Starting from roots of thermal coatings & woodworking, morphing into an industry-leading CNC machine tool OEM, and a few years ago bridging into the Additive Manufacturing space; the Thermwood group had a multi-faceted presence at this year’s RAPID+TCT show.
“We’re showing the end-to-end solutions we offer, especially for fixturing and tooling that’s either printed or machined,” Brent East, US Account Manager for Thermwood explains. At their front-row RAPID+TCT booth, there was a demo station for their new Cut Layer Additive system, along with an array of different examples of tooling for composite layups, thermoforming molds, and enclave fixtures for baking aerospace-grade components. That, along with some of the friendliest exhibitors at the show made for an excellent experience learning about the latest & greatest with this reputable machine tool OEM and CAD/CAM software partner.
From humble roots as a contract manufacturer
In the early years of Thermwood, the team started as a job shop for tooling & fixtures for thermoforming and woodworking applications. The expertise derived from the company’s knowledge in the CNC machining industry still remains a core element of the organization today. This spawned a new era for the group as they began to evolve, where they envisioned a product to bring to market. The accumulated expertise as a manufacturer proved to be vital when the group began to develop their own line of CNC Gantry Systems tailored for woodworking; some of the first to enter the market in the early 1970’s.
To the emergence of Cut Center for traditional CNC routers
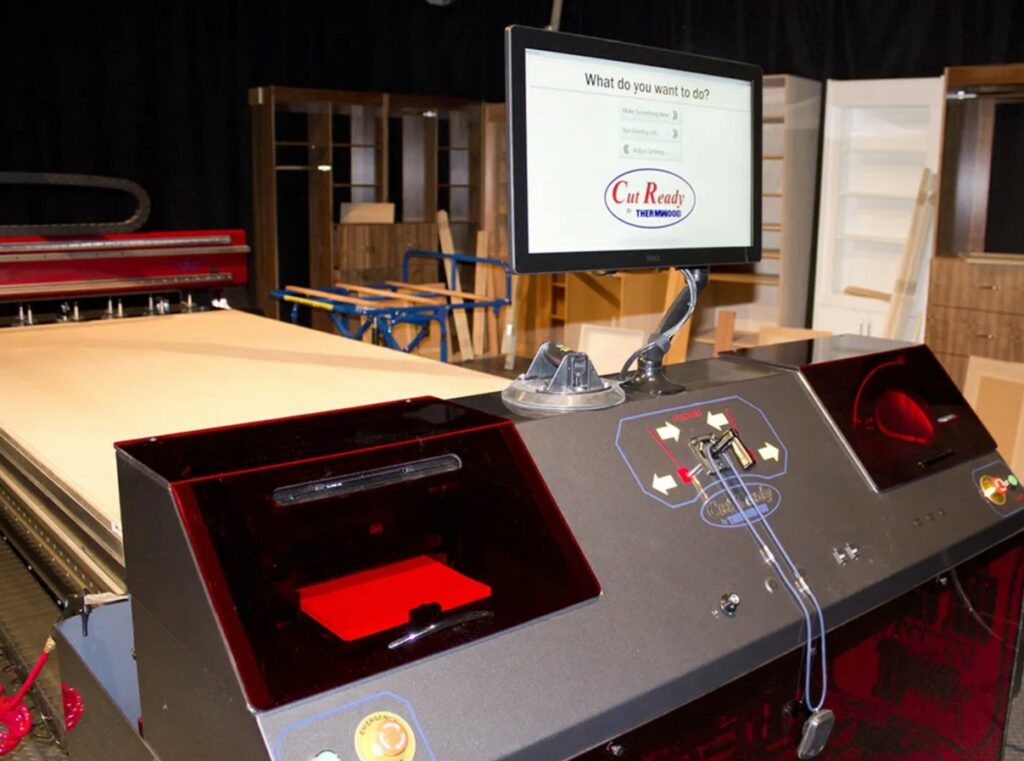
Cabinet builders, carpenters and woodworkers alike were among the main end users for Thermwood’s initial line of large-format gantry-style 3-axis CNC machine tools.
“While working with these different woodworking companies, we found that they often needed a way to get from CAD to end-product in an efficient manner. We really developed the software (Cut Center) around the cabinet maker, and thought through all of the typical issues they’re facing when moving into production,” Jody Wilmes, Product Manager at Thermwood explains. “Things like placing dowel pins, mapping fixturing/tooling for doing batch runs, and especially automating the CAM programming were all elements that we focused on when writing the software.”
Cut Center was born after several years of development, and later found its place in the market for more than just building cabinetry. Soon thereafter, many designers and programmers found its ease of use and productivity increases a crucial part of their product development process. Today you can find a number of shops all across the world utilizing Cut Center as their main programming tool. If you want to learn more about some of the customers having success with the software, follow their customer testimonials here.
