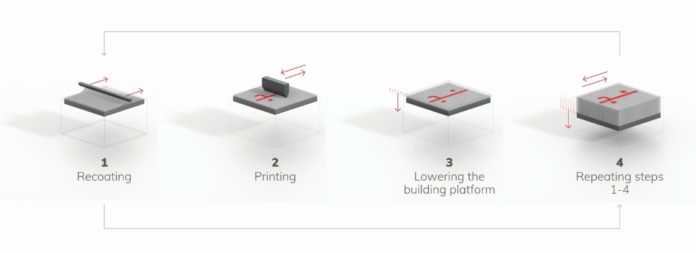
A collaboration between GE Renewable Energy, Fraunhofer IGCV, and voxeljet AG
While onshore wind turbines seem to be appealing for construction 3D printing, offshore wind turbines seem to have found in Sand Binder Jetting 3D printing their ideal manufacturing technology. So far, the environmental factors have often influenced the offshore wind turbine design and made production efficiency on open water a challenging prospect.
Fortunately, technology productions are being enhanced. As a matter of fact, a recent collaboration between GE Renewable Energy, Fraunhofer IGCV, and voxeljet AG might help us seen further improvements as the three companies ambition to develop what they describe as the “world’s largest sand binder jetting 3D printer for offshore wind turbines”. The main objective behind this development is to streamline the production of key components of GE’s Haliade-X offshore wind turbine.
One of the first advantages I can directly see is, that at the manufacturing level, GE Renewable Energy will be able to appreciate the capabilities of various manufacturing techniques for wind energy turbines. Remember, the company had signed a partnership with COBOD and LafargeHolcim to establish new record by co-developing 200 metres high 3D Printed wind turbines. Not that the comparison could be important for COBOD and Holcim, but it could be important to learn lessons for the renewable energy industry.
If you are a regular reader of 3D ADEPT Media, then you probably know research institute Fraunhofer IGCV that drives innovation with focus on efficient engineering, networked production, and smart multi-material solutions. We may have seen the organization’s involvement in several projects related to the transport industry such as the POLYLINE, or the approval of 3D printed parts for the railway industry, but the organisation’s major focus is on the future scenarios and topics of the casting industry.
Voxeljet on the other hand, is a 3D printer manufacturer that has been in this industry for more than two decades. The company’s solutions are currently being used across several industries, and the addition of renewable energy to this board will only make voxeljet, a high-profile manufacturer for this industry.
So, what should we know about this new 3D printer?
First of all, from a financial perspective, let’s note that the Advance Casting Cell (ACC) 3D printer under development will receive financial support from the German Federal Ministry for Economic Affairs and Energy.
As far as manufacturing is concerned, voxeljet will bring here its expertise in “Binder-Jetting” technology, since the modular 3D printing process will leverage its technology.
The production will be based on casting, a manufacturing process in which a liquid material is usually poured into a mould, which contains a hollow cavity of the desired shape, and then allowed to solidify. The solidified part is also known as a casting, which is ejected or broken out of the mold to complete the process.
That being said, the 3D printer could print moulds to cast components for the nacelle* of the GE Haliade-X that can each weigh more than 60 metric tons, reducing the time it takes to produce this pattern and mould from ten weeks or more to just two weeks. (A nacelle is a housing unit on top of the tower of a wind generator that contains its mechanical components.).
So, the production of sand moulds for casting the highly complex metal parts of different shapes and sizes will make up an offshore wind turbine nacelle. With the modular manufacturing process, the machine can be configured to print molds for castings up to 9.5 meters in diameter and 60-plus tons in weight, dimensions.
While no exact figures have been given to support this statement, the partners said we might expect the 3D printer to reduce the product’s carbon footprint since there will no longer be the need to transport the large parts from a central manufacturing location.
Juan Pablo Cilia, Senior Additive Design Engineer at GE Renewable Energy, said, “The 3D printed molds will bring many benefits including improved casting quality through improved surface finish, part accuracy and consistency. Furthermore, sand binder jet molds or additive molds provide cost savings by reducing machining time and other material costs due to optimized design. This unprecedented production technology will be a game changer for production efficiency allowing localized manufacturing in high cost countries, a key benefit for our customers looking to maximize the local economic development benefits of offshore wind.”
The Fraunhofer Institute for Casting, Composite and Processing Technology IGCV is responsible for casting and materials technology issues as well as digital process monitoring. “We are taking a close look at thermal management during casting, and we will evaluate the ideal proportions of the printing materials,” said Dr. Daniel Günther, Head of Department Molding Processes and Molding Materials at Fraunhofer IGCV. “Also, we will develop and test new approaches to process monitoring as part of the project.”
Based on prior experience the team expects to significantly improve the environmental footprint of processes involved in producing the Haliade-X type wind turbines. This sustainability aspect is a firmly established guiding principle of research at Fraunhofer-Gesellschaft, according to the institute’s director, Prof. Dr. Wolfram Volk, who adds: “We aim to optimize the mold printing to avoid extremely costly misprints or even miscasts, to save on binder and activator, and to improve mechanical and thermal behavior during casting. By developing a process that conserves resources as much as possible, we want to help to improve the environmental and cost balance in the manufacture of wind turbines.”
Christian Traeger, Director of Marketing and Sales at voxeljet, said, “The test mold we printed for GE in 2019 consisted of dozens of individual parts. With the ACC, we aim to print a significantly reduced number of parts for the full set. Added to that, the mold can be optimized in terms of functionality and material consumption. This optimization makes completely new casting designs possible that can further enhance the efficiency of the turbines.”
“While offsite on-demand 3D printing provides many benefits for small quantities of cast parts, running a 3D printing system on-site leverages the technology to its fullest capacity. Given the demand for offshore wind turbines, that will help a lot to fulfill project schedules and high market demands,” adds Dr. Ingo Ederer, CEO at voxeljet.
The partners expect to launch the project during the third quarter of 2021 with initial printer trials starting during the first quarter of 2022.
The International Energy Agency3 has projected that global offshore wind capacity will increase 15-fold by 2040, becoming a 1 trillion dollar industry, thanks to falling costs, supportive government policies and technological progress like that behind the Haliade-X offshore turbine from GE Renewable Energy. GE Renewable Energy has been selected to supply its Haliade-X turbine for 5.7 GWs worth of projects in Europe and the US. The company is a member of the Offshore Wind Industry Council (OWIC) and as part of that supports various initiatives that aim at increasing the production of sustainable wind energy.
Remember, you can post job opportunities in the AM Industry on 3D ADEPT Media free of charge or look for a job via our job board. Make sure to follow us on our social networks and subscribe to our weekly newsletter : Facebook, Twitter, LinkedIn & Instagram ! If you want to be featured in the next issue of our digital magazine or if you hear a story that needs to be heard, make sure you send it to contact@3dadept.com