability to practice essential hygiene during treatment.
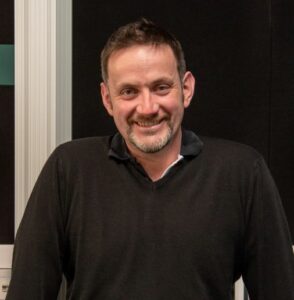
Dr Matthew Dickinson, Senior Lecturer in Biomechatronics, University of Central Lancashire, heads up the new wearable robotics unit, implementing the developments made by the Additive Manufacturing Lab to provide assistive wearable systems. Dr Dickinson’s research interests are aimed at the use of intelligent machines to aid in the recovery and mobility of patents to offer an improved quality of life through the use of the human body as a “controller” during functional movements. Dr Dickinson’s research aims introduce a new approach to the conventional method of exo-skeleton design mimicking the neuromuscular and musculoskeletal systems using low cost solutions. The investigation into the development of low cost exoskeleton technology offers a huge potential to aid in the assistance of movement disorders and rehabilitation of adults and children to all income families throughout the world. He also serves as an executive member on the ASTM F48 committee for exoskeletons and exosuits where we work with international representatives on the development of standards for safety in the development of exoskeletons.
Eager to join them?