2021 has been a busy year for machine manufacturer Thermwood as the company has unveiled new 3D printers, new devices to enhance the printing process with its LSAM process and sign new partnerships with organizations.
One of the first things we learned from the provider of very large format 3D printing hardware and services with composite chopped Fiber Reinforced Polymer (FPR) pellet materials is that, there is a market for very large 3D printed parts. How big or small that market is in Europe?
In the midst of formnext 2021, we caught up with Dieter Ottmann, Business Development Managerof Thermwood in the DACH region, to understand where the European market for Large Scale Additive Manufacturing (LSAM) is headed – both from a manufacturing and business standpoints.
According to Ottmann, LSAM is a process that attracts the same vertical industries in Europe than in the USA: Aerospace, Machinery and Plant construction, Automotive, and Construction. “However, the arrangement of the supply chain is in some areas different to the American Market”, he notes. In terms of applications, large works of art that seem very appealing for LSAM in the USA are not widespread yet in Europe, Ottmann continues.
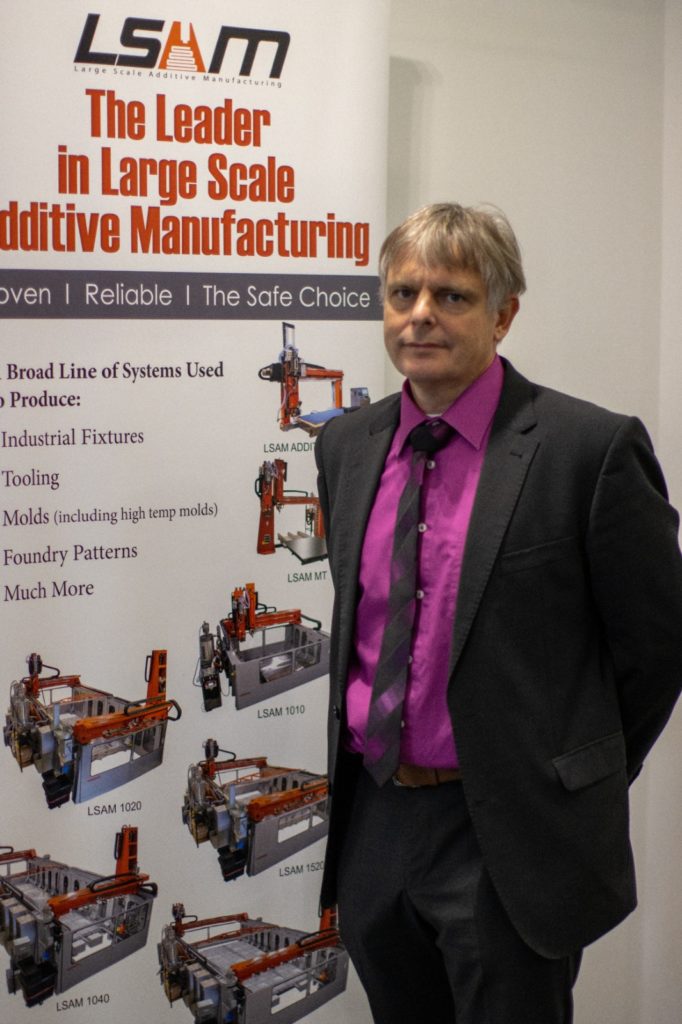
However, in industrial environments, Thermwood’s LSAM process has proven its capabilities in achieving a wide range of applications including autoclave tooling. As a reminder, such applications have become pivotal for processing high quality polymer composite aerospace structural components. In the aerospace for instance, an investment in the required manufacturing equipment needs to be done very strategically because its manufacturing often comes with certain challenges at the materials level, at the dimensions level (the challenge here being to achieve the same dimensions for every axis), to name a few.
As far as materials are concerned, one of the advantages in processing chopped fibres on LSAM is that operators can take advantage of the strength properties along with widespread availability and lower cost of pellets as compared to filaments. Not to mention that the use of chopped fiber provides distributed reinforcement throughout the matrix of the print.
To demonstrate the potential of these materials with LSAM process, Thermwood showcased at formnext 2021 two large parts that have been 3D printed with a part of the most widely-used material in Composite 3D printing: carbon-fiber. The material delivers higher strength, thermal conductivity and a lower coefficient of thermal expansion, all highly critical for tooling applications.
