Cela fait une décennie que l’impression 3D de bois existe. Pourtant, il a fallu le lancement de Forust™, la filiale de Desktop Metal dédiée aux pièces en bois à usage final, pour s’interroger sur l’avenir de ce matériau dans cette industrie. Forust™ affirme que sa technologie de « binder-jetting » permet d’obtenir de grands volumes de pièces en bois à usage final. Est-ce à cela que ressemblera l’industrialisation de l’impression 3D sur bois ?
Il y a dix ans, l’impression 3D de bois était assimilée à l’utilisation de filaments de bois avec une imprimante 3D FDM. Pour faire simple, du bois neuf ou usagé était réduit en poudre fine, puis mélangé à des liants tels que le silicate de sodium, le ciment, la cellulose, le gypse, les plastiques et les adhésifs pour créer un filament. Au fil des ans, les chercheurs qui s’intéressaient à ce matériau ont proposé de nouvelles solutions qui pouvaient être utilisées avec d’autres technologies et, parfois, qui permettaient une production respectueuse de l’environnement, sans abattre d’arbres.
Types de matériaux en bois
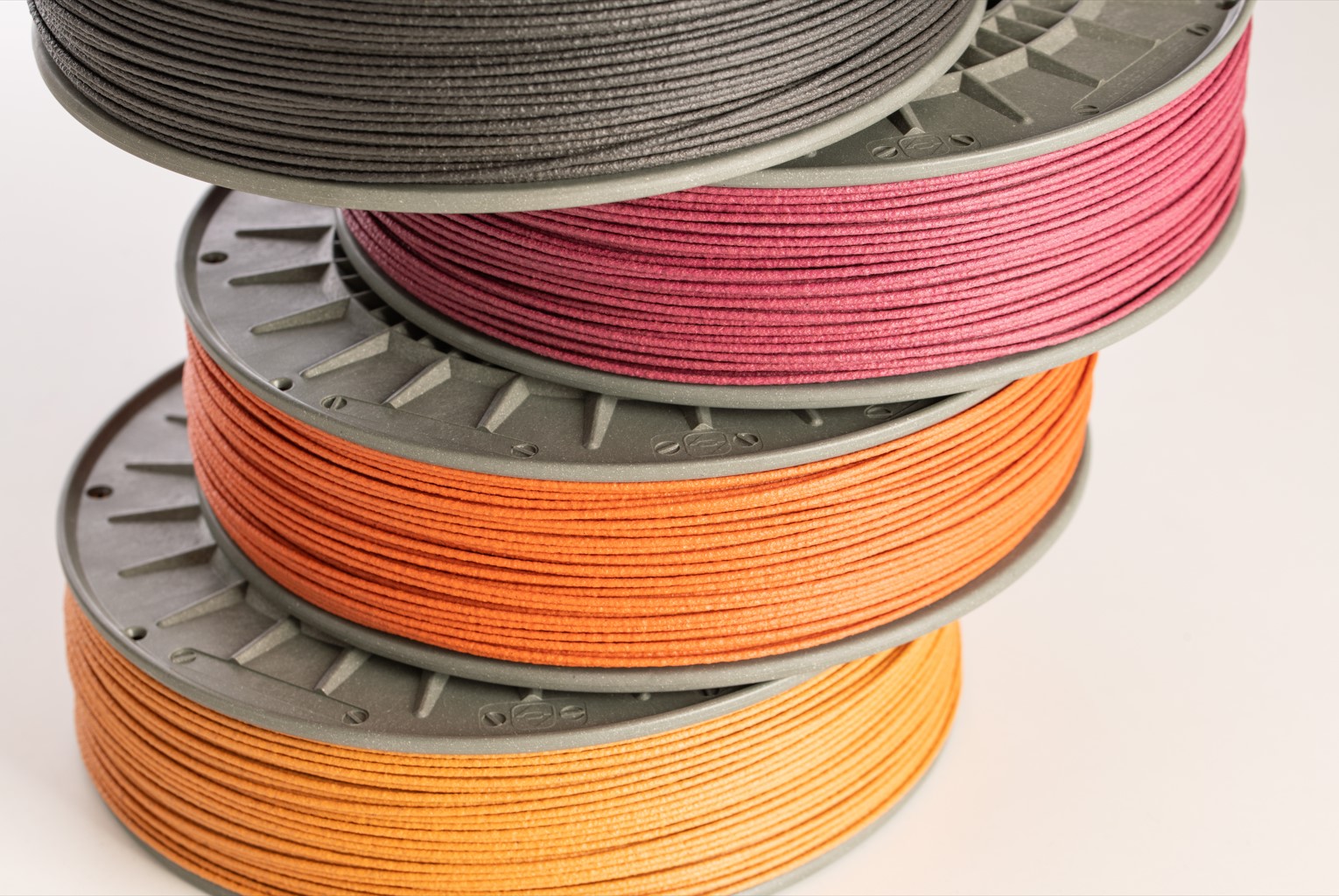
Comme indiqué plus haut, outre l’impression 3D FDM qui traite le filament de bois, le bois peut également être traité par jet de liant. Dans le cas de Forust™ par exemple, le processus est basé sur une technologie de FA brevetée de jet de liant en un seul passage qui valorise les sous-produits de la fabrication du bois (poussière de cellulose) et de l’industrie du papier (lignine) et re-matérialise des pièces de bois fonctionnelles grâce à l’impression 3D à grande vitesse, y compris le grain numérique dans toute la pièce. Le matériau est ensuite traité par l’imprimante 3D sous forme de poudre.
Outre la poudre, le bois peut également être disponible sous forme de granulés. Industry SE, un fabricant de machines basé en Suède, utilise ce type de matériau pour ses imprimantes 3D. Jonas Carlsson, CEO de l’entreprise, explique que ce processus est intéressant à la fois en termes de « coûts des matériaux et d’efficacité d’impression« . « Nous travaillons principalement avec Stora Enso, l’une des plus grandes entreprises forestières de Suède. Ils ont développé un matériau appelé Durasens 50 et 30. Le Durasense 50 contient 50 % de