In a recent Additive Talks session, one learned the importance of thermal/fluid system designs to enhance speed, and performance in electrification. A few weeks later, Megnajet, a fluid management system expert, appeared on our radar with a new fluid management system designed for AM. This raised so many questions on the use of fluid management systems in Additive Manufacturing that we have decided to ask Mike Seal, Megnajet General Manager.
Megnajet (a subsidiary of Xaar) may have appeared on our radar lately, but the company was founded in 2010 to meet the growing demand for inkjet print systems in various industries. The more inkjet technology advanced, the more industrial sectors were looking for customizable solutions to create any image in any quantity at any time. As the potential of this ‘industrial inkjet revolution’ was gaining momentum in the ceramics industry, the subsidiary of Xaar decided to explore this potential for inkjet 3D printing, thus providing fluid management systems to several players in the AM realm.
Simply put, fluid management systems are a set of devices, and procedures that help to control, measure, and maintain the flow of fluids in various industrial applications. This set of tools has proven to be critical in a number of industries such as pharmaceuticals, manufacturing, food & beverage processing, and wastewater treatment, to name a few. This management system, therefore, consists of several components that can often be produced using AM. They include for instance valves, flow meters, tanks, pumps, filters, and sensors.
Nevertheless, in AM and inkjet printing in particular, fluid management systems help to provide precise control and conditioning of the fluid, to ensure the printhead can jet effectively.
According to Mike Seal, “All printheads require a reliable input to deliver a consistent and accurate output. Fluid management systems are responsible for this reliability by conditioning the fluid, ensuring it is at the correct temperature, pressure, particle uniformity, and that the particles are maintained in suspension – all of which are critical for effective jetting.
Inkjet 3D printing applications demand a high level of fluid control due to the multilayered nature of the printing process. Any faults or failures of the system to deliver each layer reliably could result in a range of errors from cosmetic to part failure – which is exacerbated the larger the part is, or the more parts are produced. In addition, developments in printhead capability to jet higher viscosity fluids mean a fluid management system must maintain precise temperature control to ensure an ink’s viscosity remains within the optimal range for seamless jetting.
High-viscosity inkjet typically utilizes recirculating architecture within the printhead which when matched with an effective fluid management system fully realizes this capability and provides increased reliability. These technologies are significant for inkjet 3D printing as they enable the use of more advanced materials and ultimately improve the functionality of parts and ensure part failure is avoided.”