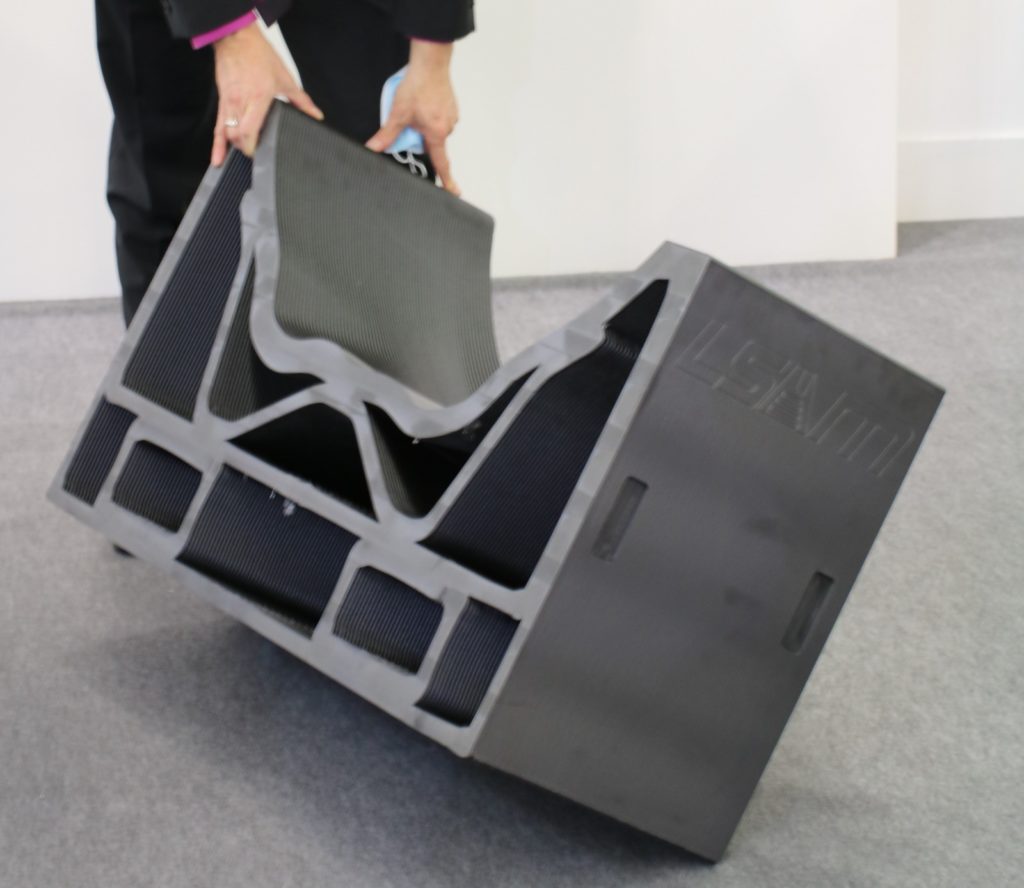
“The first part is an Air Foil tool made from Sabic ULTEM (20% Carbon Fiber filled), and was printed and trimmed on an LSAM 1020. The second (half-trimmed part) is also made from Sabic ULTEM (20% Carbon Fiber Filled), and was live printed on an LSAM Additive Printer 510 during the Rapid show in Chicago” the company’s German leader explains.
Interestingly, these examples reveal LSAM process’ ability to meet the needs of tooling and prototyping, which at the end of the day, are the main applications highlighted by those willing to produce very large parts. On the other hand, they lead us to question the ability of the technology to meet the needs of ready-to-use production parts.
In response to this question, Ottmann replied: “the vast majority of our customer base wants to build exactly what they had with traditional tooling with the cost and time savings of 3D printing. What we realized early on is that, we have to minimize the risk of adopting an emerging technology through extensive functionality, software, and training”.
By refocusing the debate on the manufacturing standpoint, Ottmann recalls that Thermwood designs the control software around managing the printing process so every day, functions happen with a push of a button.
“A few examples would be properly loading and unloading material and layer time control, which is monitored and managed by the system. Unlike most machine builders, Thermwood produces the control so we don’t have to wait for a third party to make updates. Thermwood’s ability to build each aspect makes the printing process much smoother with little room for operator error. Thermwood also provides extensive training both in the classroom as well as hands-on”, our interviewee adds.
