Desktop Metal continues to gain momentum in the industry. It looks like when it is not expanding metal AM applications, or exploring new acquisitions, the company is looking to debut new segments. The latest one is Forust™, its subsidiary dedicated to high-volume AM of end-use wood parts.
At the heart of the newly created company, we found Andrew Jeffrey, co-inventor and CEO, Virginia San Fratello, Architect and co-inventor, as well as Ronald Rael, Designer, Educator and Co-inventor. The three of them share the same vision for turning wood byproducts, including sawdust and lignin, into finished wood products, combining both stunning design and functionality.
To do so, they have developed a new process to sustainably produce functional end-use wood parts using a patented single pass binder jetting AM technology.
“The inspiration for Forust was to begin with sawdust and end with forests,” said Jeffery. “Our process is based on extensive research conducted over the past decade in the field of hardwood lumber, leading to complex and elegant finished structures. Through advanced CAD software, proprietary materials and Desktop Metal binder jetting mass production platforms, we can now manufacture beautiful, functional and innovative wood products for a variety of architectural, interior, and home goods applications from upcycled wood byproducts.”
The Forust process upcycles waste byproducts from wood manufacturing (cellulose dust) and the paper industry (lignin) and re-materializes functional wood parts through high-speed 3D printing including digital grain throughout the part.
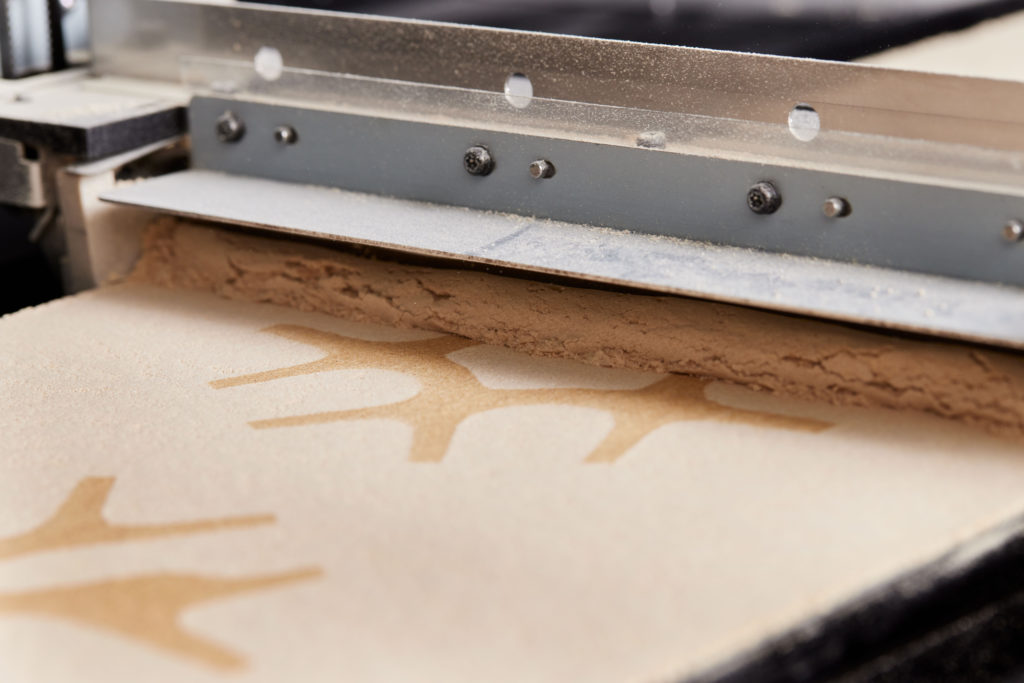
According to William McDonough, “the Forust technology allows us to take something that was previously wood waste and re-materialize it into exquisitely beautiful and useful things. We are honoring the cellulose and lignin of the trees by rearticulating them into assets for present and future generations. By allowing millions of trees to remain in place in their forests, Forust is launching a highly evolved technology for the circular technosphere that supports and celebrates stewardship of the natural, regenerative, and diverse biosphere, making it not only smart, but wise. This is a historic and material opportunity in the history of design and the making of things that reminds me of Arthur C. Clarke’s famous quote, ‘Any technology that is sufficiently advanced is indistinguishable from magic.’ As a lover of wood and forests, I find Forust indistinguishable from magic. The 3D printing of wood using waste natural materials is a gamechanger. We have only begun to explore its beneficial potentials, but it is clear they are immense.”
On the path to a Greener Future with Additive Manufacturing for Wood
From a manufacturing perspective, the explain in a press communication wood products can be manufactured using either the Shop SystemTM or a custom version of the new RAM 336TM 3D printer, which supports prints up to two cubic meters in volume at speeds in excess of 100 liters of parts per hour.
Forust_LivingWall_tiles Forust_Propellers_cropped
During the printing process, layers of specially treated sawdust are spread and selectively joined by a non-toxic and biodegradable binder. Digital grain is printed on every layer and parts can then be sanded, stained, polished, dyed, coated and refinished in the same manner as traditionally manufactured wood components.
“Forust offers nearly unlimited design flexibility,” said Jeffery. “From exotic grain structures to grainless wood, we can digitally reproduce wood textures and a myriad of grain types. And, because they are made from a wood and bioresin compound, these parts exhibit the functionality and stiffness in line with conventional wood. Our finished pieces are indistinguishable from traditionally manufactured wood products you would find in a store. The additive manufacturing process literally becomes invisible.”
In this green world that Desktop Metal invites us to explore, we can find applications that include but are not limited to architectural accents, luxury interior components, furniture pieces as well as home goods products.
Remember, you can post free of charge job opportunities in the AM Industry on 3D ADEPT Media or look for a job via our job board. Make sure to follow us on our social networks and subscribe to our weekly newsletter : Facebook, Twitter, LinkedIn & Instagram ! If you want to be featured in the next issue of our digital magazine or if you hear a story that needs to be heard, make sure to send it to contact@3dadept.com