More agility, investments, COVID-19, product launches, mergers & acquisitions
As 2021 is around the corner, 3D ADEPT Media looks at some of the topics that will shape up the additive manufacturing industry.
Needless to remind that 2020 made us go through an emotional rollercoaster: from several human losses to the positive response of the AM industry to the Covid-19 pandemic, some companies had to close their businesses, reduce their workforces while others have had their best year ever.
Unfortunately, for the near-term, COVID-19 will still be a part of business planning and operations in 2021. The good news is that, additive manufacturing is built for situations like this, and ultimately, companies will find their own rhythm to adjust to market conditions.
While we cannot tell for sure what will happen, there are signs that do not lie about the direction the AM industry will take.
More agility in the Supply Chain process
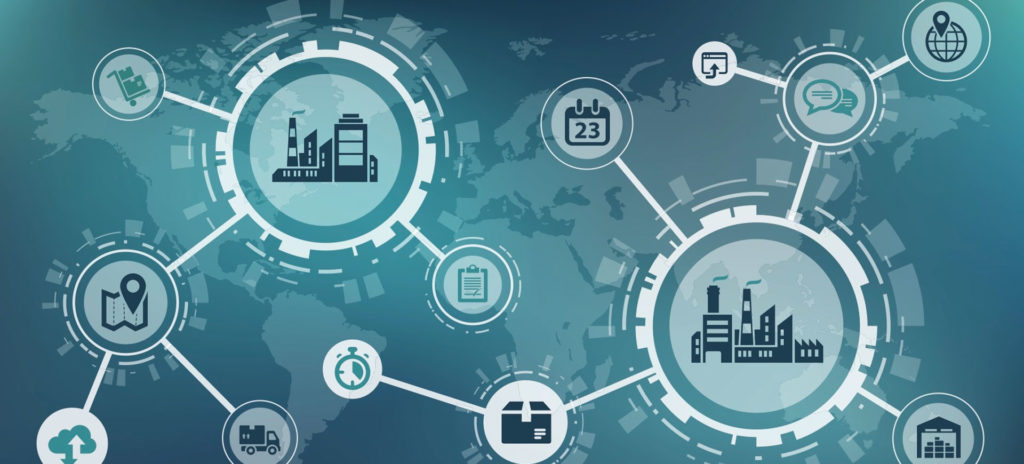
According to Shapeways, companies will continue to rethink redundancy, who their suppliers are, and look to high mix – low volume on-demand manufacturing. 3D printing will play a large part in the supply chain conversations as they have in 2020. In addition, more distributed manufacturing will be a consideration as end products are produced closer to the end user.
More investments for 3D printing companies
Materials, hardware, and software for additive manufacturing will attract investors to the space. Furthermore, the confirmation of Desktop Metal as a publicly traded company has raised further interest in AM among investors. According to Arno Held, Chief Venture Officer (CVO) at AM Ventures, with this confirmation, “it should be a little bit easier to get money”.
Improved digitization processes
Since the pandemic puts us in a state of emergency, companies are in the rush to accelerate their digitization processes. However, to bring digitization to reality faster, they will make choices based on risk, cost and quick return on investment (ROI).
As AM is one of those digital technologies that can deliver short-term ROI, low-cost manufacturing, and low risk, Materialise states that the entry point has typically come with a lengthy learning curve. Some companies started the AM adoption process ten years ago and are well-positioned to make greater shifts to the technology, but companies new to AM no longer have the luxury of time.
Materialise Vice President for Medical, Brigitte de Vet, explains: “As a result, we see a growing trend for services that guide companies along this path. We see this for example in the medical world, where the value of personalized medicine is well known, but there is a low tolerance for uncertainty. New solutions need to offer strong evidence that they are safe and effective and can deliver a high-quality standard of care. Consultancy services can help minimize the risk of such big investments and accelerate the timelines by sharing their expert knowledge of what the technology can and can’t do, and the right manufacturing method needed for each unique case.”
In the same vein, the industry will see a rise of 3D printing software to scale businesses. 3D printing at scale is very involved from nesting, tray planning, file fixing, build planning and more. In the nutshell, software tools provide the insight required to get prints manufactured correctly and therefore make it easier to produce quality products.
Expected product launches & commercialization
An industry without product launches is not really one. Several companies have announced the commercial availability of their technologies for 2021.
