There’s an old saying in business that “being early is the same as being wrong“. Indeed, when you are too early, your startup is more likely to fail because it is ahead of its time. This happened to be true for many companies in the additive manufacturing industry, except in voxeljet’s case.
Going through the various crisis that marked this engineering market and standing strong today makes voxeljet a unicorn we wanted to discover more about. To help us tell this story, we’ve invited in this Opinion of the Week segment, Tobias King, the company’s Director for Marketing and Applications.
It’s already been two decades that Dr. Ingo Ederer founded voxeljet. The machine manufacturer was then focused on the development of 3D printing technology for metal casting applications. In a nutshell, their technology additively manufactures sand casting molds and plastic models for investment casting. This was quite crazy because as you may know, at the time, molding and milling processes were mainly utilized for the production of tools and moulds. Not to mention that these technologies do not really enable to achieve certain geometric complexity.
So, when voxeljet debuted on this market, it established a new manufacturing standard, which turned to be a mission to continuously innovate and stimulate a “new industrial and constructive thinking”, a mission that has been refined over time as today the company aims to redefine additive mass manufacturing.
King on the other side joined the 3D printing pioneer in 2008. From project engineer to Director of Marketing & Applications, he is one of those collaborators that helped define and implement strategic objectives & operating marketing measures, for the expansion of the company’s products and applications portfolio. As per his words, his role includes but is not limited to new applications such as the construction, laminating and polymer markets in which their products can be used as concrete casting formwork, laminating tools and functional polymer parts for end use applications.
Anyway, voxeljet has strived to remain mission-focused. As the company’s representative states:
“When we initially started, our printers had a building volume of 1.500 x 700 x 750 mm. That was already quite big for printers launched in 2003. Today, our largest 3D printing system has a building volume of 4.000 x 2.000 x 1.000 mm. This leaves a lot of room for either very large molds or a very high number of small parts. In 2011 we also developed a concept of a continuous 3D printer which could be able to create infinite numbers of parts. In general, we continuously strive to rethink and redefine our products in a future oriented manner. Today, 3D printing has matured to a manufacturing technology that finds applications far beyond prototyping and spare part production.”
Nevertheless, voxeljet has opened new doors to casters, engineers and toolmakers who wanted to keep metal casting at the heart of their production environment. The manufacturer has become acknowledged for supporting foundries in casting shapes that would not be possible to achieve with traditional processes. Remember the story of the Indian Steel Foundry that invested in the industrial 3D printer VX4000 to manufacture and supply steel castings.
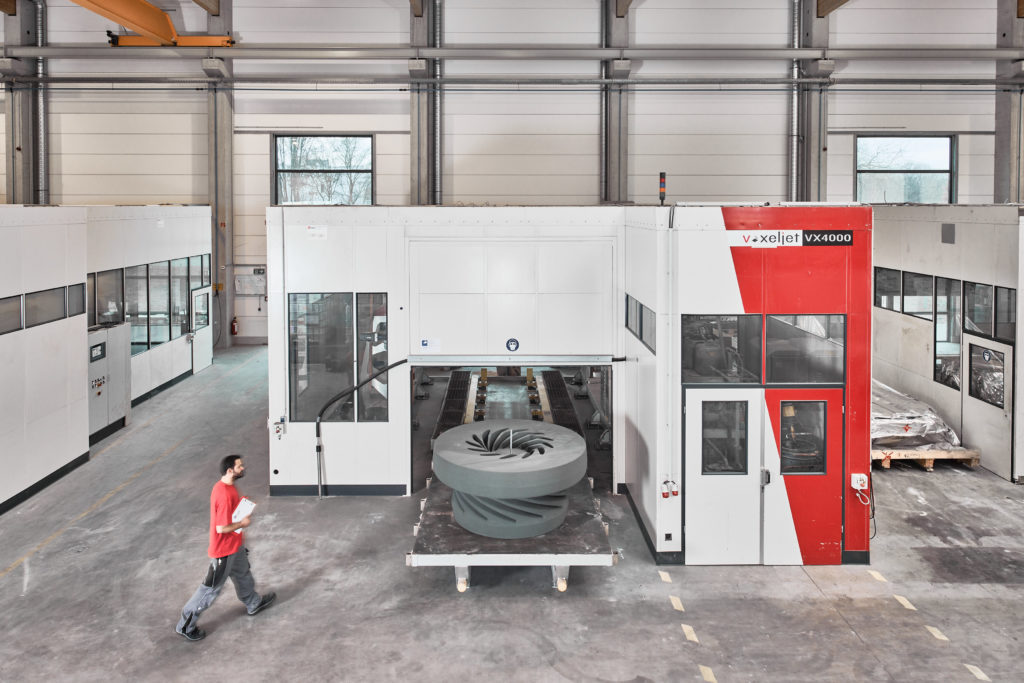
From a technical perspective, those applications in investment casting and sand 3D printing are made possible thanks to the company’s Binder jetting technology. King explains that, at voxeljet, they bond powder materials with high performance industrial print heads and create parts within a powder bed. Such process enables therefore to print everything that comes in a powder state, hence the focus on sand for “sand casting applications, and acrylic powder for investment casting applications at first.” When asked what makes their technology a good candidate for these applications, the Director Marketing & Applications points out the importance of using affordable standardized foundry materials such as silica sand and various resins, time and cost savings.