Building off that in the Additive Manufacturing space
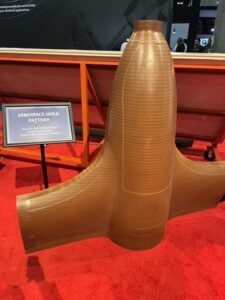
While large-format CNC Machining began to take off, engineers at Thermwood looked for ways to expand their product portfolio. In the late 2000’s the team began to conceptualize a line of LSAM (Large Scale Additive Manufacturing), largely aimed at tool & die and other fixture makers for the Aerospace, Automotive and Industrial markets. Because of the team’s extensive knowledge in programming subtractive (CNC) metal or woodworking machines, the transition to Additive machines for polymers was one with a fairly short learning curve. After a few years of R&D, Thermwood Corporation launched a series of large-format 3D printers in the 2010’s, specializing in particularly large, net-near finish parts.
While recently launching a SaaS product for automating CAM in 3D printing
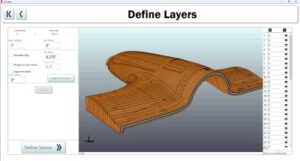
At this point, Thermwood had several decades as a machine OEM, as well as extensive time building out a successful software product. Now that they were in the 3D printing space, the R&D developers internally looked for a way to automate the 3D printer slicing process.
“It was a natural transition for the company,” Wilmes points out. “We proved ourselves in the CNC machine tool industry, scaled up to Large-Scale Additive systems for demanding industries, and branched into the software space after years of printing (and machining) countless parts for our customers,” Wilmes went on to explain that although their Cut Layer Additive Software is newer to the market, they work very closely with their customers to help make improvements to their product.
“We have a close relationship with some of our large install bases, it’s easy for us to provide free updates to our customers to have them trial for parts they’re working on everyday,” Wilmes states.
Why Cut Layer Additive matters for manufacturers
There are a number of occasions when you want to make a large part, but don’t want to machine away a bunch of material to cause waste and minimize profit. “Simply inputting your material & wall thickness (as shown in software illustration above) is all that’s needed to produce the CAM for any large-format 3D printer. The built-in machine learning allows for routing things like dowel pins and other common ways to assemble a large part that’s printed (or machined) in multiple pieces,” Wilmes says. “What’s usually taking a skilled CAM programmer weeks to program can happen in a matter of hours with very few inputs from the user.” There’s no expensive hardware to run Cut Layer, computing can be done at the machine or offline, and inputting the CAM file into a Thermwood machine will have you printing (or cutting) in fairly little time. That’s the power of Cut-Layer, its embedded machine learning algorithm which makes manufacturing a large-format part much easier than hand-calculating, CAD model manipulation, mapping the toolpaths manually, and so many other tedious time-consuming tasks.
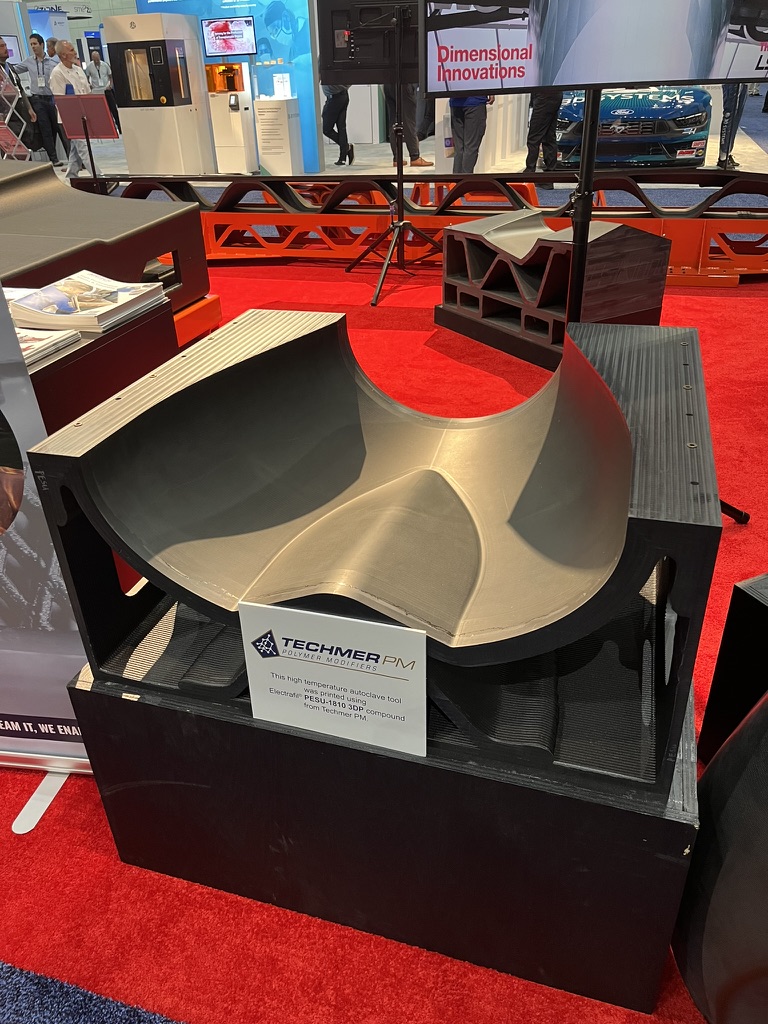
Additive solutions showcased at RAPID+TCT 2024
At the RAPID+TCT show, Brent East walked me through some of the various tooling examples they had on display. “On the Additive side, we’re featuring large scale tooling for composite layups as well as fixturing to take the final tool to production. In talking with vendors at RAPID, we’re seeing an uptick in material advancements which we’re adapting to on the machine side of things to stay current with the latest in polymer technology.”