Starting in January, Wayland Additive will launch its Calibur3 AM system and NeuBeam technology. The latter promises greater flexibility and stability, as well as the ability to process materials like tungsten, copper and tantalum. The UK-based manufacturer explained at length the features of this new eBeam process that would be very different from traditional eBeam PBF processes. Indeed, the charging issues that make EBM so unstable have been fully neutralized with NeuBeam using core physics principles developed in the demanding semi-conductor industry. Moreover, NeuBeam is a hot “part” process rather than a hot “bed” process. This efficiently creates parts that are free of residual stresses because the high temperatures are only applied to the part and not the bed, ensuring free-flowing powder post-build (no sinter cake) and stress-free parts with reduced energy consumption.
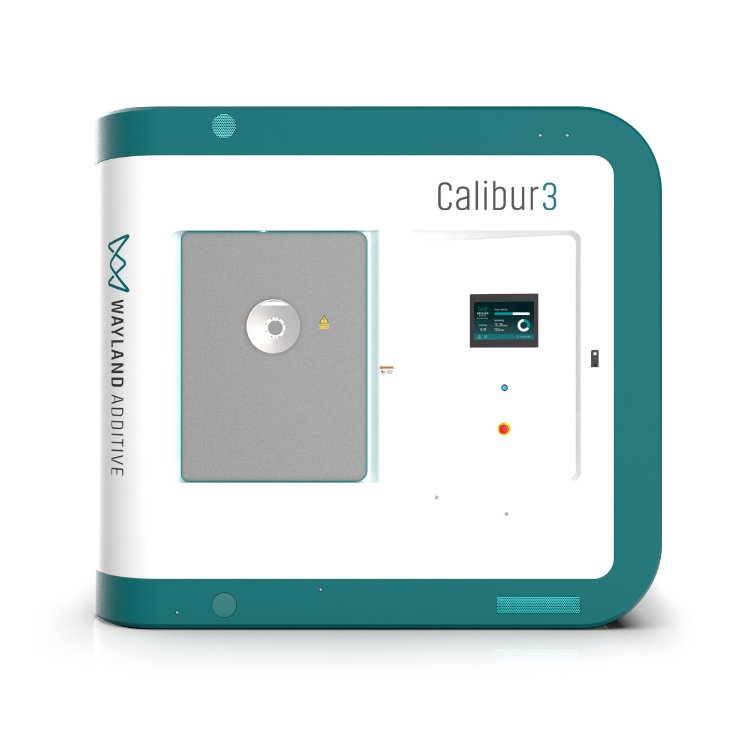
GE Additive is currently preparing the launch of a binder jet technology that is set to achieve high volume, low-cost additive production. A Binder Jet beta partner program currently involves some companies such as Sandvik that develop the beta H2 system into pilot lines.
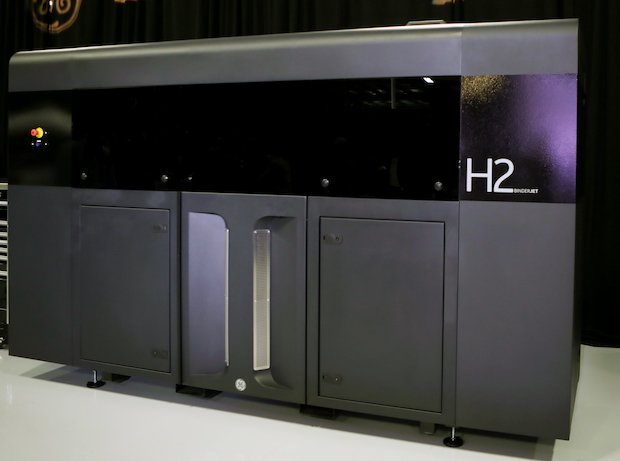
Two years ago, HP revealed the first details of its metal jet 3D printing technology. While the technology was originally only available via select services such as GKN and Parmatech, the manufacturer ensured the broader availability of this technology for H2 2021. With the goal of achieving the same success it has had with polymers, HP’s Metal jet technology promises speed, quality, reliability, scale and the ability to provide up “to 50 times more productivity at a significantly lower cost than other 3D printing methods.”