poussière de scierie et le Durasense 30 en contient 30 %. Stora Enso dispose d’une imprimante 3D MAGNUM dans ses locaux de Hyltebruk, en Suède. L’entreprise a utilisé notre machine pour développer le matériau, mais aussi pour la production dans le cadre de son concept OneLoop. [Une chaise de bar peut être imprimée en moins de 2,5 heures, par exemple.] Il est possible de réutiliser ce matériau jusqu’à 20 fois. Lorsque le produit imprimé en 3D a atteint sa fin de vie, il suffit de le déchiqueter en granulés et de l’imprimer à nouveau en MAGNUM », il ajoute.
Par ailleurs, en Israël, une autre équipe de scientifiques développe le bois sous sa forme liquide pour l’impression 3D. Shany Barath, du Disrupt.Design Lab (D.DLab), a expliqué à 3D ADEPT que « certains matériaux ont été développés au sein du Disrupt. Design Lab (D.DLab) à l’Institut israélien de technologie du Technion. Ce processus de développement implique une exploration itérative axée sur la conception et visant à créer une pâte de bois imprimable. En outre, les efforts de collaboration s’étendent à des partenaires industriels tels que Daika Wood, ce qui implique l’expérimentation de leurs matériaux à base de déchets. Le matériau arrive sous forme de poudre et, grâce à des expériences avec différents ratios de formulation, nous définissons la pâte adaptée à nos besoins d’impression. En utilisant des liants naturels, la sciure de bois dérivée des déchets industriels peut être efficacement réutilisée pour des applications d’impression 3D. La technique d’impression employée repose sur les principes du matériau à dépôt liquide (LDM = Liquid Deposition Material), un choix justifié par les propriétés inhérentes du matériau, qui s’apparentent aux procédures utilisées pour l’impression de matériaux à base d’argile. »
Une autre approche de l’impression 3D du bois qui mérite d’être mentionnée est celle d’Ashley Beckwith, une ancien étudiante du MIT qui a fondé FORAY bioscience pour développer de nouvelles méthodes de culture du bois sans couper d’arbres. Leur technique fait appel à l’ingénierie tissulaire pour produire de la matière végétale en laboratoire. Jusqu’à présent, les scientifiques n’ont utilisé cette méthode que pour la culture de cellules animales.
