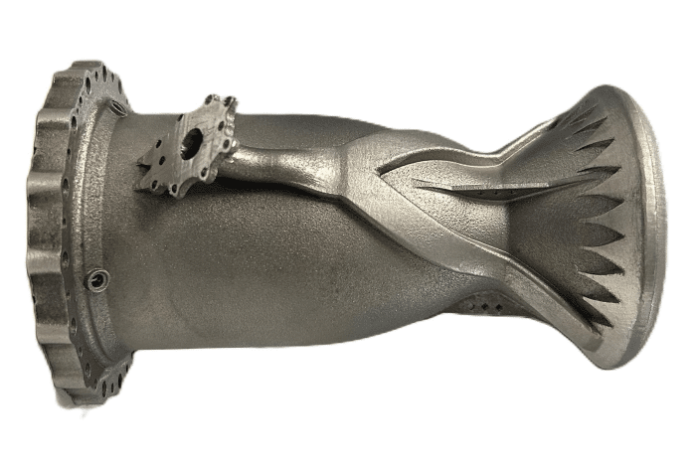
Wipro 3D a provider of 3D printing services, joins forces with the Indian Space Research Organisation (ISRO), to manufacture a PS4 3D-printed rocket engine. The rocket engine powers the 4th stage of the Polar Satellite Launch Vehicle (PSLV), an expendable launch system designed to place earth observation and Scientific satellites into precise orbits enabling multiple applications like remote sensing, oceanography, cartography, mineral mapping, disaster warning etc.
To ensure accurate orbital placement, the PS4 stage is equipped with advanced navigation, guidance and control systems. Its adaptability for different kinds of spacecraft missions is enhanced by its ability to support multiple restart capabilities and payload adapters.
The PS4 engine, traditionally manufactured through conventional machining and welding, underwent a redesign thanks to Additive Manufacturing.
The two partners relied on Design for Additive Manufacturing (DfAM) and Laser Powder Bed Fusion (LPBF) technology, to consolidate the multiple and diversified PS4 engine intricate components into a single unified production unit, enhancing production efficiency and structural integrity.
Yathiraj Kasal, GM & Business Head, Wipro 3D, expressed, “We’re honored to collaborate with ISRO on this pioneering project, highlighting the potential of advanced manufacturing in Space. This partnership not only advances ISRO’s ‘Make in India’ initiative but also promotes domestic innovation and manufacturing. It is an honor and a privilege to manufacture the PS4 engine for the PSLV vehicle. We are eagerly awaiting the successful second round of testing to fly high alongside ISRO.”
The 3D-printed PS4 engine, featuring integral complex cooling channels, prioritizes sustainability and efficiency in its design, with minimal material wastage and post-print machining operations. Rigorous testing of the hardware at the facilities at ISRO Propulsion Complex in Mahendragiri confirmed the engine’s performance under real-world conditions, meeting the design safety and efficiency standards.
The key performance metrics of the ISRO 3D-Printed Rocket Engine extended duration test included optimal chamber pressure, fuel management, combustion efficiency, and specific impulse (Isp). ISRO’s adoption of additive manufacturing offers superior precision, minimal resource utilization, and significant reductions in material wastage and production time.
Remember, you can post job opportunities in the AM Industry on 3D ADEPT Media free of charge or look for a job via our job board. Make sure to follow us on our social networks and subscribe to our weekly newsletter : Facebook, Twitter, LinkedIn & Instagram ! If you want to be featured in the next issue of our digital magazine or if you hear a story that needs to be heard, make sure to send it to contact@3dadept.com