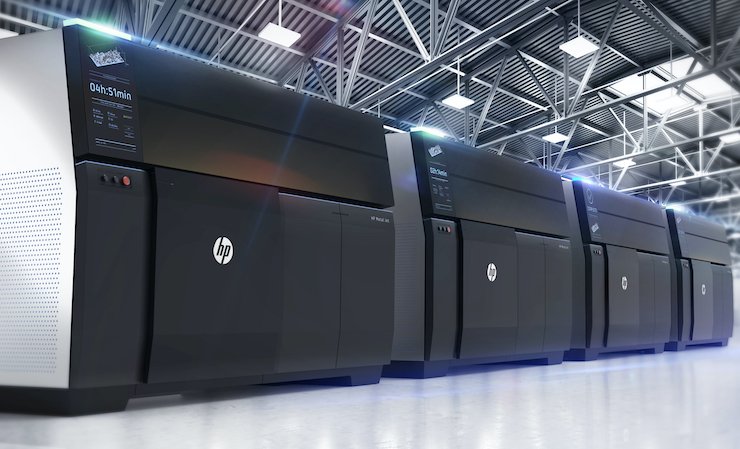
Evolve Additive Solutions will (finally) ship its first Scalable Volume Production (SVP) system, a true milestone for the company that has been working on the Selective Thermoplastic Electrophotographic Process (STEP) technology for twelve years. As a reminder, the STEP technology would process 100% dense thermoplastics with isotropic properties, deliver multi-materials and multi-colour, custom blends at voxel level and complex geometries and fine features.
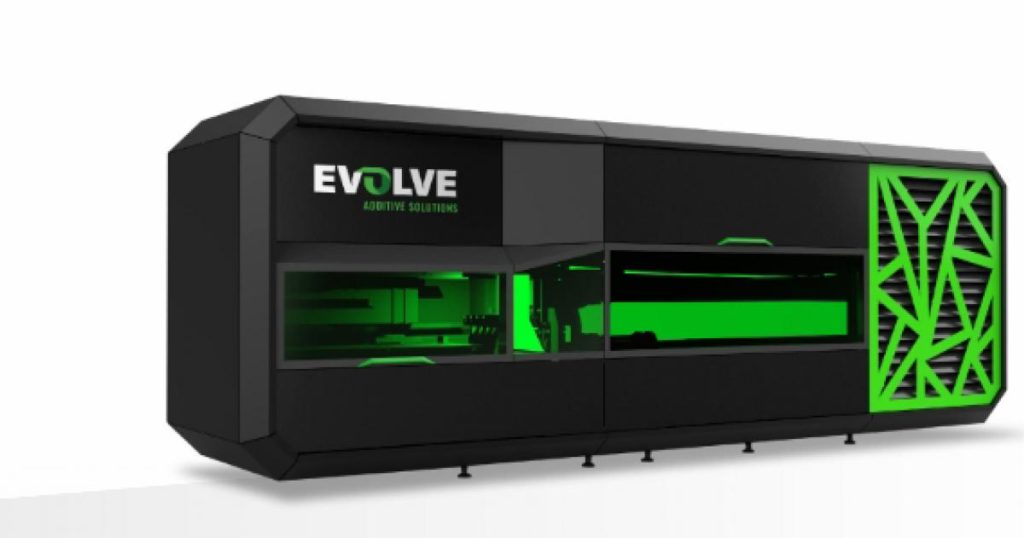
We will end this non-exhaustive list with Additive Industries that has recently given a sneak peek its latest model, the MetalFAB-600. Planned to be unveiled at the end of 2021, the industrial machine offer a build size of 600x600mm and 1000mm Z-height, one of the largest volumes in the industry, and 5X larger in volume than the manufacturer’s current MetalFAB1, that already offers 420x420x400. The MetalFAB-600 will be highly productive with a deposition rate up to 1000cc/hour, using 10x1kW lasers. It is developed on a platform that allows even further expansion of the build volume and productivity in the future.
Mergers & Acquisitions
Two main acquisitions are expected to be completed in 2021: the acquisition of DSM by Covestro and the acquisition of Origin by Stratasys.
As part of a $1.61 billion acquisition of its resins & Functional Materials business, Covestro announced the complete takeover of DSM’s 3D printing – takeover which is set to be finalized in H1 of 2021.
