It’s been a decade that wood 3D printing has been around. Yet, it takes the launch of Forust™, Desktop Metal’s subsidiary dedicated to end-use wood parts, to question the future of this material in this industry. Forust™ claims that their binder-jetting technology can achieve high-volume of end-use wood parts. Is that what industrialization of wood 3D printing will look like?
Ten years ago, wood 3D printing was assimilated to the use of wood filaments with an FDM 3D printer. Simply put, new or waste wood was milled to a fine powder, and thereafter mixed with binders such as sodium silicate, cement, cellulose, gypsum, plastics, and adhesives to create a filament. Over the years, researchers with an interest in this material came up with new material solutions that could be used with other technologies – and sometimes, that would allow for production in an environmental-friendly way, without cutting trees.
Type of wood materials
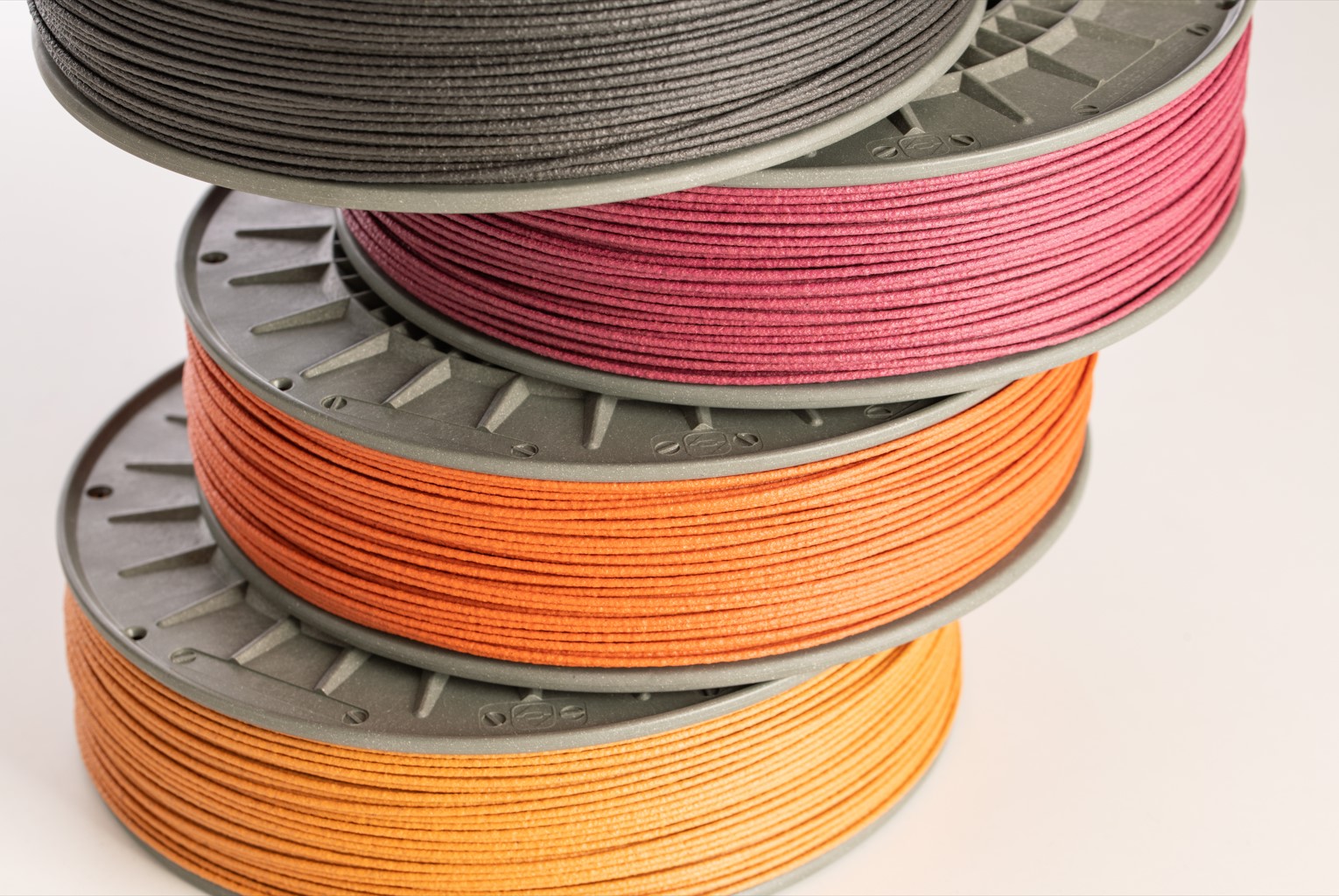
As said above, apart from FDM 3D printing that processes wood filament, wood can also be processed with binder jetting. In Forust™’ case for instance, the process is based on a patented single-pass binder jetting AM technology which upcycles waste byproducts from wood manufacturing (cellulose dust) and the paper industry (lignin) and re-materializes functional wood parts through high-speed 3D printing including digital grain throughout the part. The material is then processed by the 3D printer in the form of a powder.