Next challenges to address from both the user’s and the manufacturer’s standpoints
One thing we often omit to say in the way companies leverage AM is that, teams are often led by people who do not always have the required technical experience to embrace all facets of the technology. This is also the case for users of Thermwood’s LSAM process which is why Ken Susnjara, founder, Chairman and CEO of Thermwood Corporation, has written “A Manager’s Guide to Large Scale Additive Manufacturing”.
This 315-page book, currently available as either an eBook or paperback hardcopy, aims to help non-technical managers understand the basics behind a new technology that is revolutionizing production of large composite molds, tools and other industrial and commercial products.
Susnjara explains in everyday, no nonsense language what it is, how it works, what actually works, what doesn’t and why. A non-technical manager should not try to understand LSAM in all details to master the technology. However, he should be aware of all the basics to appropriately calculate the benefits and changes LSAM can bring to a business.
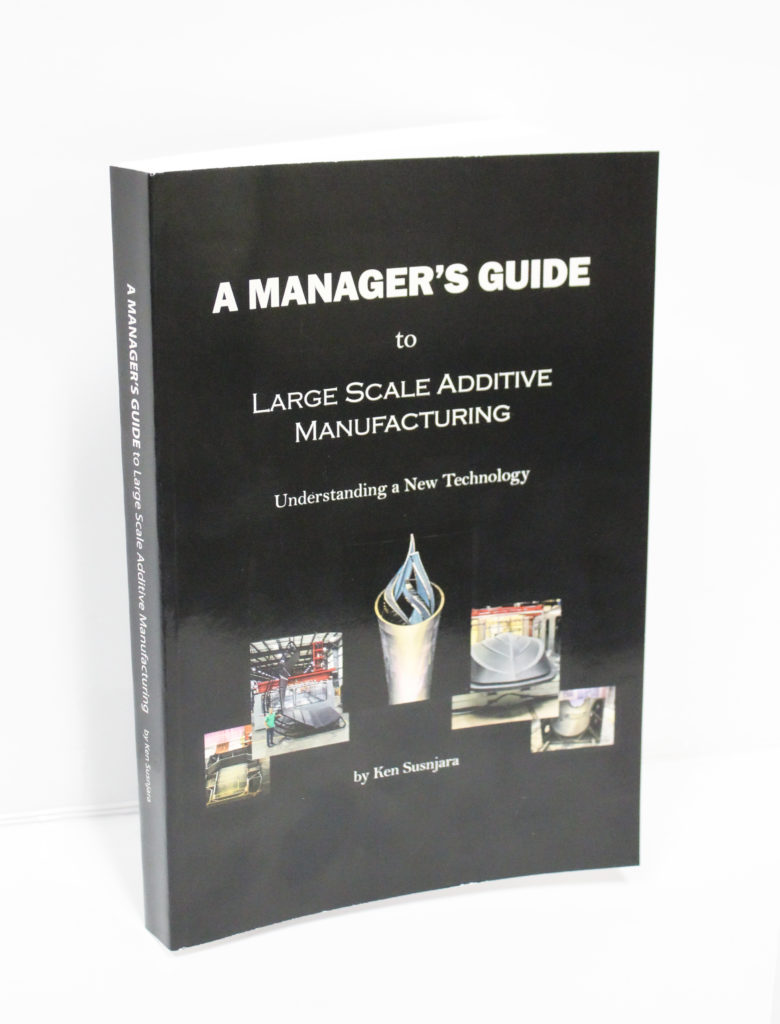
At present, the fact that Thermwood has successfully managed to install its large scale additive machines in everyday production environments within various industries, reconfirms the market of very large 3D printed parts is growing. Most importantly, it shows that this market goes beyond the simple act of selling machines as prototypes.
For this success to last, Thermwood, just like other machine manufacturers, must continuously enhance the manufacturing process with its machines. For this reason, the company will be releasing the “Angle Layer Printing” (short for ALP) in a few days. Other announcements will follow as well, announcements that promise to bolster Thermwood’s position within the market. To date, the company has always kept its promises, so I have no doubt that it will continue to do so.
Remember, you can post free of charge job opportunities in the AM Industry on 3D ADEPT Media or look for a job via our job board. Make sure to follow us on our social networks and subscribe to our weekly newsletter : Facebook, Twitter, LinkedIn & Instagram ! If you want to be featured in the next issue of our digital magazine or if you hear a story that needs to be heard, make sure to send it to contact@3dadept.com