Jonathan Jaglom, a long time veteran of 3D Printing, has recently brought to our attention a few problems with coating processes: they are “typically time consuming, labour intensive, costly and limited” in terms of offering and colours. He now aims to address these challenges using Additive Manufacturing – and that alone was enough for us to try to understand how.
Based in Israel, flō uses AM technology to produce advanced lens coatings. “We have the ability to coat lens by accurately depositing material on the lens. This is a very innovative approach as today’s technologies are mainly driven by what is called a wet process (lens are dipped into a vat, removed and dried)”, Jaglom explains.
At the heart of the manufacturing process, one finds an inkjet-based 3D printing technology that applies unique, multi-material, multi-layer coatings to lenses. This proprietary deposition technology is built on a rich expertise in digital printing.
As seen in the short overview below, the process would jet material at a voxel level, enabling for accuracy at the production level. The process would allow for the distribution of the material where needed, resulting in the creation of lenses with customized functionalities for specific uses.
First agreement will help us see the potential of flō
Unlike most companies that turned stealth mode off by announcing a funding round, flō decided to show that their solution already attracts specific targets. One of them is Yeda Research and Development Co. with which it has signed an exclusive license agreement. The agreement concerns the use of Weizmann Advanced Materials for optical coatings, applied via flō’s proprietary Additive Manufacturing (AM) technology.
This agreement lays emphasis on the fact that coatings range in function and vary according to customer needs. And these specific needs often come from the ophthalmic labs that fulfil the opticians’ requests.
“These labs are manufacturing hubs, generating thousands of customized lenses daily. flō’s platform will serve this audience, allowing the labs huge benefits around the use of our technology,” Jaglom points out.
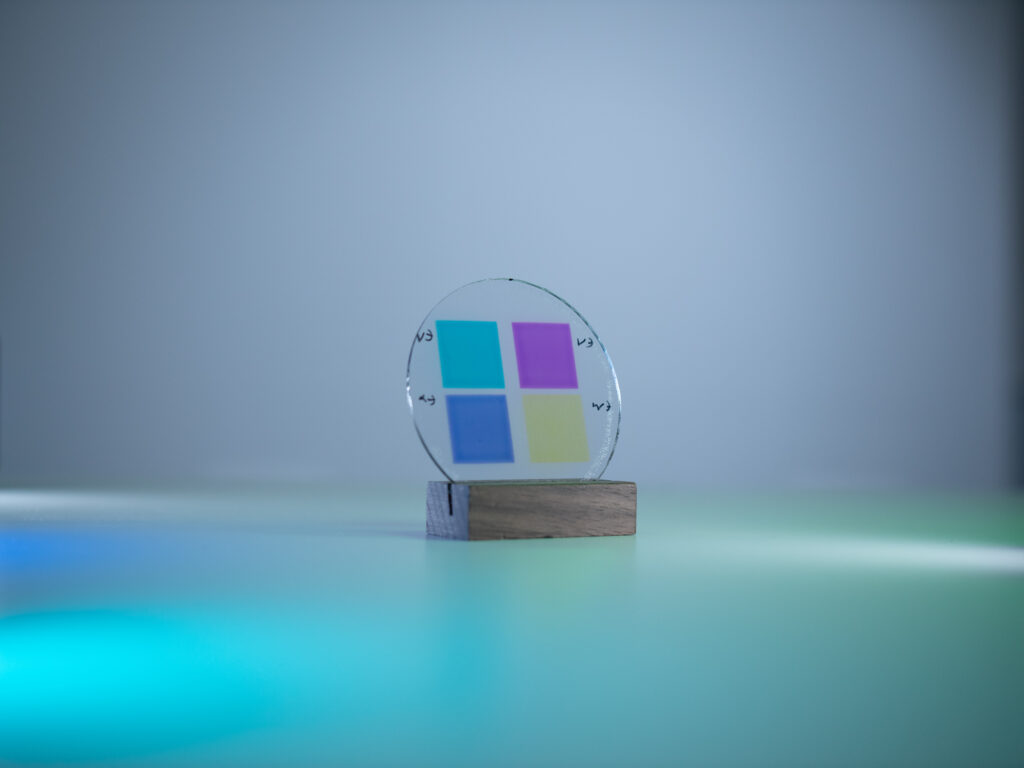
Benefits in terms of cost, functionality, customization and on-demand production are expected.
Speaking of “on demand production”, Jaglom explains that “at peak seasons, demand can spike, and further systems can be installed. At holiday seasons they can be shut down and cartridges can be reused. This all doesn’t exist in today’s market.”
“flō systems are much more environmentally friendly. The platforms are closed and ventilated, cartridges are sealed and can be reused. There is a lot less water used as part of the concentration of the materials. This all leads to a much more environmentally friendly platform,” he adds.
flō is definitely ahead of the curve on this market and with a team that collectively cumulates some 150 years of expertise in digital printing, over 120 patents registered in digital print in their previous life, and some 35+ products developed, I trust that they will do well.
Discover more about their product here and what they are up to.
Remember, you can post job opportunities in the AM Industry on 3D ADEPT Media free of charge or look for a job via our job board. Make sure to follow us on our social networks and subscribe to our weekly newsletter : Facebook, Twitter, LinkedIn & Instagram ! If you want to be featured in the next issue of our digital magazine or if you hear a story that needs to be heard, make sure to send it to contact@3dadept.com