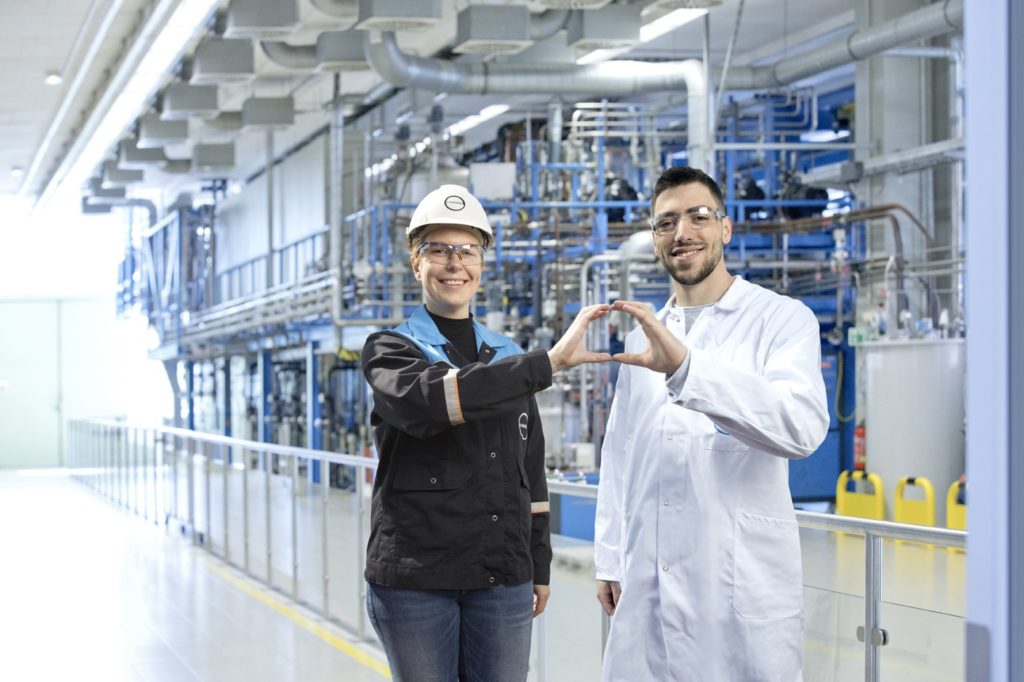
This agreement occurred after DSM had acquired a part of Clariant’s 3D printing business. With Clariant and DSM onboard, Covestro’s corporate strategy will focus on complementary technologies and customer industries on the one hand, on the other hand will increase its commitment towards circular economy.
Earlier this month, Stratasys announced an agreement to acquire Origin in a deal that could reach $100m. Both companies will benefit from each other as Stratasys wants to expand its portfolio with the integration of Origin’s Programmable PhotoPolymerization (P3) technology and Origin is interested in taking advantage of Stratasys’ go-to-market capabilities.
P3 which is at the heart of this deal, is a Digital Light Processing technology that has been packaged into the modular Origin One platform. It can process a host of resin-based materials developed by acknowledged materials suppliers such as BASF, DSM and Henkel.
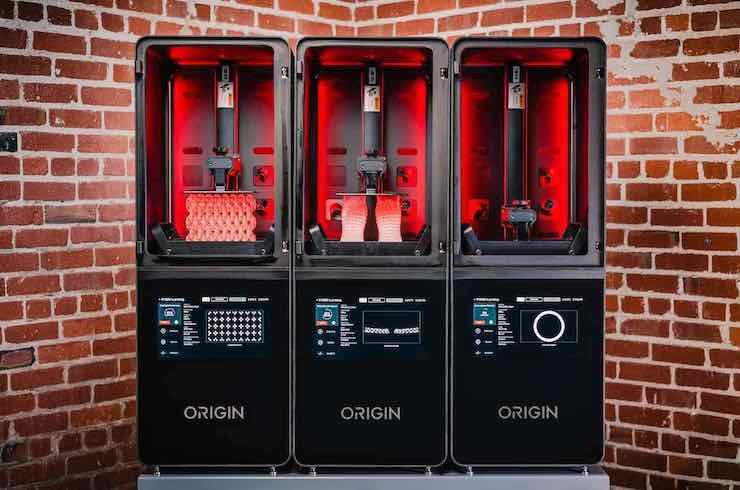
New opportunities to be explored
As for companies that haven’t yet announced a clear defined path for 2021, we might still expect new opportunities to pop up at anytime.
Indeed, as Materialise explained, global crises are incentivizing industries to fast-track their technological innovation, and this climate of radical reinvention represents an opportunity for AM to really become instrumental in the areas of design and manufacturing.
One thing AM taught every one is to focus on the solution instead of the product and “starting fresh doesn’t mean starting from nothing. By going back to the drawing board, we create freedom to give new technologies a chance. To unleash new perspectives and possibilities. Then, the only limit to the change we can create, is our imagination”.
Remember, you can post free of charge job opportunities in the AM Industry on 3D ADEPT Media or look for a job via our job board. Make sure to follow us on our social networks and subscribe to our weekly newsletter : Facebook, Twitter, LinkedIn & Instagram ! If you want to be featured in the next issue of our digital magazine or if you hear a story that needs to be heard, make sure to send it to contact@3dadept.com