« Des concepts analogues n’ont pas été transposés à l’espace de culture des plantes, en particulier en ce qui concerne la production de matériaux. Ce travail représente donc un premier regard sur une approche d’agriculture cellulaire pour la génération de matériaux végétaux », notent les chercheurs dans leur étude. Dans le but de réduire considérablement la déforestation, la prochaine étape pour cette équipe est d’imprimer du bois en 3D en laboratoire à partir de cellules d’arbres comme le pin.
Applications : L’industrialisation est-elle possible ?
Si la plupart de ces solutions d’impression 3D du bois ont déjà produit des prototypes viables, il convient de noter qu’elles ne ciblent pas toujours la même industrie verticale.
Avec l’impression 3D FDM et la projection de liant, certaines des applications intéressantes qui ont déjà été partagées publiquement ont été réalisées pour l’industrie des biens de consommation.
Impression 3D FDM
Le producteur de matériaux Fillamentum, par exemple, propose Timberfill, un matériau composé de fibres de bois, en particulier de fibres d’épicéa. « Le matériau composite Timberfill est spécialement conçu pour les besoins de l’impression 3D, notamment pour la technologie FDM/FFF, de sorte que la longueur des fibres a dû être prise en compte. Timberfill a été mis au point en mélangeant des biopolyesters à base de PLA et des fibres de bois d’épicéa. Le processus de développement consiste à mélanger des biopolyesters et des fibres de bois dans le rapport souhaité, généralement 15 % de fibres de bois et 85 % de PLA. Les objets imprimés ont un aspect authentique et une odeur temporaire de bois. Nous proposons actuellement 8 nuances de couleurs et en préparons d’autres. Grâce à l’origine biosourcée du matériau, il est 100% biodégradable par compostage industriel » explique Barbora Jurčová, responsable de la recherche et du développement.
