Whether it is to leverage the design potential of Additive Manufacturing, to optimize and convert CAD into machine code or to rule out human errors, there is a lot to master when it comes to additive manufacturing software.
While many engineers know software is crucial for successful deployment of AM processes, and Design for AM in particular, there is still a lack of understanding of all areas to take into account when it comes to keeping cost and lead times at an acceptable level using AM-dedicated software tools.
With two and a half decades of expertise, it’s safe to say MachineWorks knows a thing or two about software. The UK-based company started as an internal spin-off from Lightwork Design, now part of Siemens PLM. Today, the company is part of Heidenhain GmbH.
MachineWorks first built extensive expertise in conventional manufacturing processes by developing a technology that is used on CNC controls. In addition to commercializing component technology, primarily to other software OEMs, MachineWorks also develops custom software solutions for in-house customers in larger companies.
In this Opinion of the Week, Richard Baxter, Sales Manager at MachineWorks discusses the company’s activities within the AM industry with a key focus on hot topics that shape AM software development.
MachineWorks’ solution for AM
If MachineWorks is first acknowledged for its ability to simulate the CNC material removal process, the company further raised our interest when their Polygonica tool helped reconstruct a 17th century flute model by enabling 3D printing of playable replicas. Polygonica is a component for Additive Manufacturing Print Preparation. It is also used to simulate hybrid AM processes.
“Polygonica is the better known brand in the AM industry” Baxter said. [It] “is a general polygon mesh processing engine. It provides a wide range of useful functionality that is well implemented, fast and stable. It is known for being one of the best automatic mesh-healing engines in the industry but it also offers unique and innovative solutions for widely required 3D operations such as Booleans, offsetting, remeshing and tolerance-based decimation. These are extremely useful for developing print-preparation functionality such as hollowing, lattice creation, support-generation, slicing, hatching and in-fill.”
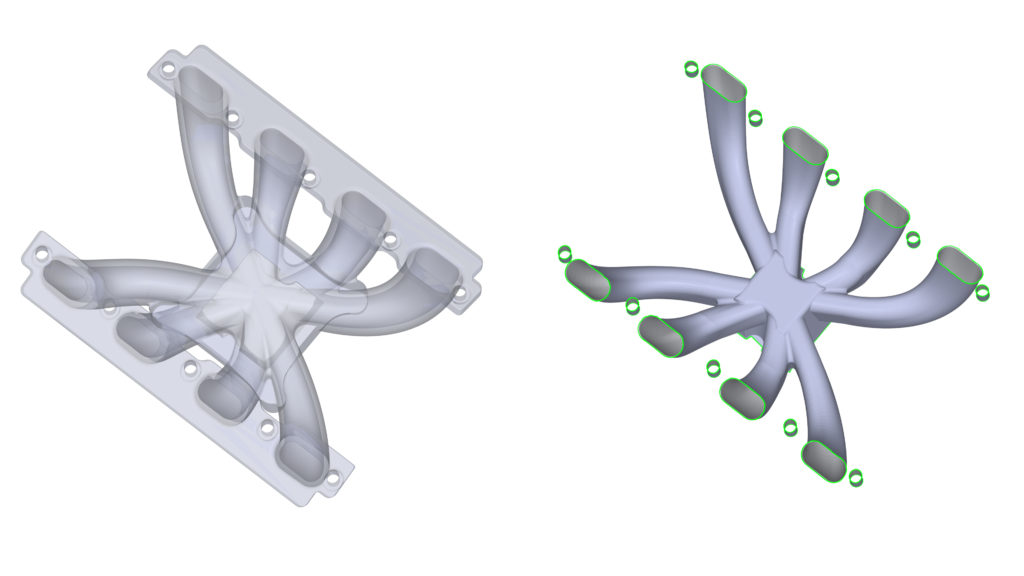
We rarely heard about component vendors themselves, yet their engines are used extensively by well-established AM brands. The Polygonica team focuses on the development of general geometric algorithms that are embedded in other software processes.
“The best testament to the quality and support offered by Polygonica is the list of leading products in which it is embedded. These include 3DSprint, 3DXpert and Cimatron/E from 3D Systems, GrabCAD Print from Stratasys, the wide product range from ANSYS, including ANSYS Discovery and Spaceclaim, Desktop Metal Fabricate and Live Parts, EnvisionTEC Perfactory, AM Studio from CADS Additive, Z-Suite from Zortrax and Renishaw’s Dental Modelling System. Polygonica is also used by a number of high-profile OEMs in what can loosely be termed the cloud-based auto-quoting market. There are now over forty OEMs licensing the technology so the above list only represents a small subset of the software applications that make use of it”, Baxter continued.
How does Polygonica’s key specifications meet the current needs in AM?
First, Design for AM continues to raise significant challenges among designers who, do not always know how to effectively represent and optimize intricate geometries and functionally graded structures in certain applications. For these designers, the struggle consists in incorporating Design for AM knowledge into the design process.
Taking the example of ANSYS, Baxter explained that newer CAE tools such as ANSYS Discovery Live help the designer to see the effects of design changes on important physical characteristics almost immediately.