AM processes that require the use of fluid management systems
While fluid management systems can be used with AM processes that involve fluid control and conditioning, Megnajet decided to focus on polymer jetting, binder jetting and inkjet-based powder-bed fusion technologies.
Among these technologies, the focus on inkjet 3D printing makes sense when we know the company already has deep expertise in 2D printing, when we know there was a shift from single-pass digitalized printing of ceramic tiles to a wide range of applications with diverse printing requirements.
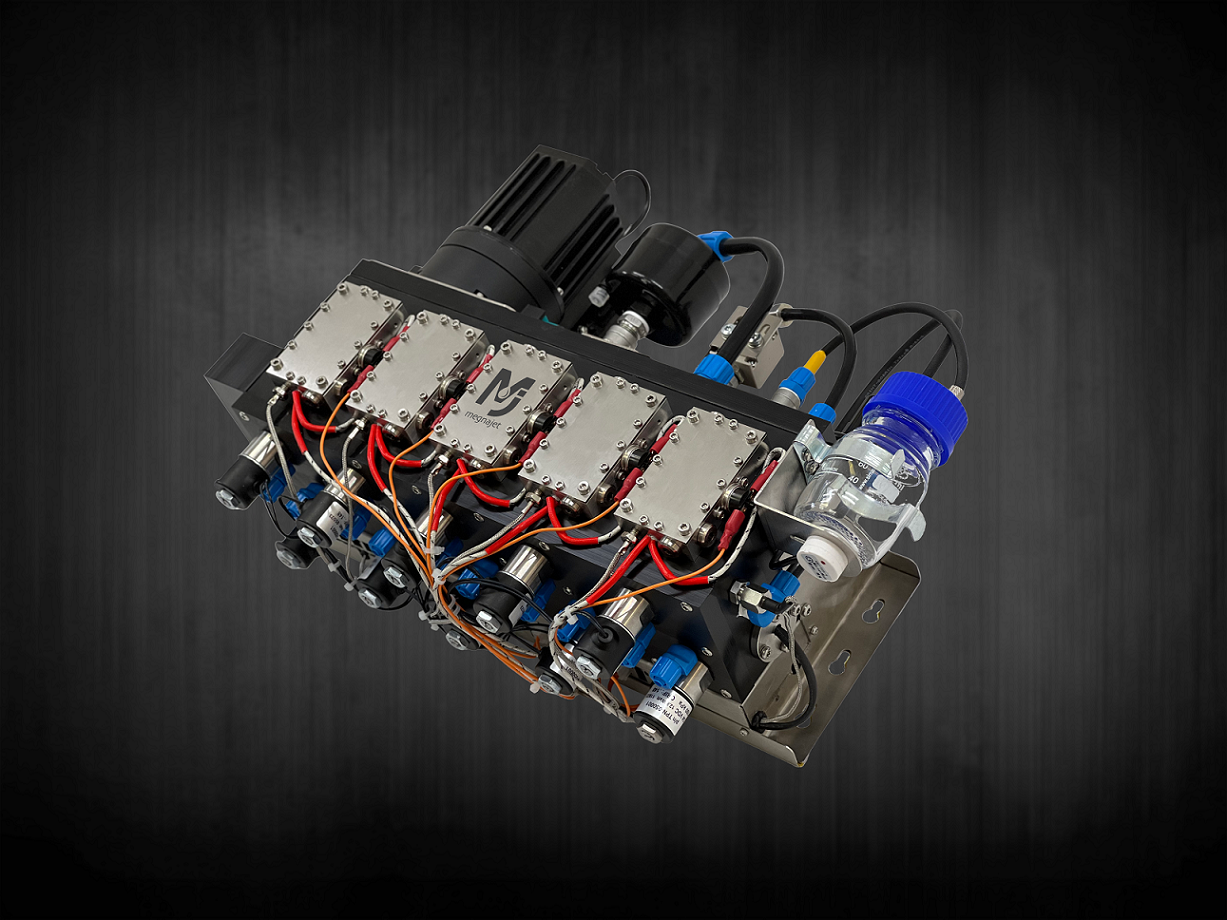
The development of the JetSource in particular, the fluid management system Magnajet recently unveiled, has been driven by a demand from clients in inkjet 3D printing and Label printing who wanted to achieve higher flow rates, faster speeds, higher productivity, and a wider array of printheads.
“Our latest fluid management system recirculates fluid at up to four liters per minute across up to five independent ports for printheads for use in various applications such as inkjet 3D printing, labeling and packaging embellishments, special varnish effects and braille. This system allows for increased productivity and improved scalability in 3D printing processes”, the General Manager outlines.
Speaking of the key specifications related to the use of fluid management systems with the aforementioned AM technologies, he adds:
“In inkjet 3D printing, reliability is paramount. A small defect in one layer can lead to a costly and timely functional or structural failure in the final printed product. Therefore, fluid management systems are indispensable in additive manufacturing to achieve consistent and reliable printing results.
In binder jetting, fluid management systems are responsible for accurately delivering binders to the printheads for depositing onto powder beds to create 3D-printed parts. Precise control over the fluid parameters is essential to achieve accurate and repeatable results.
Similarly, in inkjet powder bed fusion, our systems are crucial for maintaining the right fluid characteristics, such as temperature, pressure, particle uniformity and dispersion to ensure proper fusion of each layer to itself and subsequent layers during the printing process. Thermal regulation of the fluid over a high-temperature powder bed is also an important role of the fluid management system in inkjet-based powder-bed fusion.
In polymer jetting, fluid management systems are crucial because they must be able to handle heated fluids, often at higher viscosities than typical inkjet applications. Megnajet’s systems excel in both traditional and high-viscosity fluids, surpassing the capabilities of most conventional inkjet systems. This capability enables the use of a broader range of materials in 3D inkjet printing applications, including advanced polymers and functional fluids.”
So, how does one select the fluid management systems that work best for an AM process/ an AM application?