“The traditional tool creation can take up to 8-12 weeks and costs a lot of money. That’s a lot of time and resources to create a prototype, that in the worst case won’t qualify for production. With our Binder Jetting technology the moulds can be printed, delivered and casted in just a week, at a fraction of the cost compared to classic tooling. And the handling for the caster himself doesn’t change at all, the moulds or the investment casting models can be integrated into the traditional casting process. This is what makes additive manufacturing so attractive.
Additionally, the materials we use aren’t that expensive. With the fastest build rates in AM that Binder Jetting offers, combined with the total costs of ownership of a 3D printing system, or the on demand production in our service centres is rather low. That’s why we can target markets with high output rates such as the automotive industry. If customers don’t need a whole printing system, because e.g. the amount of low, customers can always drop orders in our service centres and get the parts delivered within few days.”
Things got exciting three years ago, when they launched their High Speed Sintering (HSS), opening new doors to the creation of polymer parts whose properties can be similar to SLS or injection-moulded parts.
“Industrialization of core printing”
This was also the time when voxeljet woke up from its stealth mode and decided to address specific issues raised by vertical industries adopting AM including automotive. Beyond being a crucial vertical for any AM manufacturer, the automotive industry is also a key target for production volumes.
The developer of sand binder jetting technology expressed the need to position on such markets within the ICP project, short for “Industrialization of core printing”; a project that saw the development of the VJET X 3D Printers series made in collaboration with foundry expert Loramendi and materials specialist ASK Chemicals. While the three companies aimed to achieve additive serial production of water jacket cores, the project itself has helped voxeljet reach a milestone in its vision to redefine additive mass production. Laying emphasis on the technical specifications, King highlights the use of their VX1300 X 3D printer as part of this production line. “It’s a high performance 3D printer with more than 10 times the speed than our usual printers. The printer uses an inorganic binder, developed by ASK Chemicals, to bond the sand. The advantage of the inorganic binder is, that during casting, only water vapour is created, which improves the working conditions within the foundry significantly and has a positive impact on the environmental footprint. Loramendi developed the whole, fully automated post processing of this production line. This production line is installed at an automotive customer in Germany.”
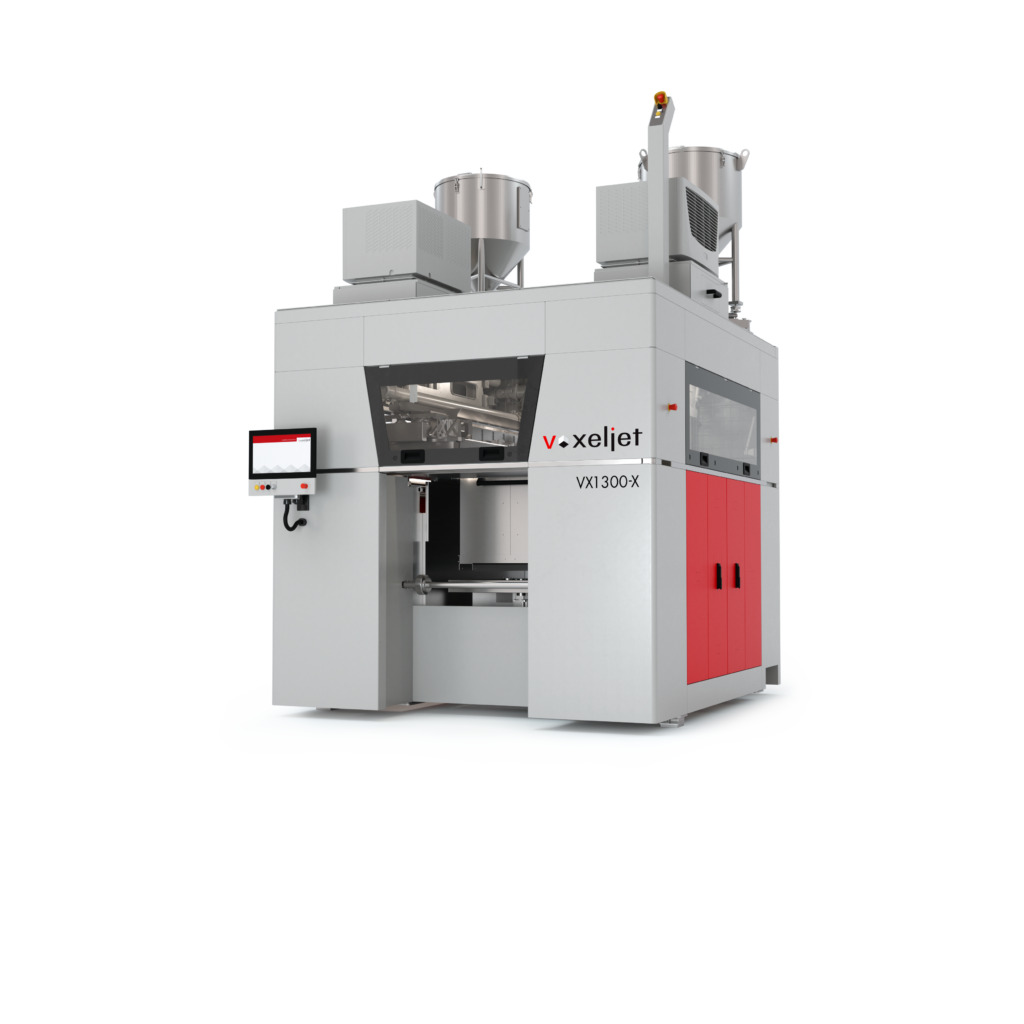
The next steps for voxeljet?