“We’ve seen that the outputs from generative design and topology optimisation processes can often need quite a bit of post-processing so that they can be properly checked in downstream solvers, which themselves can be quite picky with respect to the quality of input data. So we’re adding more functionality to assist in this area such as foldover detection and removal and also gluing, a kind of “fuzzy Boolean” designed to remove small gaps where two surfaces don’t quite meet correctly”, the Sales manager pointed out.
Furthermore, Polygonica can provide a wide range of benefits to the AM industry thanks to the use of software in other industries and the team’s experience in conventional manufacturing processes. For our guest, this cross-pollination of ideas can only drive innovation.
“Most obviously the innovations used in Polygonica’s healing and offsetting came from techniques developed for the subtractive industry, not for additive. But we’ve also seen functionality requested by AM customers adopted and used in the construction industry for analysing building schedules. The shrinkwrap technology developed for the purposes of reducing data for faster VR/AR/XR visualisation is also being used in the mining and civil industries to create cleaner meshes from scans of underground tunnels and in AM to identify internal tunnels and spaces to analyse accessibility for powder and support removal. The foldover removal was originally requested by our dental scanning customers but is now being evaluated for use in AM for lighter-weight automotive components”, MachineWorks’ expert noted.
Today, Polygonica can convert laser scan data to usable meshes. The company has recently released its 3.0 version of Polygonica, which delivers improved surface detection capabilities. The AM-dedicated tool can now recognise surfaces and features from noisy laser scans. This capability is of paramount importance for designers are looking to make scans more useful, whether working directly with polygon meshes that result from the scans or reverse-engineering them to CAD surfaces.
SurfaceDetection_Wheel Surface Detection_Wheel_With Facet Edges
Moving forward, should we remove .STL from the AM process chain?
The STL format is the most renowned format for a 3D modelling file. It has become the de facto international standard for 3D printing enthusiasts. However, over time, many designers have pointed out the weaknesses of this format in an industrial environment. For many experts including some software companies, its specifications have remained unchanged and they do no longer meet current industrial needs. In a previous issue of 3D ADEPT Mag, Olivier Desmaison, Head of Simulation Solutions Development for Additive Manufacturing at ESI Group explained that “the STL format is still widely used but it only provides the minimum set of information. There are several limitations including the basic geometry, a simple triangulated model which brings out a few data when generating the STL file and removes a lot of crucial information contained in the original model.”
The use of .STL in the repair of corrupted 3D models is even more controversial, not to mention other challenges faced by manufacturers. That’s why many designers would like to replace it by new file formats for additive manufacturing.
Baxter brings today another point of view on the table. He strongly believes blaming all the problems on the little old STL format is conceptually convenient but replacing it is only going to solve a tiny subset of the problems real manufacturers are facing.
“In most industries there are fundamental differences between the underlying data structures used for design and manufacture, be it structural analysis, CFD or CAM toolpath generation. Put simply, in most cases the former work with parametric surfaces e.g. NURBS, whilst the latter mostly work with polygon meshes.
Switching between these representations – and others – present significant geometric challenges irrespective of how that data might be captured in a particular file format. Polygonica’s healing algorithms are a great get out of jail card for software developers working on these advanced systems.”
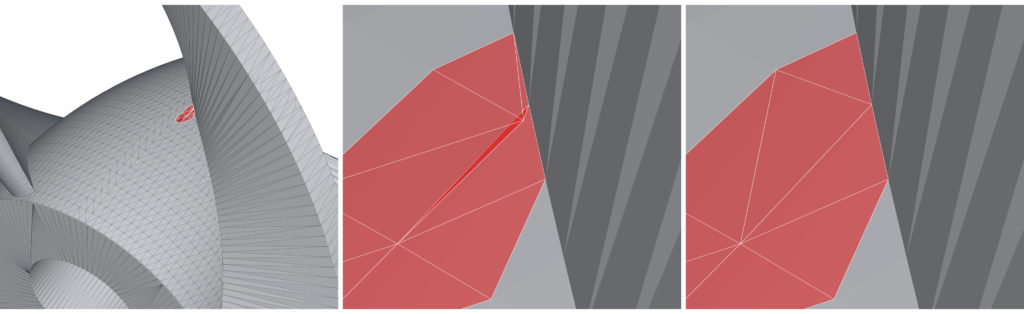
Baxter recalled a recent discussion with a Project Manager at an aerospace engine manufacturer. That company was using best-in-class software for all its processes but still needed healing to make its design, analysis and manufacturability workflows reliable.
“That situation may, rightly, seem incredible to an engineer, but I don’t see it changing anytime soon. Fundamentally developing this type of software reliably is really hard so having a tool that can reliably fix errors when they occur is really useful”.
In a nutshell…
Additive manufacturing, large models and improved techniques of rapid CAE meshing are three areas where MachineWorks is uniquely positioned to address market needs. Thanks to its polygon-based modeling kernel, the Polygonica team recreates interest in a format that has lost its value. This ability to clean and heal models in preparation for AM and to enable watertight representations for accurate CAE meshing are only made possible thanks to the company’s extensive experience across industries and the cross-pollination of ideas that emerge from it.
Remember, you can post AM job opportunities for free on 3D ADEPT Media or look for a job via our job board. Make sure to follow us on our social networks and subscribe to our weekly newsletter: Facebook, Twitter, LinkedIn & Instagram! If you want to be featured in the next issue of our digital magazine or if you hear a story that needs to be heard, make sure to send it to contact@3dadept.com