In addition to powder, wood can also be available in the form of pellets. Industry SE, a machine manufacturer based in Sweden is utilizing this type of material for their 3D printers. Jonas Carlsson, the company’s CEO explains that this process is interesting both in terms of “material costs and print efficiency”. “We work mainly with Stora Enso, one of the largest forest- and wood companies in Sweden. They have developed a material called Durasens 50 and 30. The Durasense 50 contains 50 % of sawmill dust, and the Durasense 30 contains 30%. Stora Enso has a MAGNUM 3D printer installed at their facilities in Hyltebruk, Sweden. They have used our machine for developing the material, and also do production within their OneLoop concept. [A bar chair can be printed in less than 2.5 hours for example]. It is possible to reuse this material up till 20 times. After the 3D printed product has reached its end-of-life, you simply shred it into pellets again and print it in the MAGNUM again,” he adds.
Furthermore, in Israel, another team of scientists is developing wood in its liquid form for 3D printing. Shany Barath, Disrupt.Design Lab (D.DLab) told 3D ADEPT that “certain materials have been developed within the Disrupt. Design Lab (D.DLab) at the Technion Israel Institute of Technology. This development process involves design-led iterative exploration aimed at creating a printable wood paste. Additionally, collaborative efforts extend to industry partners like Daika Wood, involving experimentation with their waste-based materials. The material arrives as a powder, and through experiments with different formulation ratios, we define the suitable paste for our printing requirements. Utilizing natural binders, sawdust derived from industrial waste can be efficiently repurposed for applications in 3D printing. The employed printing technique hinges on the principles of Liquid Deposition Material (LDM), a choice substantiated by the inherent material properties, akin to the procedures utilized in printing clay-based materials.”
Another approach to wood 3D printing that is worth mentioning is the one of Ashley Beckwith, an ex-MIT student who founded FORAY bioscience to further develop new methods for growing wood without cutting trees. Their technique requires the use of tissue engineering for producing plant matter in a lab. So far, scientists have only used this method for animal cell culture.
“Analogous concepts have not been translated to the plant culture space, particularly with respect to the production of materials. This work thus represents a first look at a cellular agriculture approach to plant material generation,” the researchers note in their study. With the goal to drastically reduce deforestation, the next step for this team is to 3D print timber in a lab from cells of trees like pine.
Applications: Is industrialization possible?
While most of these wood 3D printing solutions have already produced viable prototypes, it should be noted they do not always target the same vertical industry.
With FDM 3D printing and binder jetting, some of the interesting applications that have already been publicly shared, have been made for the consumer goods industry.
FDM 3D Printing
Material producer Fillamentum for instance offers Timberfill, a material made up of wood fibers, specifically spruce fibers. “The composite material Timberfill is specifically designed for 3D printing needs, specifically for FDM/FFF technology, so the length of the fibers had to be taken into account. Timberfill was developed by mixing PLA-dominated biopolyesters and wood fibers obtained from spruce trees. The development process involves mixing biopolyesters and wood fibers in the desired ratio, typically 15% wood fibers and 85% PLA. The printed objects have an authentic look and a temporary smell of wood. We currently offer 8 color shades and are preparing more. Thanks to the bio-sourced origin of the material, it is 100% biodegradable by industrial composting” Barbora Jurčová, head of Research & Development explains.