Building on its years of experience, voxeljet is now looking to enhance current bottlenecks of the manufacturing process such as automation at the post-processing stage and develop a new line of products. Following the launch of the first prototype of their VX1000 HSS system at Formnext 2019, the voxeljet team will keep the development of the large-scale polymer 3D printer as one of their priorities for the upcoming months.
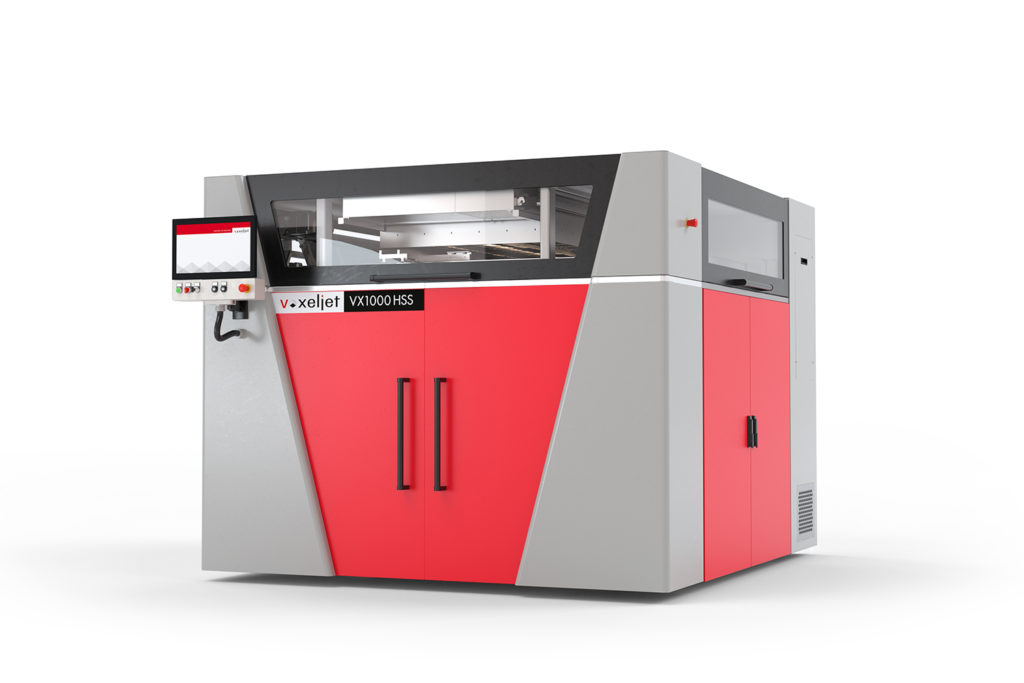
However, for next year, “we fully focus on our vision to bring additive polymer manufacturing into serial production with the launch of the beta version of the VX1000 HSS. 2020 was a special year, with many enormous challenges we all had to face. But for the additive manufacturing industry it was quite interesting. The sudden lack and surplus demand for many products could be met with AM technologies. This showed the world what this technology is already capable of. We’ll continue on our mission and work on our 3D printing solutions in order to pave the way for a new manufacturing standard” King concludes.
In the meantime, if you feel you want to interact with the company’s experts during a show, feel free to meet them at the upcoming Formnext Connect.
Remember, you can post free of charge job opportunities in the AM Industry on 3D ADEPT Media or look for a job via our job board. Make sure to follow us on our social networks and subscribe to our weekly newsletter : Facebook, Twitter, LinkedIn & Instagram ! If you want to be featured in the next issue of our digital magazine or if you hear a story that needs to be heard, make sure to send it to contact@3dadept.com