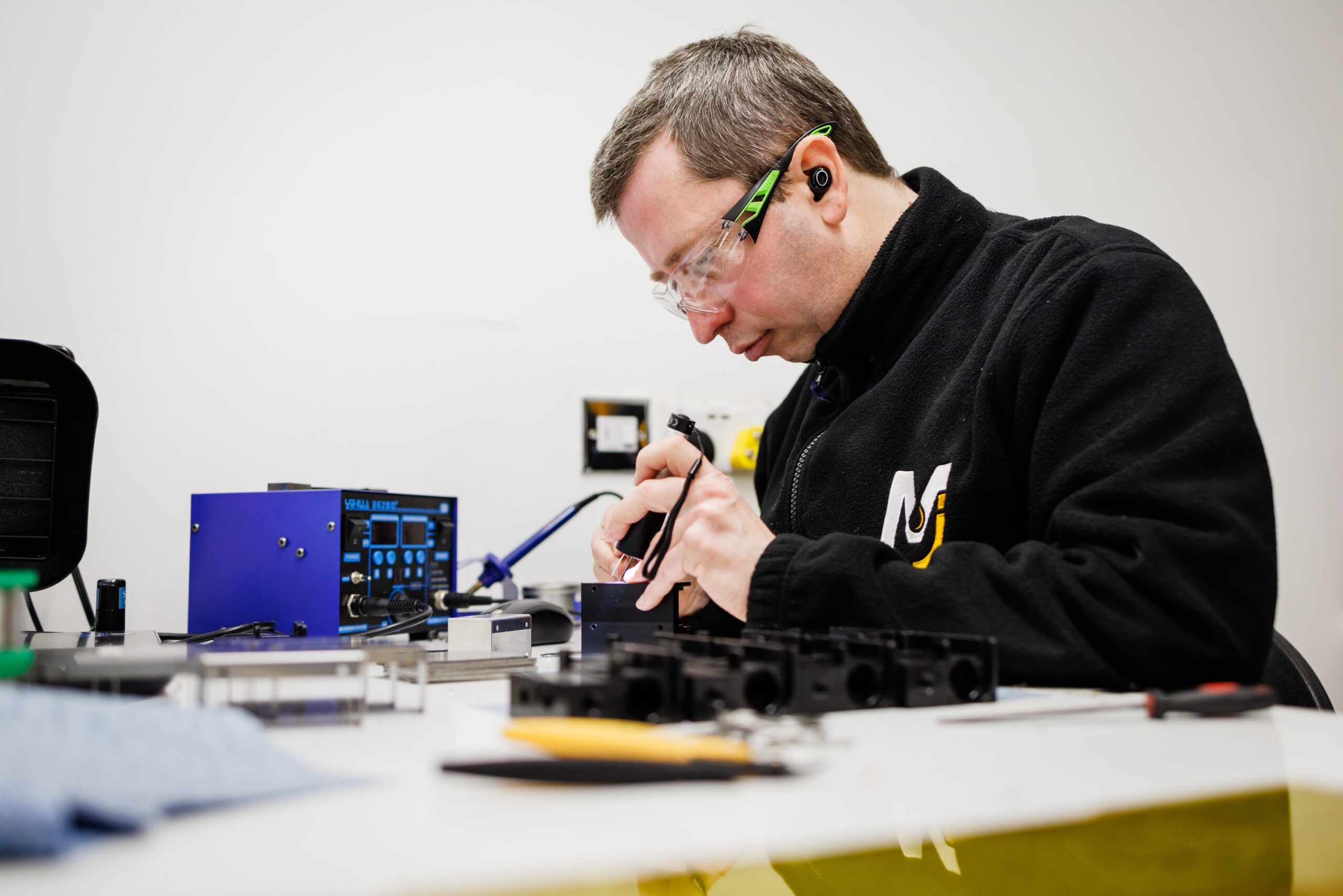
Just like there are different types of AM processes, we also have different types of fluid management systems, each designed to meet the requirements of specific printhead technologies and the number of printheads required for the application.
As little information is available on how to select the ideal fluid management system in an AM application, AM experts should have a conversation with experts in the field to have a clear understanding of what might meet their needs. Not to mention that testing can often be offered by companies to help industrials make up their mind.
That being said, by creating fluid management systems that are based on industry sector requirements and specific customer needs, Seam ensures that Megnajet can supply off-the-shelf, customized and bespoke solutions for a wide range of printhead technologies and applications.
This article has first been published in the July/August edition of 3D ADEPT Mag.
Remember, you can post job opportunities in the AM Industry on 3D ADEPT Media free of charge or look for a job via our job board. Make sure to follow us on our social networks and subscribe to our weekly newsletter : Facebook, Twitter, LinkedIn & Instagram ! If you want to be featured in the next issue of our digital magazine or if you hear a story that needs to be heard, make sure to send it to contact@3dadept.com