En ce qui concerne les applications, le matériau peut être utilisé pour développer des enceintes imprimées en 3D comme celle développée dans le cadre du projet Spirula en coopération avec Akemake.
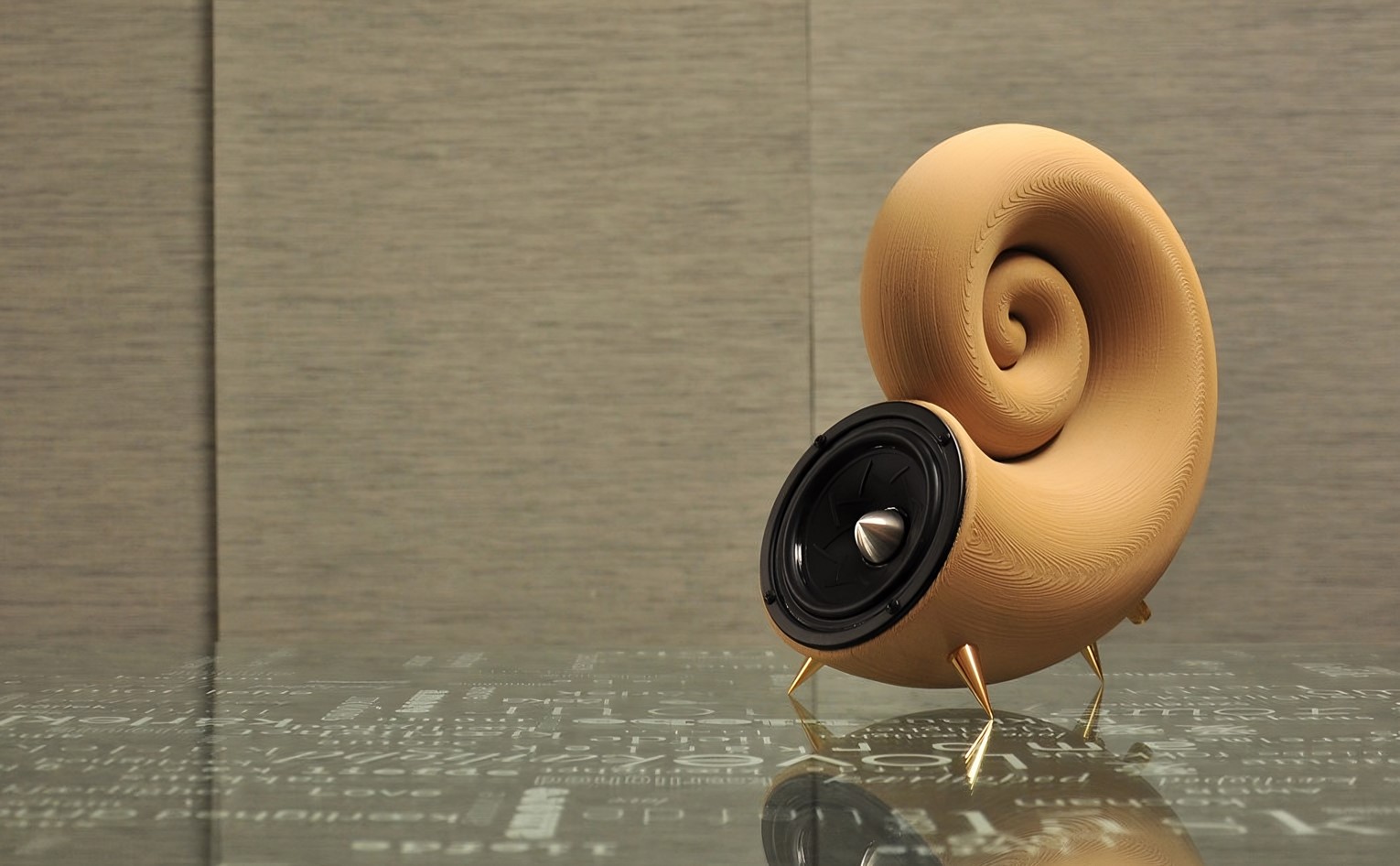
Au niveau de la fabrication, l’utilisation du matériau Timberfill dans le processus d’impression 3D nécessite des considérations spécifiques pour obtenir des résultats optimaux. Selon Jurčová, comme le matériau contient des fibres de bois, il peut influencer l’imprimabilité et provoquer une usure accrue des buses. Pour atténuer ce phénomène, il est conseillé aux utilisateurs d’employer une buse durcie spécialement conçue et adaptée aux fibres composites. En outre, il est recommandé d’utiliser une buse d’un diamètre minimum de 0,5 mm. Il est essentiel de sécher correctement le matériau avant l’impression afin d’éviter la dégradation du matériau, le filage et une mauvaise adhérence des couches. Comme pour tout filament, le réglage précis des paramètres d’impression, notamment la température, la hauteur de couche et la vitesse d’impression, joue un rôle essentiel dans l’obtention d’impressions de haute qualité.
D’autres applications concernent toutes sortes d’objets décoratifs, de sculptures artistiques, de modèles de meubles, de cadeaux personnalisés et même de pièces fonctionnelles ayant l’apparence du bois. La polyvalence de l’impression 3D à partir de filaments de fibres de bois ouvre des perspectives dans de nombreux secteurs, en particulier le design, l’art et le prototypage.
En ce qui concerne l’industrialisation, il convient de noter que plusieurs facteurs peuvent limiter le développement des filaments à base de fibres de bois. « Les propriétés mécaniques sont limitées (principalement la fragilité) par rapport aux matériaux traditionnels tels que les métaux ou les plastiques.
