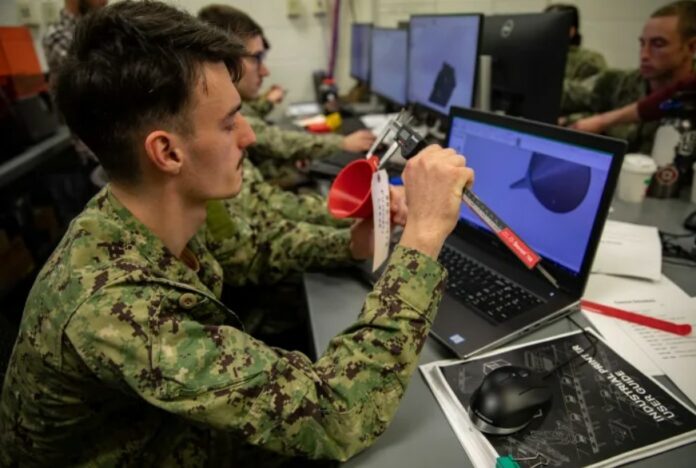
The AM journey of US Navy started in 2016. Ever since they validated their first business case, different divisions of the organization have been exploring the capabilities of this technology. The latest example they shared reveals how they have been able to address supply chain issues with AM.
According to Matt Sermon, the executive director for the Program Executive Office for Strategic Submarines, the industrial base struggles the most to keep up with the required capacity of heavy metal parts and components. These include castings, forgings, valves, fittings and fasteners.
The Navy looked at 5,500 parts that have presented schedule challenges for new construction and maintenance availabilities for submarines and ships; six materials account for 70% of late deliveries, Sermon notes. Add to that the fact that some of the parts are complex to manufacture using some of these conventional manufacturing processes, the maintenance process is further slowed down. Castings for instance, are particularly tough for the yard, and there’s a long list of cast metal parts they’re struggling to procure on time and in good quality. Additive Manufacturing could shorten the production timeline for certain metal pieces by an average of 80%, depending on the printer’s efficiency.
These parts have always been a challenge to the industrial base, as the fundamental metallurgy is complex and can lead to flaws. But there are fewer companies making these components today than in past decades, and that smaller base is struggling to keep up with growing demand.
The Navy has developed a plan to mature the metals, printing machines and processes associated with those six materials this year, such that by March 2024 they can be printed in volume and put on submarines, Sermon said.
“We don’t have that process fully matured to the point where we’re able to scale additive manufacturing like I think we need to,” Bill Galinis, the commander of Naval Sea Systems Command said. “We can do the one-off parts, and frankly, even for a reactor component, we’ve built some fairly complex parts using additive manufacturing, but we haven’t gotten to the point where that’s scalable.”
The next step for the team is now to identify high-volume, high-usage parts, and have a printing capability that allows them to print those on a pretty regular basis.
The “challenge right now is, one, quickly coming through the certification process, codifying what that’s going to look like, and then being able to scale additive manufacturing”, Galinis explains.
Remember, you can post jobopportunities in the AM Industry on 3D ADEPT Media free of charge or look for a job via our job board. Make sure to follow us on our social networks and subscribe to our weekly newsletter : Facebook, Twitter, LinkedIn & Instagram ! If you want to be featured in the next issue of our digital magazine or if you hear a story that needs to be heard, make sure to send it to contact@3dadept.com