As far as applications are concerned, the material can be used to develop 3D-printed speakers like the one developed as part of the Spirula project in cooperation with Akemake.
At the manufacturing level, utilizing Timberfill in the 3D printing process requires specific considerations to achieve optimal results. According to Jurčová, as the material contains wood fibers, it can influence printability and cause increased nozzle wear. To mitigate this, users are advised to employ a specially designed hardened nozzle suitable for composite fibers. Additionally, using a nozzle with a minimum diameter of 0.5 mm is recommended. Properly drying the material before printing is essential to prevent material degradation, stringing, and poor layer adhesion. Just like with any filament, fine-tuning print settings, including temperature, layer height, and print speed, plays a critical role in obtaining high-quality prints.
Other applications involve all kinds of decorative objects, artistic sculptures, furniture models, personalized gifts and even functional parts with the appearance of wood. The versatility of wood fiber filament 3D printing opens up opportunities in a variety of industries, especially design, art and prototyping.
As far as industrialization is concerned, it should be noted that several factors can limit the development of filaments with wood fibers. “There are limited mechanical properties (mainly fragility) compared to traditional materials such as metals or plastics. Furthermore, it is the low-temperature resistance of the material, which is due to the polymer used. For some users, the need to dry the filament before using it, as well as the use of a nozzle with a larger diameter, can be limiting. And last but not least, it is a higher price compared to standard PLA or ABS filaments,” Jurčová outlines.
Timberfill is available today in 8 colors, which can deliver “an authentic-looking wooden surface”. According to the company, the potential for robotic 3D printing opens up possibilities for manufacturing large-scale objects, bolstering the case for industrial adoption.
Pellet 3D printing
While the consumer segment has a great potential, the combination of wood pellets and 3D printing has already delivered interesting applications in architecture.
The current use of the technology for one-time applications such as decorative objects or artistic sculptures makes it hard to envision an industrialization project.
Wood 3D printing with Liquid Deposition Material
The WoodenWood project of D.DLab is the only one we’ve seen so far, that explores the use of wood as a paste. With the goal of developing circular solutions for wood products and processes, Barath explains that they incorporate traditional modular woodworking expressions with robotic printing of wood paste for the prototyping of seating elements.
The printing toolpath creates a new ‘wood-textile’ resembling a rattan texture while using an inferior material, sawdust. The raw wood structure serves as the mold for the printing process, avoiding additional waste through by-products. Together, traditional and digital designs present a circular expression for wood waste towards a new end of life. Our primary objective was to prototype a case study that could be expanded to a wide range of applications using natural waste and degradable materials in the fabrication process. The WoodenWood project serves as a demonstrator of this platform, with potential applications spanning from construction and architecture to fashion and various product designs, Barath adds.