En outre, c’est la résistance à basse température du matériau qui est due au polymère utilisé. Pour certains utilisateurs, la nécessité de sécher le filament avant de l’utiliser, ainsi que l’utilisation d’une buse de plus grand diamètre, peuvent être contraignantes. Enfin, le prix est plus élevé que celui des filaments PLA ou ABS standard », souligne Mme Jurčová.
Le matériau Timberfill est aujourd’hui disponible en 8 couleurs, ce qui permet d’obtenir « une surface en bois à l’aspect authentique« . Selon l’entreprise, le potentiel de l’impression 3D robotisée ouvre la voie à la fabrication d’objets à grande échelle, ce qui plaide en faveur de son adoption par l’industrie.
Impression 3D de granulés
Si le segment grand public présente un grand potentiel, la combinaison des granulés de bois et de l’impression 3D a déjà donné lieu à des applications intéressantes dans le domaine de l’architecture.
L’utilisation actuelle de la technologie pour des applications ponctuelles telles que des objets décoratifs ou des sculptures artistiques ne permet pas d’envisager un projet d’industrialisation.
Impression 3D de bois avec des matériaux à dépôt liquide (Liquid Deposition Material)
Le projet WoodenWood de D.DLab est le seul que nous ayons vu jusqu’à présent, qui explore l’utilisation du bois comme pâte. Dans le but de développer des solutions circulaires pour les produits et les processus du bois, Barath explique qu’ils incorporent des expressions modulaires traditionnelles de travail du bois avec l’impression robotisée de pâte de bois pour le prototypage d’éléments de sièges.
Le parcours d’impression crée un nouveau « textile de bois » ressemblant à une texture de rotin tout en utilisant un matériau de qualité inférieure, la sciure de bois. La structure en bois brut sert de moule pour le processus d’impression, ce qui évite de produire des déchets supplémentaires sous forme de sous-produits. Ensemble, les conceptions traditionnelles et numériques présentent une expression circulaire pour les déchets de bois vers une nouvelle fin de vie. Notre objectif premier était de créer un prototype d’étude de cas qui pourrait être étendu à un large éventail d’applications utilisant des déchets naturels et des matériaux dégradables dans le processus de fabrication. Le projet WoodenWood sert de démonstrateur de cette plateforme, dont les applications potentielles s’étendent de la construction et de l’architecture à la mode et à la conception de divers produits, Barath explique.