In walking the show at RAPID, this uptick in material science was evident on all levels of the spectrum. Whether it was at the consumer level with polymer companies like Polymaker branching into metal powders from Linde, along with carbon fiber and other composite filament manufacturers.
Read more about the RAPID+TCT show overview here.
East went on to talk about some of the recent expansions in the space industry along with home-building: “With all of the investments in R&D that are made on the polymer side, it’s typical for hardware OEMs like us to adapt to that newer, faster polymer on the market and build machines to utilize that.” The group is also noticing a large displacement in the casting and foundry industry as well, with end-users looking towards Large-Scale Additive as a solution for shorter lead times and lower costs, as long as the production volume allows for the economies of scale. Aluminum tooling is another area this group has extensive experience in, which was clearly demonstrated at RAPID.
Innovations to expect from Cut-Layer Additive & beyond
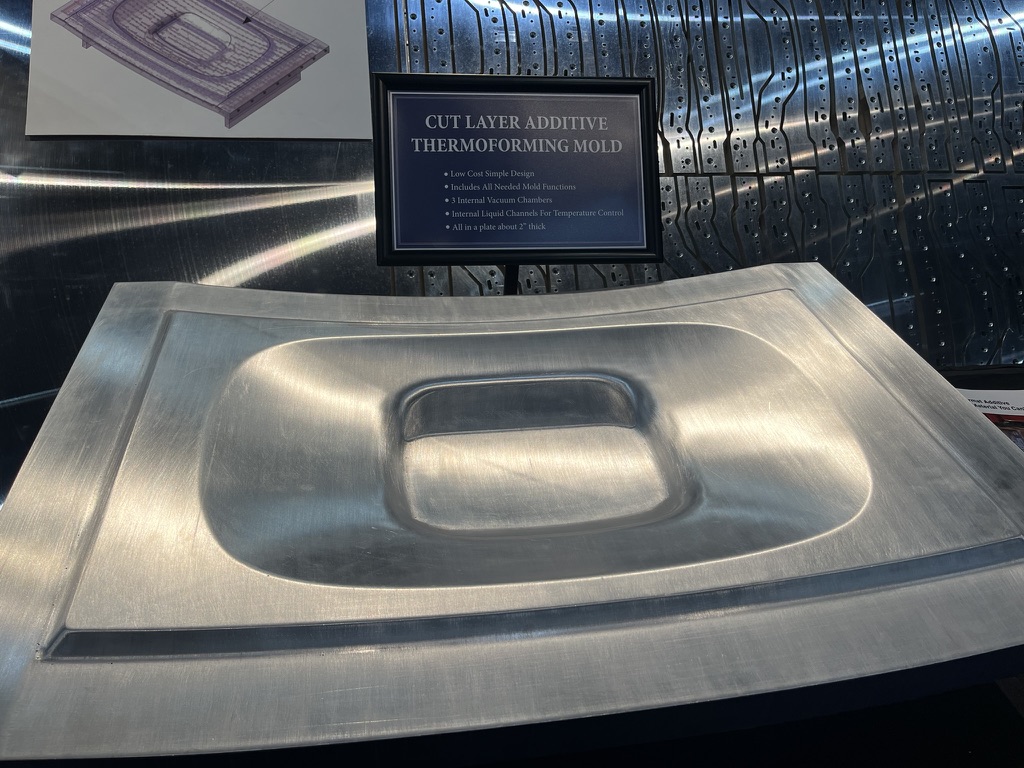
One of the impressive parts the Thermwood team had on display at the RAPID+TCT show this year was a particularly large piece of tooling (shown above). While large parts are well within Thermwood’s scope, it’s the vacuum channels that were placed using the automated CAM software (Cut Layer Additive) that routed all of the fixturing/mold channels, assembly features, CNC machining programming, internal channels for cooling, part simulation, and more using Cut Layer.
“This is a huge step forward for anyone who is still paying an expensive programmer to manually map out everything that goes into already expensive tooling & fixturing” Wilmes says, “We’re going to continue putting forth immense effort in developing this tool to make it better. Things like Automatically Locating Dowels, Automatic Temperature Control Lines, and Creating Molds from an Original 3D Pattern are all aspects we plan to improve on in future updates.”
Throughout their booth, the Thermwood team demonstrated significant real-life examples of how they’re addressing Large-Scale Additive and Machining with a variety of use cases on display. Whether it was prototype end-use parts, fixturing and molds for composite layup, or thermoforming tooling for Aerospace components, this Indiana-based group brought out their best.
This content has been written by Will Kruspe. Read more about Thermwood’s activities in the AM industry.