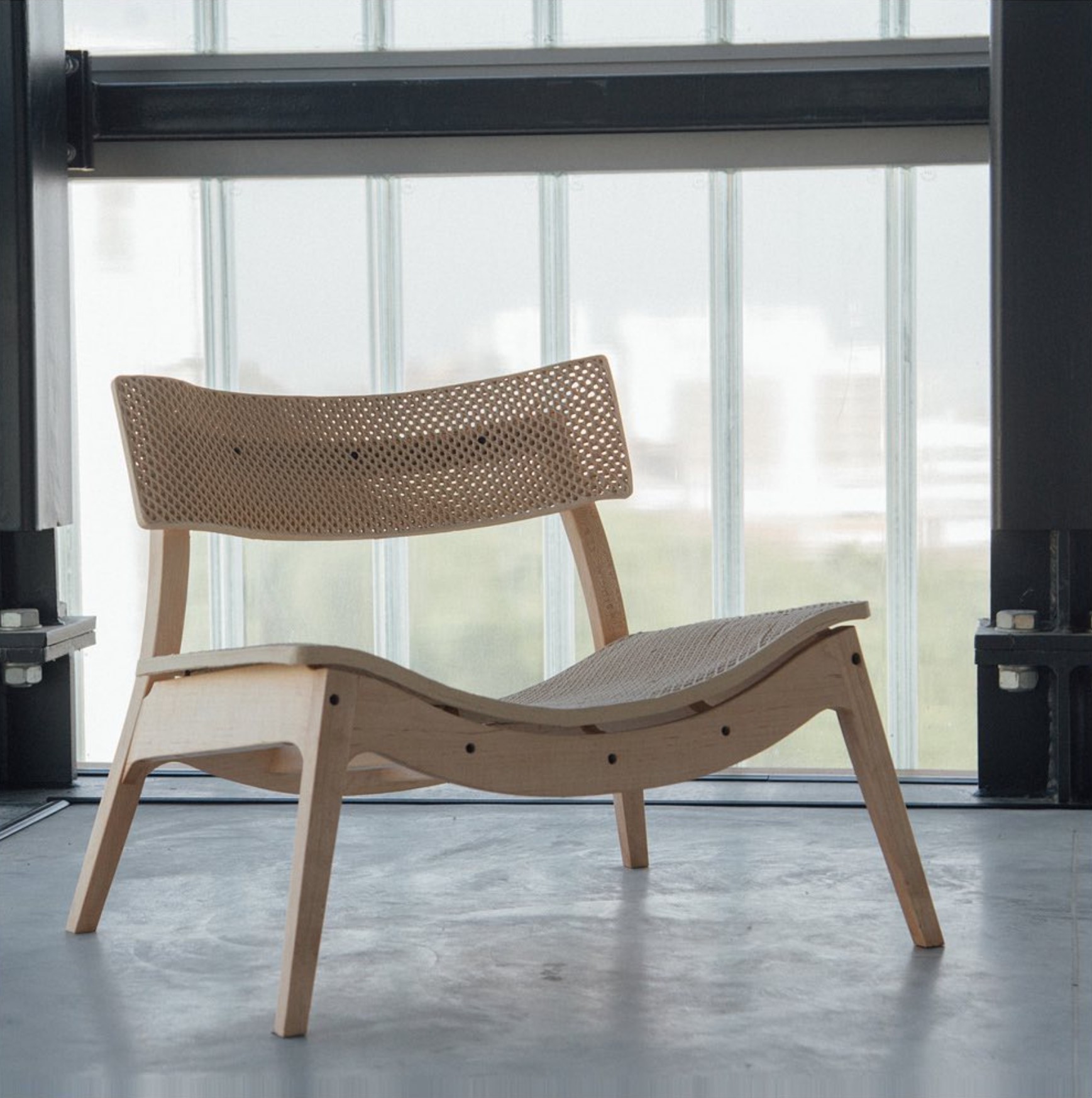
At the manufacturing level, the material formulation is suited for LDM printers (such as clay printers) that are based on air pressure. However, the developed design to manufacturing workflow requires knowledge in computational design and robotic tool pathing techniques. The truth is, the use of natural materials within LDM printing requires establishing specific protocols to handle the inherent shrinkage and subsequent drying processes effectively.
What might slow down the adoption of this technology is the disruption in the fabrication processes. Considerations such as overhangs, bridging, slamp, drying, etc. become more exaggerated as the print grows in scale. Therefore, adjustments to the formula and print toolpath are needed, and this requires further research and experimentation. In addition, apart from its design-oriented nature, mechanical testing is essential for evaluating the performance of the process at different scales, Barath outlines.
While it is too soon to speak about industrialization, it should be noted that in the long run, they seek to achieve applications tailored to the construction industry.
Conclusion
Wood 3D printing is definitely appealing, regardless of the AM process used. However, the current types of applications that can be achieved with these methods make it hard to envision an industrialization-based business model for companies exploring these techniques. Hopefully, with the improvement of these techniques, users will be more confident to make the shift from prototypes and small series to actual series production.
This dossier has first been published in the July/August edition of 3D ADEPT Mag.