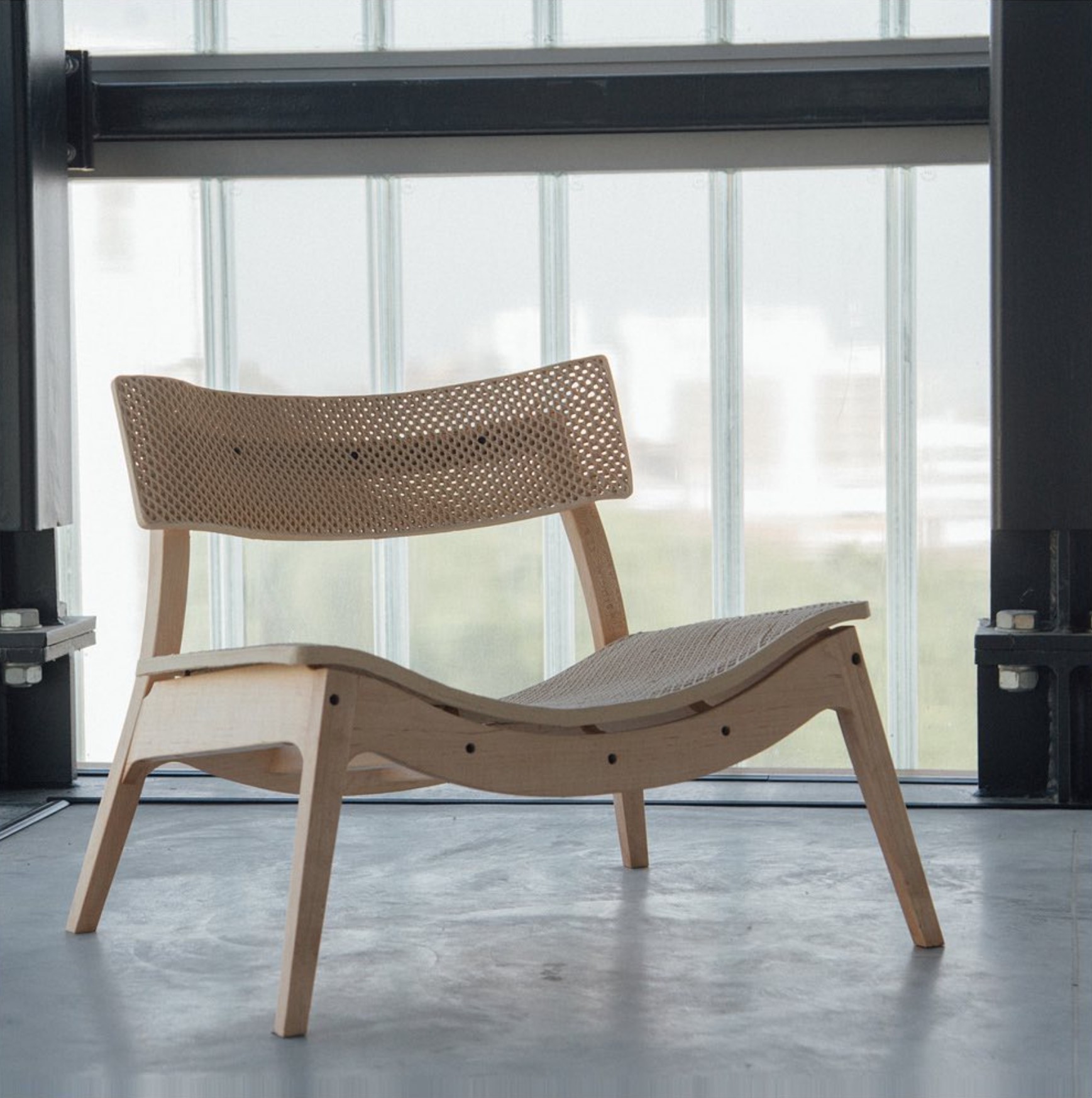
Au niveau de la fabrication, la formulation du matériau est adaptée aux imprimantes LDM (telles que les imprimantes à pâte à modeler) qui sont basées sur la pression de l’air. Cependant, le flux de travail de la conception à la fabrication nécessite des connaissances en conception computationnelle et en techniques de trajectoire d’outils robotisés. En réalité, l’utilisation de matériaux naturels dans l’impression LDM nécessite l’établissement de protocoles spécifiques pour gérer efficacement le rétrécissement inhérent et les processus de séchage ultérieurs.
Ce qui pourrait ralentir l’adoption de cette technologie, ce sont les processus de fabrication. Les considérations telles que les surplombs, les ponts, les étouffements, le séchage, etc. deviennent plus importantes au fur et à mesure que l’échelle de l’impression augmente. Il est donc nécessaire d’ajuster la formule et le parcours de l’outil d’impression, ce qui requiert davantage de recherche et d’expérimentation. En outre, outre sa nature axée sur la conception, l’essai mécanique est essentiel pour évaluer les performances du processus à différentes échelles, souligne Barath.
Même s’il est trop tôt pour parler d’industrialisation, à long terme, ils cherchent à obtenir des applications adaptées à l’industrie de la construction.
Conclusion
L’impression 3D de bois est certainement attrayante, quel que soit le procédé de FA utilisé. Cependant, les types d’applications actuels qui peuvent être réalisés avec ces méthodes font qu’il est difficile d’envisager un modèle d’entreprise basé sur l’industrialisation pour les entreprises qui explorent ces techniques. Il faut espérer qu’avec l’amélioration de ces techniques, les utilisateurs seront plus confiants pour passer des prototypes et des petites séries à la production en série.
Ce dossier a été initialement publié dans le numéro de Juillet/Août de 3D ADEPT Mag.