If you want to manufacture parts that measure up to 30 meters in a single printing operation; if you want this production to be automated and accurately repeated, there is a great chance that robotic 3D printing is your ideal production candidate. On paper, such a combination of robotics and 3D printing is what most industries picture as the ideal move towards smart manufacturing. In practice, there are some hidden constraints that prevent a large adoption of this form of manufacturing.
When talking about robotic 3D printing, it might be easy to get carried away by robotic solutions that are increasingly being developed across industries to support or replace human tasks. Please, note that this article is in no way related to that. However, if you are looking to learn more about the combination of robotics and 3D printing used in the manufacturing of parts, then stay with us.
Robotics and 3D printing can be combined in two main ways.
One of the most widely used techniques consists in combining a 3D printer head that extrudes materials with a multi-axis robotic arm. This technique provides a level of freedom that “conventional 3D printers” do not usually provide. This is often the most widely used technique as it is directly linked to manufacturing per se. This form of manufacturing – which constitutes the focus of this article – is referred to as Robotic arm 3D printing, robotic additive manufacturing (or simply “RAM”) and can be integrated into different types of AM technologies (FDM, metals, ceramics, concrete, etc.). Confusion should not be made with a gantry system for 3D printing. (A gantry system moves in three axes whereas a robotic arm moves in six axes).
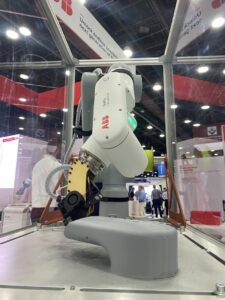
“There are many different types of end-of-arm tooling for robots for a 3D printing application. [They] range from thermoplastic, metal injection molding, ceramic to concrete systems [and more]. [They can be] optimized and built specifically for additive and robotic printing applications,” Tyler McNaney, Founder and Managing Director at Massive Dimension explains.
“Robots are very customizable and versatile. A single robot could be placed on a static pedestal and the print might move, or the robot could be made movable and the part is stationary. Both of these could change the DFAM, depending on the process. Let’s take for instance the buckling that can happen when printing a large part vertically: it may be necessary to create buckling mitigating features on the part. If the part has the ability to be printed on its side or upside down, then the physics of gravity on the part may impact the need for, or design of, these features.
Furthermore, robots can very easily be configured with multiple end effectors, thus it is very easy to repurpose a robot. This means someone who starts with a wire arc end effector can keep the same robot and change to a laser powder process. Imagine doing that with a powder-bed machine!
This also allows us to look toward multiple dissimilar materials being printed on one cell, like a plastic or elastomer on a metal – things that might normally be done with a plastic injection process.
Robots are not as precise as what we’ve come to see as the standard for AM, powder bed machines or SLA machines. Recognizing this inaccuracy at the design level, and that post-print processing will be required, is necessary,” Justin Ferguson, Autodesk, Senior Solutions Engineer adds.
On another note, 3D printing and robotics can also complete each other when one is looking to establish an integrated solution throughout the manufacturing process. In such cases, an industrial robot could replace a manual step of the manufacturing process. It could be replacing a 3D printer’s build plate or performing the washing, curing and final finishing steps in post-processing with robotic arms.
“A robotic additive printing solution is very flexible in terms of customization; the initial printing setup can be customized beyond what it was originally designed to produce. For example, a robotic printer could have one work volume on a fixed surface, in another location, a rotary positioner could be added, and furthermore, additional build areas can be installed for specific part build requirements. Within the printing process various deposition tools can be added to the end of the robotic arm, as well as post-processing tools such as mills, sanders, or other finishing tools,” McNaney outlines.
A double-edged sword
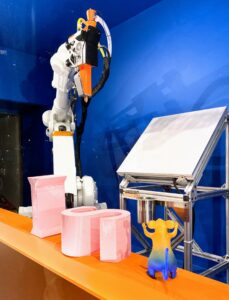
As mentioned above, the need to manufacture large-scale parts is often the first argument that plays to the strengths of RAM. RAM also amplifies the freedom of creating complex shapes that AM already enables. The reason for this is quite simple: with their articulated joints, robotic arms can easily move along and around multiple axes. In the same vein, a robotic print bed that can rotate also gives room for more freedom. This enables the manufacturing of parts without support structures and a reduction in materials usage. Those support structures can even be completely avoided when the build platform moves, enabling this way the model to be reoriented.
Here is the thing, these advantages can be a double-edged sword as with so many moving parts, the machine would need detailed computer instructions to meet the manufacturing requirements. Indeed, improper planning and control can influence the printing quality or can lead to the arm hitting the printed part, causing damage. Not to mention that the robot’s motion control systems can also influence the part quality or effectiveness of the printing process.
“Where a conventional XYZ printer can only build up, a robotic movement system can reach down after building an object; robot system can be quickly adapted for a range of printing methods such as non-planar, multiplanar, and angled printing,” McNaney points out before warning on the design considerations that should be taken into account: “features should be designed within the nozzle diameter size and should not exceed the capabilities of the printer or materials just as like desktop printing.”
To date, there are no recognized standards for the transfer of information between the CAD system and the arm, which leads many machine manufacturers to create their own workflow to simplify the manufacturing process with a robotic programming software solution.
That said, one will never emphasize enough the importance of the 3D software solution used as part of the manufacturing process. The movement of the robotic arm and therefore the distribution of the material depends on this software solution. The ideal 3D software should be able to accurately model the developing part as it is built, to ensure that the robotic arm does not collide with the build as it grows and to prevent potential shrinkage issues that may occur during the printing process.
Applications and current market
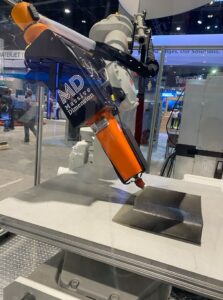
Boats, car bumpers, large molds, fixtures, and any object in the rotomolding industry can be produced with robotic 3D printing.
From the technology standpoint, the market isn’t exactly overflowing with hundreds of 3D printer manufacturers, given the specialized nature of robot-assisted 3D printing. The robotic AM market features an exhaustive list of companies that provide robotic 3D printing software, end-of-arm printheads and extruders, robotic arms and robotic 3D printers.
The table below provides a few names that you may find in this market – it does not take into account companies that provide robotic 3D printing services:
Robotic 3D printing software | End-of-arm printheads and extruders | Robotic arms | Robotic 3D printers |
ADAXIS | Weber Additive | Comau | CEAD AM Flexbot |
AiBuild | Massive Dimension | ABB | MX3D M1 |
Robotmaster | Dyze Design | Stäubli | Caracol |
Octopuz OLRP | Rev3rd | KUKA | Continuous Composites |
RoboDK | Bloom Robotics | Vertico (for concrete) | Orbital Composites |
Twente AM (for concrete) | |||
Hyperion Robotics (for the construction industry) |
On a commercial standpoint, leveraging an in-house robotic 3D printing solution requires a strong business case. Indeed, in addition to the related equipment that a standard AM process may require, a customized robotic 3D printing solution may require a robotic arm, a robotic 3D printing software solution if it is not already integrated into the printing solution, and the printhead. Most of the times, these solutions do not always come from the same provider and this makes the overall cost of investment quite expensive.
This raises some complexities with the integration of certain platforms and the adoption of robotic 3D printing solutions at scale – all of which can be addressed through collaborations between the main technology providers.
This article has first been published in the May/June edition of 3D ADEPT MAG.